Bochum. .
Das Bochumer Warmwalzwerk kann bald bis zu 4,2 Millionen Tonnen Warmbandstahl produzieren. Bislang fehlte Thyssen-Krupp dazu das entsprechende Material. Doch das kommt künftig auch aus dem Stahlwerk in Brasilien. Nun ist die erste Fuhre da.
Jetzt sind die ersten Brammen aus Brasilien im Bochum eingetroffen. Um mehr zu produzieren, fehlte dem ThyssenKrupp-Werk bislang das entsprechende Vormaterial. Bald könnte das Werk bis zu 4,2 Millionen Tonnen Warmbandstahl im Jahr liefern.
Der Zugführer hat die Ruhe weg – seine mit 1000 Tonnen Stahlbrammen beladenen 15 Waggons steuert er ganz cool vom ersten Waggon aus, mit der Fernsteuerung. Die Diesellok drückt von achtern und bremst sanft ab. Dass Werksleiter Klaus Kurke samt Tross über die Verspätung von über einer halbe Stunde ein wenig ungehalten ist, ficht den Eisenbahner wenig an. Was soll’s auch, für ihn sehen die Brammen aus wie immer: stahlgrau mit Rostspuren. Dass es die Ersten sind, die aus Brasilien nach Bochum kommen, spielt für ihn keine Rolle.
Auch interessant
Dabei verrät eine ganz einfache Prüfung die Herkunft. Gleich nebenan auf dem Lagerplatz für Stahlbrammen auf dem Gelände des ThyssenKrupp-Werkes liegen nämlich solche aus dem nahen Duisburger Werk. Optisch kein Unterschied. Doch wer die Hand auflegt, zuckt unwillkürlich zurück. Der Stahl ist noch warm, fast heiß – dieses Material hatte es nicht so weit.
2500 Tonnen werden in Bochum weiterverarbeitet
Die anderen sind schön kühl. Kein Wunder: Vor drei Wochen wurden 10 000 Tonnen Stahl im Werkshafen Walsum mit Blasmusik in Empfang genommen. 18 Tage lang waren sie auf See, nachdem sie im neuen ThyssenKrupp Hüttenwerk in der Bucht von Sepetiba in Brasilien produziert worden sind. Ein Viertel dieser ersten Lieferung, also 2500 Tonnen, sind bestimmt für die Weiterverarbeitung im Werk Bochum, genauer für das Warmbandwalzwerk. So ist der Anflug von Zorn bei Werksleiter Klaus Kurke schnell verflogen. Denn erst jetzt machen die Investitionen von mehr als 100 Millionen Euro in Bochum Sinn. „Um mehr zu produzieren, fehlte uns bislang das entsprechende Vormaterial.“ Für viel Geld musste von anderen Stahlwerken zugekauft werden, denn bei der startenden Konjunktur waren die eigenen Hüttenwerke in Duisburg schnell ausgelastet.
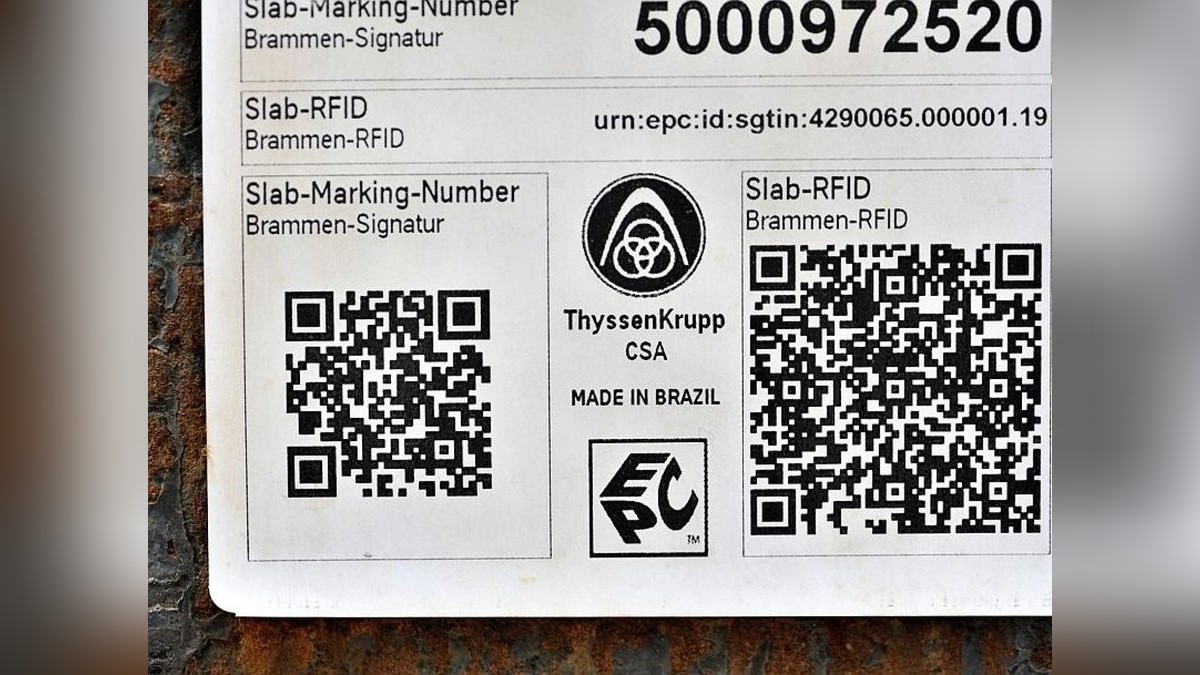
Spielt die Konjunktur mit, könnte Bochum bald seine Höchstleistung, die Produktion von bis zu 4,2 Millionen Tonnen Warmbandstahl im Jahr, erreichen. Vor dem Umbau waren es rund 600 000 Tonnen weniger. Damit alles rund läuft, nimmt ThyssenKrupp noch einmal Geld in die Hand. Allein der Einbau einer Walzenverschiebung schlägt mit 38 Millionen Euro zu Buche. „Die Kunden wollen flachere Profile, dafür ist diese Investition notwendig“, so der Werksleiter. Den Stillstand von 16 Tagen nimmt man dafür gern in Kauf.
Kapazität des Lagers wird ebenfalls erhöht
Mittlerweile hat die Lokomotive einen Teil der 15 Waggons in die riesige Werkshalle gedrückt. Anhand der unscheinbaren weißen Aufkleber „Made in Brazil“, steht wie im Kaufladen auf den Zetteln, lassen sich die Brammen genau zuordnen, ihr Weg aus Brasilien über den Antlanitik und weiter vom Umschlaghafen Rotterdam bis nach Bochum lässt sich mit dieser RFID-Technologie genau verfolgen. Ein unsichtbarer Speicherchip gibt Auskunft. Die Informationen sind jederzeit mit einem Scanner ablesbare Die Technik ähnelt den Geräten an profanen Supermarktkassen.

Frank Schlömann zeigt sich im Werk als Teamleiter für den Ofenbereich und die Brammenlogistik zuständig. „Schon am Mittwoch gehen die Brammen in die Produktion.“ Ein Zeichen, wie dringend sie erwartet wurden.
In den nächsten zwei Jahren soll die Kapazität des Lagers ebenfalls erhöht werden. Bis zu 60 000 Tonnen Stahl könnten dann dort lagern, was gar nicht so viel ist, denn das Werk schafft es, in guten Tagen bis zu 13 000 Tonnen Stahl zu Coils zu verarbeiten.