Hamburg. Der Flugzeugbauer fährt die Fertigung der A320-Familie hoch. Für das neue “grüne“ Wasserstoffflugzeug liegen drei Konzepte vor.
Die riesige Halle 260 bei Airbus auf Finkenwerder steht für den Wandel des Konzerns. Bis vor wenigen Jahren wurde in ihr noch das größte Passagierflugzeug der Welt hergestellt. Nach dem Produktionsaus für den A380 wegen zu geringer Nachfrage wird hier nun an dem Verkaufsschlager A320-Familie gearbeitet. Fast 20 Rumpfabschnitte stehen nebeneinander. Manager André Walter stellt sich für die Fotografen in eine der „Tonnen“ genannten Abschnitte. Sie trägt die Seriennummer MSN 11.230. Es ist also der 11.230. Jet der Familie, der gebaut wird.
Später wird er für die Lufthansa fliegen. Die Mitarbeiter der Ausrüstungsmontage füllen in diesen und den nächsten Tagen das einst nackte Aluminium-Skelett mit technischem Leben: Isolierungen, Fenster, Klima- und Hydraulikrohre, elektrische Leitungen, Abwasser- und Wassersysteme werden nach und nach eingebaut. Nach zehn Tagen kommt die ausgerüstete „Tonne“ in die Endmontage.
Airbus: A321XLR hob im Juni ab
Auf der anderen Seite der Halle wurde monatelang am Hoffnungsträger des Konzerns gearbeitet. Dort begann der Zusammenbau der ersten drei Versionen des neuen A321XLR. Die 44,50 Meter lange Maschine erhielt einen Zusatztank im Frachtraum und kann dadurch sogar auf der Langstrecke eingesetzt werden. Im Juni hob der Flieger erstmals ab. Mehr als 500 Bestellungen für ihn liegen bereits vor. Die ersten Schritte des Zusammenbaus werden auch künftig in Halle 260 erfolgen.
Die Corona-Krise hat der Flugzeugbauer längst abgehakt. Im Frühjahr 2020 bangte er noch um die eigene Existenz und fuhr die Fertigungsrate der A320-Familie um ein Drittel auf 40 Maschinen pro Monat herunter. Mehr als 2200 Stellen sollten in Hamburg gestrichen werden. Ein Jahr später verließen rund 1000 Beschäftigte das Unternehmen und nahmen Abfindungen oder den angebotenen vorgezogenen Ruhestand an.
Airbus sucht händeringend Personal
Doch die befürchtete Stornierungswelle aufgrund der global lahmgelegten Luftfahrt blieb aus. Stattdessen erholt sie sich wieder – und Airbus braucht nun massiv Personal, um den geplanten Hochlauf zu schaffen. „Wir suchen im Moment händeringend Mitarbeiter“, sagt Walter wenig später im Gespräch mit Journalisten in einem Konferenzraum. Allein in diesem Jahr seien im Flugzeugbereich in Deutschland 700 Mitarbeiter fest eingestellt worden sowie 1400 Leiharbeitskräfte an Bord gekommen. Der Grund: Bis zum Jahr 2025 soll die Fertigungsrate bei der A320-Familie wieder auf 75 Maschinen pro Monat hochgefahren werden – so viele wie nie. Derzeit sind es rund 52 Jets.
Traditionell werden etwa die Hälfte der Maschinen in einer der vier Endmontagelinien auf Finkenwerder gefertigt, der Rest in Toulouse (zwei Endlinien) sowie in Tianjin/China und Mobile/USA (je eine). Aber auch für die dortigen Fertigungen kommen wichtige Teile wie ausgerüstete Rumpfabschnitte aus Hamburg, die Bausätze für die außereuropäischen Standorte werden am Betriebshafen verschifft. Es wartet also viel Arbeit im Werk an der Elbe, das personell weiterwachsen soll. „Für Hamburg suchen wir bis Mitte nächsten Jahres noch mal in etwa 800 bis 1000 Leute“, sagt Walter. Derzeit sind es rund 15.000 Beschäftigte, die sich neuerdings aber auf zwei Firmen aufspalten.
Arndt Stephan nun Werksleiter in Hamburg
Seit dem 1. Juli gibt es neben der alteingesessenen Airbus Operations GmbH die Airbus Aerostructures GmbH, kurz ASA. Neben den Mitarbeitern der Ausrüstungsmontage in Halle 260 wechselten auch die Beschäftigten der vorgelagerten Strukturmontage in die neue 100-prozentige Airbus-Tochter. Die IG Metall hatte in einem langen Arbeitskampf, begleitet von massiven Warnstreiks, erreicht, dass die betroffenen 4300 Beschäftigten auf Finkenwerder beim Wechsel ihre erworbenen Ansprüche behalten. Geändert habe sich für sie nur die Aufschrift der Firma auf dem Hausausweis, einen Riss durch das Werk gebe es nicht, sagt Walter.
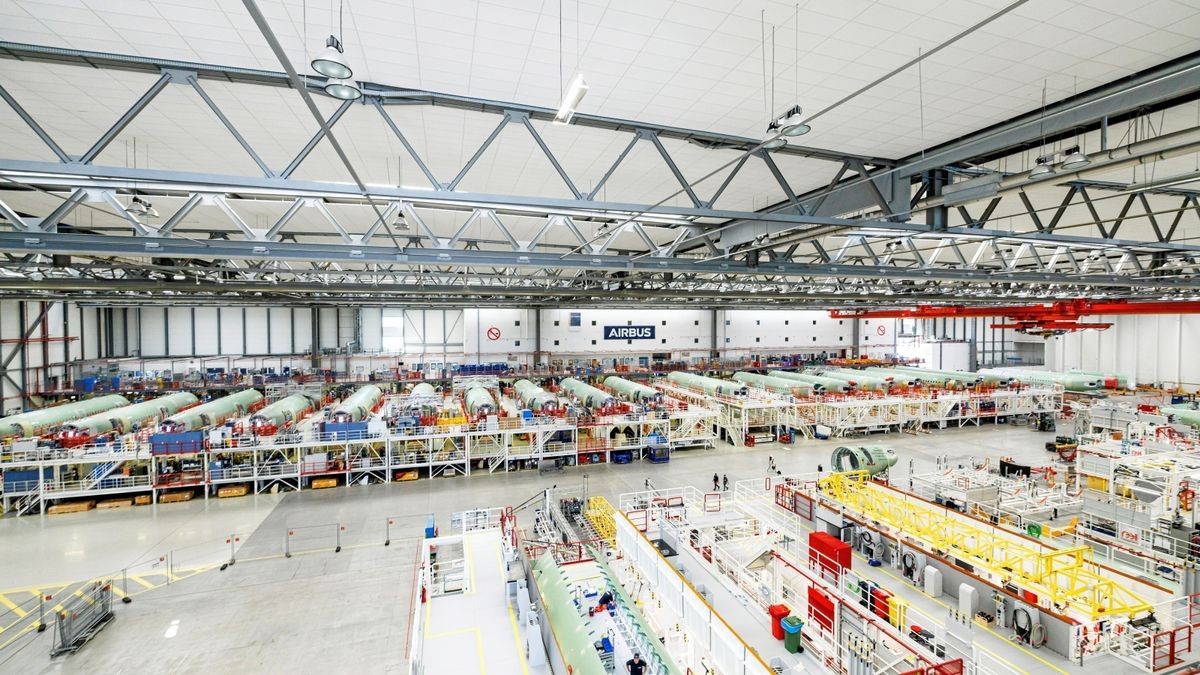
Der 55-Jährige übernahm allerdings eine neue Aufgabe. Den Job als Hamburger Werksleiter gab er an Arndt Stephan ab. Und nach drei Jahren als Vorsitzender der Geschäftsführung von Airbus Operations übt er dieselbe Position nun bei der ASA mit Sitz in Hamburg aus. Neben den 4300 Beschäftigten auf Finkenwerder zählen dazu die Standorte Nordenham, Stade, Buxtehude sowie Teile von Bremen. Insgesamt sind es derzeit rund 8400 Mitarbeiter. Bis 2025 sollen noch Beschäftigte aus Augsburg und Varel von der Tochter Premium Aerotec (PAG) zur ASA hinzustoßen, sodass sie dann mehr als 10.000 Mitarbeiter beschäftigt.
Airbus will "grünes" Flugzeug in die Luft bringen
Mit dem Start des neuen Unternehmens, das sich um die Fertigung von Flugzeugschalen und dem Zusammenbau zu Rümpfen kümmert, ist Walter zufrieden. „Wir haben beim technischen Umstellen keine großen Probleme gehabt.“ So mussten allein 60 IT-Tools umgestaltet werden. Doch die Fertigung sei stets im gewohnten Umfang gewährleistet worden. Das System liefe stabiler als früher, Störungen würden früher erkannt, man lerne viel voneinander und könne Flieger schneller mal vorziehen oder zurückstellen.
Der Konzernumbau sei sinnvoll und notwendig gewesen, sagt Walter und verweist auf das „grüne“ Flugzeug, das vor knapp zwei Jahren angekündigt wurde. Airbus möchte in 13 Jahren eine mit Wasserstoff angetriebene Maschine in die Luft bringen. „Wir sind davon überzeugt, dass wir bis 2035 den CO2-neutralen Flieger hinbekommen“, sagt Walter. Dafür wurden drei Konzepte vorgestellt, die derzeit unter die Lupe genommen werden. Mit Propellern, mit einem Turbofan wie heutige Jets oder den futuristisch anmutenden Nurflügler, der wie ein B2-Kampfbomber aussieht und gleich acht kleinere Motoren haben könnte.
Airbus muss sich für Konzept entscheiden
Das Problem: Wasserstoff ist sehr voluminös. Das erfordert Veränderungen an der Flugzeugarchitektur – ein wichtiger Grund, warum Airbus die Rumpfstruktur wieder als Kernkompetenz ansieht, die Fertigung von Rumpfschalen von der Tochter PAG zurück in den Konzern holte und zusammen mit der Struktur- und Ausrüstungsmontage in eine neue Firma packte. Spätestens bis Anfang 2026 müsse man sich entscheiden, auf welches der drei Konzepte man setzen wolle, sagt Walter. Dann müsse man parallel dazu die Produktion aufbauen. Der Wasserstoff könne entweder direkt verbrannt werden oder in einer Brennstoffzelle.
Daran wird seit Jahren intensiv in Hamburg geforscht. In der künftigen firmenmäßig geteilten Airbus-Arbeitswelt wird die Operations GmbH im Engineeringbereich für die Entwicklung der Technologie Brennstoffzelle zuständig sein, sagt Walter. „Wie bau ich eine Brennstoffzelle und wie bau ich sie nachher ein, das machen wir“, sagt der neue ASA-Chef: „Wir sind immer die Industrialisierung der Idee.“ Die Arbeiten erfolgten stets in enger Abstimmung untereinander.
Viel Geld für Produktionssysteme eingeplant
Bis 2025 soll viel Geld für Produktionssysteme und Hardware locker gemacht werden. „In Summe wird im Bereich Aerostructures 1,2 Milliarden Euro investiert werden“, sagt Walter. Zum einen müssten Basistechnologien wie Dichtungen und Oberflächenschutz verbessert werden, um möglichst leichte und widerstandsfähige Flugzeuge hoher Qualität zu bauen. Zum anderen stellt die Wasserstofftechnologie und die Integration des Tanks in den Rumpf eine besondere Herausforderung dar.
- Warum Berlin Hamburg derzeit bei Langstreckenflügen abhängt
- Kleinere Aufträge für Airbus auf Messe bei London
- Airbus gegen Boeing: Wer gerade die Nase vorn hat
Dabei kooperiere man mit den Bremer Kollegen, die in der Raumfahrt viel Erfahrung sammelten, so Weber: „Es ist aber etwas anderes, einen Tank zu bauen, der nur einmal fliegen muss, als einen Tank zu bauen, der kurz am Boden steht, schnell betankt wird und weiterfliegt. Das ist eine ganz andere Technologie.“
Airbus: Beim A321XLR ist der Tank fest eingebaut
Aber auch in Hamburg wurden bereits wichtige Erkenntnisse gewonnen. Beim A321XLR wurde der Tank fest im Frachtraum eingebaut. „Das ist schon mal eine gute Übung, einen Tank im Rumpf zu installieren“, sagt Walter. „Das hört sich sehr simpel an, ist vom Toleranzmanagement aber eine sehr große Herausforderung von Design und Produktion.“ Der Einbau geschah in Halle 260.