Lauenburg/Geesthacht. Durch das Hochwasser in Lauenburg ist der Zeitplan der Hitzler-Werft durcheinandergeraten. Aber jetzt wird richtig Tempo gemacht
Das Hochwasser hatte es in diesem Jahr nicht eilig, die Region bei Lauenburg zu verlassen. Es floss ab, kehrte zurück und hielt sich lange hartnäckig in der Halle der Hitzler-Werft, in der zurzeit die „Coriolis“, das neue Forschungsschiff des Helmholtz-Zentrums, gebaut wird. „Wir sind nun ein wenig im Zeitplan hinterher“, sagt Werft-Geschäftsführer Kai Klimenko. Erst seit März werden die Arbeiten von der Elbe nicht mehr behindert.
Nun aber ist der Werftboden wieder knochentrocken. Es riecht nach Schweißen, der Geräuschpegel ist hoch, es wird gehämmert und gesägt. „Wir sind jetzt in einer Phase, wo extrem viel passiert, extrem spannende Dinge“, freut sich Kai Klimenko. „Die Maler, die Tischler sind auch da, die Gewerke machen Ballett. Da ist richtig Musik drin“.
Hitzler-Werft Lauenburg: „Coriolis“-Bau läuft nach Hochwasser auf Hochtouren
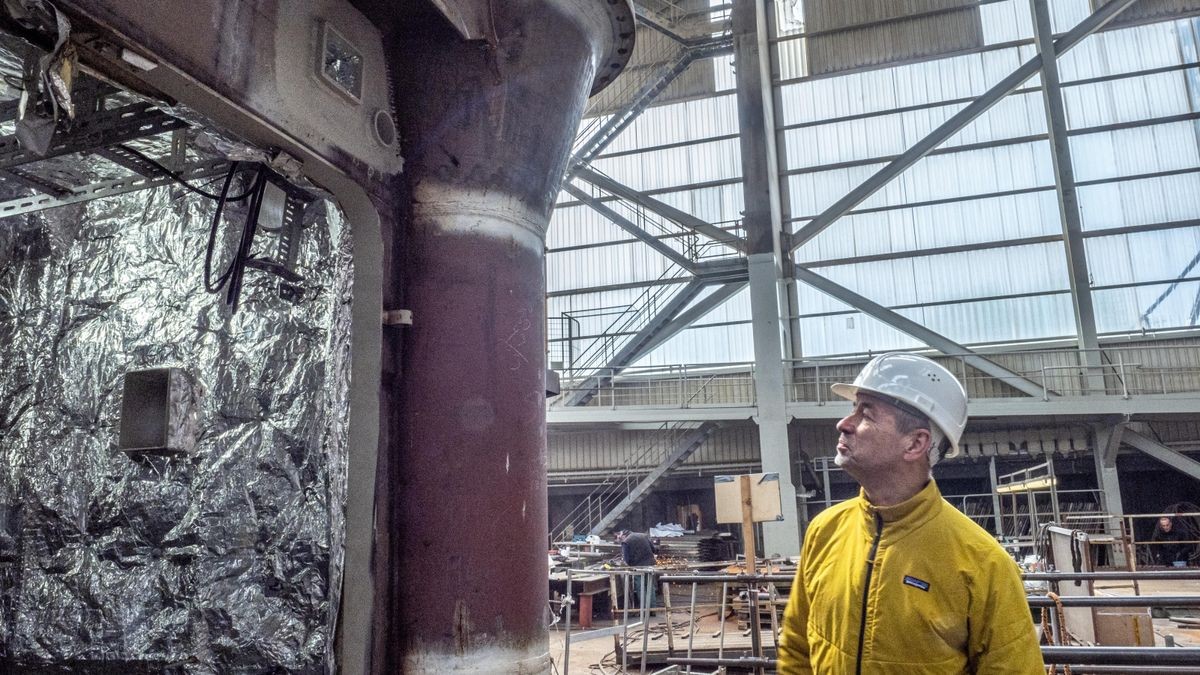
Gerade werden die Fenster und Seeschlagblenden, mit denen die Fenster geschlossen werden können, montiert, die Hälfte der Schwanenhälse für die Belüftung ist eingebaut, die Türen folgen. Auf dem Vorschiff glänzt die Ankerwinde aus Bronze. Da sieht man die Fortschritte Tag für Tag. Fast alles liegt mittlerweile vor Ort zum Einbau bereit. Und auf dem Gelände des Helmholtz-Zentrums in Geesthacht steht in Regalen für den Einbau vorkonfektioniert die Elektronik.
Die große Klima-Unit – die bordeigene Klimaanlage – und zwei Antriebsaggregate lagern gut verpackt in einer benachbarten Werfthalle, bis sie an der Reihe sind. Ebenso der Bordkran. Er wurde getestet und wieder zusammengeklappt. Er stammt von der Firma Palfinger aus Österreich, Weltmarktführer in Sachen Teleskopkräne. Die Vorrichtung, die ihn aufnehmen soll, ist in der Mitte des Schiffs bereits montiert.
Für Beiboot und Forschung – neuer Teleskopkran wird im Juli montiert
Sie sieht aus wie der Unterbau für einen Sonnenschirm. Nur, dass dieser in diesem Fall ganz besonders groß und schwer ausfällt. 32 Löcher für die Befestigungsbolzen sind auf einer Kreisfläche zu sehen. Der Teleskopkran soll im Juli montiert werden. „Er wird draufgesetzt und verschraubt, mehr ist es eigentlich nicht“, erklärt HzG-Projektleiter Volker Dzaak.
Im Alltagseinsatz wird er je nach Seegangverhältnissen und Auslage Lasten mit einem Gewicht von bis zu 6,5 Tonnen heben. Völlig ausreichend zum Beispiel für das Schwenken des Beibootes oder auch für die Forschung. „Das ist hervorragend“, freut sich Volker Dzaak. „Wir haben damit ein sehr sicheres System an Bord und können für Meeresbodenuntersuchungen bis zu 25 Meter tief hinuntergehen. Und auf den Zentimeter genau positionieren.“
Wasserstoffantrieb an Bord für die Erprobung
Für zwei wichtige Komponenten indes werden noch Auftragnehmer gesucht. So soll das Schiff zusätzlich mit einem Wasserstoffantrieb ausgerüstet werden, der während der Fahrt an Bord erprobt wird und das Schiff in diesen Phasen völlig emissionsfrei fahren lässt.
Für die Metall-Hydrid-Tanks soll die Ausschreibung im Mai herausgehen, das Auftragsvolumen beträgt 500.000 Euro. Die Ausschreibung für die Brennstoffzelle mit einem Volumen in Höhe von 350.000 Euro ist seit einer Woche veröffentlicht.
Verbaut wird eine Kabelstrecke „von Geesthacht nach Lauenburg und zurück“
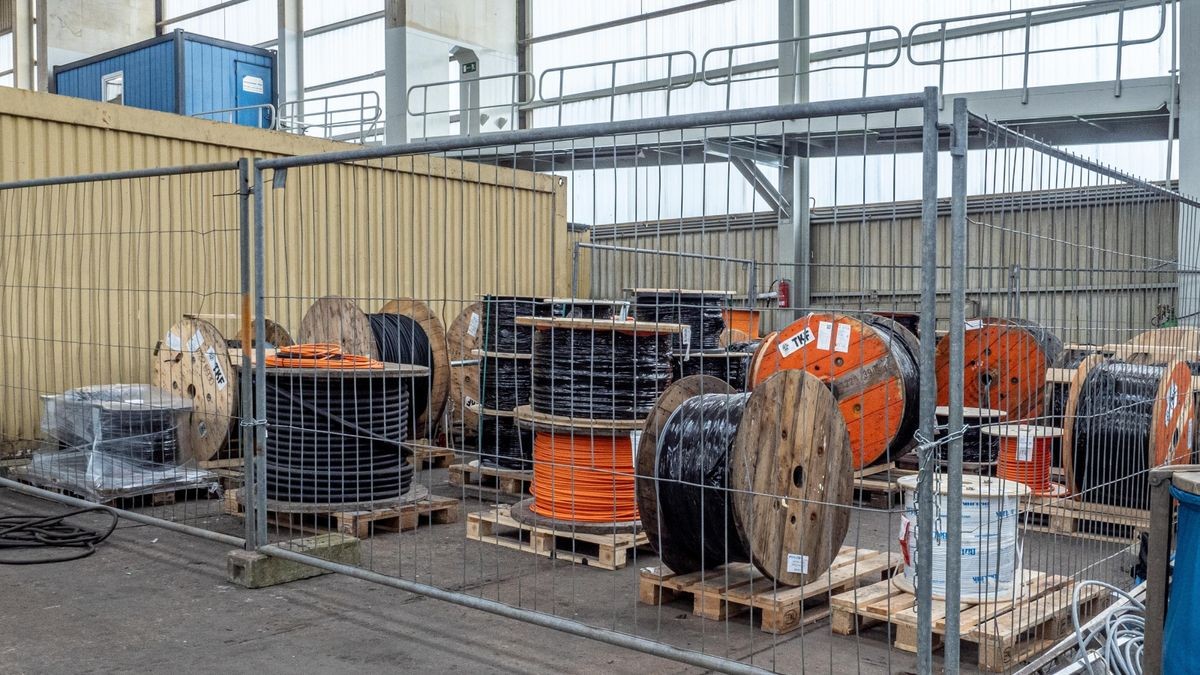
Brennstoffzelle, Batterie und Generatoren können untereinander kombiniert werden. Die Ergebnisse des Betriebs sollen genutzt werden, um Anlagen wie Bunkerstation, Brennstoffzelle, Metallhydrid-Tank und Systemsteuerung zu optimieren und die Nachrüstung von anderen See- und Binnenschiffen zu vereinfachen.
Ein Posten, der noch richtig viel Mühe machen wird, lagert auf großen Rollen hinter einem Gitterverschlag auf dem Werftboden an Land. Es sind Kabel aller Sorten und Dicke, die im Schiff verlegt werden müssen. Rote Isolierung zeigt an, welche Kabel feuerfest sind. „Sie ergeben eine Strecke von 28 Kilometern“, sagt Kai Klimenko. „Das ist von Geesthacht nach Lauenburg und wieder zurück.“
Nach der Verlegung wird penibel jedes Kabel überprüft
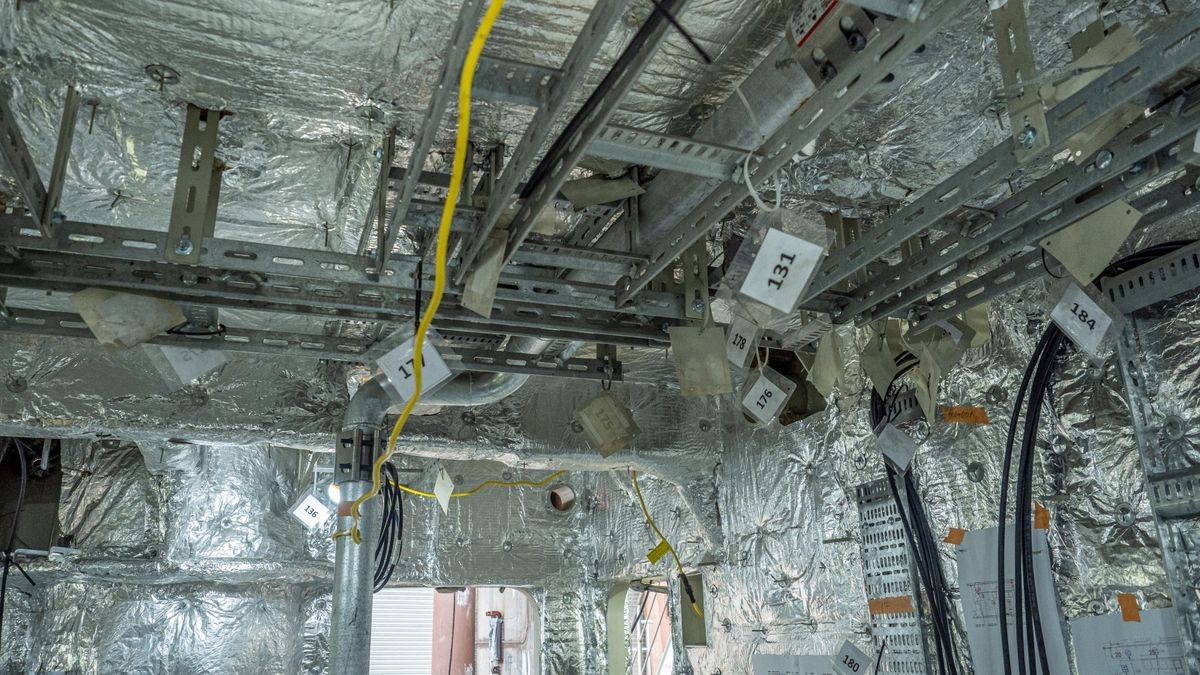
Ist die Strecke verlegt, hört die Arbeit nicht auf. Dann wird jedes Kabel überprüft. „Wir müssen jeden Draht durchklingen“, sagt Kai Klimenko. „Ist der richtig isoliert oder beschädigt? Hört er da auf, wo er aufhören soll? Habe ich irgendwo Fehlermeldungen, dass das Kabel beschädigt worden ist?“
Unter Deck ist die bevorstehende Verlegung bereits optisch sehr präsent. Von Kabelbahnen unter der Decke baumeln lauter Zettel mit Zahlen darauf. „Die Nummern gehen bis 500 hoch“, sagt Kai Klimenko. Die Kabel sind entsprechend gekennzeichnet. So lässt sich ablesen, an welcher Stelle welches Kabel verlegt werden muss.
Je nach Beanspruchung gibt es Rohre aus unterschiedlichem Material
Hinzu kommen ebenfalls kilometerlange Rohrsysteme, durch die die Kabel teilweise verlaufen. Sie sind bereits in der Vorfertigung und penibel voneinander getrennt, „damit die Maler nicht aus Versehen etwas konservieren, das eigentlich verzinkt werden müsste“, erklärt Kai Klimenko.
Je nach Beanspruchung gibt es Rohre aus unterschiedlichem Material, aus Edelstahl etwa oder aus Kupfer, manche werden verzinkt oder bestehen gleich ganz aus dem sehr strapazierfähigen Kunststoff PVDF. Einige werden passgenau angeliefert, andere erst komplett vor Ort passend gemacht, die dritte Kategorie ist eine Kombination aus den beiden Möglichkeiten.
In einem „Brunnen“ im Nasslabor schwappt das Wasser
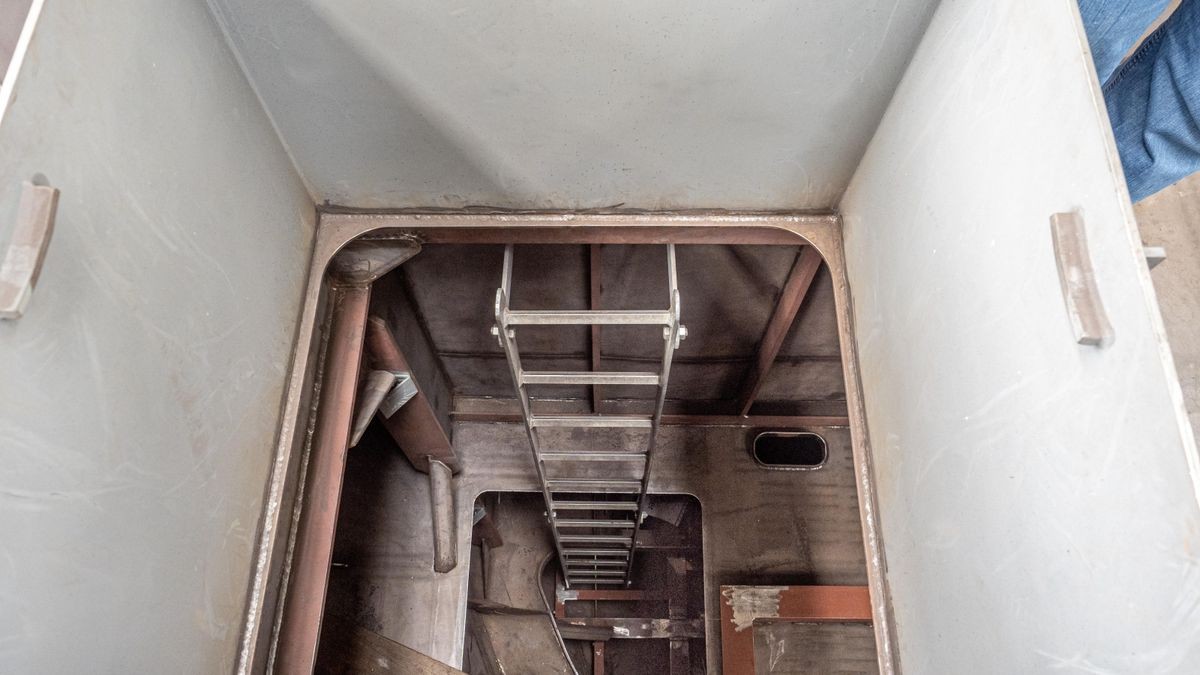
Unter Deck sieht es aus wie im privaten Disco-Keller in den 80er-Jahren. Die Wände glitzern silbern, wie mit Alufolie beklebt. Es ist die Beschichtung von Dämmstoffen, die hier fast überall verbaut sind. Vom Heck führt eine Treppe hoch ins Nasslabor.
Wird auf der Steuerbordseite – in Fahrtrichtung rechts – ein quadratischer Deckel gehoben, schwappt dort ähnlich einem Brunnen in 1,75 Meter Tiefe das Wasser. Es ließe sich auf Forschungsfahrt bequem auf die Schnelle für Untersuchungen hochpumpen.
Wenig Tiefgang – die „Coriolis“ fährt auch in die Flüsse hinein
Die wissenschaftlichen Messkampagnen der „Coriolis“ in der Küstenforschung werden in der Nord- und Ostsee umgesetzt, einbezogen werden Ems, Weser und Elbe. Wegen eines Tiefganges von nur 1,6 Metern ist die „Coriolis“ äußerst vielseitig einsetzbar.
Vom Nasslabor aus geht es die Treppe runter zum Unterkunftsbereich der drei Besatzungsmitglieder. Auf Steuerbord sind es drei Bullaugen, auf Backbord vier, geschützt mit einer Blende gegen Seeschlag. Zum Teil sind sie zu öffnen. Ein Raum wird abgezwackt für WC und Dusche.
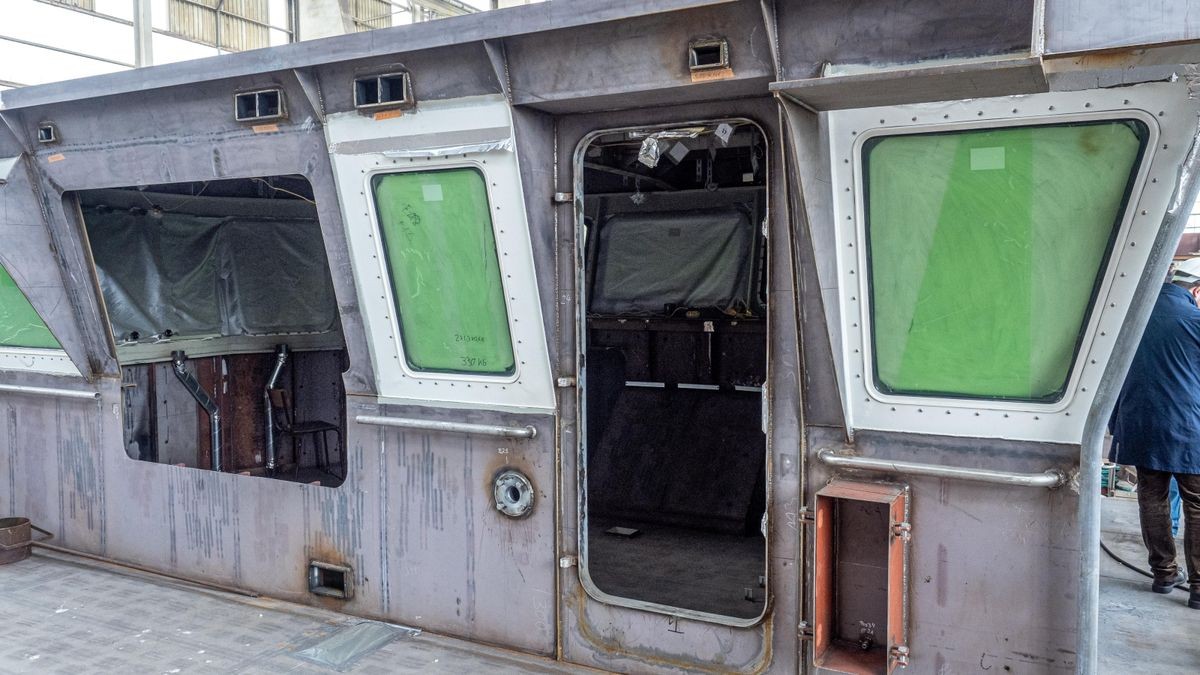
Seekarten gibt es weiterhin auch gedruckt – der Sicherheit wegen
Noch weiter geht es hier nicht nach vorn. Die Räume Richtung Bug sind für die Schiffstechnik reserviert, zum Beispiel für den Querstrahler, die Klima-Unit, Motoren für Ankerwinden, elektrische Schaltkästen und die Echolote. „Jeder Quadratzentimeter Platz wird hier sinnvoll genutzt“, sagt Kai Klimenko. Die Brücke, in der es auch einen Kartentisch für Seekarten aus Papier geben wird zur Sicherheit, sollte die EDV ausfallen, sowie eine Pantry als Aufenthaltsraum ergänzen das Raumangebot.
Auch noch interessant
- B5: 30-Tonner steckt stundenlang in der Bankette fest
- 216 neue Wohnungen in Hafencity? Ein Reptil macht Stress
- Frühjahrsmarkt auf Gut Basthorst: Das sind die Highlights
Die Taufe soll im November auf der Werft erfolgen, die Feuertaufe noch im selben Monat auf einer Prüffahrt auf der Nordsee. „Das haben wir so geplant. Das passt doch gut zu Lauenburg“, kündigte Volker Dzaak an. Kai Klimenko hörte es gern. „Wir freuen uns ja immer, wenn wir hier eine Taufe veranstalten dürfen“, sagt er.
Hintergrund: Ein auf der Hitzler-Werft gebautes Wallaby-Boot mit innovativer neuer Stabilisierungstechnik für ruhiges Fahren war am 22. April von Wirtschaftsminister Robert Habeck in Kappeln getauft worden. Die Gesamtkosten belaufen sich für die „Coriolis“ belaufen sich auf etwa 18 Millionen Euro. Von der Bundesanstalt für Verwaltungsdienstleistung gibt es einen Förderbescheid über 560.000 Euro.