Hohenlimburg. Mehr als 10 Millionen Euro stecken die Kaltwalzer der Bilstein Group aus Hagen in das Projekt „Bilcut“ – den Laser-Zuschnitt von Formplatinen
Rund 10,8 Millionen Euro investieren die Kaltwalzer der Bilstein Group in eine neue Unternehmenssparte. In der Produktions- und Vertriebsgesellschaft „Bilcut GmbH“ soll Stahlband künftig auf neue Art per Laser hochpräzise zu Formplatinen geschnitten werden, wie sie die Automobilindustrie für Karosserie-Teile benötigt. „Wir gehen vom Kaltband aus einen Schritt weiter in Richtung Weiterverarbeitung, den wir so noch nicht gemacht haben“, sagt Jörg von Prondzinski, Leitung Anwendungsentwicklung bei Bilstein, der das Projekt mit verantwortet.
Millionen-Fördermittel
Die innovative und ressourcenschonende Herangehensweise gefiel dabei offenkundig in Berlin: So kam vergangene Woche Bettina Hoffmann, Parlamentarische Staatssekretärin des Umweltministeriums, in die Unternehmenszentrale nach Hohenlimburg, um dort einen Förderbescheid über 2.167.000 Euro für „Bilcut“ zu übergeben. Unterstützt von der Effizienz-Agentur NRW hatte sich die Bilstein Group erfolgreich für eine Förderung im Rahmen des Umweltinnovationsprogramms bewerben können.
+++ Lesen Sie auch: Hohenlimburg: Walzindustrie plant grüne Zukunft +++
Bewegen muss sich das Kaltwalzunternehmen von der Lenne auch deshalb, weil sich die Autobranche im Umbruch befindet. „Unser Kundenumfeld ändert sich rapide mit Blick auf die E-Mobilität und Formplatinen sind hier ein Zukunftsthema.“
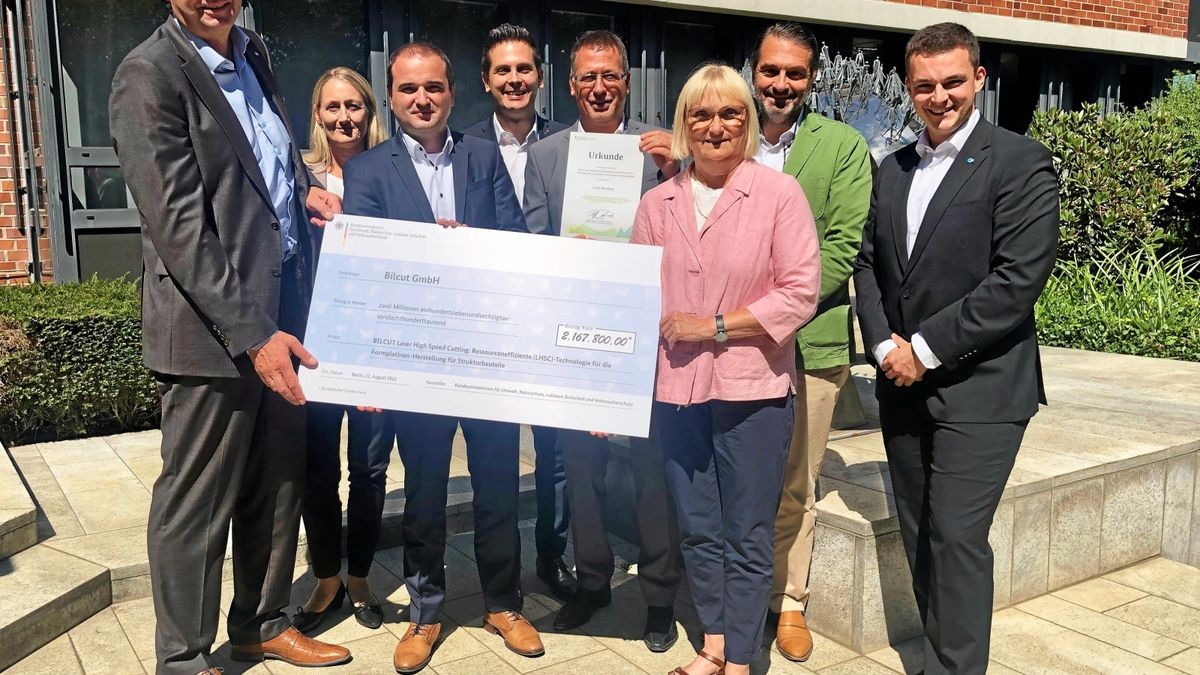
Passgenaue Bauteile
Immer mehr Fahrzeuge etwa mit Elektro- und Hybridantrieben kommen auf den Markt, zusätzlich zu der weiter großen Palette der Fahrzeugmodelle mit Verbrennungsmotor. Viele Modelle, die passgenaue Bauteile benötigen. Mit der neuen Anlage könne man flexibler auf die Wünsche der Kunden reagieren, so von Prondzinski.
Weniger CO2-Emmissionen
Zudem werde durch eine gezielte Verschachtelung der Platinen auf dem Band der Verschnitt reduziert und das Material entsprechend besser ausgenutzt. Heißt: weniger Abfallprodukte und weniger CO2-Emmissionen pro Bauteil, die hier anfallen. Zwar sei das Verfahren, Formplatinen mit dem Laser direkt vom abgewickelten Coil zu schneiden, nicht gänzlich neu. Jedoch unterscheide sich das Verfahren in innovativen Details von bestehenden Technologien.
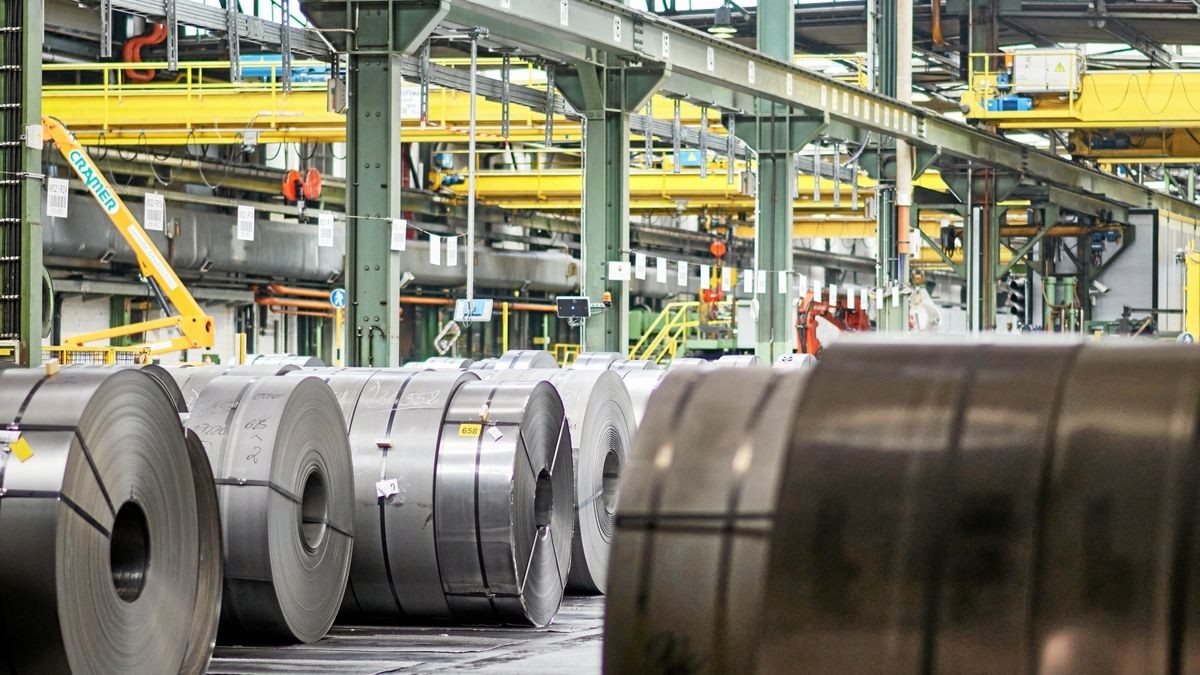
Gemeinsam mit dem Fraunhofer Institut für Lasertechnik in Aachen und einem Anlagenbauer aus Süddeutschland wird zurzeit ein Prototyp für die Laser-Zelle gebaut. In 2023 soll der Prototyp auf Tauglichkeit getestet, bis Anfang 2025 die neue „Bilcut“-Anlage gebaut und in Betrieb sein.
+++ Lesen Sie auch: Hagen: Bilstein schließt Liefervertrag für grünen Stahl +++
Die Anlage allein erstreckt sich von der Abwicklung der Coils über die Laser-Zelle bis zur Abstapelung der fertigen Formplatinen auf 60 Meter in der Länge und 20 Meter in der Breite. Zuzüglich Flächen rundherum etwa für Logistik und die Fahrwege der Stapler brauche es da eine Halle von rund 100 Metern Länge und 25 Metern Breite, beziffert von Prondzinski.
Suche nach Standort
Zu groß für den Produktionsstandort von Bilstein im Weinhof, der eingepfercht zwischen Lenne, Wohnhäusern und dem Areal an der Färberstraße rund um das Injoy liegt. Zudem braucht es eine Halle mit einem Kran, der mindestens 35 Tonnen Gewicht heben kann, für die schweren Coils.
+++ Lesen Sie auch: Flut in Hagen: Kaltwalzer wollen Hochwasserschutz angehen +++
„Wir befinden uns in Gesprächen mit der Stadt Hagen über nutzbare Gewerbeflächen einerseits und suchen andererseits nach vorhandener Hallenstruktur, die zudem gut zugänglich für die Anfahrt von Lkw ist“, so von Prondzinski. Die Suche nach einem Standort sei nicht einfach, „aber wir haben eine mögliche Fläche im Blick.“ Genauer wollte er noch nicht werden.