Eine Kleinstadt, die niemals schläft: Wir haben Menschen und Maschinen im Werk Finkenwerder rund um die Uhr beobachtet.
Eine Feuerwehr, ein Ärztezentrum, ein Hafen, drei Buslinien: Das Airbus-Werk auf Finkenwerder verfügt über die Infrastruktur einer Kleinstadt – mit eigenem Flughafen. Täglich kommen 16.000 Beschäftigte in das Werk des Flugzeugbauers, dessen Areal die Fläche von 340 Fußballfeldern einnimmt und in dem rund um die Uhr und an 365 Tagen im Jahr gearbeitet wird.
Doch was geschieht eigentlich bei Airbus nachts um halb eins? Wie montiert man an einem A321 die Flügel? Und wer sorgt dafür, dass im frischen Lack einer neuen Maschine keine Fliege kleben geblieben ist? Die 24-Stunden-Reportage von Wolfgang Horch (Text) und Michael Rauhe (Fotos).
Die Lackierer
0.44 Uhr In einer kleinen Halle der Lackiererei sind auf einem Seitenleitwerk für die A320-Familie mit blauem Band die Ränder des Logos von Sri Lankan Airlines markiert. Orange, Rot, Grün sollen die Abschnitte später aussehen. „Jedes Feld wird separat vorbereitet und jede Farbe später einzeln lackiert“, sagt Oliver Dettmar. Er setzt die Kreppbandrolle an, drückt ein Stück fest und reißt es ab. Bahn für Bahn. Von Farbe ist nichts zu sehen. Noch knapp zwei Stunden werden er und sein Kollege Torsten Stelljes mit Kleben, Schleifen und Reinigen beschäftigt sein. „80 bis 90 Prozent unserer Arbeitszeit verbringen wir mit Abkleben“, sagt Kollege Markus Smeddinck. Je nach Logo brauchen sie drei bis sechs Tage für ein Seitenleitwerk.
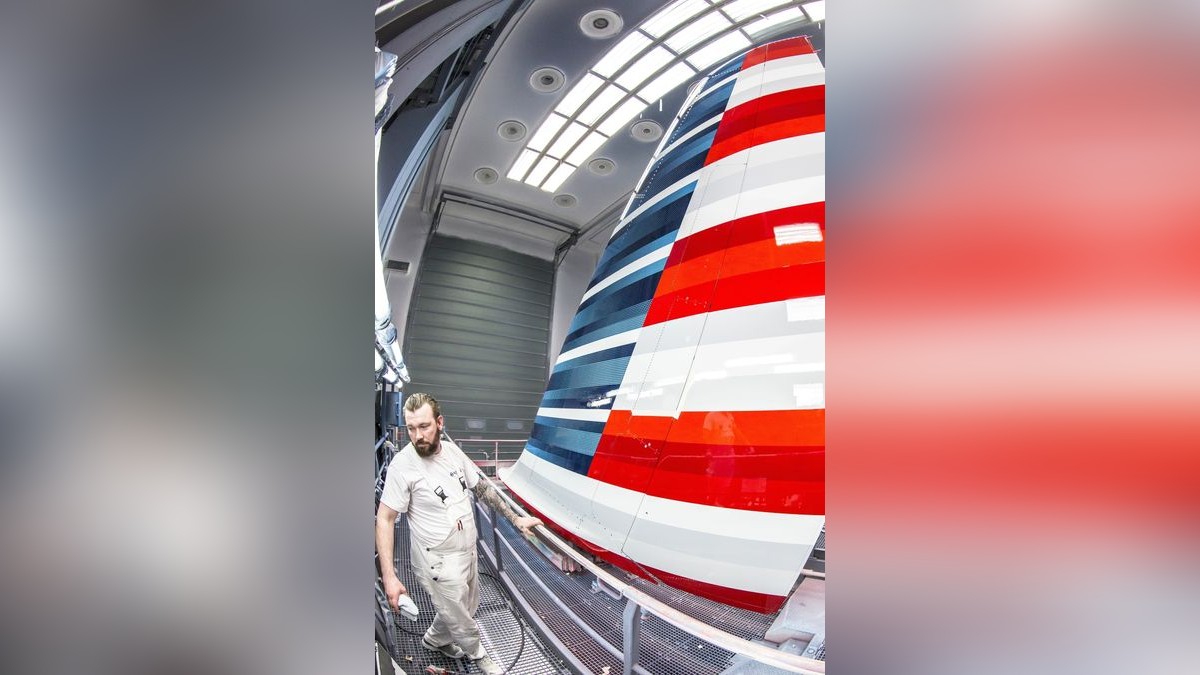
0.56 Uhr In einer benachbarten Halle sprüht Steffen Kröger Wasser auf ein eigentlich fertiges Seitenleitwerk von American Airlines. Dann setzt er die Schleifmaschine an. Eine Fliege hat sich im frisch lackierten Teil verewigt. „Ich schleife das jetzt plan, und dann wird das aufpoliert“, sagt Kröger. Er benutzt verschiedene Körnungen vom 600er- bis zum 6000er-Papier. Zehn bis 15 Minuten braucht er für eine Stelle. Als Nächstes ist eine Laufnase dran. „Bei elektrostatischen Lackierungen zieht es den Lack mehr zu den Schrauben als zu der Klappe aus Kohlenfaserstoff. Dann entstehen schon mal die Nasen“, sagt Kröger.
2.21 Uhr „Alle Mann auf die Plätze“, gibt der Teamleader in Halle 11 das Kommando. Es ist einer der sechs großen Hangars, in denen Flugzeuge lackiert werden. Ein A320 bekommt seine Grundschicht, den Primer. „Das riecht wie im Fischladen“, sagt Smeddinck. Der Mittelstreckenjet wird von Arbeitsbühnen aus Metall eingerahmt. Von vier Ebenen aus arbeiten jeweils zwei Lackierer. Sie sind in weiße Schutzanzüge eingepackt und tragen Atemschutzmasken. Hinter sich ziehen sie zwei Schläuche. Der eine führt zur Spritzpistole und beinhaltet den Primer. Der andere führt zur Maske und enthält Atemluft.
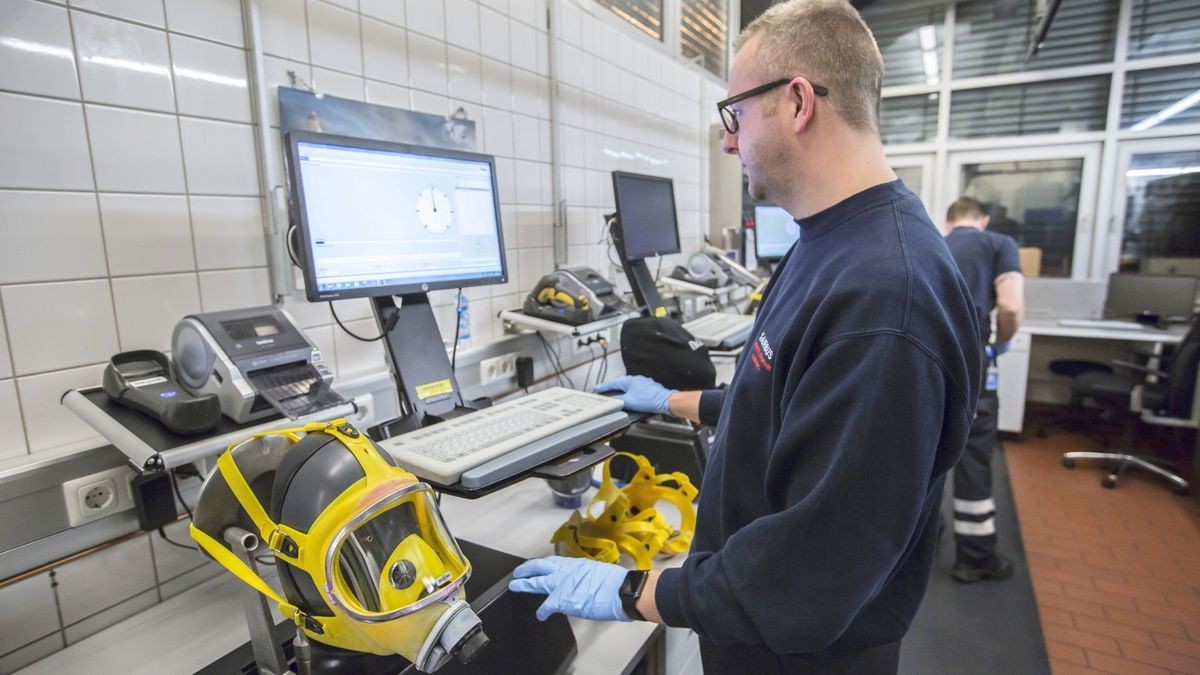
Das oben auf der Bühne stehende Zweierteam fängt an. Links und rechts vom Flugzeug schwingen sie die Spritzpistole in ausschweifenden Bewegungen am Rumpf entlang. Es geht vom Cockpit nach hinten zum Heck. Als die oberste Crew rund zwei Meter geschafft hat, steigt das zweite Team ein, auf der Fensterebene. „Sie bestimmt das Tempo, weil sie am meisten Fläche hat“, sagt Smeddinck. Es folgt das dritte Tandem und als letztes das am Boden unter dem Rumpf arbeitende Duo. Der Jet wird versetzt lackiert, sonst stünden die unteren im von oben fallenden Sprühnebel.
Aus den Lautsprechern dröhnt Herbert Grönemeyers Hit „Kinder an die Macht“ – sein Titel „Flugzeuge im Bauch“ würde besser passen, denn die Identifikation mit der Luftfahrt ist bei vielen Mitarbeitern hoch. Rund 40 Minuten dauert das Auftragen des Primers. Vier bis sechs Schichten Lack bekommt ein Flugzeug, mehr als 200 Liter Farbe haften letztlich am Rumpf. „Wir brauchen vier bis sieben Tage für ein Flugzeug“, sagt der stellvertretende Paintkoordinator Dennis Wohlers. Rund 700 Beschäftigte sind in der Lackiererei tätig. Sie arbeiten rund um die Uhr, jeden Tag bis auf die Feiertage.
Die Transport-Crew
3.24 Uhr Andre Rahmelow drückt an einem Bedienpult auf einen weiß leuchtenden Knopf mit der Aufschrift „Bewegung“. Ein Alarmsignal ertönt, ein orangefarbenes Warnlicht blinkt in der Halle 2/6, in der am Airbus-Jet gearbeitet wird, dem A330. Dann schiebt sich das Rumpfsegment des Langstreckenjets langsam nach vorn. Mit vier Beschlägen befestigt, hängt in etwa 2,50 Meter Höhe die Sektion 13/14 in einem Transportautomaten, der „Laufmaschine“. Sie ist durch die Strukturmontage durch und soll nun etwa 40 Meter weiter vorn den Korrosionsschutz erhalten. Sechs Minuten dauert die Fahrt. Verantwortlich dafür ist die insgesamt 110 Mitarbeiter starke Takt Crew. „Wir bewegen alles, was keine Räder hat“, sagt Industriemeisterin Saskia Hilmer, die eine von drei Frauen im Team ist und die Nachtschicht leitet. „Und wir sind auf dem ganzen Gelände unterwegs.“
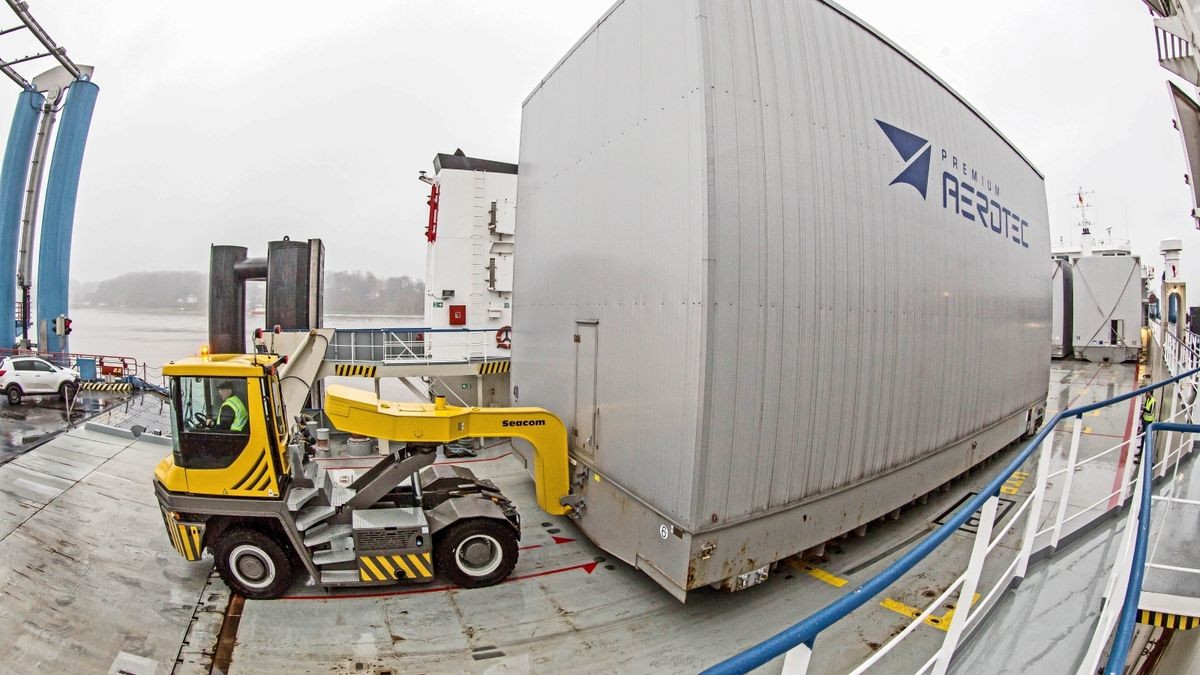
Die Feuerwehr
4.04 Uhr In der Werkstatt für Atemschutzmasken trägt Feuerwehrmann Dennis Jednat blaue Gummihandschuhe, greift sich eine gereinigte Atemschutzmaske, scannt sie in den Rechner ein und setzt einen Stopfen aufs Ventil. Dann zieht er die Maske über einen schwarzen Silikonkopf, schaut, ob die innere und äußere Dichtlippe fest anliegen und gibt Druck auf den Atemschutz. In einer Minute darf die Maske nicht mehr als ein Millibar den Druck verändern. „Bei Bedarf machen wir kleinere Reparaturen wie Glasscheiben oder ein Kopfband austauschen selbst“, sagt Jednat. Die Maske besteht die Prüfungen. Jednat nimmt den Stopfen heraus, packt sie in eine Tüte und versieht sie mit einem Etikett. 1200 Stück, die vor allem in der Lackiererei eingesetzt werden, sind im Werk im Umlauf.
„Das Reinigen der Masken ist unser Hauptgeschäft“, sagt Thomas Woitera, der als Schichtführer Chef von 14 Mann ist: „Unsere Werkstatt ist 365 Tage im Jahr geöffnet.“ Zum Tagesgeschäft gehört aber auch das Warten der Feuerlöscher oder die Schulung von Airbus-Mitarbeitern. Im vergangenen Jahr wurde in 88 Kursen 1200 Beschäftigten vermittelt, wie sie zum Beispiel richtig mit der Schutzausrüstung umgehen. Und im Winter räumt die Feuerwehr die Start- und Landebahn von Schnee und Eis.
4.25 Uhr In der Einsatzleitzentrale hat Dieter Lengsfeld mehrere Bildschirme fest im Blick. „Hier laufen alle Fäden zusammen“, sagt der Einsatzleiter. „Vom Ausfall einer Maschine über die Störung eines Rauchmelders im Flugzeug bis zu den Wetterdaten und einem Alarm am Zaun.“ 800 Kameras an den Zäunen überwachen die Werksgrenzen. Und von 18 bis 6 Uhr laufen auch noch alle Anrufe für die Telefonzentrale von Airbus in der Einsatzleitstelle auf. Plötzlich erscheint ein roter Streifen auf einem Monitor: eine Alarmmeldung. Was Schlimmes? Ruhig klickt sich Lengsfeld mit der Maus in die Meldung hinein. „Da hat irgendeiner eine Tür aufgemacht, die alarmgesichert ist.“

Ein Kollege fährt raus und schaut sich vor Ort um. Rund 2500 Einsätze im Jahr, davon 600 Rettungseinsätze, absolvieren die 65 Mitarbeiter. Mehrmals täglich werfen sie sich in voller Montur in die Feuerwehrautos. „Wenn wir Flugbetrieb haben, sitzen wir in Einsatzkleidung auf den Fahrzeugen“, sagt Woitera. „Wir müssen innerhalb von drei Minuten an jedem Punkt der Start- und Landebahn sein und die Hälfte unserer Löschmittel ausgebracht haben.“ Und die drei Flugfeldlöschfahrzeuge fassen immerhin je 10.000 Liter Wasser, 1000 Liter Schaum, 500 Kilo Pulver und 240 Kilogramm Kohlendioxid zum Flammenersticken. Im wahrsten Sinne des Wortes das Highlight des Fuhrparks ist das Teleskopfahrzeug. 54 Meter hoch reicht die Leiter – damit kommen die Retter locker bis an den Tower heran.
Der Tower
6.15 Uhr Seit einer Viertelstunde hat der zweite Flughafen der Stadt geöffnet, Hamburg Finkenwerder Airport mit dem Kürzel XFW. Im Tower auf der Elbinsel überwacht Fluglotse Michael Udowenko das Geschehen. „Kontrollwagen, Position halten, Charterlandung“, weist er per Funk den Fahrer des Autos an. Dann sieht man die Lichter des Airbus A319 von Germania. Montags bis freitags gibt es zwischen den beiden wichtigsten Airbus-Standorten einen Shuttle-Verkehr. Jeweils morgens und abends fliegt eine Maschine von Toulouse nach Hamburg und eine in die andere Richtung. Kurz zuvor ist die Maschine in Fuhlsbüttel gestartet, fliegt über dem Tower eine Kurve in Richtung Moorburg, dreht über Ohlsdorf, fliegt über der Elbe heran und landet. „Kleinschlepper und Schlepper 12, Ihr könnt jetzt beide queren, ohne Abmeldung.“ Jedes Fahrzeug, das über die Start- und Landebahn gefahren wird, muss am Tower angemeldet werden. Airbus braucht den bis 22 Uhr geöffneten Flughafen, damit Maschinen zu Test- und Auslieferungsflügen abheben können. Die Zahl der Flugbewegungen ist mit 25 bis 30 pro Tag überschaubar.
Der Werkshafen
7.09 Uhr Wind peitscht den Regen ins Gesicht. Hafenkapitän Uwe Falldorf betritt im Werkshafen das Schiff „Kugelbake“ und öffnet die Tür eines Transportcontainers, der die Ausmaße eines großen Einfamilienhauses hat. „Vom Volumen würden circa 17 normale 20-Fuß-Container in einen A380-Container hineinpassen“, sagt Falldorf. Tatsächlich befinden sich Rumpfsegmente in den insgesamt drei Boxen. Einmal für das größte Passagierflugzeug, den A380, und je einmal für die Langstreckenjets A330 und A350. Ein Mitarbeiter der Takt Crew kommt mit einem Truck angefahren.
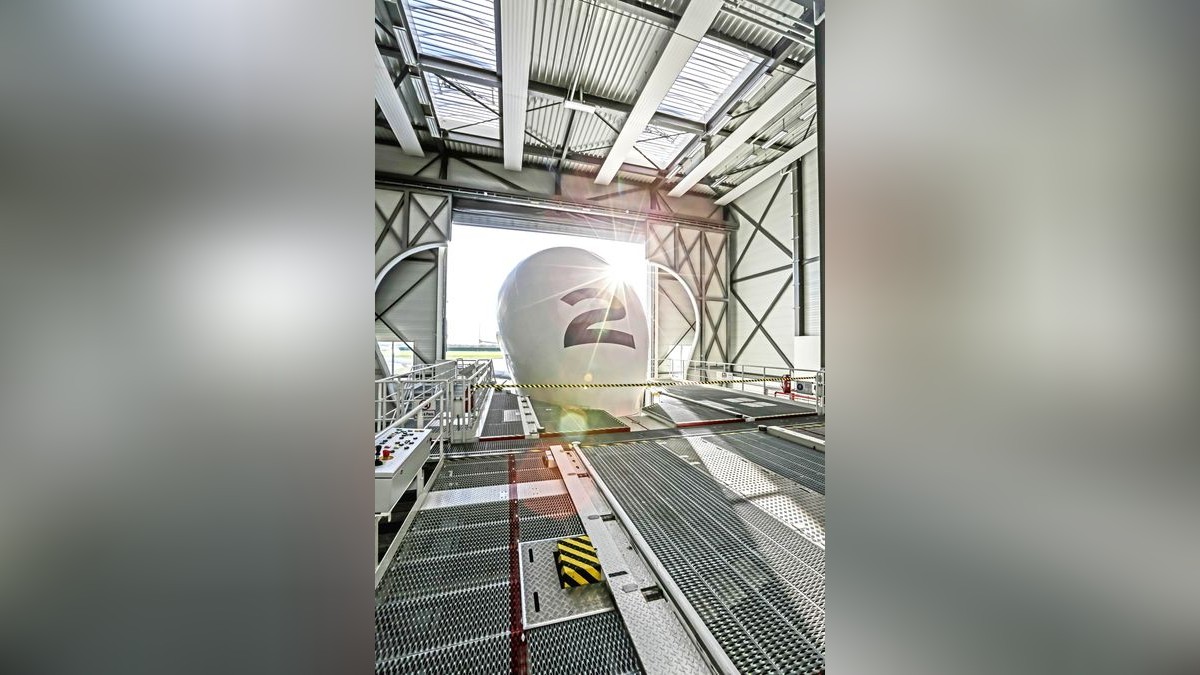
„Der Fahrer setzt den Schwanenhals ein und drückt damit den Transportcontainer hydraulisch hoch“, sagt Falldorf. Das sieht man den Reifen an, unter der Last von rund 80 Tonnen wölben sie sich nach außen. Dann ziehen sie die Box von Bord des „Open-Deck-Carriers“ an ihren Stellplatz auf dem Gelände. Flankiert wird der Lastzug links und rechts von einem Mitarbeiter der Takt Crew, denn das Monstrum ist so breit, dass der Fahrer Orientierungshilfe braucht.
Zwei- bis dreimal die Woche pendelt die knapp 80 Meter lange und acht Meter breite „Kugelbake“ zwischen Hamburg und Nordenham, wo die Airbus-Tochter Premium Aerotec Rumpfsegmente fertigt, die auf Finkenwerder ihr Innenleben erhalten. Fünf- bis sechsmal pro Woche kommen mit einer Flussfähre Seitenleitwerke aus Stade. Einmal pro Woche wird ein Bausatz für den A320 zum Containerterminal Tollerort gebracht. Dort werden die Teile nach China verschifft, um im Airbus-Werk in Tianjin endmontiert zu werden. Auch für den Standort Mobile/USA werden A320-Bausätze verladen. Und mit drei Schiffen gibt es einen Liniendienst nach Frankreich für A380-Teile.
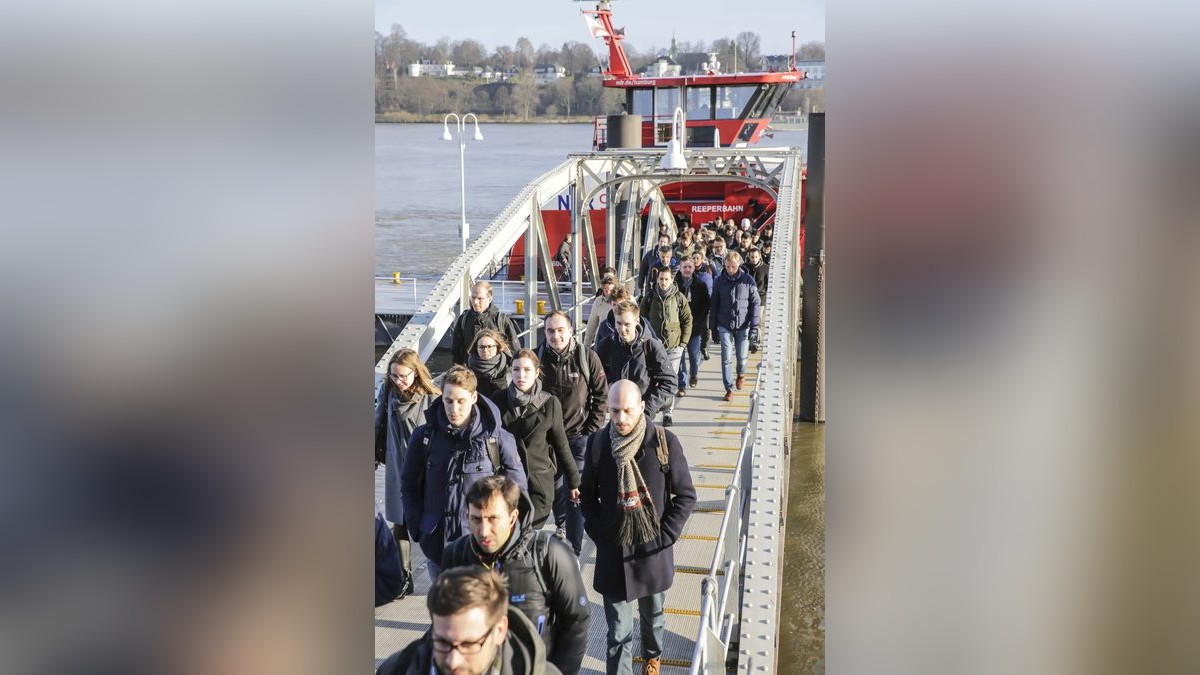
Der Fähranleger
8.03 Uhr An einer anderen Stelle der Elbe kommt die Hadag-Fähre „Reeperbahn“ am Schiffsanleger an. Die Linie 68 verbindet Nord- und Südufer. Zwischen 5.30 und 9.30 Uhr sowie zwischen 12.30 und 22.45 Uhr verkehren die Fähren. Von dort gehen die Mitarbeiter zu Fuß zum Arbeitsplatz, steigen aufs Rad oder nehmen eine der drei Buslinien.
Die A380-Auslieferung
9.21 Uhr Im A380-Auslieferungszentrum hält Kundenbetreuerin Mar Bustamante Rocabruna gerade ein Briefing ab. „Das ist kein Drama, aber wir müssen das Teil justieren“, sagt die Maschinenbauingenieurin zu den Repräsentanten der Fluglinie Etihad, David Hamilton und Dominique Lucbernet. An einer Anzeige für das Anschnall- und Mobilfunkzeichen gibt es einen Lichtspalt, der nun beseitigt werden soll. Es ist der neunte A380, den die Airline aus Abu Dhabi bekommt. Rund 500 Passagiere passen auf Unter- und Oberdeck in die laut Listenpreis 436,9 Millionen Dollar teure Maschine – hohe Rabatte sind üblich.
Das Prozedere dauert acht Tage und beginnt mit Cockpitchecks, dem Anlassen der Motoren im Leerlauf und einer intensiven Sichtprüfung von außen und innen. Am zweiten Tag steht ein drei bis vier Stunden dauernder Flug an, bei dem die Piloten des Kunden mit an Bord sind. Treibstoff-Verbrauchswerte werden ebenso wie das Entertainmentsystem in der Luft gecheckt. Es folgen bis zu vier Tage für Nacharbeiten und gegebenenfalls einen zweiten Flug. Am siebten Tag gibt der Kunde seine Unterschrift, dass er die Maschine technisch akzeptiert. „Dann ist das Flugzeug fertig für den Verkauf“, sagt Jörn Senkspiel, der das A380-Auslieferungszentrum leitet. Am achten Tag müssen die Banken das Geld freigeben und auf das Airbus-Konto überweisen. Dann erfolgt der sogenannte transfer of title, dem Kunden gehört der Jet – und er kann zum Überführungsflug abheben.
Die Küche
10.32 Uhr Aus einer Wanne mit 97 Grad Celsius heißem Wasser hebt Küchenchef Marco Schaalo einen Bottich mit Reis, stellt ihn in den Rollwagen, packt Abtropfwannen darunter und schiebt ihn in den Kühlraum. „Der Reis wird auf den Punkt gekocht, dann auf unter vier Grad Celsius schockgekühlt und später an der Ausgabe gefinished“, sagt Küchendirektor Titiaan Stuurmann. Die Vorbereitungen für die heiße Phase in der Kantine Elbblick sind weitgehend abgeschlossen. Sie ist von 10 bis 2 Uhr nachts geöffnet, bietet 800 Sitzplätze und ein gutes Dutzend Gerichte zur Auswahl. Die beliebtesten Essen sind Klassiker. „Currywurst und Spaghetti Bolognese sind nach wie vor der Renner“, sagt Stuurmann.
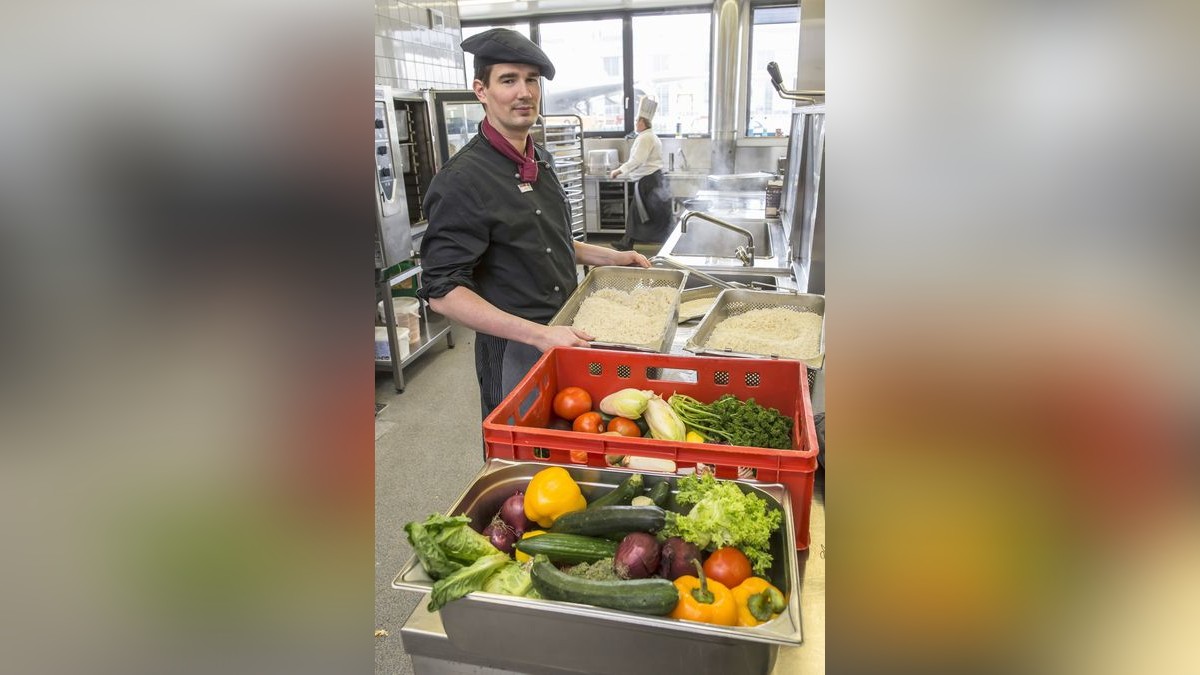
Bis zu 23.000 Kunden gibt es pro Tag. „Bis 13 Uhr haben wir 80 Prozent unserer 13.000 Hauptgerichte pro Tag verkauft“, sagt Michael Pokorski. Er ist Projektleiter beim Caterer Aramark, der die fünf Restaurants auf dem Werksgelände plus die Kantinen im Werk Stade und in der Ersatzteilversorgung in Groß Borstel bestückt. Seine 200 Mitarbeiter liefern zudem Kaffee und Kekse in die 330 Meeting-Räume, bestücken die mehr als 270 Automaten mit Kalt-/Heißgetränken, Suppen und belegten Brötchen und verkaufen in sechs Shops Backwaren, Getränke, Süßes und Zeitungen.
Das Medizinpersonal
12.47 Uhr Im Gesundheitszentrum nimmt die arbeitsmedizinische Assistentin Marlena Noack bei einem Mitarbeiter einen Augencheck vor. Er bekommt am Computerbildschirm Bilder aus bunten Punkten zu sehen. „Ich kontrolliere das Farbsehen. Das ist besonders für Elektriker wichtig“, sagt Noack. „3, 8, 72, 29, 26“, nennt der Mitarbeiter die richtigen Zahlen. Vorsorgeuntersuchungen sind eine der Aufgaben für die zwölf Personen im Gesundheitszentrum. Zudem gehört für die sieben Ärzte die Aufklärung über gesundheitliche Risiken bei Tätigkeiten wie Lackieren dazu, das Erstellen von Verhaltensempfehlungen für Dienstreisen und das Krisenmanagement zum Beispiel bei Unfällen.
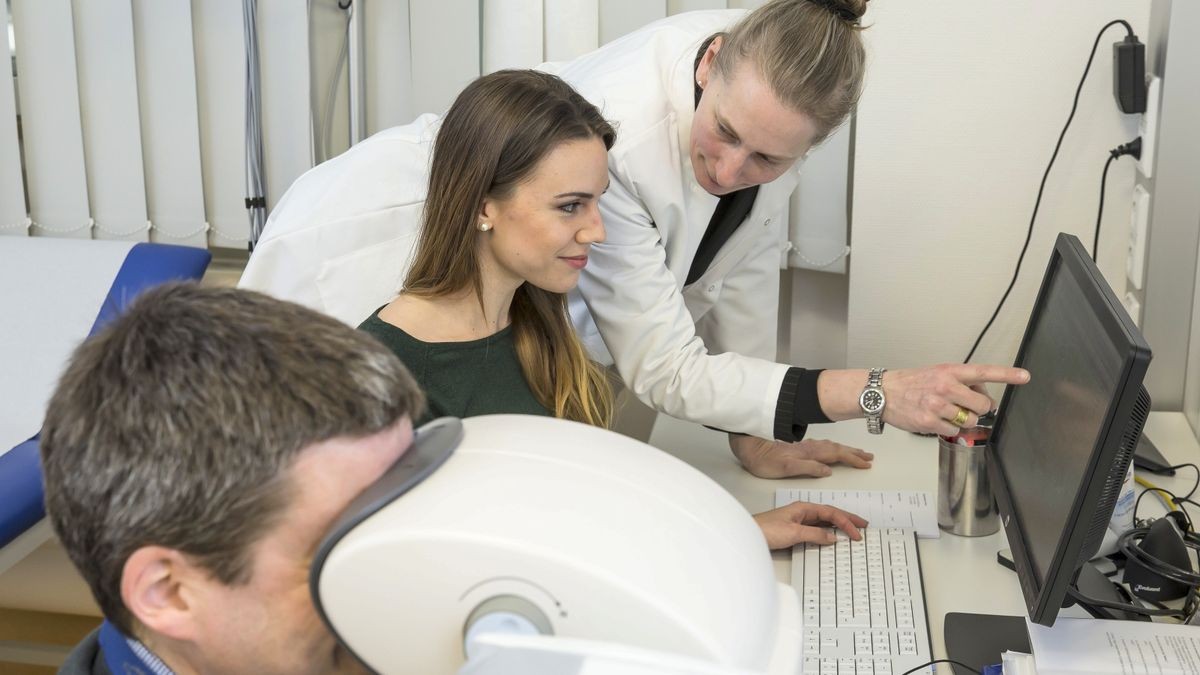
„Montags bis freitags übernehmen wir von 7 bis 15.30 Uhr die notärztliche Versorgung am Standort“, sagt Regina Loibl, Fachärztin für Innere Medizin und Arbeitsmedizin: „In der Regel sind es ein bis zwei Einsätze im Monat.“ Unterzuckerung, Krämpfe bei Epileptikern oder mal ein festgebohrter Finger, weil der Arbeiter die Bohrmaschine mit Handschuhen angefasst und damit in den Bohrer gekommen ist. Loibl: „Insgesamt ist das Unfallgeschehen am Standort niedrig. Die häufigsten Unfallursachen sind aber Stolpern, Rutschen, Stürzen.“
Rund 10.000 Kontakte mit Beschäftigten gibt es pro Jahr, Tendenz steigend. Zu den typischen Beschwerden gehören Hautausschlag, Kopfschmerzen oder Grippesymptome. Patienten mit Rücken- oder Knieschmerzen erhalten auf Kosten des Arbeitgebers Rezepte für Krankengymnastik. Zwei Physiotherapeuten des Reha-Zentrums Harburg sind jeden Tag zum Fitmachen der Beschäftigten, deren Durchschnittsalter übrigens bei 43 Jahren liegt, auf dem Gelände. Bei seelischen Problemen wird mit der Asklepios Klinik Harburg kooperiert.
Die Flugzeugtester
14.13 Uhr Im Cockpit eines neuen A320 für Air Arabia gibt Thomas Heidemann in den Computer als Abflug- und Zielflughafen Finkenwerder ein, als Alternative Fuhlsbüttel. Er tippt die Flugnummer AIB614B ein. Die ersten drei Buchstaben stehen für Airbus, die drei Ziffern stammen aus der Seriennummer 7614 der A320-Familie, und das B steht für den Zweitflug der Maschine. Heidemann vereint zwei Jobs in einer Person. Er ist Pilot und Flugtestingenieur. Jeder neue Jet, den Airbus ausliefert, wird von ihm oder seinen 40 Kollegen auf Herz und Nieren getestet. Zunächst werden am Boden die Systeme und die Triebwerke gecheckt und schließlich ein Startabbruch geprobt. „Wir simulieren einen normalen Start, legen aber bei 80 Knoten eine Vollbremsung hin“, sagt Heidemann. Die aufgezeichneten Daten werden analysiert. Und in der Kabine schaut man, ob alle Verkleidungen, Sitze und Schrauben noch festsitzen. Erst dann hebt der neue Jet ab. Zwei Testpiloten, ein Flugtestingenieur und ein Groundtestingenieur sind beim Erstflug dabei.
Richtige Härtetests werden zuvor bei den Jungfernflügen neuer Typen gemacht. „Wir gehen in der Luft an alle Limits heran, machen viele Dinge, die man normalerweise mit einem Flugzeug nie machen würde“, so Heidemann. Der Jet wird in extreme Schräglagen versetzt, nimmt fast Überschallgeschwindigkeit an, um später bei weniger als 100 Knoten einen Strömungsabriss zu provozieren. Die Triebwerke werden ausgeschaltet.
Beim Erstflug wird etwa zwei Stunden lang ein detailliertes Programm absolviert. In der Kabine wird vor allem nach Undichtigkeiten an den Türen Ausschau gehalten, weil diese häufig Krachmacher sind, und das Luftdrucksystem getestet. „Es kann auch schon mal sein, dass es einen furchtbaren Knall tut und eine Niete rausfliegt“, sagt Heidemann. „Aber wir haben selten schwerwiegende Probleme im Flug.“ Wenn es keine Störung gibt, ist der Jet auslieferbar. Dann kommt es zum Zweitflug mit einer Delegation der Fluglinie. 90 Minuten ist der Air-Arabia-A320 in der Luft, es geht Richtung Rügen-Berlin – und zurück in die Hansestadt. Heidemann: „Wir sind die einzigen Piloten, die viel fliegen, aber nirgendwo hinkommen. Wir fliegen nur Finkenwerder–Finkenwerder.“
Der Standortleiter
15.33 Uhr Im Büro von Standortleiter Georg Mecke tagt die Stabsrunde. Erstes Thema: die Arbeitssicherheit. 2016 gab es 914 Ausfalltage von Mitarbeitern, weil sie gestolpert, gerutscht oder gestürzt sind. Assistent Maximilian Fuß kann dem Chef eine gute Nachricht verkünden. In den ersten beiden Monaten hat sich die Unfallrate etwa halbiert. „Eine sichere Arbeitsumgebung ist für uns essenziell“, sagt Mecke und will mit neuen Kampagnen die Rate senken.
Fabian von Gleich, am Standort verantwortlich für Strategie und Entwicklung, berichtet über die Fortschritte des geplanten Dienstleistungszentrums vor den Werkszäunen. Auf gut 20.000 Quadratmetern sollen Läden, ein Hotel, ein Fitnessstudio entstehen – und ein neues Besucherzentrum. Pro Jahr schauen sich 60.000 Interessierte an, wie Jets montiert werden. „Künftig peilen wir 100.000 Besucher an“, sagt von Gleich. Sie sollen sich künftig auch über Geschichte und Zukunft des Fliegens informieren können. In zwei Jahren könnte der Bau starten, zurzeit spricht man mit den Anwohnern. Man lege viel Wert auf eine gute Zusammenarbeit und berücksichtige die Anliegen der Nachbarn, sagt Mecke. Er ist die Schnittstelle zwischen innen und außen und wird auch als Bürgermeister von Airbus in Hamburg bezeichnet. Warum? „Wir haben jeden Tag 16.000 Menschen hier“, sagt Mecke: „Das ist wie eine Kleinstadt.“
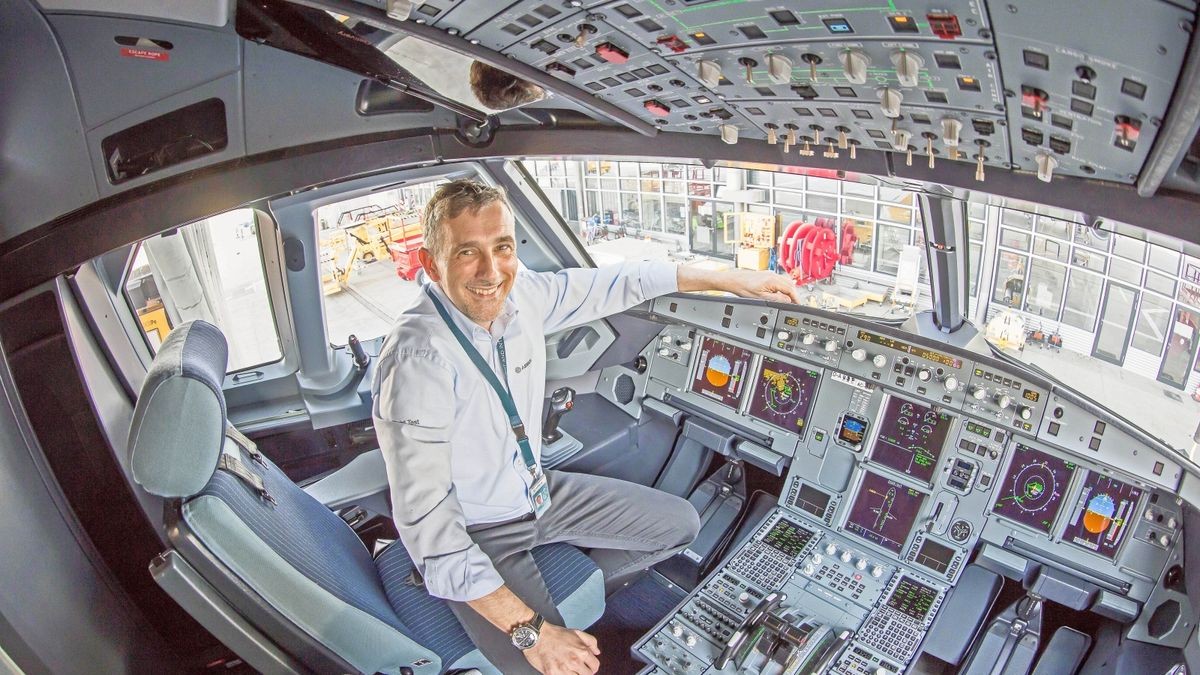
Zum Abschluss der Runde stellt Projektleiter Matthias van Hove einen neuen Film des Innovationsmanagements vor. Durch die Ideen der Mitarbeiter seien auf Finkenwerder im vergangenen Jahr 1,8 Millionen Euro gespart worden. Der Clip soll den Beschäftigten Lust auf weitere Vorschläge machen.
Die Beluga-Belader
16.37 Uhr Ground Coordinator Birger Thomßen hat in einer Halle die größte Klappe von Airbus vor sich: die geöffnete Ladeluke des Frachtfliegers Beluga. Thomßen drückt einen Hebel auf der Fernbedienung und fährt die Rumpfsektion eines A330 hinein. „Ich mache alles bis zur Beluga, dann übernimmt der Flugingenieur“, sagt Thomßen.
Im Schnitt viermal pro Tag laden er und seine Kollegen Jetteile aus und ein. 90 Minuten haben sie, dann muss der Flieger zur Startbahn rollen. Rund 2500 Flügel, Cockpits und Rümpfe transportieren die fünf Belugas pro Jahr zwischen elf Standorten in Europa. Das ist der historisch gewachsenen arbeitsteiligen Airbus-Welt geschuldet. Hamburg ist das Kompetenzzentrum für die Kabine, in Saint-Nazaire werden die Cockpits gebaut – entsprechend fährt Thomßen als Nächstes ein leeres Gestell für die Flugzeugführerkabine in den Bauch der Beluga. Im Cockpit bereitet Beluga-Pilot Fred Lafaurie den Abflug in die französische Atlantikstadt vor. „Wir haben heftigen Gegenwind und brauchen zwei Stunden Flugzeit“, sagt Lafaurie. Ein Gewittersturm erwartet ihn in Saint-Nazaire. Auf Finkenwerder hebt er 30 Minuten später bei Sonnenschein ab.
Die Innovationstreiber
18.13 Uhr In einem Besprechungszimmer hält Peter Sander einen Halter für eine Cockpittür-Trennwand, der zuvor einem Belastungstest mit dem 16-Fachen der Erdbeschleunigung unterzogen wurde. „Der Apparat hat sich um einen halben Millimeter verzogen. Da müssen wir noch einmal einen Millimeter Titan draufpacken“, sagt Sander, der für die Entwicklung von Zukunftstechnologien zuständig ist, zu Mitarbeiter Matthias Radny. Das Besondere: Der Halter kommt aus dem 3-D-Drucker. Dabei werden Teile Schicht für Schicht aus Metallen wie Titan aufgebaut statt sie wie vorher aus einem Block zu fräsen. Die Vorteile: Es entsteht weniger Abfall. Die Teile sind in der Regel mindestens 25 Prozent leichter, was sich in geringerem Treibstoffverbrauch und Geldersparnis für die Airlines ausdrückt. Und mitunter wird die Arbeit erleichtert – so wie bei dem Halter für die Cockpittür. „Der Halter konnte so intelligent geteilt werden, dass er nur noch aus zwei Stücken besteht. Hiermit kann in der Montage viel Zeit gespart werden“, sagt Radny. Statt bis zu 16 Stunden brauchen die Arbeiter nun etwa 20 Minuten für den Einbau.
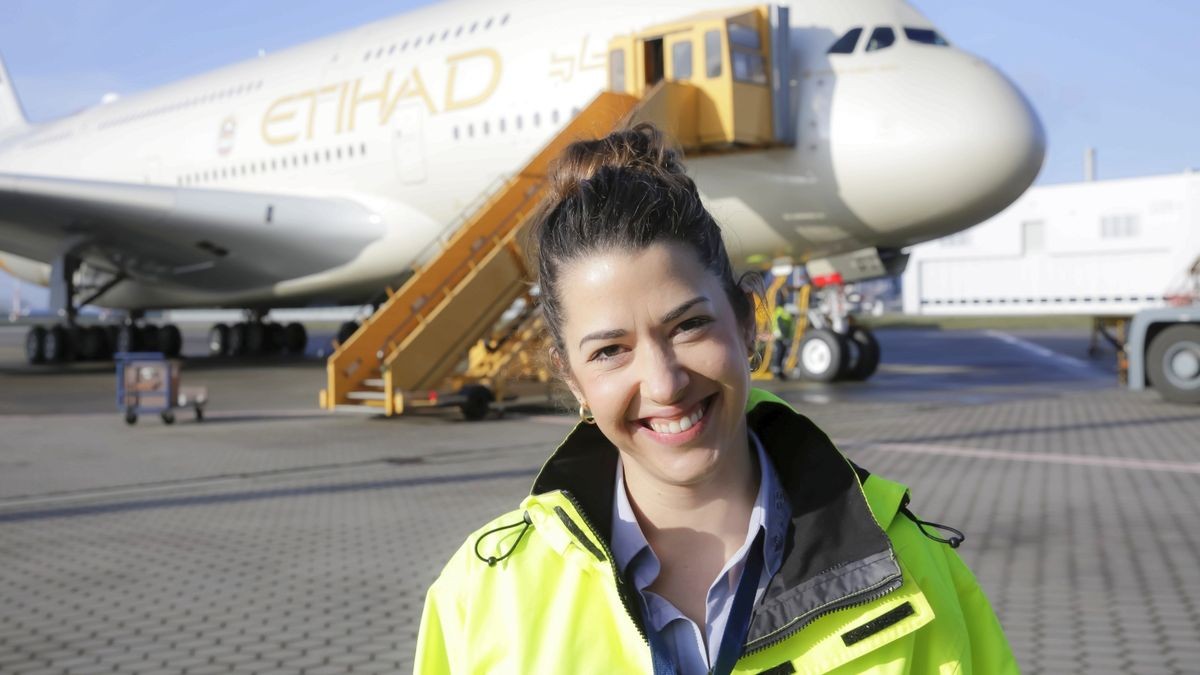
Hunderte Teile aus 3-D-Druckern fliegen schon, vor allem aus Kunststoff. Als Nächstes gehen metallene Steuerblöcke in die Flugtestphase. Sanders Team lernte schon von Schleimpilzen und Seerosen, versucht also Phänomene aus der Natur auf die Technik zu übertragen (Bionik). So vergleicht Sander die Adern und feinen Verästelungen einer Riesenseerose mit Spanten und Stringern – dem tragenden Gerüst in Jets. Durch das Bilden von Dreiecken bleibt die Pflanze stabil. Das Prinzip erwartet Sander bald in der Luftfahrt: „Im Jahr 2025/30 könnten wir ein bionisches Flugzeug bauen.“
Das Bodenpersonal
19.17 Uhr Ground-Support-Mitarbeiter Arne Segert winkt in der Dämmerung auf dem Vorfeld mit rot leuchtenden Sticks. Der Germania-Shuttle aus Toulouse ist gerade gelandet, auf Segerts Befehle bringt der Pilot die A319 in die Parkposition. Segert führt beide Sticks an der Seite nach oben – der Kapitän hält an. Triebwerke aus, Flugzeugtreppe ran, 144 Airbus-Beschäftigte steigen aus. Segert und seine Kollegen holen die Koffer aus dem Bauch der Maschine, packen sie auf einen Anhänger, ziehen ihn per Hand zum Band und legen die Koffer darauf.
Die Rumpfausstattung
21.31 Uhr Kai Kalmbach spielt Fangen – so sieht die futuristische Szenerie in der A350-Ausrüstungsmontage zumindest aus. Er steht in einer Rumpfsektion des Langstreckenjets, die mit Innenleben ausgestattet werden soll. Kalmbach hält in der Hand eine Spiegelkugel und wird von einem roten Laserstrahl auf der Brust getroffen. Dann fängt er den Strahl mit der Kugel ein und leitet ihn zu den Adaptern an den Messpunkten, die sein Kollege Marc Schröder zuvor an der Sektion befestigt hat. Das Lasermessgerät prüft, ob die Tonne – wie der Rumpfabschnitt genannt wird – gerade steht. Nach wenigen Sekunden rät der Computer: „Bitte an den Heißbeschlägen nachstellen.“ Schröder läuft zwei Treppen nach unten, senkt vorn und erhöht hinten den Druck mit einer Handpumpe um Millimeter. Danach prüft das Messgerät wieder. „Leveln der Sektion erfolgreich“, teilt der Rechner mit. Kalmbach: „Damit größere Bauteile einwandfrei montiert werden können, muss der Rumpf exakt gerade ausgerichtet sein.“
Wenn die Rumpfabschnitte für den A350 in die Halle 261 kommen, ist außer den tragenden Teilen nichts drin. An sechs Stationen erhalten sie ihr Innenleben. Rein kommen Isoliermatten, Fenster, Antennen, Fußböden, Türen und unzählige Leitungen für Elektrik, Klimaanlage, Frisch- und Abwasser. „Alles, was der Kunde nachher nicht mehr zu sehen bekommt, bauen wir ein“, sagt Stationskoordinator André Leuth. Nach zwölf Tagen in der Halle ist das Bauteil bereit für den Flug nach Saint-Nazaire, wo das Cockpit angebaut wird. Endmontiert werden alle A350 später in Toulouse.
Die Endmontage
23.07 Uhr Martin Schultz bohrt in Halle 14 Löcher in einen Flügel, macht jedes Bohrloch fettfrei und setzt eine Niete ein. Zwischendurch wechselt er immer wieder das Werkzeug. An diesem Bauplatz 40 wird Hochzeit gefeiert – so nennt man das Anbringen der rund vier Tonnen schweren Tragflächen an den Rumpf (in diesem Fall eines A321). Verkürzt könnte man sagen: Danach sieht das Flugzeug auch aus wie ein Flugzeug.
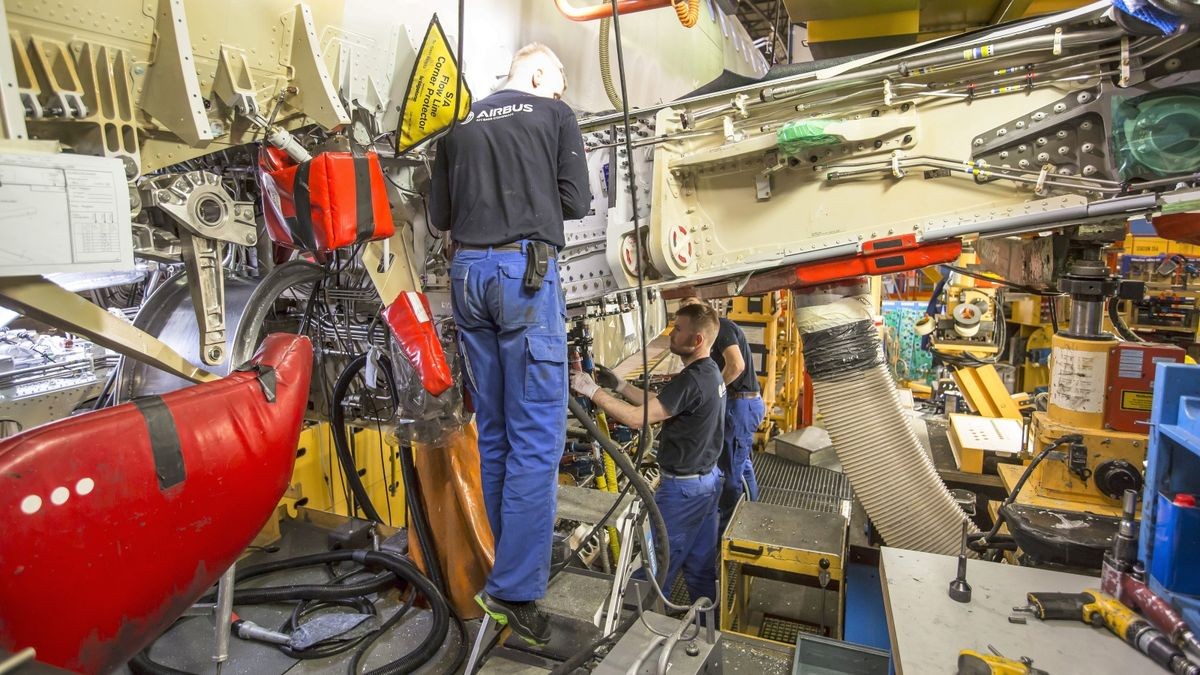
Im Inneren des Jets wird die Küchenmontage beendet und der Fußboden geschlossen, Cockpitmonitore, Toiletten und Verkleidungen werden angebracht. Draußen werden die Fahrwerke und die Pylone montiert, an denen die Triebwerke hängen. Es ist eine Vielzahl von Arbeitsschritten, die erledigt werden müssen. Deshalb wird an der Station an fünf Tagen die Woche rund um die Uhr gearbeitet – als einziger in der A320-Endmontage, die sonst im Zweischichtsystem erfolgt.
Das Flugzeugprogramm ist der Bestseller im Airbus-Portfolio. Schultz arbeitet an der Seriennummer 7667. Etwa die Hälfte der Maschinen ist made in Hamburg. Mehr als 5500 Jets sind in den Auftragsbüchern. Um der Bestellungen Herr zu werden, entsteht auf Finkenwerder eine vierte Endmontagelinie. Die Arbeit geht nicht aus – auch für Schultz in der Nachtschicht nicht, so Stationskoordinator Torsten Stöver: „Die Flügel hängen beim A321 an insgesamt 2198 Nieten. Er hat noch einige Stunden zu tun.“