Siek. Betonbelag wird zwischen Stapelfeld und Bargteheide auf sechs Kilometern erneuert. Im Dezember soll die neue Fahrbahn fertig sein.
Mehr als eine ganze Wand füllen die Pläne und Skizzen im provisorischen Containerbüro von Marc Neumann an der Autobahnraststätte Buddikate bei Todendorf. Erst beim genaueren Hinsehen lässt sich erkennen, dass es sich bei den eingezeichneten Linien und Flächen um eine Autobahn handelt. „Von der Dicke der verschiedenen Betonschichten bis zur Position der Fugen – ich habe immer vor Augen, wie die Fahrbahn nach der Fertigstellung aussehen soll“, sagt Neumann. Das ist der Job des 35-Jährigen: Als Bauingenieur in der örtlichen Bauüberwachung sorgt Marc Neumann von der Autobahn GmbH des Bundes dafür, dass auf Stormarns größter Baustelle alles rund läuft.
Es türmen sich meterhohe Berge von rotem Kies
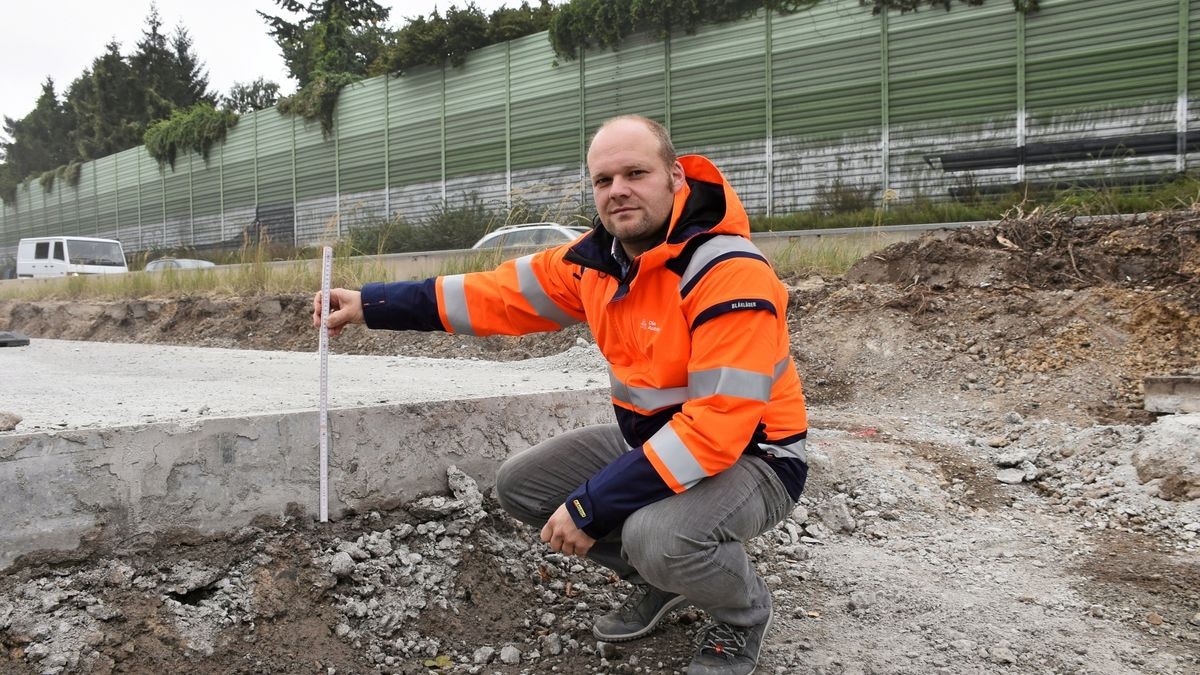
Seit dem 29. Juli saniert die Firma Strabag im Auftrag der bundeseigenen Gesellschaft, die mit dem 2. Januar dieses Jahres die Zuständigkeit für die Instandhaltung der Fernstraßen von den Verkehrsbetrieben der Länder übernommen hat, die Fahrbahn der Autobahn 1 in Richtung Lübeck zwischen Stapelfeld und dem Kreuz Bargteheide. Fünf Monate wird es dauern, bis der Fahrbahnbelag auf dem sechs Kilometer langen Streckenabschnitt erneuert ist. 16,5 Millionen Euro investiert die Bundesregierung, im Dezember soll die Fahrbahn wieder freigegeben werden.
Um stets den Überblick zu haben, ist Marc Neumann einen großen Teil des Tages auf der Baustelle unterwegs. „Ich bin gern draußen auf der Straße unterwegs, das gefällt mir an meiner Arbeit“, sagt der 35-Jährige. Er streift die orangefarbene Warnweste mit den Reflektorstreifen über seine Jacke, dann geht es mit dem Auto raus auf die Baustelle. Erster Stopp ist ein Feld an der Landesstraße 224 bei Siek. Bis vor wenigen Monaten war hier noch ein Acker, jetzt ist das Areal, das die Autobahn GmbH vorübergehend gepachtet hat, der zentrale Umschlagplatz für Baumaterial und Maschinen. Der Boden ist mit einer mehr als einen Meter dicken Schicht aus feinem Schotter bedeckt. Im hinteren Bereich türmen sich meterhohe Berge von rotem Kies. „Hier lagert nicht der Split für den neuen Fahrbahnbelag, wir stehen gerade auf den aufgebrochenen Überresten der alten Betondecke“, sagt Marc Neumann.
Betonkrebs zerstörte den alten Fahrbahnbelag

„Der alte Fahrbahnbelag hatte Betonkrebs“, sagt Neumann. Bei dem chemischen Prozess, der eigentlich Alkalikiessäure-Reaktion (AKR) heißt, bildet sich in den Poren des Betons Gallert. „Dadurch dehnt der Beton sich aus und platzt auf“, erklärt der 35-Jährige. Auslöser sei die Reaktion eines bestimmten Bestandteils von Betonmischungen, die früher im Straßenbau verwendet worden seien, mit dem ebenfalls enthaltenen Zement sowie mit Streusalz. Neumann: „Heute verwenden wir Mischungen, bei denen es das Problem nicht mehr gibt. Ende August haben wir begonnen, die alte Fahrbahn aufzufräsen.“
Sechs Tage dauerte es, die 92.000 Quadratmeter Betondecke abzutragen. „Das entspricht 13 Fußballfeldern“, erläutert Neumann. „Wir haben im Schichtbetrieb 24 Stunden gearbeitet, waren dafür fast vier Tage schneller fertig als geplant.“ 2400 Lkw-Ladungen Schutt wurden zum Lagerplatz bei Siek transportiert, dort mit Maschinen zerkleinert. „Die Reste werden weiter aufbereitet und anschließend bei anderen Bauprojekten wiederverwertet, beispielsweise als Füllmaterial“, so der Bauingenieur.
Derzeit wird auf dem Areal die Mischanlage für den neuen Fahrbahnbelag errichtet. 65.000 Tonnen Split verschiedener Gesteine werden hier in den kommenden Wochen mit Zement und Wasser zu Beton vermischt. Einer der Monteure ist Uwe Peters. „Höhenangst sollte man in dem Job nicht haben“, sagt er. Peters steht auf der etwa ein mal zwei Meter großen Gitterplattform seines Hubsteigers. 27 Meter trennen ihn vom Boden. Höhe und Position der Plattform steuert Uwe Peters mit einem Joystick von oben aus. „Vier Silos werden zuerst mit einem Kran aufgerichtet und dann montiert“, erklärt er. Für Marc Neumann geht es jetzt weiter auf die Autobahn. Er steckt einen Stecker in den Zigarettenanzünder seines Wagens. „Bevor ich auf die Baustelle fahre, muss ich die Warnlampe auf dem Dach einschalten, damit das Auto als Baustellenfahrzeug erkennbar ist“, erklärt er.
Fahrbahn besteht aus drei verschiedenen Schichten
Eine feine, weiß-gräuliche Pulverschicht bedeckt den Boden dort, wo früher einmal die Fahrbahn war. „Zement“, sagt Neumann. „35 Kilogramm pro Quadratmeter.“ Das Pulver werde mit einem speziellen Streufahrzeug gleichmäßig aufgebracht. Neumann sagt: „Derzeit erneuern wir die Verfestigung.
So heißt die Schicht, die zur Stabilisierung unter der eigentlichen Betonfahrbahn liegt.“ Sie setze sich aus grobem Kies, Sand und Zement zusammen. „Wir verwerten die alte Verfestigung wieder, bereiten sie auf“, sagt Neumann. „Der Belag einer Autobahn besteht eigentlich aus drei verschiedenen Schichten“, erklärt der Bauingenieur. „Auf die Verfestigung kommt der Unterbeton, dann der etwas anders zusammengesetzte Oberbeton, der die eigentliche Fahrbahnoberfläche ist.“ Das richtige Mischverhältnis des Betons sei entscheidend, damit die Eigenschaften am Ende stimmten. „Bis der Beton aufgetragen wird, dauert es noch“, sagt Neumann. „Zunächst muss das Zementpulver mit dem Sand und Kies der alten Verfestigung vermischt werden.“
16 Tonnen schwere Walze presst den Untergrund fest
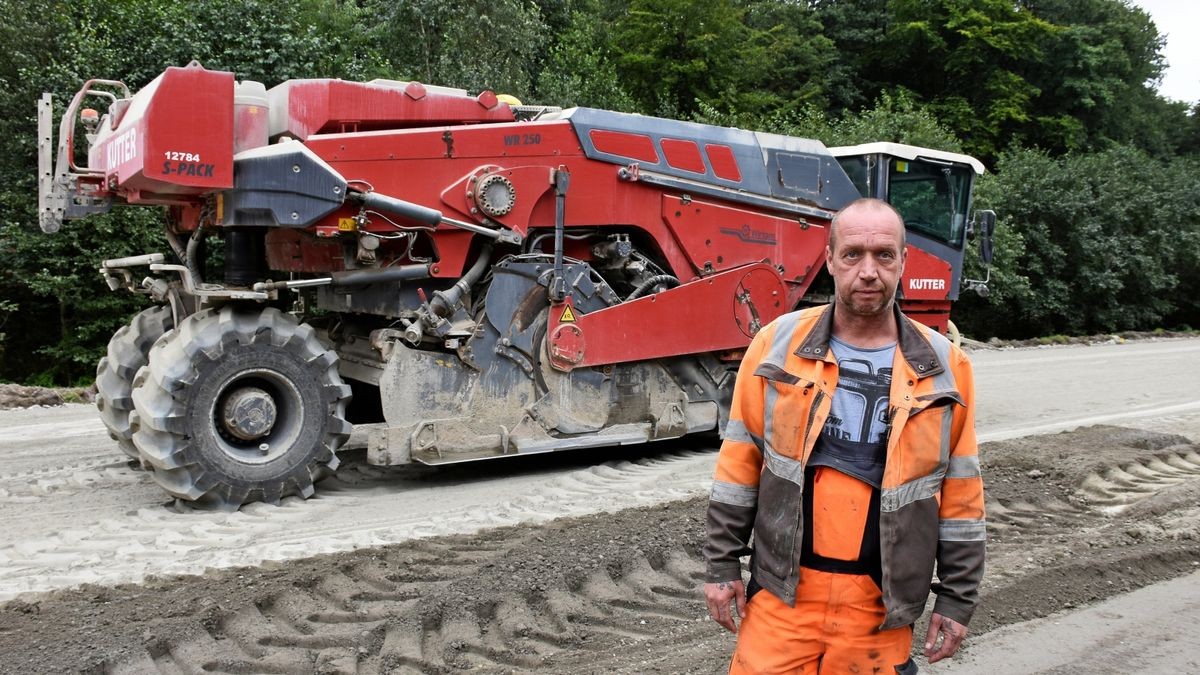
Das ist die Aufgabe von Frank Milz. Mit einer Fräse fährt er über den Untergrund. „Sie dringt 25 Zentimeter in den Boden ein“, sagt Milz. Zum Reagieren benötige der Zement Feuchtigkeit. „Ich schiebe mit der Fräse einen Tanklaster vor mir her, aus dem sich die Maschine das Wasser zieht und es über Düsen in den Fräsvorgang einspritzt“, erklärt Frank Milz. Zehn Tage benötige es, bis die gesamte Strecke umgefräst sei.
Einige Hundert Meter weiter ist Marco Eckert-Göpfert mit der Installation eines Messgerätes beschäftigt. Hier ist die Verfestigung bereits fertig umgefräst, erkennbar an einer dunkelgrauen Färbung. Bevor sie aushärtet, muss sie begradigt werden. Dazu kommt ein sogenannter „Grader“ zum Einsatz, ein Fahrzeug, das einem Schneeschieber ähnelt. „Die Messstationen dienen als Fixpunkte und übermitteln Daten an den Grader“, erklärt Eckert-Göpfert. „Das funktioniert wie ein Navigationsgerät. GPS kann Höhenunterschiede nicht so exakt darstellen, wie wir es benötigen.“
Der Grader werde mit einem Plan der fertigen Fahrbahnoberfläche bespielt, die Schaufel stelle sich anhand der Daten der Messstationen automatisch ein. „Die Technik spart nicht nur Arbeit, sondern macht sie auch genauer“, so Eckert-Göpfert. Eine 16 Tonnen schwere Walze presst den Untergrund im Anschluss fest.
Sollbruchstellen werden in den Betonbelag geschnitten
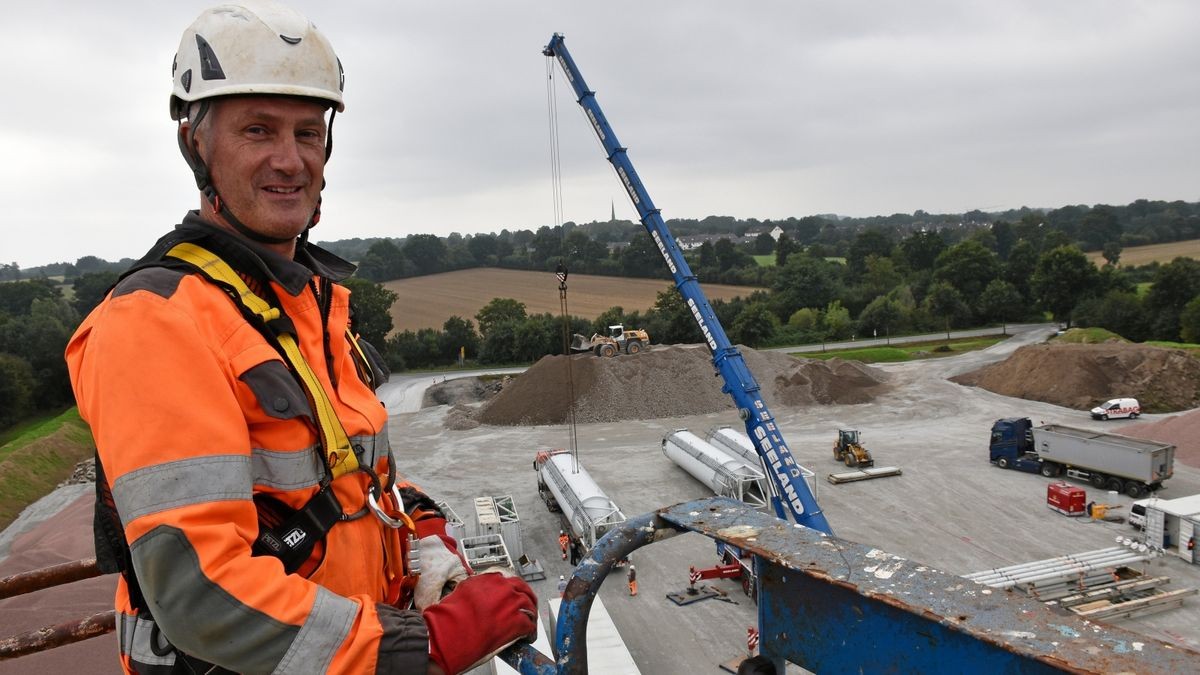
„Erst jetzt kommt die eigentliche Fahrbahn“, sagt Bauingenieur Marc Neumann. Mit einem Betongleitschalungsfertiger werde das flüssige Gemisch aufgebracht. „Danach wird die Schicht alle drei Meter längs und alle fünf Meter quer zum Fahrbahnverlauf eingeschnitten.“ Es handele sich um Sollbruchstellen, die verhindern sollten, dass der Beton willkürlich aufbricht. „Mehrere Zentimeter dicke Eisendübel werden in die Fugen eingedrückt, damit sich die einzelnen Betonplatten nicht verschieben.“
Wenn das Wetter günstig sei, dauere es sieben Tage, bis der Belag fertig sei. Neumann: „Beim Aushärten muss es möglichst trocken sein.“ Dann werde die Oberfläche mit speziellen Fahrzeugen ausgebürstet. „Erst dadurch entsteht die Waschbetonoberfläche mit ihrer typischen Struktur.“ Sie gebe Reifen besseren Halt und mindere den Lärm.
Zurück im Baubüro an der Raststätte Buddikate blickt der 35-Jährige auf die Planskizzen an der Wand hinter seinem Schreibtisch. „Wir liegen gut im Zeitplan“, sagt er zufrieden.