Duisburg. Das sind die Standorte der Stahl-Hersteller in Duisburg – und diese Veränderungen bringt die Umstellung auf eine klimafreundliche Produktion.
Mit einer Produktion von rund 16,4 Millionen Tonnen pro Jahr ist Duisburg der größte Stahlstandort Europas. Weil die Verhüttung von Eisenerz und Kokskohle auf der „Hochofenroute“ allein in Duisburg jährlich etwa 20,4 Millionen Tonnen CO₂ verursacht, streben die Unternehmen einen Technologiewechsel zur klimafreundlichen Direktreduktion auf Wasserstoff-Basis an. Hier geben wir einen Überblick über die wichtigsten Anlagen in Duisburg und die Entwicklung der Standorte:
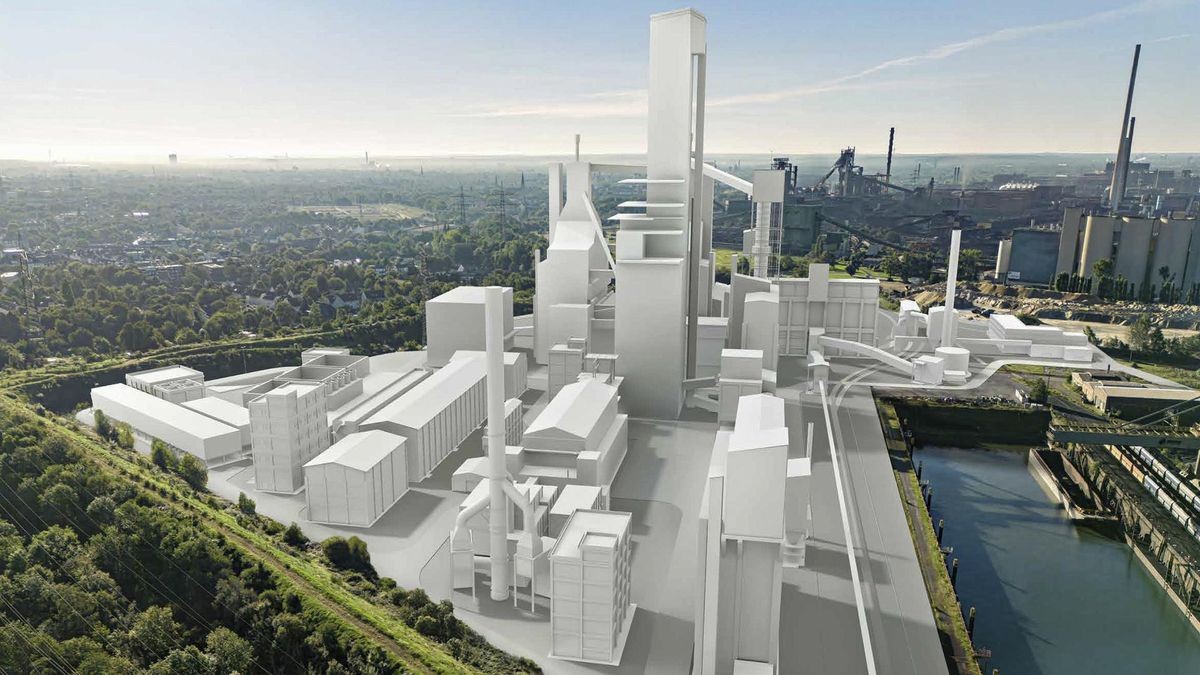
Hinweis der Redaktion: Dieser Artikel wurde erstmals am 2. April veröffentlicht, also bevor Thyssenkrupp Steel am 11. April tiefe Einschnitte an seinen NRW-Standorten ankündigte.
Lesen Sie auch diese Artikel über Duisburg, Europas größten Stahl-Standort:
- Thyssenkrupp Steel: Ernüchterung verdrängt Aufbruchstimmung
- Thyssenkrupp: Fast ein Viertel der Stahlproduktion fällt weg
- Kommentar: Schrumpfkur stellt Thyssenkrupp vor Zerreißprobe
- Thyssenkrupp Steel bereitet Einschnitte vor: Unruhe ist groß
- TKS, HKM und Arcelor: Das ist die Stahlhochburg Duisburg
- Thyssenkrupp und HKM: April als Monat der Entscheidungen?
- IG Metall warnt: Es steht schlimm um Thyssenkrupp
- Deutschlands klimaschädlichste Fabriken stehen in Duisburg
Thyssenkrupp Steel: Das Herz aus Stahl schlägt im Duisburger Norden
Mit vier Hochöfen, den Werken in Hamborn, Bruckhausen und Beeckerwerth, jeweils zwei Stahlwerken, Warmbandwerken und Kaltwalzwerken, dazu eine Gießwalzanlage, Feinspalt-, Veredelungs- und Beschichtungsanlagen, bildet Thyssenkrupp Steel (TKS) im Duisburger Norden alle Schritte der Stahlherstellung ab. Diese beginnt in der werkseigenen Kokerei und Sinteranlage, das entstehende Gas wird in den Prozessen entweder direkt verwertet oder in eigenen Kraftwerken (Hermann Wenzel, Ruhrort) verstromt und zu Versorgung des integrierten Hüttenwerks eingesetzt.
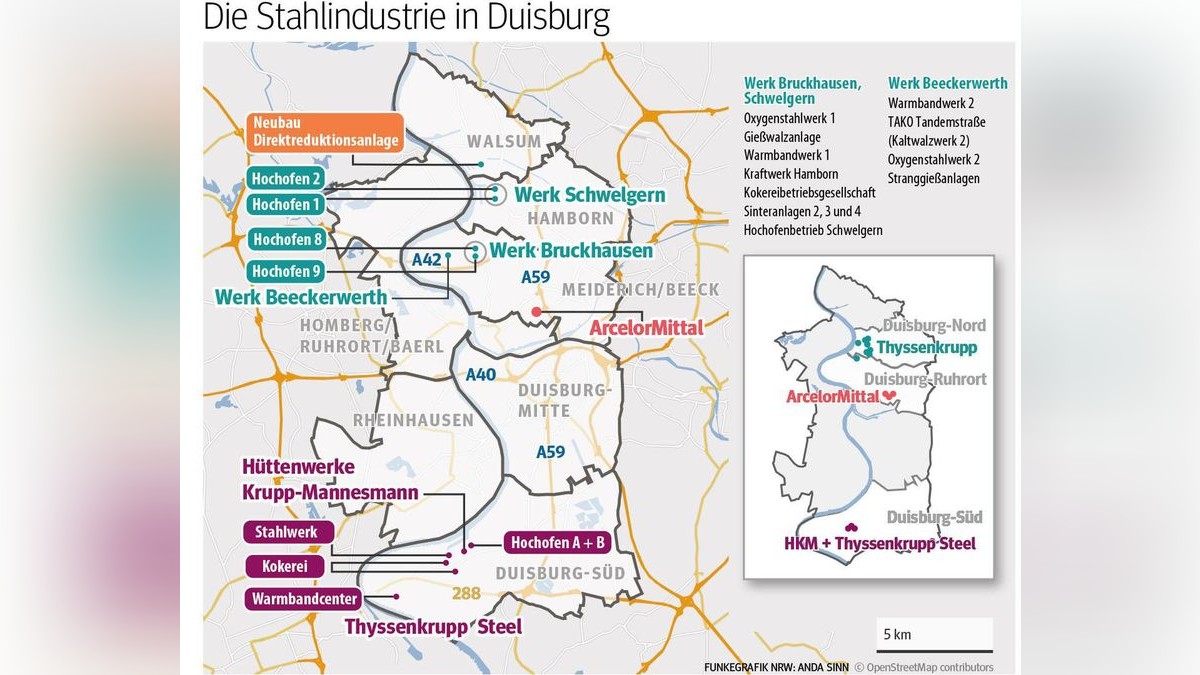
[Nichts verpassen, was in Duisburg passiert: Hier für den täglichen Duisburg-Newsletter anmelden.]
Im Hüttenheimer Warmband-Center werden pro Jahr rund 850.000 Tonnen Stahlbleche gebeizt, geölt und nach Kundenbedarf gespalten. Das Grobblech-Werk auf dem Werksareal im Duisburger Süden hatte TKS bereits vor einigen Jahren geschlossen, hier sollen künftig Unternehmen mit Wasserstoff-Bezug angesiedelt werden.
Für die erste Direktreduktionsanlage (DRI) im äußersten Norden des Werksgeländes in Walsum werden bereits die mächtigen, bis zu 30 Meter tiefen Fundamente gegossen für die knapp 150 Meter hohe Anlage. In fünf Millionen Arbeitsstunden von bis zu 2000 eigenen Mitarbeitenden wird der Düsseldorfer Anlagenbauer SMS die Direktreduktion und zwei Einschmelzer bis Ende 2026 aufbauen. Fortan soll sie 2,5 Millionen Tonnen Roheisen pro Jahr produzieren. Die Anlage soll zunächst mit Gas, später mit grünem Wasserstoff befeuert werden. Der Bedarf ist mit rund 143.000 Tonnen pro Jahr gewaltig.
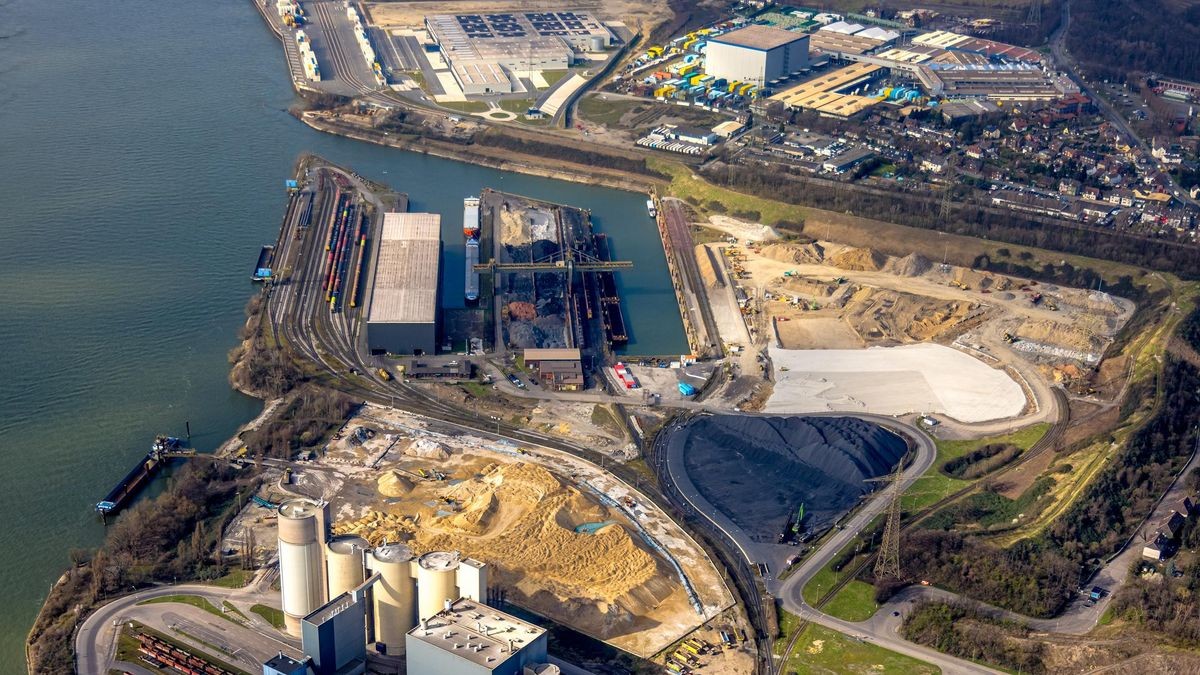
Das Drei-Milliarden-Projekt kann Thyssenkrupp Steel nur mit finanzieller Unterstützung des Bundes (eine Milliarde Euro) und des Landes NRW (700 Millionen Euro) umsetzen. Die Politik sichert damit den Erhalt der nationalen Stahlproduktion, die am Anfang einer langen Wertschöpfungskette steht, und ihrer Arbeitsplätze. Thyssenkrupp Steel beschäftigt allein in Duisburg 13.500 Menschen. Aus Sicht von TKS ist der Einstieg in die neue klimaneutrale Produktion alternativlos: Die konventionelle Produktion wird mittelfristig wegen der steigenden Bepreisung des CO₂-Ausstoßes unrentabel.
Auch interessant
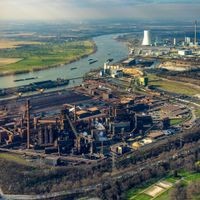
Technologiewechsel vollzieht sich über zwei Jahrzehnte
Der Technologiewechsel wird sich dennoch über Jahrzehnte erstrecken. Denn im Zuge des Hochlaufs der DRI-Anlage soll zunächst nur einer der vier Hochöfen im Duisburger Norden stillgelegt werden. Welcher das sein wird, könnte sich auch an der Restlaufzeit bis zum Ende ihrer bis zu 20 Jahre langen „Hochofen-Reise“ bemessen.
Die Zahlen sprechen für den Weiterbetrieb der Hochöfen 1 (modernisiert 2021) und 2 (2014) in Schwelgern. Der Hochofen 9 in Buckhausen, mit Baujahr 1962 der älteste, wurde 2012 modernisiert. Der benachbarte Hochofen 8, er ging 2007 in Betrieb, wäre der erste, bei dem eine Neuzustellung ansteht. Diese kostet einen dreistelligen Millionen-Euro-Betrag. Bis in die 2040er Jahre könnte also die konventionelle Produktion noch weiterlaufen. So lange werden auch Kokerei und Sinteranlagen noch benötigt.
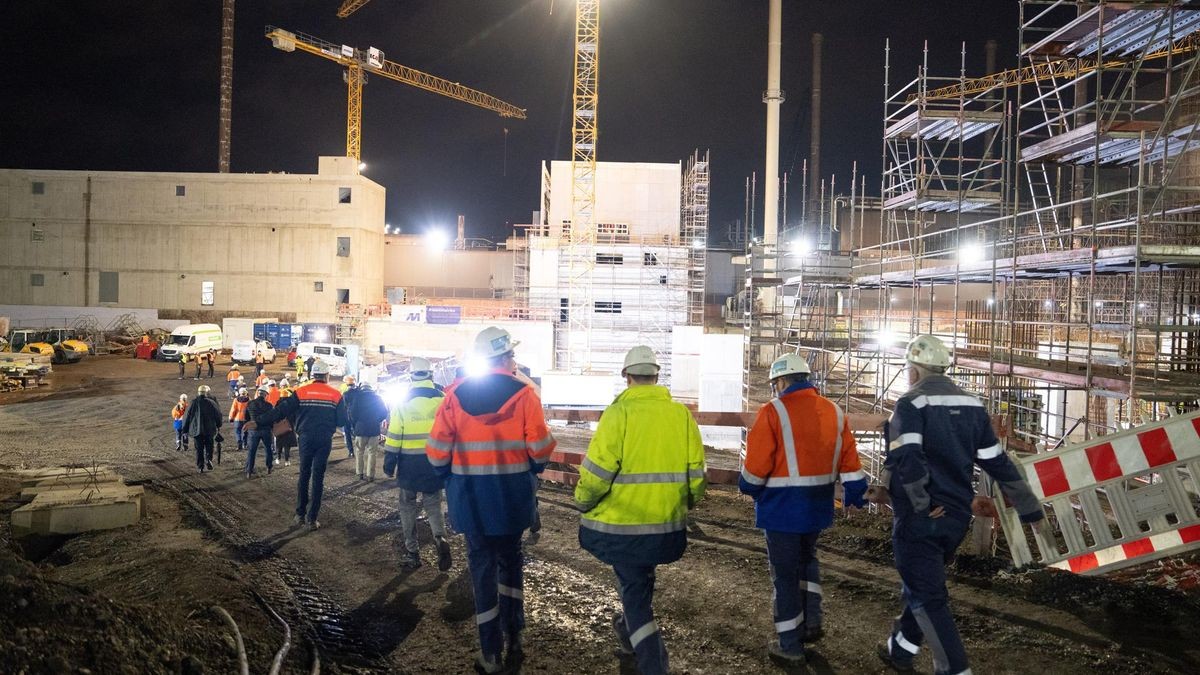
Modernisierung der Anlagen verbessert die Wettbewerbsfähigkeit
Schon seit einigen Jahren geht der Konzern mit der „Strategie 20-30“ die Modernisierung seiner Standorte mit einem Gesamtvolumen von über 800 Millionen Euro an. Ein neuer Hubbalken-Ofen für rund 50 Millionen Euro ging im November 2022 im Warmbandwerk Beeckerwerth in Betrieb, seit dem vergangenen Herbst läuft die Großbaustelle in Bruckhausen für ein neues Brammenlager, den Ausbau der Gießwalzanlage zum Warmbandwerk 4, den Um- und Neubau von zwei Stranggussanlagen und den Bau von zwei weiteren Hubbalkenöfen. Mit dieser Investitionen in die Qualität der Produkte werde TKS „der Nachfrage nach geringeren Toleranzen sowie höheren Festigkeiten und optimierten Oberflächen gerecht“, sagt Produktionsvorständin Dr. Heike Denecke-Arnold.
Hüttenwerke Krupp-Mannesmann (HKM): Das Werk im Süden plant den Technologiewechsel
Die Hüttenwerke Krupp-Mannesmann (HKM) sind kein unabhängiges Unternehmen, sondern Lieferant von Vormaterial für ihre Gesellschafter Thyssenkrupp Steel (50 Prozent der Anteile), Salzgitter Mannesmann GmbH (30 Prozent) und Vallourec (20 Prozent). Das Hüttenwerk im Duisburger Süden produziert mit rund 3100 Beschäftigten in seinen beiden Hochöfen die vereinbarte Menge, derzeit rund vier Millionen Tonnen pro Jahr.
Vallourec-Ausstieg: Suche nach einem neuen Investor
Mit der werkseigenen Kokerei, vor zehn Jahren für 400 Millionen Euro auf eine Kapazität von 2,3 Millionen Tonnen Koks erweitert, ist das zweitgrößte deutsche Hüttenwerk auch Koks-Lieferant für seine Gesellschafter TKS und Salzgitter.
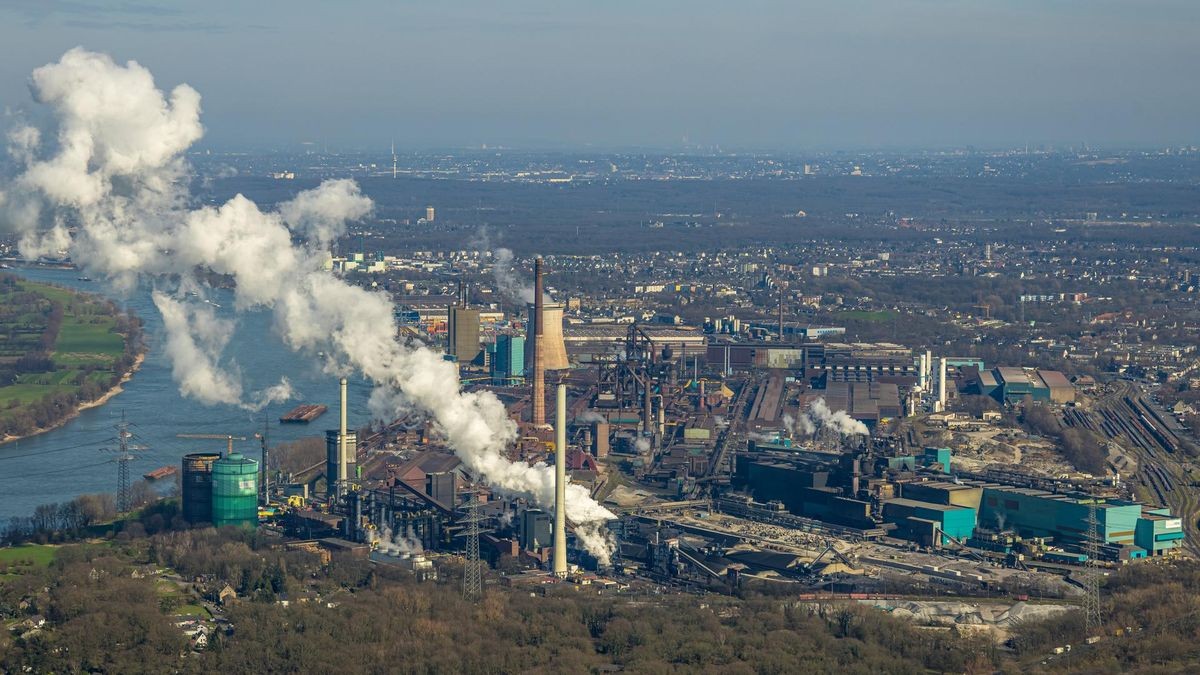
Das liegt unterhalb der Kapazität des traditionsreichen Standorts, an dem seit fast 125 Jahren Stahl gekocht wird. Mit der Einstellung der Grobblech-Produktion im benachbarten Werk von Thyssenkrupp Steel verlor die HKM einen wichtigen Kunden, ein weiterer ist Vallourec – mit der Einstellung der Produktion in Mülheim und Düsseldorf verbindet der Rohr-Produzent auch seinen Abschied als Gesellschafter. Die Suche nach einem neuen Investor läuft.
Einer von zwei Hochöfen vor dem Ende seiner Reise
Die Expertise der HKM ist das Vergießen flüssigen Stahls zu einem festen Strang, die Rundstäbe werden zu nahtlosen Rohren weiterverarbeitet, die sich etwa in Pipelines in aller Welt finden. Außerdem entstehen im Stahlwerk durch die Zugabe anderer Metalle über 100 verschiedene Stahlgüten nach den Erfordernissen der Kunden, viele von ihnen aus dem mittelständischen Maschinen- und Anlagenbau in NRW.
Um ihren Bestand zu sichern, planen auch die HKM den Bau einer Direktreduktionsanlage. Hier drängt die Zeit, denn der Hochofen A erreicht schon in wenigen Jahren das Ende seiner Reise. Vor vier Jahren nutzte das Unternehmen die Corona-Absatzkrise zu einer Reparatur der zwölf Jahre alten Ausmauerung des Hochofens. Sie brachte eine Laufzeit von sechs bis acht weiteren Jahren.
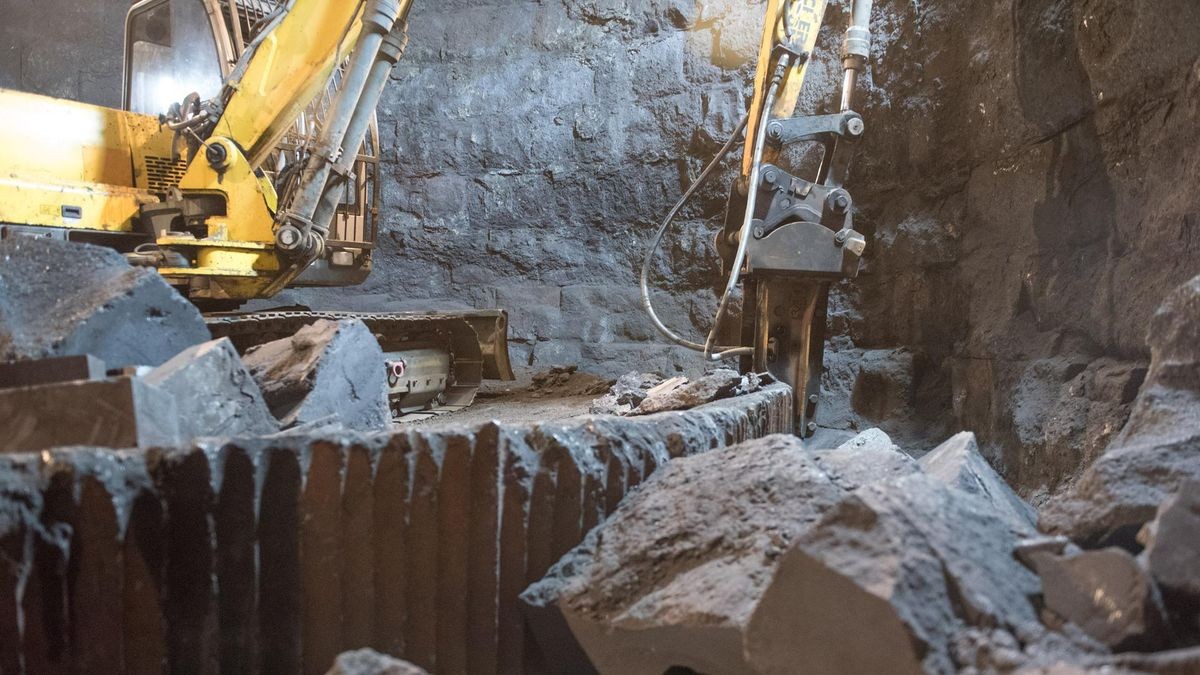
Der Hochofen B wurde zuletzt 2017 neu zugestellt, kann also mindestens noch bis Mitte der 2030er Jahre laufen. Ein Ein-Ofen-Betrieb, fürchten Betriebsrat und IG Metall, werde den Bestand des Werkes nicht sichern.
Die Entscheidung über die Milliarden-Investition in eine DRI-Anlage obliegt aber den Gesellschaftern, entscheidend ist wie auch bei TKS eine Förderung, wahrscheinlich über die Klimaschutz-Verträge des Bundeswirtschaftsministeriums.
ArcelorMittal: Ruhrorter Drahtwerk wartet auf Förderung für Lichtbogenofen
Auch das Drahtwerk von ArcelorMittal in Ruhrort (900 Beschäftigte) steht vor dem Technologiewechsel zur klimafreundlichen Produktion. Noch bezieht das Werk sein Roheisen für die Jahresproduktion von rund 450.000 Tonnen von Thyssenkrupp Steel im Stadtnorden, doch der Liefervertrag endet 2027.
Auch interessant
Der Plan: In einem neuen Lichtbogenofen, in den das Unternehmen 270 Millionen Euro investieren will, sollen künftig Schrott und Eisenschwamm aus der Hamburger Direktreduktionsanlage des Konzerns eingeschmolzen werden.
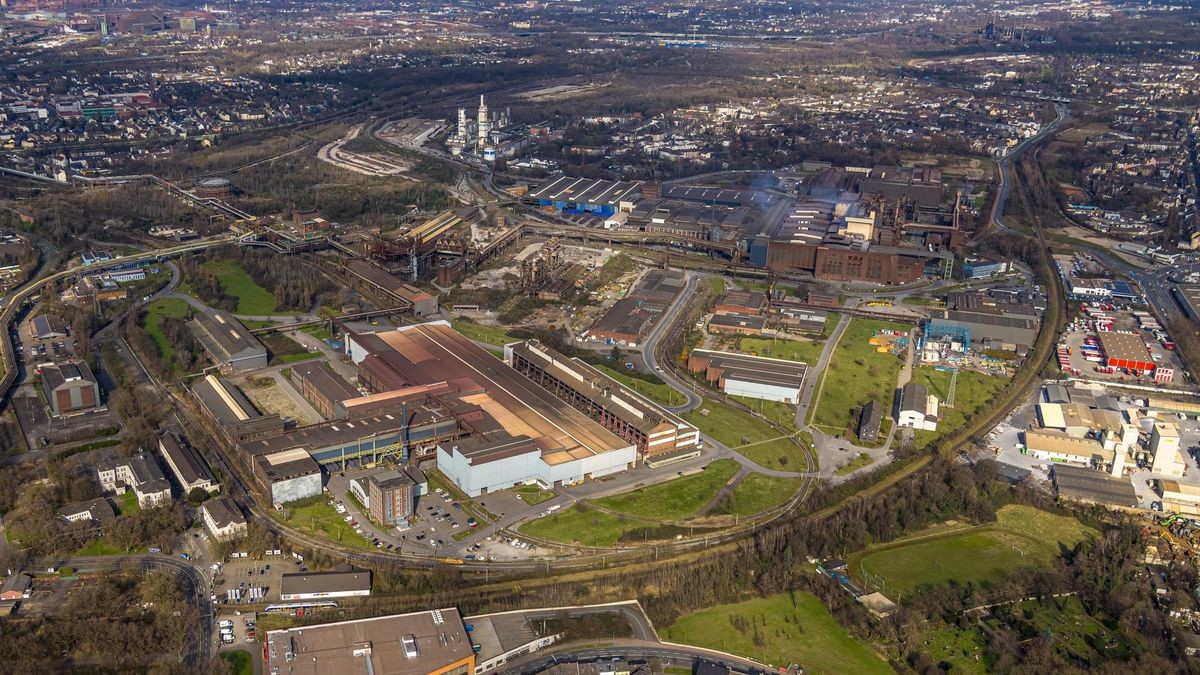
ArcelorMittal in der Warteschleife für passendes Förderprogramm
Genau da liegt jetzt das Problem: Die künftige CO₂-Einsparung findet also nicht in Ruhrort statt, sondern im Hochofenprozess bei TKS. Deshalb ist eine Förderung aus dem Programm für Vorhaben, die den Klimagas-Ausstoß unmittelbar reduzieren, nicht möglich. So wartet das Projekt seit zwei Jahren auf ein Programm, dessen Richtlinien zum Ruhrorter Projekt passen.
Weil der Lichtbogenofen noch bestellt, gebaut und errichtet werden muss, drängt die Zeit. Ein passendes Programm für die staatliche Förderung von Transformationstechnologie sollte Anfang 2024 schon freigegeben worden, bisher gibt es noch kein grünes Licht für die Unterstützung der Ruhrorter Investition.