Hamburg. Kühlende T-Shirts, elektrische Handschuhe und eine Fehlersuche per App sind auf Finkenwerder geplant. Erste Einblicke.
„Das T-Shirt ist ja ein cooles Teil“, könnte bei einem der größten Arbeitgeber der Stadt bald zum Standardspruch gehören – auch wenn die Textilien vom äußeren Erscheinungsbild eher gewöhnlich sind. In Weiß steht „Airbus“ auf dem dunkelblauen Shirt, das in der Produktion des Flugzeugbauers auf Finkenwerder getragen wird. Das Besondere: Die Oberbekleidung hat ein Innenleben. Weil es bei der Arbeit im Rumpf der Jets oftmals heiß zugeht, steckt in dem Shirt eine Art private Klimaanlage, bestehend aus einem gartenschlauchähnlichen System. Angeschlossen ist es an die Druckluftversorgung, die die Beschäftigten zum Betrieb ihrer Werkzeuge ohnehin mit sich führen. „Der Mitarbeiter wird permanent mit einem Luftfilm umströmt“, sagt Airbus-Produktionstechniker Robert Goehlich.
Der promovierte Ingenieur für Luft- und Raumfahrttechnik ist beim MDAX-Konzern Projektmanager für Exoskelette. Das sind am Körper getragene Systeme, die Menschen bei ihren Tätigkeiten unterstützen. So können Beschäftigte Kräfte sparen sowie Arbeiten länger und schonender erledigen. Vor drei Jahren wurde in Hamburg mit der Erforschung der Hilfsmittel begonnen. Das Anwendungsgebiet Gesundheit ist ein wichtiger Schritt hin in Richtung Industrie 4.0.
Vierte industrielle Revolution
Darunter wird die vierte industrielle Revolution verstanden, in der reale und virtuelle Welt durch das Internet immer stärker zusammenwachsen. Das Schlagwort mit Leben zu füllen, bemüht sich Airbus zurzeit im Werk auf Finkenwerder. „Wir entwickeln gerade die ,Fabrik der Zukunft‘“, sagt Eckart Frankenberger. Er ist als Chief Industrial Architect für das ganzheitliche Konzept zuständig. „Das Kennzeichen einer modernen Fabrik ist, dass wir mit den Daten und Informationen aus dem Produktionsprozess arbeiten – in Echtzeit und zum Nutzen aller Beteiligten.“
Wenn heute eine Schraube montiert werden muss, steht in der Arbeitsanweisung mit welchem Werkzeug und Drehmoment das zu erfolgen hat – noch auf Papier. Künftig könnte es elektronisch übermittelt werden. Mit den heute bereits verfügbaren Daten könne man viel erreichen, wenn man sie automatisiert in Zusammenhang setzt, sagt Frankenberger.
Bei Problemen wird zum Tablet gegriffen
Wie die Arbeit in Zukunft häufiger aussehen könnte, zeigt die Mixed Reality (MiRa)-Anwendung, die in der Fertigung des A350 eingesetzt wird. In den neuen Großraumjet müssen in verschiedenen Ausführungen Tausende Halter eingebaut werden, an denen Kabel und Leitungen befestigt werden sollen. Immer wieder kommt es zu Unterbrechungen der Produktion an einzelnen Stellen, weil zum Beispiel ein Halter vergessen wurde oder weggebrochen ist.
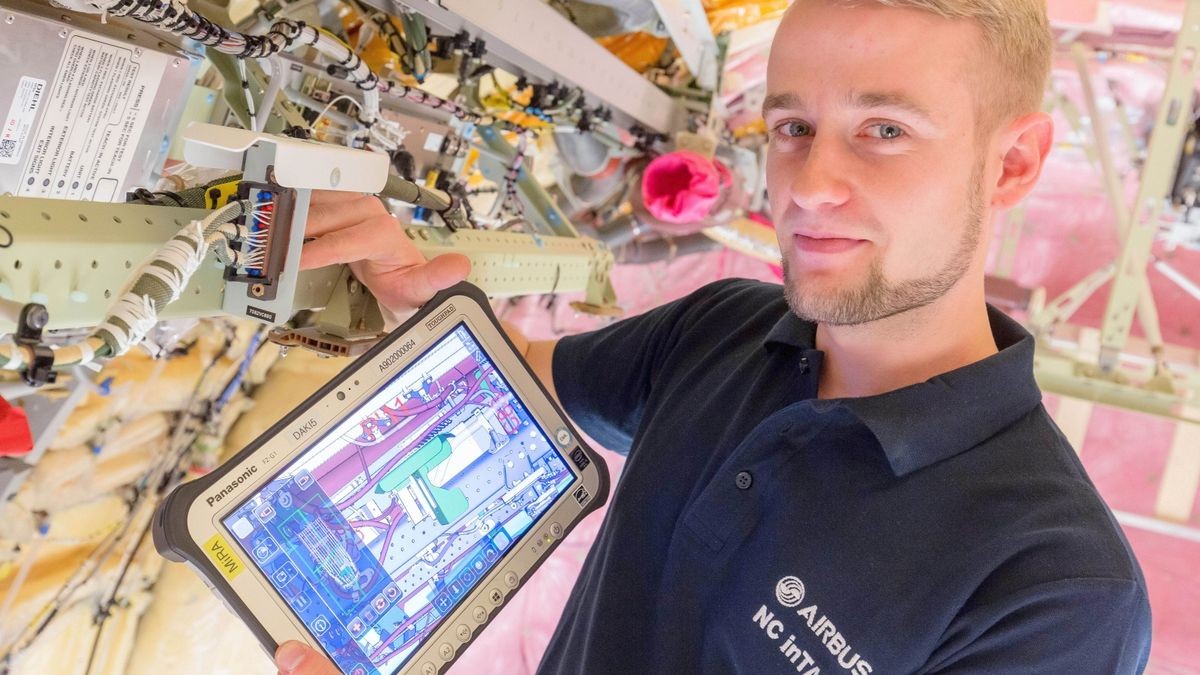
Im September 2016 startete ein Pilotprojekt, das mittlerweile standardmäßig angewendet wird. Seitdem greifen Mitarbeiter zum Tablet, wenn ein Problem auftaucht. Sie machen ein Foto, erfassen den Fehler und laden ihn per App direkt ins System hoch. Die Logistik wird automatisch angewiesen, das Produktionsteil zu liefern. „Wir können in Echtzeit reagieren“, sagt Stefan Lechel, der in Hamburg für das MiRa-Projekt zuständig ist. „Wir sparen pro Defekt im Durchschnitt circa 15 Minuten.“
Die Gründe dafür sind vielfältig: Weil früher alles handschriftlich auf Papier erfasst wurde, kam es wegen schwer zu lesender Handschrift zu Verwechslungen oder Nachfragen. Der Zettel konnte länger unbeachtet in der Logistik liegen. Es dauerte, bis ein Prüfer die Freigabe für einen Teileaustausch gab. Der Ort des Fehlers war mangelhaft beschrieben, MiRa erfasst ihn hingegen automatisch – langes Suchen ausgeschlossen.
Weitere moderne Technologie
Dass die MiRa-Anwendung bei dem modernsten Jet von Airbus eingesetzt wird, ist kein Zufall. „Der A350 ist in 3D konstruiert. Da können wir leichter eine Durchgängigkeit der Daten herstellen vom 3-D-Modell der Konstruktion hin zu Mixed Reality in der Produktion“, sagt Frankenberger. Die erfolgreiche A320-Familie (intern Single Aisle genannt) wurde hingegen bereits in den 1980er-Jahren zweidimensional auf Papier konstruiert. Da ist noch viel Datenaufbereitung notwendig – aber auch hohes Potenzial für Verbesserungen in der Produktion gegeben. „Single Aisle ist daher ein Startpunkt für viele Ideen“, sagt der für Innovationen zuständige Fertigungstechnologe Ingo Krohne.
Im Werk auf Finkenwerder soll bald weitere moderne Technologie einziehen. Zu den aufwendigen Arbeiten gehört der Einbau der Türen. Eine Schicht ist damit beschäftigt, die Türen einzustellen, eine Schicht lang dauert anschließend die Kontrolle. 300 Stellen müssen dabei mit dem Schieber nachgemessen werden. Mit Partnern werde nun daran geforscht, den Einbau von Kameras überwachen zu lassen. Sensoren überprüfen die Arbeiten permanent.
Check per 3-D-Scan
Das Ziel: Mit dem Abschluss des Einbaus ist auch der Check per 3-D-Scan abgeschlossen, Montage und die in der Luftfahrt aus Sicherheitsgründen sehr umfangreiche und zeitaufwendige Dokumentation erfolgen zugleich. „Wir streben an, die erforderliche Arbeitszeit für Einbau und Dokumentation mindestens zu halbieren – mit einem optimal spannungsfreien Einbau“, sagt Frankenberger. In sechs bis neun Monaten könnte das System einsatzbereit sein.
Airbus erhofft sich, dass mit dem Einzug von Industrie 4.0 insgesamt die Transparenz gesteigert wird. Bricht beispielsweise ein Teil ab, könnte automatisch sofort ein Ersatzstück geordert werden. Verzögerungen in der Produktion könnten so reduziert werden, wenn möglich andere Arbeiten vorgezogen werden. Ein Grundproblem gibt es aber für die Branche noch: die komplexe Produktion. Während ein Flugzeug aus mehreren Millionen Teilen mit einem geringen Anteil an Vormontagen besteht, seien es bei einem Auto nur 10.000 bis 16.000 Komponenten, die zu einigen Hundert Modulen vormontiert wurden.
Neues Produktionszeitalter
Das ermögliche den Zusammenbau der Kraftfahrzeuge durch Roboter, sagt Frankenberger: „Zudem wird der Flieger noch bis relativ spät im Prozess den Wünschen des Kunden angepasst, und viele Montageschritte sind noch Handarbeit. Das macht den Schritt zu Industrie 4.0 schwieriger, aber umso erforderlicher. Momentan stehen wir noch am Anfang dieses Prozesses, mit ersten sehr vielversprechenden Anwendungen.“ Wichtig sei es, die Entwicklung nah am Nutzer voranzutreiben.
Die Mitarbeiter auf die Reise in das neue Produktionszeitalter mitnehmen soll Jan Balcke. Er leitet in Hamburg die Ausbildung und das Projekt Human Ressources 4.0. „Es wird sicherlich eine Verdrängung von sehr einfachen, sich wiederholenden Tätigkeiten geben“, sagt Balcke. Das Zusammenspiel von Mensch und Roboter werde eine immer wichtigere Rolle einnehmen. Einen deutlich geringeren Bedarf an Arbeitsplätzen erwartet Balcke aus heutiger Sicht nicht: „Der Flugzeugbau wird auch zukünftig von manueller Arbeit geprägt sein.“ Einige Jobprofile fielen zwar sicherlich weg, generell sei Industrie 4.0 eher Chance denn Bedrohung. Seine Aufgabe besteht darin, die Mitarbeiter für das Thema zu sensibilisieren, zu qualifizieren und den Arbeitsplatz an moderne Möglichkeiten anzupassen.
Maximallasten wegnehmen
Für solche Entwicklungen ist Krohne zuständig. Der promovierte Maschinenbauingenieur hat sich einen Handschuh übergestreift, in dem Sensoren eingenäht sind. Wenn er Daumen, Mittel- und Ringfinger bewegt, hört man ein leichtes Surren. Der Handschuh unterstützt die Bewegung der Finger und gibt bei einer Zangenbewegung zusätzliche Kraft, indem ein künstliches Sehnensystem aktiviert wird. Die Energie dafür stammt aus einer kleinen Batterie, die der Mitarbeiter am Gürtel trägt. Eingesetzt wird das Hilfsmittel in der Produktion. Dort müssen beim Zusammenbau der Rumpfsektionen mehrere 100 Klemmhefter gesetzt werden. Eine kraftraubende Handarbeit. Krohne über die Neuentwicklung: „Ein Mitarbeiter sagte: ,Das hätte ich schon vor 25 Jahren haben sollen.‘“
Ein Zusatzgewicht von rund vier Kilogramm hat sich unterdessen Goehlich auf den Rücken gepackt: Es ist ein Exoskelett mit Armunterstützung. Eingesetzt wird es in der Strukturmontage der A320-Familie und des A350. Beim Nieten im Rumpf müssen die Monteure stundenlang über Kopf arbeiten oder das fünf bis acht Kilogramm schwere Werkzeug vor der Brust halten. Da wird der Arm schon mal schwer, und der Nacken verspannt. Mit dem Exoskelett wird ein Teil der Belastung aus dem Arm genommen und in Rückenpartien geleitet, in denen man mehr Kraft hat. „Die Maximallasten sollen weggenommen werden“, sagt Goehlich. Fehlhaltungen können dadurch allerdings nicht behoben werden, sondern nur Unterstützung gewährt werden.
Mit Exoskelett lässt sich viel Kraft sparen
Wer sich das Hilfsmittel selbst einmal umschnallt und ein Gewicht hochhebt, merkt wie der Arm ab einer gewissen Höhe nach oben gedrückt wird. Für den Effekt sorgt eine Blattfeder. Zwar wirkt das System zunächst unhandlich und die Arbeiter sahen noch Verbesserungspotenzial bei der Bewegungsfreiheit im Schulterbereich, aber grundsätzlich sei das Feedback aus der Produktion, in der die Prototypen getestet werden, positiv. Goehlich überrascht das nicht, denn er hat ausgerechnet: „Das Exoskelett hilft, rund ein Drittel Kraft zu sparen.“
Nicht auf weniger Kraft, sondern auf weniger Schweiß ist das kühlende T-Shirt ausgelegt. Dank dreier Kreisläufe können Brust, Rücken und Achseln separat belüftet werden, manuell oder automatisch. Das T-Shirt ist in etwa so schwer wie ein Sweat-Shirt. Jeder Mensch kann die gewünschte Temperatur eingeben, das System hält sie konstant. Goehlich: „Bei den Mitarbeitern ist die Innovation sehr gut angekommen. Es soll demnächst ein Vorserienprototyp gefertigt werden.“