Siegen. Ein neues Press-Verfahren soll Emissionen bei der Fertigung von Autoteilen senken. Ein Team der Uni Siegen arbeitet dran: So funktioniert’s.
Um bis zu 47 Prozent will ein Team der Universität Siegen den CO2-Ausstoß bei der Herstellung von Autobauteile reduzieren. Der Lehrstuhl für Fahrzeugleichtbau entwickelt zusammen mit Industriepartnern ein neuartiges Fertigungsverfahren. Das „Hybridpressen“ soll im Vergleich zur herkömmlichen Produktion eine deutlich bessere Klimabilanz haben.
+++Mehr Nachrichten aus Siegen und dem Siegerland finden Sie hier!+++
„In modernen Autos werden zunehmend so genannte Hybridbauteile eingesetzt“, erläutert die Uni Siegen in einer Mitteilung. Sie bestehen teilweise aus Metall und teilweise aus Kunststoff und reduzieren das Gewicht und den Materialverbrauch. „Sowohl die Produktion als auch die Nutzung der Fahrzeuge schonen somit Rohstoffe und das Klima“, heißt es weiter. Fahrzeugbauer der Uni Siegen hätten bereits vor einigen Jahren ein neuartiges Fertigungsverfahren entwickelt, das die bisherigen drei Arbeitsschritte zu einem einzigen zusammenführt. Die Umformung des Metalls (Schritt 1), die Formgebung des Kunststoffs (Schritt 2) sowie die Verbindung beider Komponenten durch einen chemischen Klebstoff (Schritt 3) erfolgen zeitgleich in einer Presse.
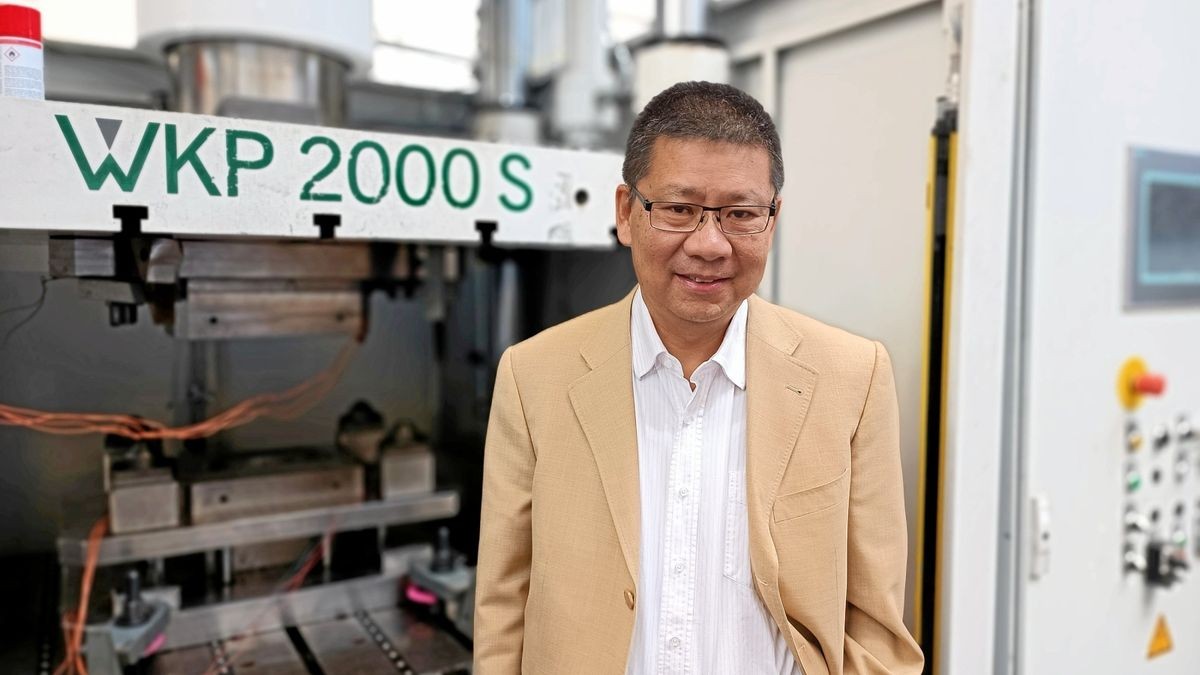
Universität Siegen: Mit weniger Fertigungsschritten in der Automobilindustrie ans Ziel
Gemeinsam mit verschiedenen Partnern aus der Industrie möchten die Wissenschaftler dieses sogenannte Hybridpressen in den kommenden drei Jahren weiterentwickeln. Das Bundesministerium für Wirtschaft und Klimaschutz (BMWK) fördert das gerade gestartete Projekt mit 2,5 Millionen Euro, von denen 520.000 Euro an die Uni Siegen gehen.
+++ Lesen Sie hier: Siegen nicht durch Baustellen lahmlegen: Details zu Uniumzug +++
„Durch das Zusammenführen mehrerer Fertigungsschritte verbraucht unser Verfahren deutlich weniger Energie, was angesichts steigender Energiepreise natürlich ein entscheidender Faktor ist“, sagt Projektleiter Prof. Dr. Xiangfan Fang vom Lehrstuhl für Fahrzeugleichtbau. „Damit einhergehend sinkt die CO2-Emission.“ Sein Ziel ist es, das Hybridpressen so weit zu verbessern, dass es in der Serienproduktion eingesetzt werden kann. Dazu arbeiten er und sein Team mit verschiedenen Unternehmen zusammen: Darunter zwei Automobilzulieferer, ein Werkzeug- und ein Kunststoffhersteller sowie ein Chemie- und ein Stahlkonzern. Außerdem sind die Autohersteller Audi und Ford als begleitende Partner am Projekt beteiligt.
Uni Siegen will neues Verfahren für Automobilindustrie zeitnah zur Marktreife bringen
Am Beispiel von zwei konkreten Autobauteilen soll das Verfahren zur Marktreife gebracht werden: Eine hybride B-Säule und ein Federbeinlager, das ebenfalls teils aus Metall und teils aus Kunststoff besteht, wollen die Projektpartner mit dem Hybrid-Pressverfahren fehlerfrei herstellen. „Metall und Kunststoff haben sehr unterschiedliche Eigenschaften. Will man beide Materialien in einer einzigen Produktionslinie zu einem Bauteil verarbeiten, muss man deshalb besonders darauf achten, dass im Produkt keine Fehler entstehen und die Stabilität hoch bleibt“, erklärt Prof. Fang.
+++ Auch interessant: Siegen: E-Autos fordern Mechatroniker – und ihre Lehrer +++
Um das zu garantieren, möchten er und sein Team das Hybridpressen im Rahmen des aktuellen Projekts verfeinern: Wurden das Stahlblech und der Kunststoff bisher simultan in einem gemeinsamen Werkzeug um- beziehungsweise urgeformt und miteinander verbunden, so soll das „neue“ Pressverfahren zweistufig arbeiten, erklärt Prof. Fang: „Um eine höhere Produktqualität zu erzielen, führen wir die Metall-Umformung separat durch. Das fertig geformte Blechteil wird dann in Stufe zwei mit dem erwärmten Kunststoff zusammengebracht, der Kunststoff wird dabei gleichzeitig geformt und mit dem Blechteil verbunden.“ Der Clou: Beide Stufen erfolgen innerhalb eines einzigen Pressvorgangs. Die Energie für die Presse muss also nach wie vor nur einmal aufgewendet werden, Energieverbrauch und CO2-Ausstoß bleiben entsprechend gering.
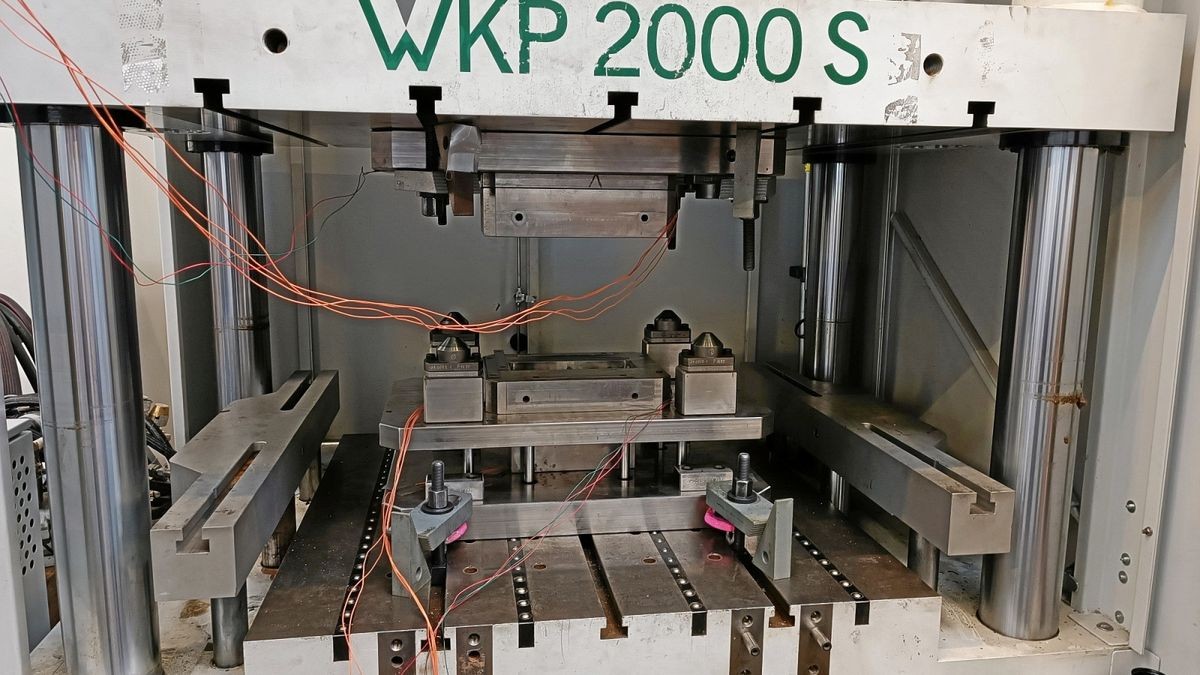
Uni Siegen erwartet großes Interesse der Industrie an neuem Hybridpress-Verfahren
„Das Interesse an dem neuen Verfahren seitens der Industrie dürfte angesichts des rasanten Anstiegs der Energiekosten noch steigen“, schreibt die Uni Siegen. Zum Einsatz kommen könne es – wenn alles nach Plan läuft – in einigen Jahren. Werde das dreijährige Forschungsprojekt erfolgreich abgeschlossen, schließe sich die Vorentwicklung seitens der Automobilzulieferer an. „Wir hoffen, dass das Verfahren nach diesen Schritten freigegeben wird“, sagt Prof. Fang. „Es wäre ein toller Erfolg, wenn eine Siegener Entwicklung künftig in der Serienproduktion von Autoteilen eingesetzt würde.“
+++Die Lokalredaktion Siegen ist auch bei Facebook!+++