Hamburg. Hinter den Kulissen des Hamburger Airbus-Werks. In Halle 245 arbeiten Mensch und Roboter zusammen. Es lauert eine Gefahr. Die Video-Reihe.
Die Flugzeugproduktion bei Airbus auf Finkenwerder beginnt in Halle 245. Grüne Aluminiumschalen hängen dort von der Decke herab. „Unsere Mitarbeiter schauen sich jede Schale noch mal an“, sagt Jan Eric Wilde. Er ist der Leiter der Strukturmontage für die A320-Familie in Hamburg: „Gibt es Beschädigungen durch den Transport? Gibt es auffällige Anomalien?“ An einigen Schalen sieht man graue Ausbesserungsstellen. Dort wurden schadhafte Stellen beseitigt.
Bevor die Rumpfschalen in Hamburg zur sogenannten Tonne weiterverarbeitet werden und den runden Charakter eines Flugzeuges erhalten, haben sie schon eine Schiffstour hinter sich. Gefertigt werden sie in Nordenham beim Zulieferer Premium Aerotec. Dann werden sie mit dem Spezialfrachter „Kugelbake“ über die Elbe in die Hansestadt geliefert und am Betriebshafen auf einen Lastwagen geladen.
Airbus Inside: Aus Schalen wird die Tonne – so startet der A320 ins Leben
Dieser bringt sie in die Halle 245 durch ein großes Tor, das man sich mit der neuen Halle 246 teilt. In ihr soll künftig das Leben des A321XLR beginnen. Durch einen fest im Frachtraum eingebauten Tank kann das einst für die Kurz- und Mittelstrecke konzipierte Flugzeug künftig auch auf der Langstrecke eingesetzt werden.
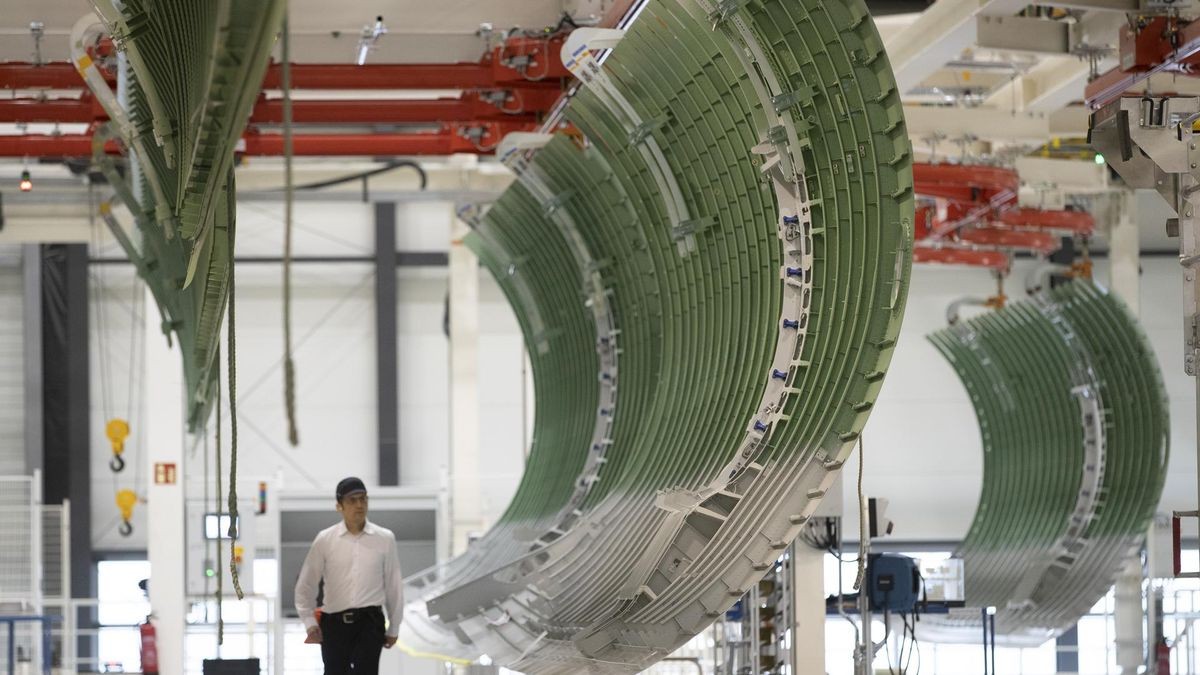
In Halle 245 werden die Schalen über ein Leitsystem in ihre Produktionsbereiche gelotst. Zwei verschiedene Rumpfabschnitte werden in der Halle montiert. Die Sektion 15 bildet den mittleren Teil des Flugzeuges, an dem später in der Endmontagelinie die Flügel angebracht werden. Zunächst werden dafür aber in der Strukturmontage die Voraussetzungen geschaffen. „Hier bekommen wir die Center Wing Box aus Nantes angeliefert“, sagt Wilde.
Die Flugzeugteile kommen aus den in Europa verteilten Werken
Die in Europa verteilten Werke des DAX-Konzerns liefern gemäß ihren Stärken unterschiedliche Komponenten. Das Cockpit und das vordere Rumpfsegment stammen aus Saint-Nazaire, das Höhenleitwerk aus Getafe, das Seitenleitwerk aus Stade, die Flügel aus Broughton, die Triebwerksaufhängungen aus Toulouse und die Landeklappen aus Bremen.
„Die Center Wing Box ist der Teil, der den Haupttank im Inneren integriert hat“, sagt Wilde. Der Großteil des Kerosins wird bei dem Kurz- und Mittelstreckenflugzeug in den Tragflächen untergebracht. Zudem ist die Box das zentrale Element, um die Flügel mit dem Rumpf zu verbinden und muss enorme Kräfte aushalten, die beim Flug entstehen.
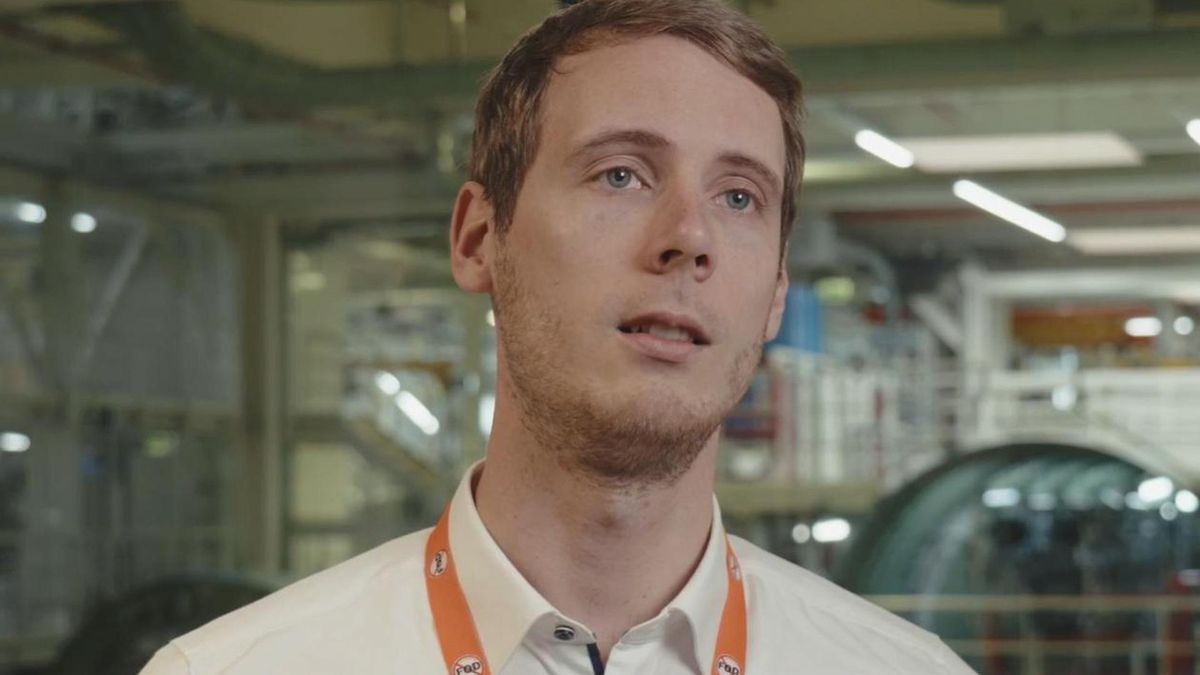
Die einzelnen Stationen in der Fertigung sind in U-Form angeordnet. Nach und nach werden mehr Teile an der Sektion montiert. Auch Halter kommen hinein, um später Kabel oder Rohre daran zu befestigen.
Airbus: Der Rumpf entsteht aus zwei Seiten- und einer Oberschale
An einer anderen Stelle in der Halle wird der nächste Rumpfabschnitt des Fliegers gebaut. „Anders als bei der Sektion 15, wo die Geometrie hauptsächlich aus der Center Wing Box mit den starken Primärstrukturteilen besteht, wird die Sektion 17 hauptsächlich um den Fußboden herumgebaut“, sagte Wilde: „Das heißt: Der Fußboden ist der ,Nullpunkt‘. Und wir bauen die Seitenschalen drum herum.“
Später werden die Schalen zur Tonne zusammengefügt. Sie besteht aus drei Schalen, zwei Seitenschalen und einer Oberschale. Ein Kran hebt diese an, fährt sie über den Bauplatz und senkt sie ab, damit Überlappungsbereiche entstehen. Ein Laser hilft bei der exakten Positionierung.
Achtung vor Fremdteilen! Warum FODs eine große Gefahr sind
Mensch und Roboter arbeiten dabei eng zusammen. „Der Roboter geht die Längsnähte auf beiden Seiten entlang und bohrt die Löcher rein. Es sind etwa 1000 Stück pro Seite“, sagt Wilde. Auf einer Arbeitsfläche direkt neben der Oberschale steht ein Mitarbeiter und schwingt den Staubsauger. Sämtliche Späne müssen aufgesaugt werden.
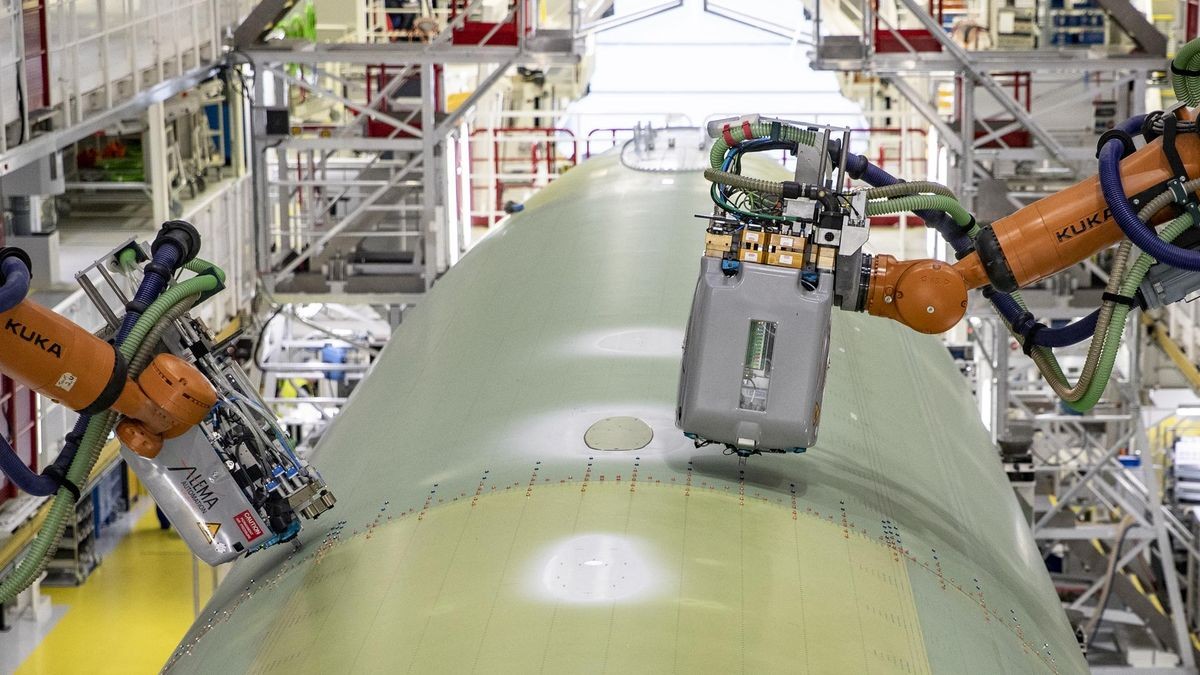
„Damit vermeiden wir Schäden durch fremde Teile, sogenannte FOD (foreign object damage)“, sagt Wilde. „Jedes kleinste Teil kann im Flugverkehr schwerwiegende Folgen nach sich ziehen. Deswegen wollen wir unsere Produkte so rein wie möglich abliefern.“ In der Halle weisen überall Schilder auf die Gefahr von FODs hin.
Am Ende der Arbeiten in Halle 245 sind Rumpf bis Heck zusammengebaut
Immer wieder sind klopfende Schläge zu hören. Ab und an gibt es ein kurzes, dröhnendes Knarzen. Oberhalb eines grünen Rumpfsegmentes sind zwei orangefarbene Arme eines Roboters zu sehen. Zwei weitere arbeiten an der Unterseite. Sie sorgen für das Knarzen.
„Die Kuka-Roboter können bohren, kitten und das Niet stecken“, sagt Wilde. „Das machen sie mehrere Tausend Male an einem Querstoß.“ Sie verbinden die Sektionen also der Länge nach. Am Ende des Prozesses in Halle 245 sind die Sektionen 15 bis 19 zusammengebaut – also der Rumpf von der Flügelanschlussstelle bis zum Heck.