Waren an der Müritz. Die Mecklenburger Metallguss baut für 110 Schiffe der Hamburger Reederei neue Schiffsschrauben. Millionen Tonnen CO₂ werden eingespart.
Eine Sirene ertönt, dann legt sich ein dunkler Schatten über die 8000 Quadratmeter große Halle. Ein Deckenkran hebt einen zehn Meter messenden, 100 Tonnen schweren Schiffspropeller in die Höhe, der die darüberliegenden Scheinwerfer verdeckt. Langsam wird das bronzene Ungetüm quer durch die Halle gehoben und auf einer vorbereiteten Freifläche abgestellt.
Dann entfernt eine Bandsäge das Tragegestell am oberen Ende des auf dem Kopf stehenden Propellers. Am anderen Ende der Halle, wo der Propeller eben noch stand, wird schon aufgeräumt, Platz gemacht für den nächsten Rohling einer Antriebsschraube. Im Dreischichtsystem werden bei der Mecklenburger Metallguss (MMG) in Waren an der Müritz Schiffspropeller hergestellt.
Hapag-Lloyd bestellt besonders sparsame Schiffspropeller
Die Liste der Aufträge reicht einmal um den Müritzsee herum. Hapag-Lloyd hat eine große Order aufgegeben. Hamburgs Traditionsreederei lässt 110 Schiffe mit neuen Propellern ausrüsten. 34 sind erst abgeliefert. Aber auch MSC, CMA CGM, Maersk und andere Großreedereien lassen ihre Frachter von den Mecklenburgern ausrüsten.
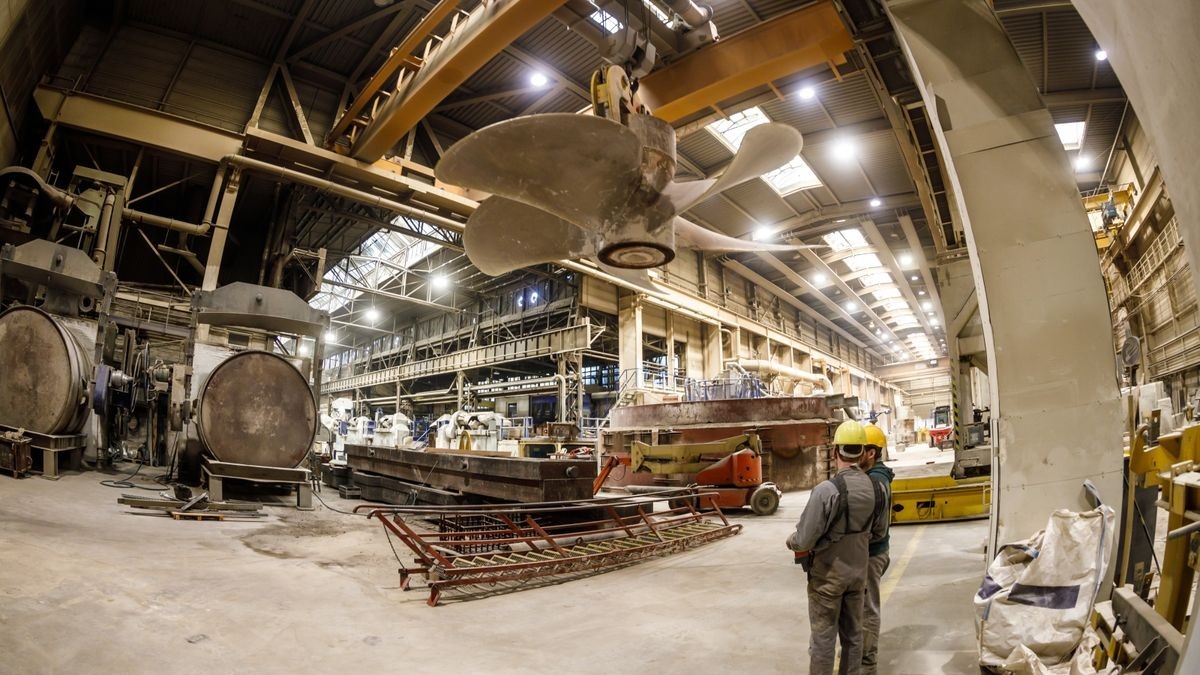
Das Unternehmen sitzt mitten in der Stadt, rund 80 Kilometer Luftlinie von der Küste entfernt. Seine Produkte sind aber auf allen Weltmeeren im Einsatz. Sie sind der Antrieb, der weltweit die Schifffahrt am Laufen hält. „Wir haben gut zu tun“, bestätigt der geschäftsführende Gesellschafter Lars Greitsch und weiß selber, dass das untertrieben ist. Das Orderbuch ist für eineinhalb Jahre voll.
Auch Marine-Verbände rüsten ihre Kriegsschiffe hoch
Die MMG ist in einer glücklichen Phase. Reedereien haben während der Corona-Pandemie den Bau vieler neuer Frachtschiffe in Auftrag gegeben, die nun alle ausgerüstet werden müssen. Zudem zieht auch das Kreuzfahrtgeschäft kräftig an, das während der Pandemie zum Erliegen gekommen war.
Auch sind mehrere Marine-Verbände der Nato Kunden der MMG. Und da das Sicherheitsbedürfnis angesichts der instabilen geopolitischen Lage steigt, werden auch Schiffe hochgerüstet. Schließlich muss die bestehende Weltflotte rasch auf den Klimawandel reagieren und ihren Ausstoß an Treibhausgasen minimieren.
Schiffe müssen zum Treibstoffsparen Tempo drosseln
Die Zeit drängt. Es gibt klare Vorgaben für eine stufenweise Reduktion der Emissionen. Das Zauberwort heißt: Retrofit. Lars Greitsch sitzt in seinem Büro und erklärt, was das heißt. „Die Reedereien müssen Treibstoff und Emissionen absenken und trimmen ihre Schiffe auf mehr Effizienz, indem sie beispielsweise das Tempo drosseln.“ Doch ein anderer Fahrstil benötigt andere Propeller. „Leichtere, effizientere“, sagt Greitsch.
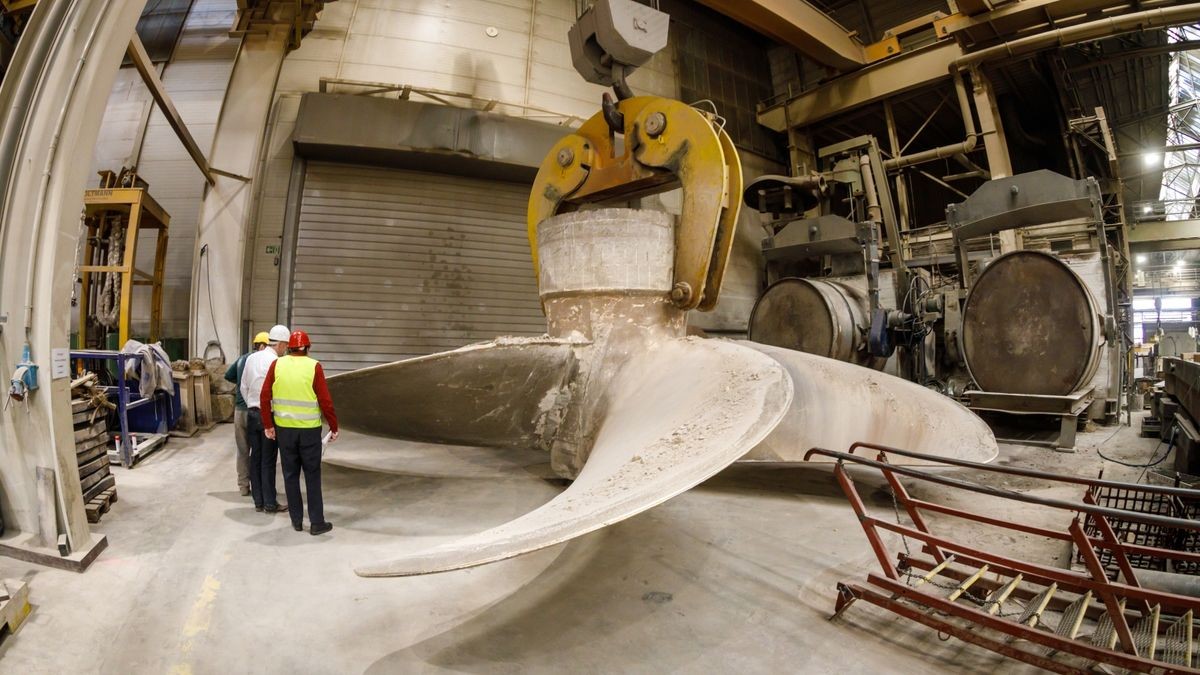
Denn Propeller ist nicht gleich Propeller. Es gibt kleine, große, dicke, dünne, welche mit vier, fünf oder sechs Flügeln. 40 bis 50 verschiedene Designs entwickelt die MMG im Jahr – passend zu jedem Schiff, jedem Motor, der Leistung und der Einsatzart. Die MMG ist ein sogenannter Hidden Champion. Der Weltmarktführer in der Herstellung von Schiffspropellern sitzt in Mecklenburg-Vorpommern.
Effizienz-Propeller sparen täglich Tausende Euro
„Schiffe können mit unseren Effizienz-Propellern zwischen vier und 15 Prozent ihres Verbrauchs einsparen, im Schnitt sind es sieben Prozent“, sagt Greitsch. Bei Treibstoffkosten von 90.000 Euro und mehr pro Tag für ein großes Containerschiff kann Hapag-Lloyd bis zu drei Millionen Tonnen CO₂-Ausstoß pro Jahr sparen und dazu täglich Tausende Euro. „Zum Teil haben sich die Investitionskosten für einen neuen Propeller bereits nach einem Dreivierteljahr amortisiert.“
Ein Arbeiter öffnet ein Rolltor, groß wie bei einem Flugzeughangar. Der inzwischen von den überflüssigen Gussteilen befreite Propeller-Rohling wird von hier aus in die direkt angebaute Fräshalle gehoben. Er wurde vor einer Woche aus seiner Gussform befreit, war da noch 400 Grad heiß. Selbst jetzt spürt man noch auf einen Meter Entfernung die Hitze, die die Bronze ausstrahlt. Es dauert Wochen, bis er komplett abgekühlt ist.
Propeller sind bis zu 100 Tonnen schwer
In der neuen Halle werden die Rohlinge zu Propellern verarbeitet. Die Flügel haben zwar schon ihre klassische, geschwungene Form. Was fehlt, ist das genaue Design. Foto-optische Aufkleber erleichtern den Maschinen die Orientierung, minimale Löcher in der Außenhaut der Flügel zeigen, wie viele Millimeter von der Legierung noch abgeschliffen werden müssen. Denn genau das macht MMG aus: Millimeterarbeit an bis zu 100 Tonnen schweren Gussstücken.
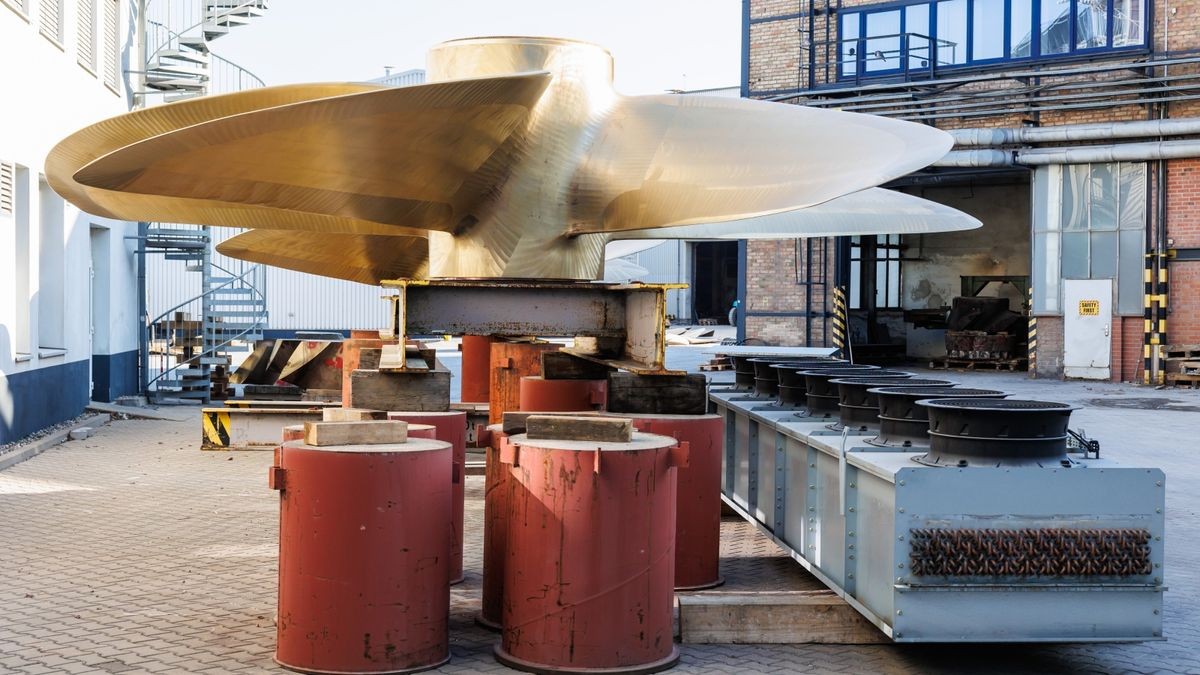
„Die Arbeit verlangt höchste Konzentration. Damit man nicht zu viel von der Legierung abträgt“, sagt Greitsch. Der Maschinenbauingenieur und promovierte Schiffbauer kam 2010 aus Hamburg hierher. Erst als Propellerdesigner, seit 2016 ist er Geschäftsführer des Unternehmens mit langer Tradition.
Entlassungen bei der MMG in der Schifffahrtskrise
1948 hat sich der vor mehr als 150 Jahren gegründete Gussbetrieb auf das Herstellen von Propellern spezialisiert. Zunächst hatte das Unternehmen nur Rohlinge an Werften geliefert. Dann begann es, aus den Rohlingen fertige Propeller zu fertigen. Nach und nach stieg MMG in die Verbundforschung ein, testete verschiedene Legierungen, entwickelte anhand von Strömungssimulationen immer neue Modelle und baute das Wissen auf, von dem man heute lebt.
„Wir haben auch schlechte Zeiten erlebt“, sagt Greitsch und verweist auf die lange Schifffahrtskrise im vergangenen Jahrzehnt. 2018 habe er Mitarbeiter entlassen müssen. 170 Köpfe zählte damals noch das Personal. Heute sind es wieder 210, und Greitsch hat offene Stellen. „Fünf bis sechs weitere Mitarbeiter können wir jederzeit brauchen.“
Der Jahresumsatz liegt heute bei 100 Millionen Euro
Probleme bei der Suche nach Fachkräften kennt er aber nicht. „Wir stellen ein interessantes Produkt her, mit dem sich die Mitarbeiter identifizieren“, sagt er. „Und außerdem zahlen wir gut.“ Rund 25.000 Menschen leben in Waren an der Müritz. Viele sind im Tourismus, in Kliniken vor Ort oder bei der Kommune angestellt. Kaum jemand verdient so gut wie die Mitarbeiter der MMG. „Wir zahlen IG-Metall-Tarif – fast schon auf West-Niveau.“ 100 Millionen Euro beträgt der Jahresumsatz.
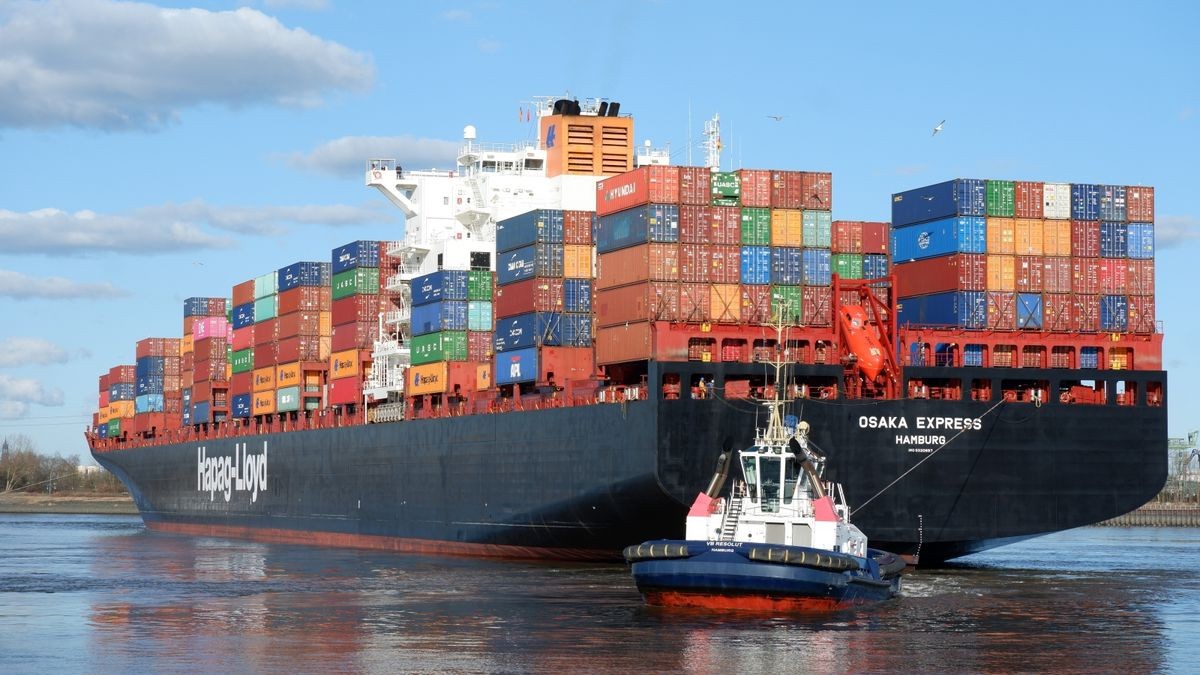
Durch Tor 21 gerät man in eine weitere Halle, die links und rechts durch verschiedene Abteile strukturiert ist. Jedes Abteil für sich ist groß und nach oben hin offen, damit die alles überspannenden Kräne die Propeller darin herablassen können. Hier werden die Propeller abschließend geschliffen. In den rechten Abteilen mithilfe eines Roboterarms, in den linken Abteilen per Hand. Eine rote Kontrastflüssigkeit auf der Legierung zeigt, wo noch nachgearbeitet werden muss.
In Abteil 7 ist wieder ein Produkt für Hapag-Lloyd vor der Vollendung: ein 65 Tonnen schwerer Propeller mit 9,6 Metern Durchmesser, reserviert für ein Containerschiff mit einer Kapazität von 13.500 Standardcontainern (TEU).
Zwei Schiffspropeller werden pro Woche ausgeliefert
Alle Propeller bestehen aus dem gleichen Material: vor allem aus Kupfer, fünf bis zehn Prozent Aluminium und ein wenig Eisen. Gegossen werden die Legierungen wie früher. Zunächst lässt die MMG bei einem Modelltischler ein Holzmodell in Originalgröße für die Gussform herstellen. Diese wird dann aus Magerbeton mit geringem Zementanteil um das Holzmodell herum gefertigt. Das Holz kommt später heraus und die verflüssigte Metalllegierung wird hineingegossen und mit Gewichten beschwert.
Jede Woche liefert die MMG zwei Propeller aus. Sie werden auf Tieflader gehoben, die ihre Fracht per Autobahn zum Hamburger Hafen bringen. Dort werden sie auf Schiffe verladen, die sie hinaus in die Welt bringen. Billig ist das ganze nicht. Etwa 800.000 Euro kostet ein Propeller für ein großes Containerschiff – abhängig vom Kupferpreis.
- Wie zwei Hamburger die Schifffahrt klimaneutral machen wollen
- Riesiger Methanol-Frachter nimmt erstmals Kurs auf Hamburg
- Schifffahrt im Norden: Warum Frachter ihr Tempo drosseln
Sorgen um seinen Rohstoffnachschub macht sich Greitsch aber nicht. „Wir können die alten Propeller, die die Schiffe bisher fuhren, wiederverwenden. Das Metall kann fast ohne Verluste eingeschmolzen und neu gegossen werden.“