Hamburg. Hinter den Kulissen des Hamburger Airbus-Werks. In Halle 9 kommen hinten Rumpfteile rein und vorn fertige Flieger raus. Die Video-Reihe.
Zig Gebäude gibt es auf dem Hamburger Werksgelände von Airbus. Die verschiedensten Aufgaben werden darin erfüllt. Doch als Herz des Standortes kann man wohl die vier Endmontagelinien bezeichnen. Schließlich sind sie das sichtbarste Zeichen für das, was den Standort ausmacht. Am Ende steht ein fertiges Flugzeug.
Eine dieser vier Endmontagelinien ist in Halle 9 untergebracht. Hinten kommen die Rumpfteile in die Riesenhalle. Fünf Stationen dauert es, bis aus ihnen ein fertiger Flieger des Verkaufsschlagers A320-Familie wird. Der Höhepunkt passiert in der Mitte.
Warum Airbus alle 2,5 Tage eine Hochzeit in Halle 9 feiert
„An Station 40 bringen wir die Flügel an den Rumpf an, welchen wir zunächst aus der vorderen und hinteren Rumpfsektion zusammengefügt haben“, sagte Bernhard Holtrup, der die zweite von vier Endmontagelinien auf Finkenwerder leitet. „Wir nennen das auch Hochzeit.“ Doch bevor es so weit ist, müssen die etwa 250 Beschäftigten in der Halle eine Reihe von anderen Arbeiten erledigen.
Los geht es am hinteren Ende der Halle 9. An Station 42/43 werden viele vorbereitende Tätigkeiten ausgeführt. Ein vorderer Rumpfabschnitt mit Cockpit ist zu sehen, der aus dem französischen Werk in Saint-Nazaire zugeliefert wurde. Mehrere Rollcontainer stehen davor. Zum Beispiel sind sie mit Fußbodenplatten gefüllt, die von den Elbe Flugzeugwerken in Dresden kommen.
A320-Endmontagelinie: Küchen und WCs kommen gleich zu Anfang in die Jets
Von einem mächtigen, gelben Arbeitsgerüst aus können die Mitarbeiter direkt in das offene Ende des Rumpfsegments gehen. „Die Tonnen sind schon zu einem hohen Grad ausgerüstet, zum Teil mit Fußboden, Elektrik und Leitungen“, sagt Holtrup. „Wir setzen an dieser Stelle an, machen eine Eingangsprüfung, schauen, ob die Qualität passt, und kontrollieren die Tonnen nach dem Transport auf Beschädigungen.“
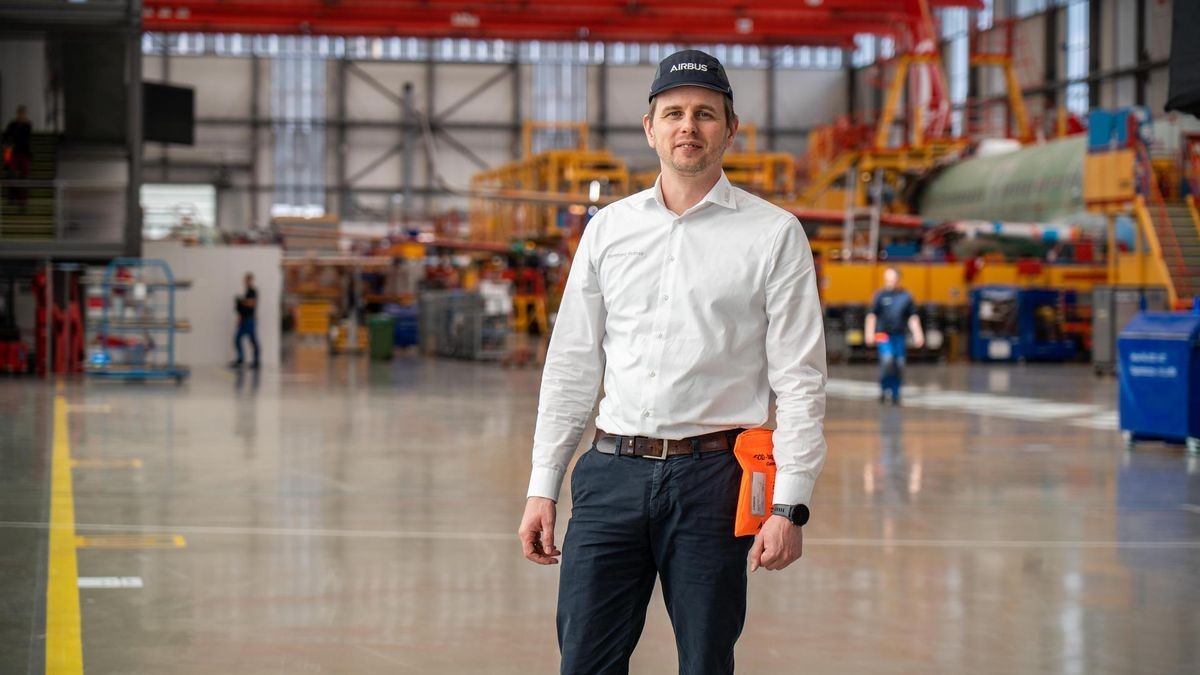
An dem benachbarten Arbeitsgerüst stehen auf Paletten die nächsten Großbauteile bereit: Küchen und Toiletteneinheiten, die von Folie geschützt sind. Sie werden schon an dieser Stelle des Fertigungsprozesses in den Rumpfabschnitt geschoben. „Später bekämen wir sie gar nicht mehr oder nur mit großem Aufwand durch die Türen in das Flugzeug hinein“, sagt Holtrup – und wird bei seinen Erklärungen immer wieder von knallenden Geräuschen gestört.
Beim Bohren und Nieten wird es laut in der Halle
Sie kommen von Station 41. Dort wird die vordere Rumpfsektion mit der hinteren aus Hamburg stammenden zusammengenietet. Beim Bohren und Nieten wird es auch mal lauter. An der Station besteht daher die Pflicht zum Tragen eines Gehörschutzes. Ansonsten ist dies in der Halle nicht notwendig, für einen Industriebetrieb ist es in ihr auch eher leise.
Mit dem Deckenkran wird die fertige „Zigarre“ dann zur Hochzeitsstation gehievt – der Station 40. Die Tragflächen werden exakt an den Rumpf ausgerichtet. „Das passiert supergenau, und hat Einfluss auf die spätere Performance des Flugzeugs“, sagt Holtrup. Im Anschluss wird gebohrt und vernietet.
2198 Nieten verbinden einen Flügel des A321 mit dem Rumpf
Es ist eine Mammutaufgabe: Insgesamt 2198 Nieten verbinden beim A321 die Flügel mit dem Rumpf. Aber dennoch erfolgt der Flügelanbau in schöner Regelmäßigkeit, so Holtrup: „Hochzeiten gehören bei uns zum Tagesgeschäft, das passiert hier alle 2,5 Tage.“
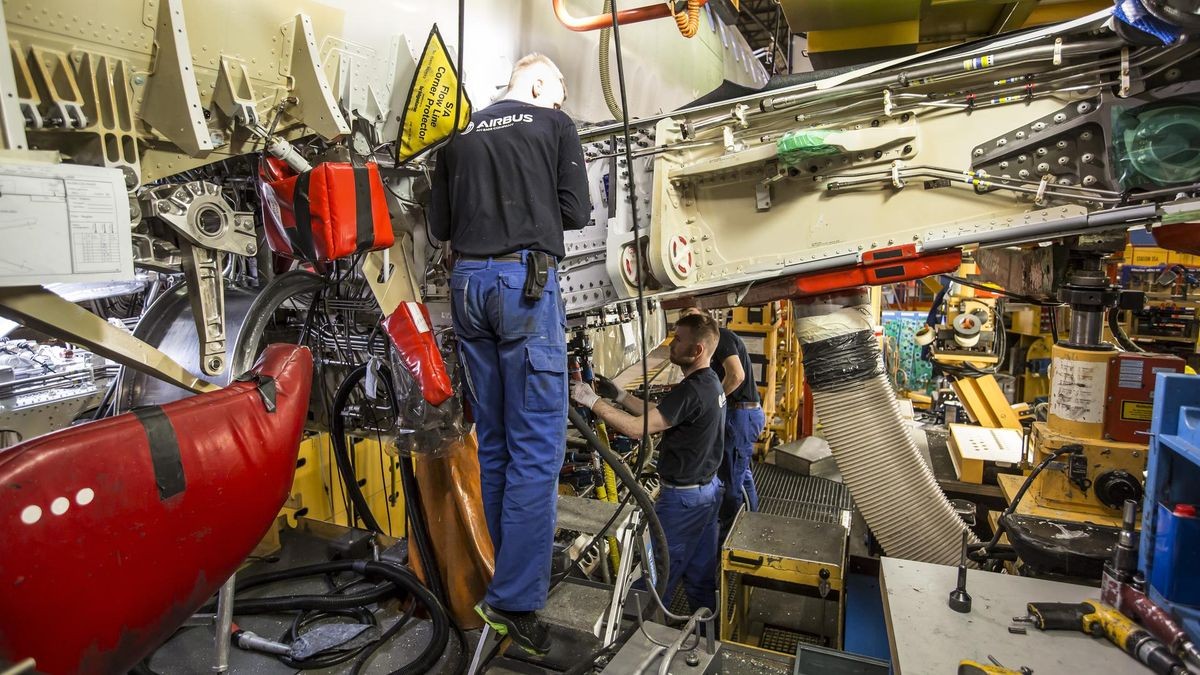
Das Arbeitspaket an dieser Station ist so umfassend wie an keiner anderen. Normalerweise wird in der Halle 9 im Zweischichtsystem gearbeitet. Hier gibt es drei Schichten, nachts wird ebenfalls malocht. Vorstationen direkt an der Hauptstation ermöglichen den straffen Zeitplan überhaupt erst.
So wird das Flügelpaar für das nächste Flugzeug schon ausgepackt, einer Qualitätskontrolle unterzogen und vorbereitet. An den Tragflächenenden werden die Sharklets montiert. Das sind nach oben gebogene Flügelspitzen, die später den Treibstoffverbrauch des fertigen Flugzeugs senken.
Die Fahrwerke des A321 müssen bis zu 97 Tonnen Startgewicht tragen
Sie fallen optisch in der Halle auf. Denn eigentlich sind alle Flugzeugteile noch in der für das Aluminium typischen grünen Grundierung gehalten. „Die Sharklets kommen als fertige Komponente von einem Zulieferer hier an. Die sind nach Möglichkeit schon in Kundenfarbe lackiert, um Arbeitsschritte vorher zu erledigen und in unseren Lackierhallen weniger erledigen zu müssen“, sagt Holtrup.
Auch Pylone stehen parat. Die in Toulouse gefertigten Teile werden an den Flügeln montiert, um später die Triebwerke zu tragen. Die Fahrwerke, die über die Köpfe der daran vorbeigehenden Menschen ragen, sind ebenfalls schon herangeschafft worden.
Bei einem A321 müssen sie bis zu 97 Tonnen maximales Startgewicht tragen. Damit die Landung sanft wird, ist ein Dämpfungssystem eingebaut. „Hier an der Station 40 bauen wir die Fahrwerke an. Das Flugzeug kann ab hier auf den eigenen Rädern rollen“, sagt Holtrup.
Flügelspitzen und Seitenleitwerk sind schon im Kundendesign lackiert
Wenn alle Arbeiten erledigt sind, werden die Arbeitsbühnen zur Seite gefahren. Ein Zugfahrzeug zieht den Flieger zum nächsten Bauplatz weiter. Das ist die Station 37. Ein Deckenkran schiebt dort gerade Schritt für Schritt das letzte Heckstück an das schon weitgehend zusammengebaute Flugzeug heran. Unterstützt wird der Vorgang von Mitarbeitern, die auf der gelben Arbeitsbühne stehen und per Hand die „Hecktüte“ vorsichtig an den Rumpf heranführen.
Das Teil kommt aus Süddeutschland und beinhaltet das Hilfstriebwerk (APU), das Strom und Druckluft produziert und mit dem später das Triebwerk angelassen wird. Das aus Getafe kommende Höhen- und das aus Stade stammende Seitenleitwerk waren zuvor schon an der Station montiert worden. Wie die Flügelspitzen ist auch das Seitenleitwerk schon im Kundendesign lackiert.
In der Maschine beginnt der Einbau von Seitenverkleidungen, den Handgepäckfächern und des Fußbodens. Leitungen für die Hydraulik und Treibstoff werden verlegt, die Flügel werden angeschlossen und verkleidet.
In Halle 9 werden schon umfassende Tests der Systeme gemacht
„Zudem fangen wir an, ganz viel an dem Flugzeug zu testen“, sagt Holtrup. „Ist das Hydrauliksystem geschlossen? Sind die Treibstoffleitungen dicht? Funktionieren Pumpen und Landelampen? Auch erste Tests im Cockpit machen wir.“
Schließlich geht es zum letzten Bauplatz in der Halle, der Station 35. Die Hauptkomponenten sind nun am Flugzeug dran, aber die Klappen für das Hauptfahrwerk werden noch angebaut. Das Testen geht weiter, zum Beispiel beim Drucktest. „Alle Türen werden geschlossen. Wir geben Druckluft in die Kabine und schauen, ob sie dicht ist. Damit wird der Überdruck in der Kabine beim Fliegen simuliert“, sagt Holtrup. Das hydraulische System wird in Betrieb genommen und auf Herz und Nieren geprüft.
Die Sitze kommen erst nach der Endmontage in das Flugzeug
Im Inneren wird weiterhin fleißig an der Kabine gewerkelt. Die Seitenwände sind nun fertig, die Handgepäckfächer auch. Für die Passagiere wesentliche Elemente fehlen aber noch. „Die Sitze kommen in einer nachgelagerten Station ins Flugzeug“, sagt Holtrup.
Das liegt auch daran, dass die in Hamburg montierten Flugzeuge immer komplexere Kabinen erhalten. Zwar wird die gesamte A320-Familie in der Hansestadt gebaut, aber der Anteil am mit 44,50 Meter Länge größten Familienmitglied A321 ist besonders hoch.
Seit einigen Jahren wird der Flieger schon als LR-Version angeboten, der dank eines Zusatztanks für längere Strecken genutzt werden kann. In diesem Jahr startet nun die Serienfertigung des A321XLR, der dank eines fest eingebauten Tanks im Frachtraum sogar bis zu 8700 Kilometer nonstop fliegen kann. Das ermöglicht Langstreckenflüge wie zum Beispiel von Hamburg nach New York.
Bei Airbus in Hamburg werden komplexe, zeitaufwendige Kabinen eingebaut
Auf solchen Flügen bieten die Airlines ihren Passagieren gern nicht nur die Holzklasse an, sondern auch eine höherwertige Ausstattung mit mehr Business- oder gar First-Class-Sitzen. „Die komplexeren Kabinen brauchen mehr Zeit in der Montage“, sagt Holtrup.
- Airbus will bald vier bis fünf Flieger pro Tag ausliefern
- Airbus A321XLR – neuer Hoffnungsjet made in Hamburg erhält Zulassung
- Airbus bereitet Auslieferung von Hoffnungsflieger vor: Was hier anders ist
Während die Economy-Sitze normalerweise im Gegensatz zu den Küchen und Toilettenblöcken durch die Türen passen, müssen die First-Class-Sitze zunächst auseinander- und in der Maschine wieder zusammengebaut werden. Sie schon an Station 42/43 hereinzuschieben, ist aber keine Option.
15 Tage verbringt der A320-Flieger in der Halle 9
Erstens wird erst im späteren Verlauf der Teppich verlegt, auf dem die Sitze stehen. Zweitens wäre es im Flieger dann für die Monteure zu eng, drittens könnten sie beim Arbeiten die Sitze beschädigen. Das Prozedere treibt die Arbeitsstunden dennoch nach oben.
Apropos Zeit: Die Zeit, die ein Flieger in der Endmontagelinie verbringt, ist verhältnismäßig kurz. „Wir brauchen 15 Tage von den ersten Arbeiten in der Halle 9 bis das Flugzeug aus ihr hinausrollt“, sagt Holtrup – Hochzeit inklusive.