Wetter. Die Deutschen Daniel Düsentriebs: VW, Mercedes, Siemens, Bosch und viele andere bekannte Marken, vertrauen den Tüftlern aus Volmarstein.
Sie sind Problemlöser, Grenzenverschieber und manchmal sogar Finanzcoaches. Sie setzen da an, wo andere Firmen resignieren. Das hat sie zu Weltmarktführern gemacht. Ein netter Titel, auf den aber gerade Chef und QASS-Firmengründer Ulrich Seuthe nicht unbedingt so viel Wert legt. Ihm geht es um viel mehr.
Grenzen werden verschoben
„Wer sich immer nur innerhalb der Regeln bewegt, hat zwar ein sicheres Leben, aber kommt nicht voran“, meint der Chef und lächelt. Natürlich gibt es auch für die Firma QASS die Regeln der Physik und der Mathematik, aber der Anwendung sind kaum Grenzen gesetzt - und wenn doch, müssen sie halt verschoben werden.
Alle Arbeitszeitmodelle vertreten
Über 60 Angestellte hat das Unternehmen, das erst 2001 gegründet worden ist. Darunter viele Werkstudenten und auch einige Teilzeitbeschäftigte. „Wir haben hier alle Arbeitszeitmodelle vertreten“, erklärt Prokurist David Müller. Dass so viele junge Menschen in dem Team arbeiten, liegt vor allem daran, dass „Studenten und Praktikanten hier nicht nur Kaffee kochen“, weiß Müller. Ein Beispiel ist Elias Wiebelitz. „Er hat schon mit zwölf Jahren während des Praktikums und bei der Erfinderwerkstatt für Kinder bei uns gearbeitet. Als Werkstudent kam er wieder und ist inzwischen Leiter unserer gesamten Softwareentwicklung“, erläutert der Prokurist. Ähnliche Lebensläufe gibt es viele bei QASS. „Bei uns wird die Nachwuchsförderung großgeschrieben. Jeder Werkstudent hat nach einer kurzen Einarbeitung seinen eigenen Bereich, für den er ganz allein die Verantwortung trägt“, erklärt Müller.
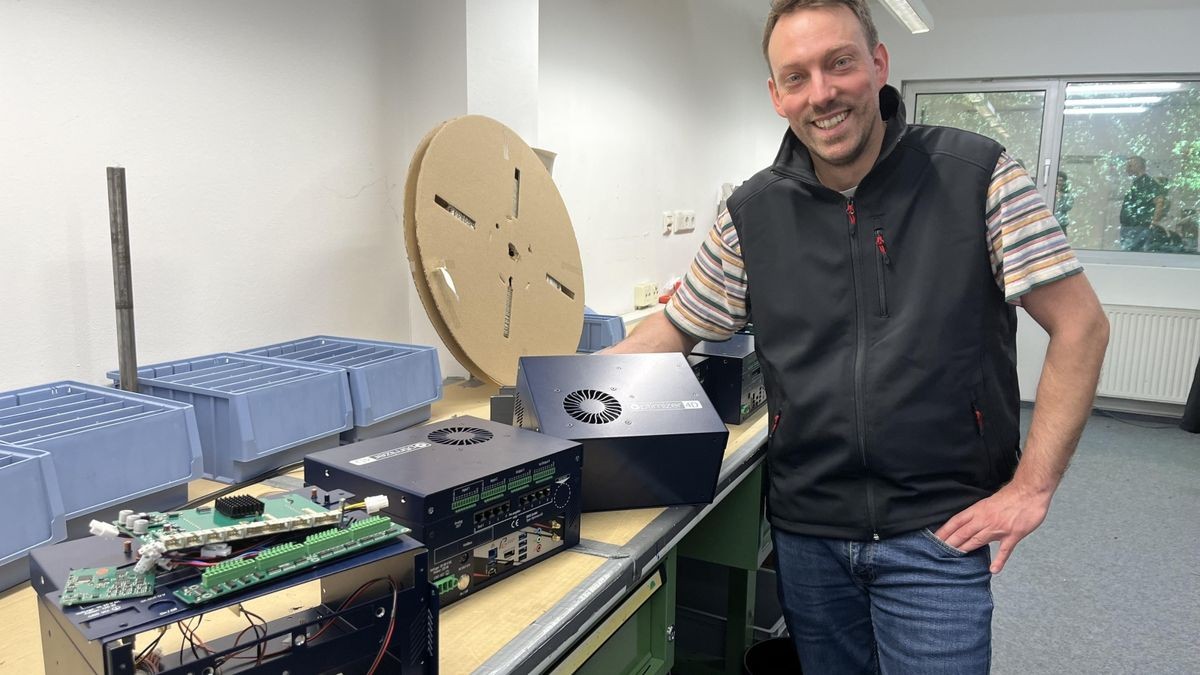
Chef ist Vorbild
Zu den großen Vorbildern gehört für die meisten aber auch der Chef Ulrich Seuthe selbst. „Er ist sowas wie der Deutsche Daniel Düsentrieb, mit Weitsicht und Durchhaltevermögen“, berichtet Müller und die Bewunderung ist ihm anzumerken. Das zahle sich aus. „Es ist schon eine Ehre, wenn Mercedes anruft und sagt, ‚wir haben ein Problem, das konnte noch nie jemand lösen, könnt ihr euch das mal angucken?‘“, so der Prokurist. Rico Lauersdorf, Elektronikentwickler bei Qass, weiß seinen Arbeitsplatz zu schätzen. Insbesondere, dass er sich probieren darf, gefällt ihm. „Hier wird das Rad nochmal entwickelt und manchmal merkt man, dass es noch nicht rund war“, sagt er und lacht.
Internationale Anerkennung
Optimieren, neu erfinden, tüfteln: Tätigkeiten, für die das Unternehmen in Volmarstein internationale Anerkennung erhält. „Es gibt kein Auto, abgesehen von Tesla und japanischen Wagen, das nicht mit QASS-Technik in Berührung gekommen ist. Wir prüfen sicherheitsrelevante Teile. In einigen Ländern dürfen solche Bauteile nicht verbaut werden, wenn sie nicht durch uns geprüft worden sind“, erklärt Prokurist Müller.
Software statt rosa Elefanten
So hat es QASS beispielsweise geschafft, innerhalb von nicht einmal zwei Jahren das Thema „fluxen“ komplett obsolet zu machen. Fluxen ist eine Werkstoffprüfung, bei der chemisch überprüft wird, ob Bauteile Risse haben. Dafür müssen die Bauteile jedoch mit einer Flüssigkeit eingestrichen werden. „Bei dieser aggressiven Ummantelung sehen die Prüfer aber nach zwei Stunden rosa Elefanten“, weiß Müller. QASS hat dieses Problem anders gelöst. Sie haben spezielle Sensoren entwickelt, die an die Maschinen angebracht werden. „Der Schall und die Vibrationen werden aufgenommen und eine spezielle Software kann heraushören, ob ein Riss am Bauteil entstanden ist. Sämtliche Umgebungsgeräusche werden dafür herausgefiltert. Passiert etwas, das nicht der Norm entspricht, wird das wahrgenommen und sofort alarmiert“, erläutert Müller das System.
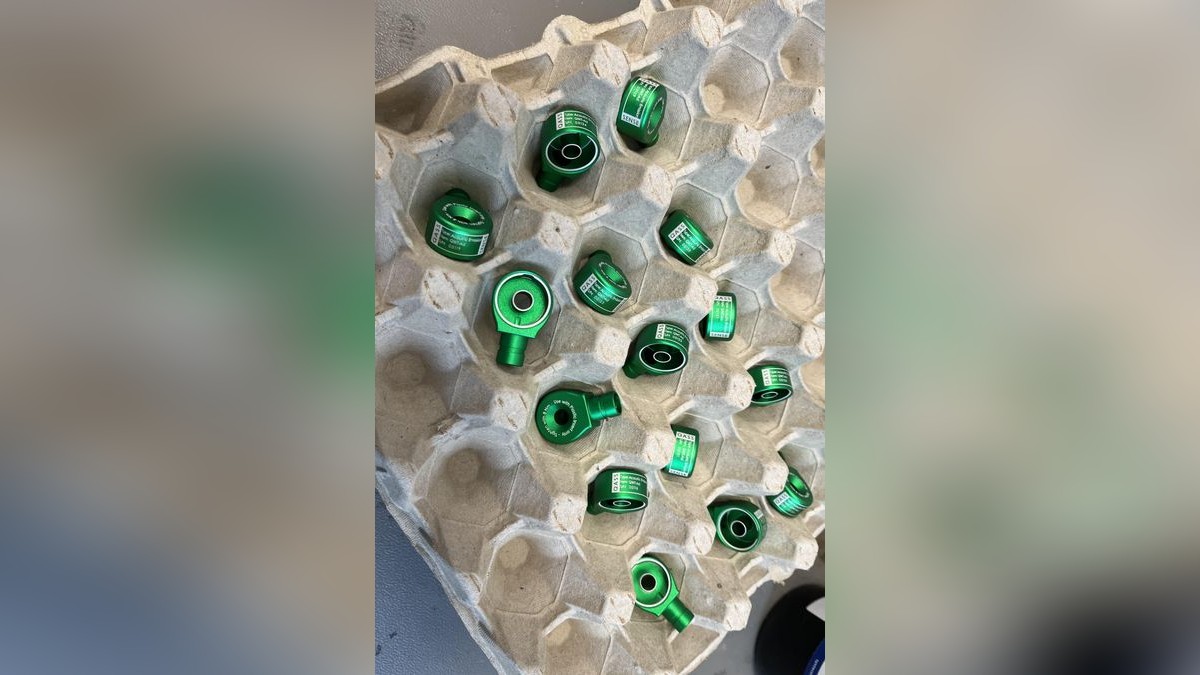
Besser als jede Fledermaus
Dafür müssen die Bauteile nicht aus der Maschine genommen werden. Das spart sowohl Zeit als auch Geld. Zumal der Sensor genau bestimmen kann, wo und welches Teil einen Riss hat. Dementsprechend muss nicht gleich eine ganze Charge vernichtet werden, wenn ein Fehler gefunden wird. Wie hochsensibel die Sensoren arbeiten, macht Axel Kähne, zuständig für Vertrieb und Marketing deutlich: „Der Sensor nimmt Geräusche 500 Mal besser als eine Fledermaus wahr.“
Komplette Kompetenz im Haus
Das komplette Prüfgerät wird bei QASS gebaut. Vom Alublock, der angeliefert wird, werden in der hauseigenen Fräse, die Sensorenträger gefertigt. „Das haben wir früher anliefern lassen, aber oft war die Lieferzeit viel zu lang, dann passte es nicht und so haben wir jetzt unsere eigene Fräse. So bleibt die komplette Kompetenz bei uns im Haus“, erklärt Müller. In der hauseigenen Produktion werden die Werkstücke dann mit der Sensorik und den Platinen bestückt und anschließend verbaut. Ein fertiger Messcomputer, der dann innerhalb von zwei Wochen ausgeliefert und beim Kunden installiert wird, kostet letztlich rund 35.000 Euro. Müller weiß, dass sich diese Investition lohnt und meist nach drei Monaten amortisiert hat und anschließend für die Kunden bares Geld einbringt.
Hohe Reparaturkosten vermeiden
Derzeit arbeiten die Tüftler in der Werkstatt an der Lösung eines anderen Problems. Bei einem Hohlrad für die Windkraftindustrie werden alle Zahnflanken derzeit noch einzeln von einem Mitarbeiter des Kunden auf Risse geprüft. Ein langwieriges, teures und aufwendiges Verfahren. Der Kunde hat QASS beauftragt, eine Lösung zu entwickeln, wie das Ganze beispielsweise mit einem Roboter funktionieren könnte. „Diese Hohlräder sind wichtig. Ist eines davon beschädigt, belaufen sich Austausch- und Reparaturkosten solch eines Schadens schnell auf rund 5 Millionen Euro. Das will keiner“, weiß Müller.
Auch Roboter müssen lernen
Ein paar Meter weiter ist ein weiterer Geniestreich gerade im Feinschliff. Ein Kunde möchte gerade sowohl Härte, Gewicht wie auch Oberflächenbeschaffenheit der Werkstücke bestimmen lassen, die in Schütten zu mehreren Teilen angeliefert wird. „Die Schwierigkeit hier bestand schon darin, dem Roboterarm beizubringen, dass er ein bestimmtes Teil herausgreifen soll, auch wenn die Teile kreuz und quer liegen“, erläutert Kähne. Inzwischen ist die Maschine aber schon in der Finalisierung.