Harburg/Meckelfeld. An der Hamburger Stadtgrenze entstehen jedes Jahr rund 600 Kilometer Schienen für die Deutsche Bahn – und andere Großkunden.
- Einem Harburger Unternehmen kommt eine Schlüsselrolle beim Ausbau und der Erneuerung des deutschen Schienennetzes zu.
- Gefertigt werden die Bahnschienen in einem Schweißwerk zwischen Rönneburg und Meckelfeld.
- Abendblatt-Reporterin Angelika Hillmer hat sich den Betrieb einmal näher angeschaut.
Versteckt zwischen der Bahntrasse zum Rangierbahnhof Maschen und einem südwestlich abzweigenden Schienenstrang liegt ein Betrieb im Landkreis Harburg, der eine zentrale Rolle für die Pünktlichkeit der Deutschen Bahn spielt: das „Langschienenschweißwerk“ des Harburger Unternehmens Vossloh Rail Services.
Das Schweißwerk auf der Ortsgrenze von Rönneburg und Meckelfeld fungiert als Scharnier zwischen Walzwerken, die Schienenstränge produzieren, und den Gleisbaustellen: Bevor Schienen verlegt werden können, müssen sie in passgenauen Längen angeliefert werden, etwa wenn Weichen auf der Strecke sind.
Schweißen für die Deutsche Bahn: In Meckelfeld werden Schienen zentimetergenau gefertigt
Imposanter als die Fertigungshalle ist das davor befindliche Schienenlager: An großen Kränen werden tonnenschwere Stränge auf eine Transportschiene gelegt, auf der die Rohlinge in die Halle fahren. Dort werden die Schienen um 60 Meter verlängert: Stahlwerke in Polen, Österreich und Tschechien liefern standardmäßig 120 Meter lange Schienenabschnitte.
Wenn sie Meckelfeld verlassen, sind sie meist 180 Meter lang. Doch auf kilometerlangen Baustellen sind auch maßgefertigte kürzere Abschnitte gefragt. Sie werden bei Vossloh Rail Services zentimetergenau zugesägt und dann in der Reihenfolge, in der sie verbaut werden, auf einen Waggon geladen.
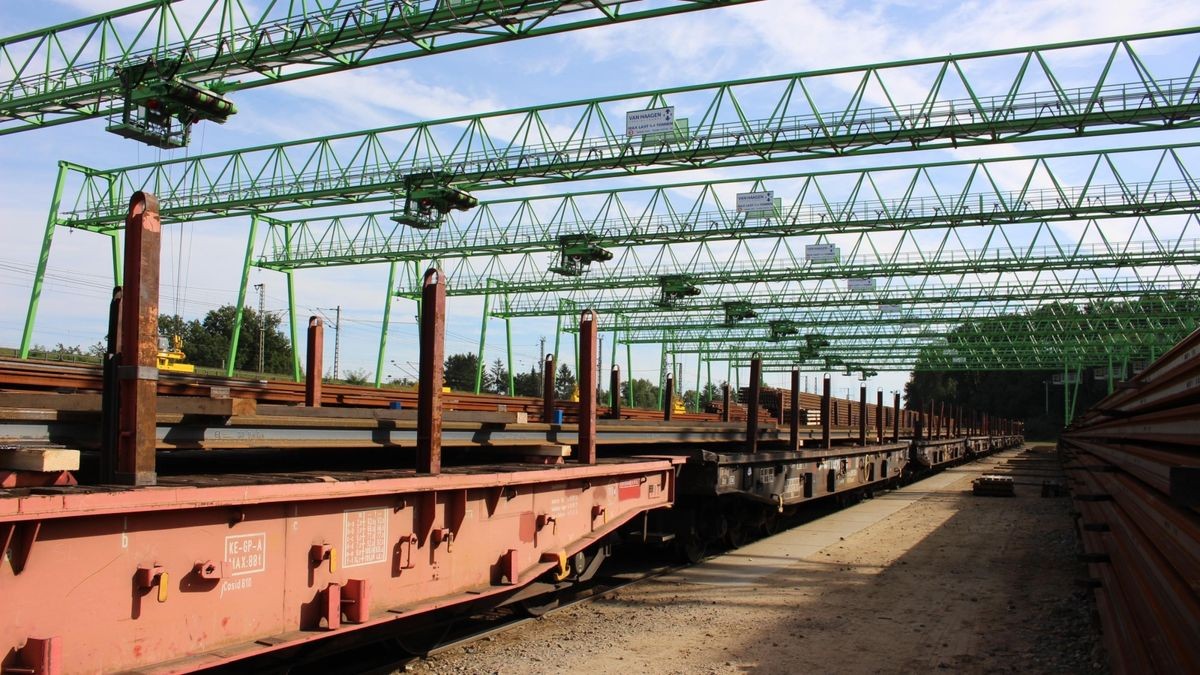
Das Schienenschweißwerk ist die Keimzelle des Harburger Unternehmens, das seinen Hauptsitz an der Hannoverschen Straße hat. Rund 220 Mitarbeiterinnen und Mitarbeiter sind bei Vossloh Rail Services beschäftigt, etwa 30 davon im Schweißwerk in Rönneburg am Reller. Dort wird in zwei Schichten gearbeitet. „1947 wurden hier die ersten Schienen zusammengeschweißt“, sagt Betriebsleiter Stefan Wilcke. „Damals durfte im besetzten Deutschland kaum Stahl produziert werden. Deshalb nutzte man alte, unbeschädigte Schienen, um die Bahninfrastruktur allmählich wieder aufzubauen.“
Für die Deutsche Bahn werden jährlich 600 bis 650 Kilometer Schienen konfektioniert
In den 1950er-Jahren nahmen deutsche Stahlwerke wieder ihren Betrieb auf und lieferten im Laufe der Zeit immer längere Gleise – bis zur heutigen Standardlänge von 120 Metern. Inzwischen werden die Schienen allerdings nicht mehr in Deutschland produziert: Die letzten Stränge „Made in Germany“ lieferte das Duisburger Walzwerk von Thyssenkrupp 2013 aus.
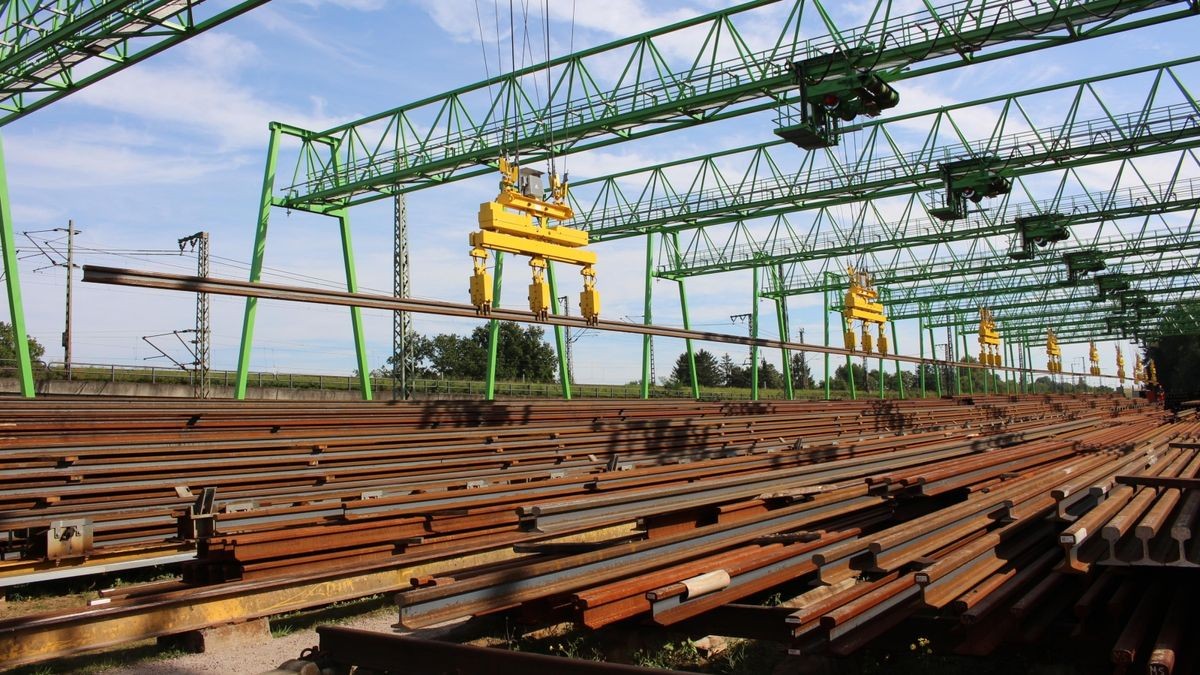
Für die Deutsche Bahn werden jährlich 600 bis 650 Kilometer Schienen konfektioniert. Die meisten werden in Norddeutschland verlegt. Wilcke: „Wir arbeiten möglichst regional, helfen aber auch aus, wenn eines unserer beiden anderen Werke in Nürnberg und Leipzig Kapazitätsengpässe hat.“ So geht in der kommenden Woche eine Lieferung nach München auf die Schiene. Auch das gesamte dänische Gleisnetz wird von Rönneburg beliefert, mit rund 300 Kilometer Schienen im Jahr. Bis zu 50 Kilometer Schienen mit speziellen Profilen reisen jedes Jahr in die Niederlande.
Schienenenden werden mit Stromstößen erhitzt und verschweißt
Zuvor werden sie in der Fertigungshalle konfektioniert. Ein Mitarbeiter glättet per Flex die Enden, bevor sie in einer abgekapselten Maschine ohne Schweißmittel minutenschnell verbunden werden. Dazu werden sie mit Stromstößen von 75.000 Ampere erhitzt. Zum Vergleich: Eine übliche Haushaltssicherung hat 16 Ampere. Die glühenden Enden werden anschließend mit hohem Druck zusammengepresst und die noch rot glühende Schweißnaht geglättet. Wenn die verlängerten Schienenteile später auf der Baustelle verbunden werden, setzt Vossloh ein mobiles Schweißwerk mit dieser Technik ein.
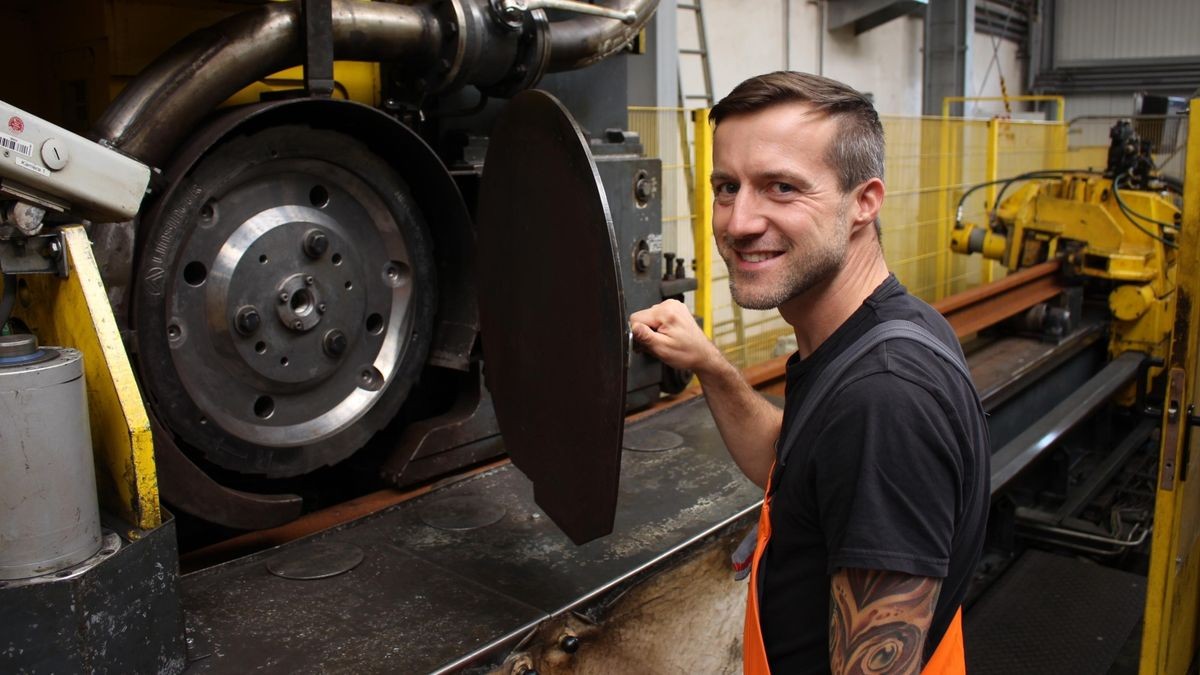
Zum Schluss durchlaufen die Schienenstücke eine Fräsmaschine. „Sie glättet die Oberfläche und macht die Schiene weniger anfällig für Riffelbildung und andere Defekte, verzögert damit den betriebsbedingten Verschleiß“, so Wilcke. Eine Spezialität sind sogenannte Isolierstöße: Ein Stück nicht leitendes Material (Kunststoff) wird an der Schiene montiert. Wenn später ein Zug darüber rollt, stellen die Räder den Stromkontakt her. Das dient der Signalsteuerung und meldet den Leitstellen, dass ein Zug gerade die Stelle passiert (hat).
- Deutsche Bahn: Aus für Neubaustrecke nach Hannover
- A7: Elbtunnel wird im Herbst zweimal für 55 Stunden gesperrt
- Bahn verspätet oder ausgefallen? So gibt es Geld zurück
Schienen-Recycling ist klimaschonend und im Kommen
Die konfektionierten Schienen werden in der Reihenfolge, in der sie benötigt werden, auf Waggons verladen und zu den Baustellen gefahren. Wilcke: „Wir können die Schienen nur ausliefern oder aber mit unserem Schienenwechselzug auch gleich selbst einbauen.“ Wenn die langen Schienenstränge mit der großen Krananlage bugsiert werden, wird sichtbar, dass der massive Stahl durchaus biegsam sein kann – so biegsam, dass mit ihm die geforderten Kurvenradien gelegt werden können.
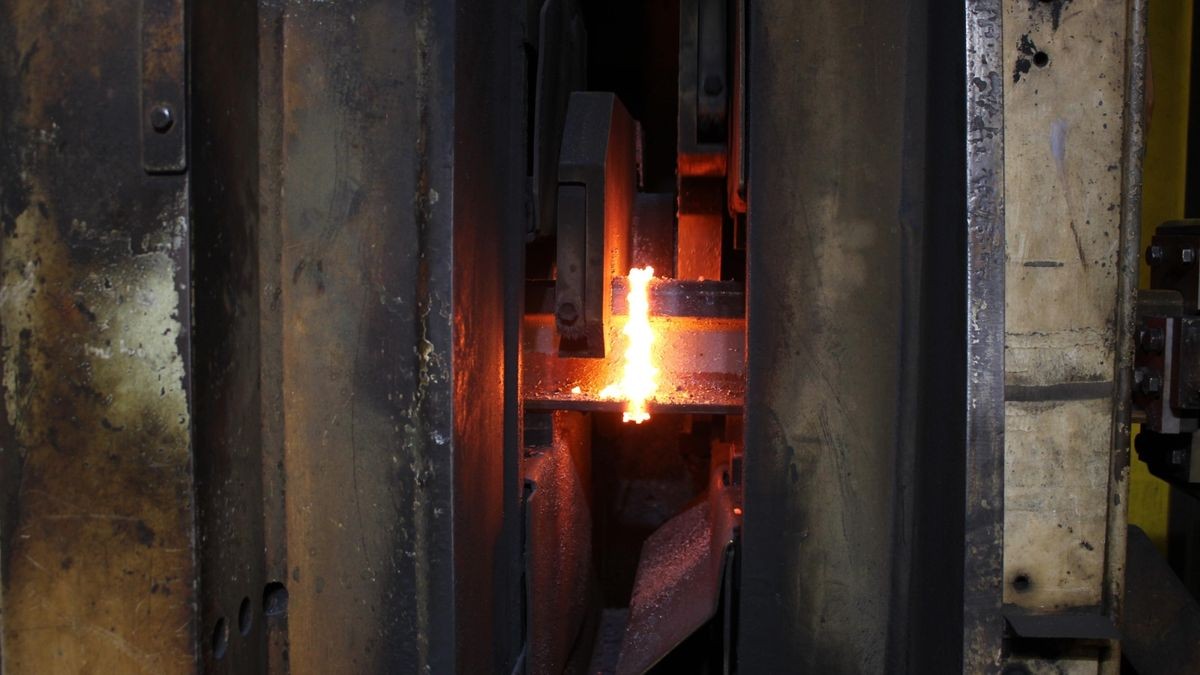
Dank des milliardenschweren Investitionsprogramms der Deutschen Bahn erwartet Marcel Taubert, Geschäftsführer der Vossloh Rail Services, steigende Auftragseingänge. Was ihn besonders freut: Es deutet sich an, dass zukünftig wieder mehr alte Schienen recycelt werden, nachdem die Wiederverwendung in den zurückliegenden Jahren immer mehr abgenommen habe: „Die CO2-Einsparung von aufgearbeiteten Schienen ist groß. Wir stellen uns darauf ein, ins Recycling einzusteigen.“ Ganz wie zu den Anfangszeiten des Werks, nur mit viel ausgefeilterer Technik.