Duisburg. „Premium-Blech made in Duisburg“ liefert Thyssenkrupp Steel für die Autoindustrie. Das trägt ein neuer Hubbalken-Ofen zu besserer Qualität bei.
Bei der Produktion von Blechen für die Autoindustrie zählt Qualität. Um die mit dem Prädikat „Premium“ zu liefern, hat Thyssenkrupp Steel (TKS) im Warmbandwerk Beeckerwerth einen neuen Hubbalken-Ofen installiert. Im neuen Aggregat, in das TKS nach eigenen Angaben in Duisburg einen „mittleren zweistelligen Millionen-Euro-Betrag“ investiert hat, wurde im August die erste Bramme erhitzt. „In der kommenden Woche beginnt der Regelbetrieb“, kündigte TKS-Produktionsvorstand Dr. Heike Denecke-Arnold am Dienstag an.
Der neue Ofen ist das erste fertiggestellte Projekt im Rahmen der Strategie 20-30 von TKS – durch die Modernisierung des Produktionsnetzwerks sollen auch Qualitätsprobleme bei den Produkten behoben werden. „Die Automobilindustrie hat höchste Ansprüche an die Oberflächenqualität“, so Denecke-Arnold, „sie wird maßgeblich beeinflusst durch das Erhitzen der Brammen auf die gewünschte Temperatur.“
Durch die Investition im Werksteil Beeckerwerth, wo Produkte für den Autobau entstehen, wolle TKS „das Wachstum des Industriezweigs begleiten“.
TKS: Brammen werden in Duisburg vor dem Walzprozess im Ofen auf 1250 Grad erhitzt
Ehe die Brammen aus dem Stahlwerk im Warmbandwerk zu bis zu 1,5 Millimeter dünnen Blechen gewalzt werden, müssen die bis zu 38 Tonnen schweren Stahlstücke auf 1250 Grad erhitzt werden. „Dabei müssen wir eine saubere Oberfläche erzeugen“, erklärt Frank Pozun. Innovativ, so der Leiter des Warmbandwerks 2, sei bereits der Transportprozess im 80 mal 54 Meter großen Ofen über wassergekühlte Röhren: „Die Brammen werden nicht geschoben, sondern getragen.“ Nach und nach erfolge dann die Erhitzung, „damit innere Spannungen vermieden werden.“
Geliefert wurde das neue Aggregat von der Firma Tenova LOI Thermprocess. Das Unternehmen, seit gut einem Jahr im Duisburger Innenhafen ansässig, gehört zur italienischen Tenova-Gruppe, die wiederum Teil des argentinischen Techint-Konzerns ist. Tenova gilt als Technologieführer für Wärmebehandlungsprozesse. „Wir bauen solche Öfen in der ganzen Welt, sie werden jeweils an die Bedürfnisse der Kunden angepasst“, erläutert Christian Schrade, Geschäftsführer von LOI Thermprocess in Duisburg.
Entsprechend international ist auch die Herkunft der einzelnen Bauteile: Schweren Stahlbau liefert Vietnam, Brenner und Steuerungstechnik kommen aus Europa, den Feuerfest-Ausbau erledigte ein Unternehmen aus dem Sauerland.
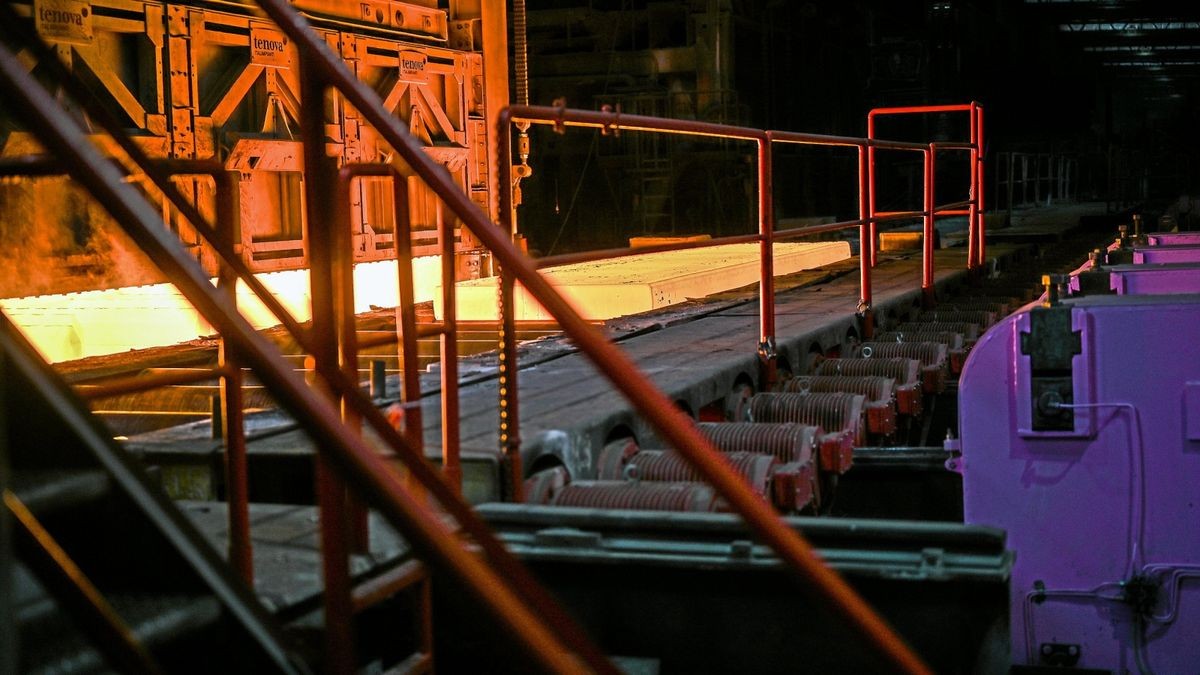
6700 Tonnen Stahl und Feuerfest-Material für das neue Aggregat
Gewaltig sind nicht nur die Ausmaße des neuen Aggregats: In 18 Monaten Bauzeit haben bis zu 250 Fachleute gleichzeitig 6700 Tonnen Stahl und Feuerfest-Material zusammengebaut. „Ungefähr die Hälfte des Gewichts des Eiffelturms“, sagt Frank Pozun. Eine neue Brennertechnik sorge dafür, dass die Anlage „auch bei Energieverbrauch und Energieeffizienz Maßstäbe setzt“, heißt es bei TKS. Weil Abgase wieder im Heizprozess eingesetzt werden, liege der Gasverbrauch um 20 Prozent niedriger als beim alten Ofen, der zuvor abgebrochen wurde. Erfreulich für TKS: Der Ofen muss nicht mit teurem Erdgas befeuert werden. Dazu können Prozessgase aus der eigenen Produktion genutzt werden, in der Zukunft ist auch ein Betrieb mit Wasserstoff möglich. Pozun: „Die Anlage ist H2-ready.“
Auch interessant
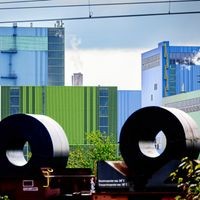
Die Walzen formen aus einer Bramme in drei Minuten eine bis zu 2000 Meter lange Blechrolle. Diese „Coils“ sind je nach Kundenwunsch zwischen 80 Zentimeter und zwei Meter breit. Pro Tag durchlaufen bis zu 300 Brammen den neuen Ofen. „Macht in 24 Stunden Blech für 500 Autos“, rechnet Frank Pozun. Insgesamt sechs Öfen stehen im Werk, vier von ihnen, sogenannte Stoßöfen, wurden in den 1960er und 1970er Jahren gebaut. Ein erster Hubbalkenofen ging vor 15 Jahren in Betrieb.
[Nichts verpassen, was in Duisburg passiert: Hier für den täglichen Duisburg-Newsletter anmelden.]
Nur Hubbalken-Öfen sind in der Lage, Brammen durch eine Hebe- und Senkvorrichtung ohne Beschädigungen der Unterseite durch den Ofen zu tragen. Kratzer können hingegen beim Schieben durch die Stoßöfen entstehen – diese „Unterseitenverletzungen“ beeinträchtigen am Ende die Qualität des Blechs. Lieber heute als morgen hätte Werksleiter Pozun deshalb gern einen weiteren Hubbalken-Ofen. „Dann würden wir alten Aggregate nicht mehr benötigen.“
DIREKTREDUKTION: ZWEI ANGEBOTE LIEGEN VOR
- Für den Bau der ersten Direktreduktionsanlage (DR), die im Duisburger Norden ab 2026 die ersten Hochöfen von Thyssenkrupp Steel ersetzen soll, gebe es zwei Angebote, hieß es am Dienstag. Um die Realisierung der Milliarden-Investition bewerben sich demnach Tenova HYL (Mexico) und Midrex (Japan) – sie gelten als die weltweit einzigen Unternehmen, die in der Lage sind, Anlagen dieser Größenordnung zu bauen. Die Auftragsvergabe könnte noch vor Jahresende erfolgen, heißt es bei TKS.
- Die Tenova HYL bezeichnet sich als „Pionier in Direktreduktion“, der 1957 die weltweit erste Industrieanlage in Monterrey (Mexico) baute. Seither hat das Unternehmen nach eigenen Angaben weltweit über 40 DR-Module ausgeliefert. Gemeinsam mit der italienischen Danieli entwickelt Tenova HYL seit 2006 DR-Anlagen auf Gasbasis unter der Marke Energiron.
- Das Midrex-Verfahren zur Direktreduktion wurde nach der Entwicklung im US-Konzern Midland-Ross 1975 zum Patent angemeldet, die gleichnamige Firma gehört seit 1983 zur japanischen Kobe Steel. Eine in den frühen 1970er Jahren in Hamburg errichtete Midrex-Anlage gehört heute Arcelor-Mittal. Kandidat für einen Bau der TKS-Anlage in Lizenz, so heißt es, sei die SMS (ehemals SMS Siemag). Das Düsseldorfer Unternehmen ist ebenfalls international in der Hütten- und Walzwerkstechnik unterwegs.