Geesthacht. Bauteil von Riftec fliegt mit der Ariane-Trägerrakete ins All. Aber nicht nur die Weltraumbranche hat das Unternehmen im Blick.
Groß ist das silberne Metallteil nicht, das Riftec-Geschäftsführer Axel Meyer zwischen den Fingern hält. Eine geballte Männerhand könnte es umschließen. Das kleine Stück Metall made in Geesthacht müsste im Ernstfall deutlich mehr Druck aushalten. Das Modul ist eine Art Stecker für Stellen im Gehäuse eines Satelliten, in denen Sensorik verbaut ist.
Das knapp fingerlange Stück sitzt an der Schnittstelle zwischen dem Vakuum des Weltraums und dem vakuumfreien Innenraum des Satelliten. „Und um Signale aus dem Gehäuse rauszukriegen, da machen wir quasi den Stecker“, sagt Axel Meyer. Der Satellit selbst wird von Airbus gebaut und soll der Forschung dienen.
Die richtigen Handschuhe für das Anfassen wurden vorgeschrieben
Das Modul, das der Geschäftsführer vorzeigt, ist zur Anschauung in einem Büroregal bei Riftec verblieben. Die „richtigen“ Module, die verbaut werden, dürfte man nicht mit der bloßen Hand anfassen. Durch Fingerabdrücke könnte zum Beispiel Korrosion entstehen. „Die Teile müssen unglaublich sauber sein. Das geht soweit, dass die Art der Handschuhe vorgeschrieben ist, die wir verwenden sollen“, berichtet Axel Meyer. „Was ja auch okay ist, da möchte man keinen Fehler gemacht haben, wenn der Satellit erst im Weltraum ist.“
Geliefert wurden Module „in der Größenordnung von zehn Stück“, sagt Axel Meyer. Gut bezahlt, aber noch wichtiger sei das Renommee, findet er. „Wir sind jetzt gerade am zweiten dran“. Der Start des Satelliten mit Inhalt aus Geesthacht mit der Ariane-Trägerrakete vom Weltraumbahnhof Kourou in Französisch-Guayana ist seit drei Jahren überfällig. „Aber die sind tiefenentspannt, was Verzögerungen betrifft“, weiß Axel Meyer. Immerhin: „Wir sollen es noch erleben.“
Die Weltraumbranche entdeckt die Vorzüge des Rührreibschweißens
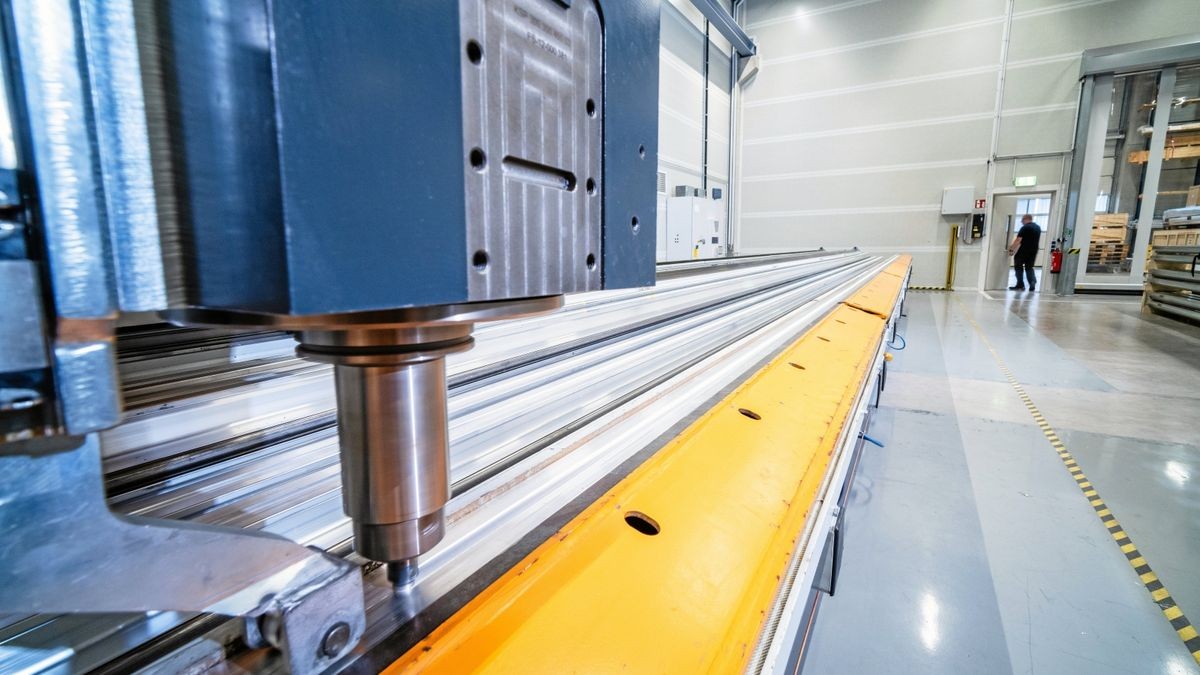
Die spezielle Technik des Rührreibschweißens scheint dem Geesthachter Unternehmen von der Mercatorstraße noch weitere Kunden aus der Weltraumbranche zuzuführen. „Es erlaubt die spannende Verbindung verschiedener Werkstoffe“, sagt Axel Meyer. Für das Airbus-Modul war es die von Aluminium als Gehäuse mit Edelstahl. Zwei Materialien werden zusammengepresst, die Fuge dazwischen fährt ein sich drehender Stichel ab. Die Wärme durch die Reibung und der Druck sorgen dann für eine Verschmelzung der Werkstoffe.
„Wir sind bekannt im Markt der Rührreibschweißer“, sagt Axel Meyer. Genauer gesagt: Riftec bezeichnet sich selbst stolz als Marktführer. „Wenn man als Satellitenbauer ein Rührreibunternehmen finden will, landet man sehr schnell bei uns“, sagt er. „Wir sind an weiteren interessanten Projekten dran, aber das ist noch nicht spruchreif“, sagt Axel Meyer. „Das Thema Raumfahrt war früher sehr abgeschottet. Nun sind plötzlich ganz neue Player am Markt, die es vorher nicht gab, die sind offener“, erzählt er.
Die Maschinen laufen von sechs bis 22 Uhr, gearbeitet wird in drei Schichten
Das Satellitenmodul ist ein gutes Symbol für die aktuelle Situation: Riftec setzt nach einem Corona-Knick zu neuem „Höhenflug“ an. Die Auftragsbücher für die großen Bauteile sind bereits jetzt bis Ende des Jahres gefüllt, die Zahl der Mitarbeiter wächst auch wieder. Vor Corona waren es 45 Mitarbeiter, dann ging es runter bis auf dreißig, nun läuft es wieder in die andere Richtung. „Wir sind schon wieder bei 33“, berichtet Axel Meyer. Noch vier weitere sollen bis Ende des Jahres eingestellt werden. Gesucht wird Personal vor allem in drei Bereichen: Anlagenbediener, Zerspaner, Produktionshelfer. „Gearbeitet wird in drei Schichten, um der Auftragslage Herr zu werden“, verrät Axel Meyer. Die Maschinen laufen von sechs bis 22 Uhr.
Das macht sich auch am Umsatz bemerkbar. „Vor Corona waren es fünf Millionen, dann sank er unter drei Millionen, jetzt arbeiten wir uns gerade wieder hoch“, sagt Axel Meyer. Dabei hilft auch der Boom in einer weiteren Branche, ausgelöst durch den Umweltschutz: des Eisenbahnbaus in ganz Europa. Produziert werden Seitenwände von Zügen, Verkleidungs- und Dachschutz und für die Schieneninfrastruktur. Überall auf dem Gelände stapeln sich Schienen für die Stromversorgung. „Sie werden in zwei Stufen produziert. Erst manuell alle Teile zusammenstecken, dann erst fangen wir zu schweißen“, sagt Axel Meyer.
Auch Muskelkraft und der Einsatz des Hammers sind noch gefragt
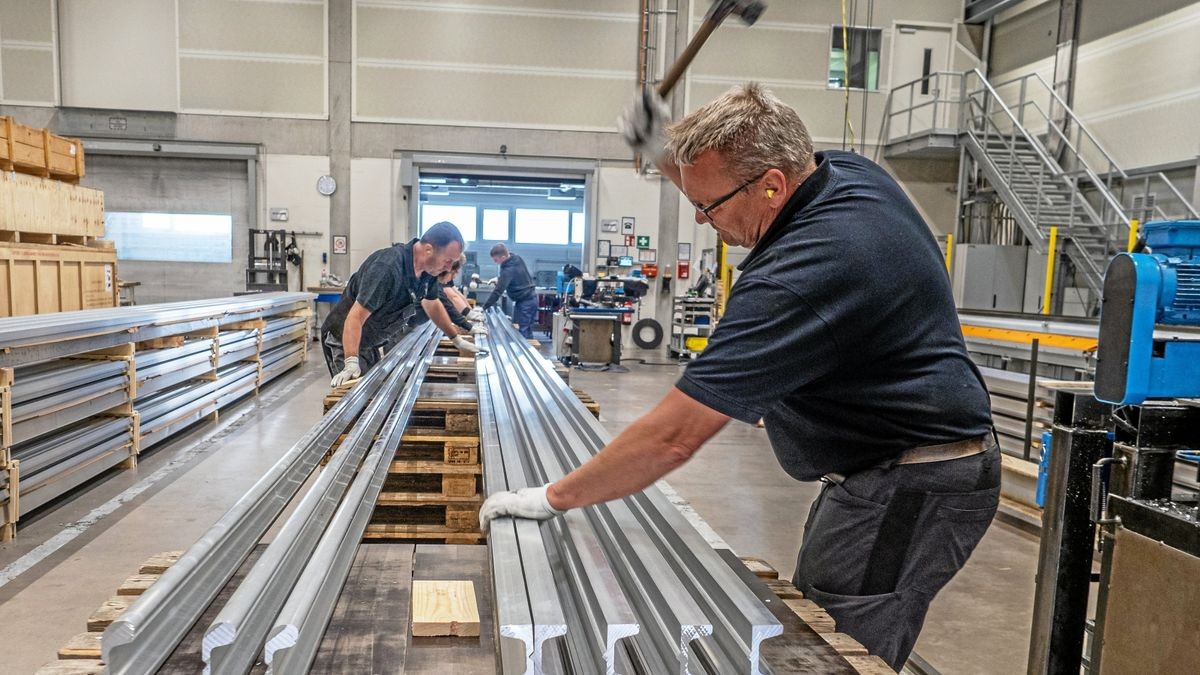
Hierbei zählt dann noch Muskelkraft und Handarbeit. Den letzten Ruck für das Zusammenstecken gibt es nur unter Einsatz eines Hammers. Die Größenkapazität der Maschine wird hierbei voll ausgeschöpft. 15,1 Meter lang sind die Schienen, die alle zwei Wochen von einem Schwerlaster abgeholt und nach Norwegen transportiert werden.
Die Auftragslage wird sich auch in Form eines weiteren Gebäudes auf dem Gelände optisch bemerkbar machen. Um zusätzliche Lagerflächen zu schaffen, soll noch in diesem Jahr eine Leichtbauhalle gebaut werden. Und: Möglicherweise kommt noch eine zweite Produktionshalle hinzu. Dann, wenn Riftec von einem Hersteller aus der Automobilbranche mit einem lukrativen Auftrag bedacht wird. Es geht um Luxusautos, mehr vermag Axel Meyer noch nicht zu verraten. Die Entscheidung für oder gegen Geesthacht könnte in einem halben Jahr fallen.
- Wo Alfred Nobel das Dynamit erfand
- Retter gesucht für Forsthaus Grüner Jäger
- Erster Zug seit sechs Jahren verlässt AKW Krümmel
Die Bindung soll diesmal langfristig abgeschlossen werden, nachdem ein anderer Kunde aus dem Zulieferergeschäft von Autobauteilen recht kurzfristig abgesprungen ist. Im Rührreibschweißverfahren fertigten die Geesthachter Deckplatten aus Aluminium für Laderegler, die in Volvo-Hybridfahrzeigen eingesetzt wurden. Die Endmontage fand in Ungarn statt. Diese Produktion ist nun komplett nach China verlagert worden, 2021 lief die Produktion an der Mercatorstraße aus. Immerhin gehört ein Hersteller von vollelektrischen Supersportwagen weiterhin zum Kundenkreis. Wer es ist, muss erneut ein Geheimnis bleiben.
Das Timing für das Ende der Durststrecke könnte nicht besser sein: Rechtzeitig zum 20. Geburtstag zeigt die Kurve wieder nach oben. Für die Kieler Woche in zwei Wochen wurde ein Segler gechartert, fast alle Mitarbeiter haben für den Törn zugesagt. Da geht es dann wohl unter vollen Segeln über die Ostsee
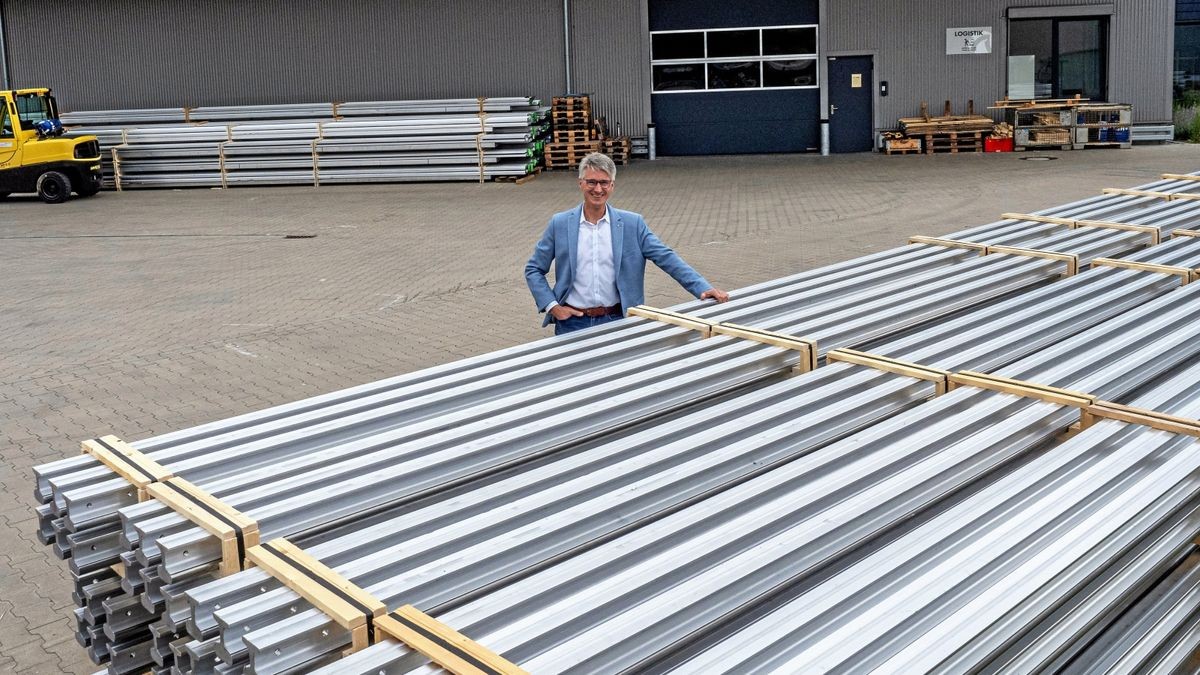
.