Fellinghausen. Siegerländer Kuppelofen aus der Zeit der Kelten hat den Verkohlungsprozess überstanden und ist bereit für den ersten Verhüttungsversuch.
Wenige Meter vom Meilerplatz entfernt und mitten im historischen Hauberg steht er: der erste originalgetreue Nachbau eines Siegerländer Kuppelofens. Gut geschützt unter einem Dach ist er in den Hang gebaut. Der Ofen ist stattlich: rund zwei Meter hoch und 170 cm breit. Er ist der ganze Stolz von Rentner Heinz Katz vom Förderverein Historischer Hauberg Fellinghausen. 700 Arbeitsstunden und rund acht Tonnen Material haben Heinz Katz und sein fünfköpfiges Team in den Bau investiert. Der La-Tène-Ofen hat den Verkohlungsprozess überstanden und ist nun bereit für den ersten Verhüttungsversuch. Am Freitag geht es los.
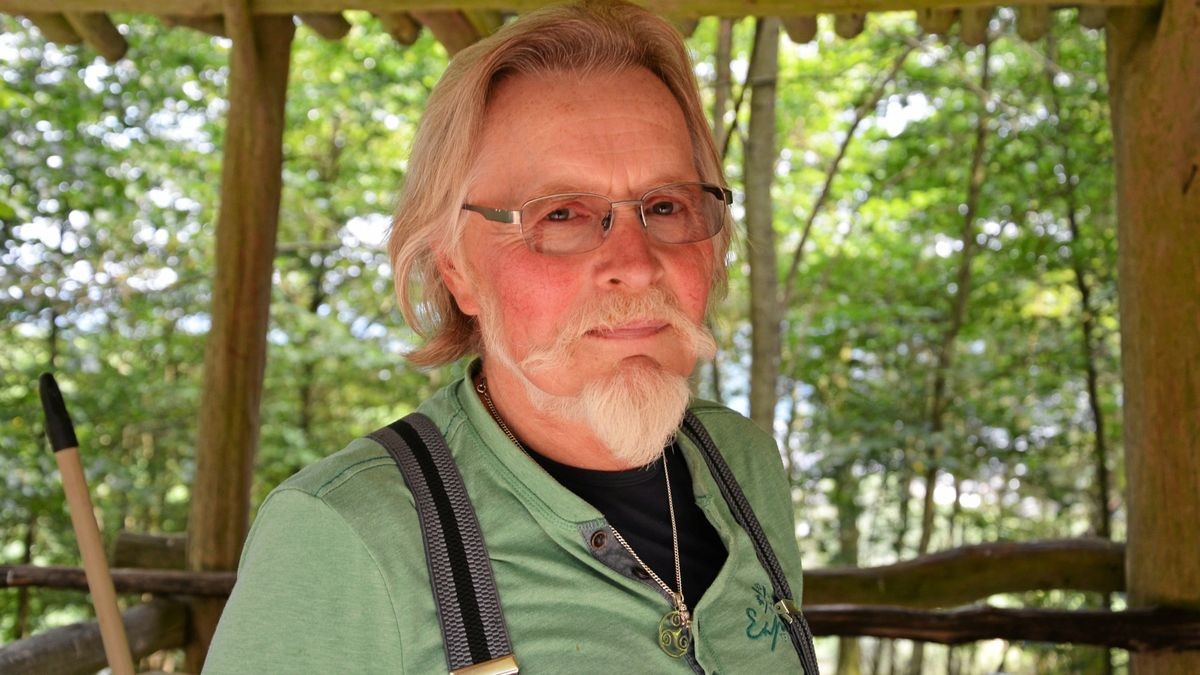
Das Ziel
Die Männer wollen schmiedbares Eisen herstellen. Das, so Heinz Katz, ist bisher noch niemandem gelungen. Die Mitglieder des Fördervereins um Heinz Katz und Manfred Flender haben sich auf dieses Experiment eingelassen. „Die Ergebnisse unseres Experiments sollen rund um die Welt gehen. Das ist mehr als ein Freizeit-Projekt“, sagt Heinz Katz. Deshalb sind auch Heinz Hadem, der bereits Erfahrung im Ofenbau hat, und Dr. Manuel Zeiler aus der Fachabteilung Archäologie des Landschaftsverbands Westfalen-Lippe (LWL) mit im Boot.
Sollte es gelingen, am Wochenende eine Luppe aus dem Eisenerz zu gewinnen, wird ein Teil davon im Bochumer Bergbaumuseum analysiert. Der Rest soll im Freudenberger Technikmuseum von einem erfahrenden Schmied gereinigt und ausgearbeitet werden. „Wir haben den Ofen so gebaut, dass wir mehrere Versuche starten können“, sagt Katz.
Der Bau
Im Sommer 2018 ging es los: Gebaut haben die Rentner den Ofen nach Ausgrabungsbefunden aus Niederschelden, Gerhardsseifen und Wartestraße. Die Originalöfen stammen aus der Zeit der Kelten, etwa um 500 vor Christus. Ein geflochtener Korb in Birnenform, der auf einem speziellen Fundament steht, bildet die Grundlage. Eine Masse aus Kaolin und Lehm gemischt mit Sand, kurzem Stroh und Wasser haben die Männer mit den Händen aufgetragen und festgedrückt. Danach eine Schicht aus selbst gemachten Ziegeln. Feldstein sowie Lehm dienen als Isolierung. Schicht um Schicht – jetzt ist die Wand 40 cm dick. „Zwischendurch sah der Ofen aus wie ein Döner“, erinnert sich Heinz Katz. Denn über Nacht musste das Konstrukt in der Bauphase gut in Frischhaltefolie verpackt werden. „Sonst hätte die nächste Schicht am Morgen nicht gehalten.“ Auch Düsen und einen Schürkanal bauen die Männer ein. Erde auffüllen, Dach drüber, trocknen lassen. Dann das Einbrennen im Februar. 1300 Grad hat der Ofen durch das Verbrennen von Holz erreicht – und bis auf kleine Risse gehalten.
Auch interessant
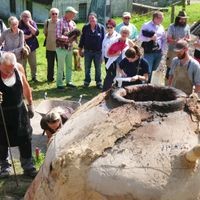
Täglich mehrere Stunden war die Gruppe vor Ort – am Wochenende gab es Unterstützung, unter der Woche waren sie zu sechst. „Es ist eine gute Gemeinschaft entstanden“, sagt Heinz Katz.
Die Vorbereitung
Momentan laufen die Vorbereitungen für den Verhüttungsversuch. Bevor es losgehen kann, muss das Holz geschnitten werden. Rund 5,5 Raummeter Holz halten die Verantwortlichen vor: Eiche aus dem heimischen Hauberg und zugekaufte Buche. Auch die anderen Materialien wie Moos und Eisenerz müssen am Wochenende bereitstehen. „Vielleicht werden wir den Ofen vorher auch schon ein wenig anfeuern“, erklärt Heinz Katz.
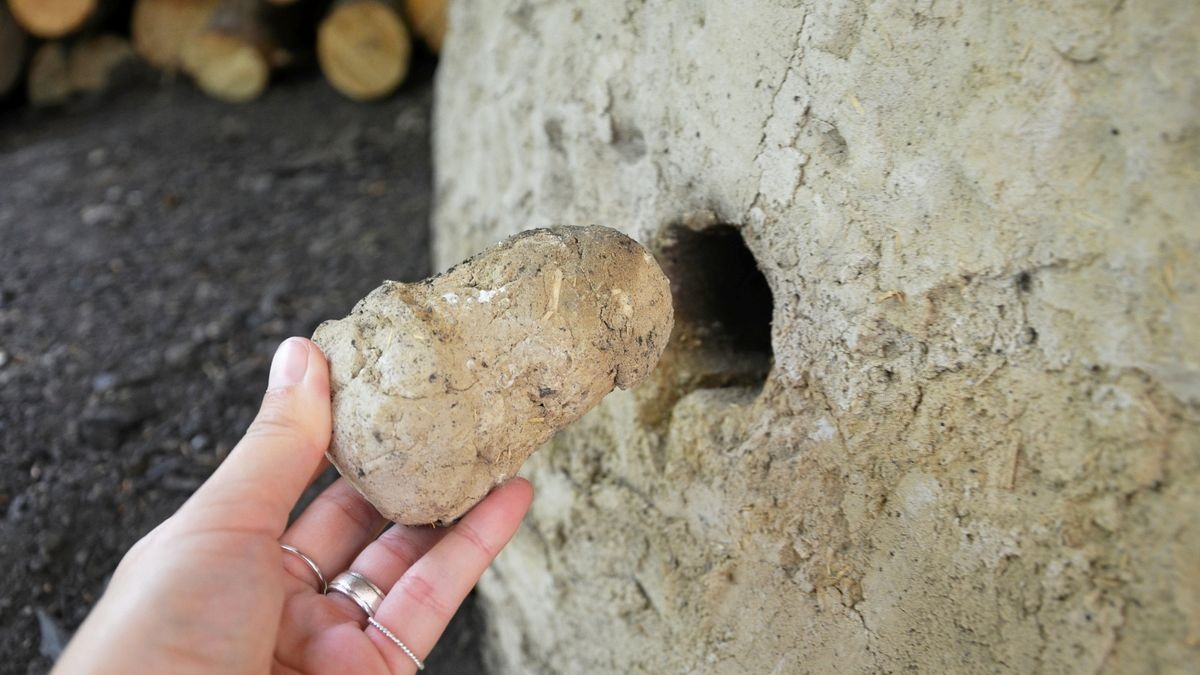
Der Verhüttungsversuch
Den ersten Verhüttungsversuch startet die Gruppe am kommenden Wochenende vom 26. bis 28. Juli. Er kann bis zu 24 Stunden dauern, weshalb sich die Verantwortlichen aufteilen und im Schichtsystem arbeiten. Der Ofen muss immer weiter angefeuert und überwacht werden. Auch müssen regelmäßig Messungen durchgeführt und die Daten notiert werden. Dabei geht es vor allem um die Innentemperatur und die Zusammensetzung der Gase im Inneren. „Wir wollen der Fachwelt später sagen können, wie genau alles entstanden ist“, erklärt Heinz Katz.
Geschmolzen wird Eisenerz aus dem Siegerland. Wie funktioniert das? Zunächst wird der Schürkanal mit selbstgebauten Düsensteinen verschlossen. Im Ofen wird Holz angefeuert und verkohlt – das können die Männer über die verschiedenen Düsen steuern. „Wir versuchen Kohle wie im Kohlemeiler zu bekommen“, sagt Heinz Katz. Wenn dann eine Glut entstanden ist, wird darauf Holz gelegt. Als Trägerschicht dient frisches Moos und darauf wird Heinz Katz dann mittig das Siegerländer Eisenerz platzieren. „Das muss dann reduzieren“, sagt der Rentner. Die obere Öffnung des Ofens soll dabei gedeckelt werden, um die Hitze im Inneren zu halten. Das Dach wird aus Sicherheitsgründen zur Seite geschoben.
Wenn genug Eisenerz reduziert und eine teigartige Luppe entstanden ist, wollen die Ofenbauer den Düsenstein entfernen und den Kanal ins Innere freimachen. Geplant ist, die Luppe loszustoßen und mit einer Schmiedezange rauszuziehen. „Bei der Entnahme kann die Luppe noch 900 Grad haben.“
Mehr Nachrichten, Fotos und Videos aus dem Siegerland gibt es hier.
Die Lokalredaktion Siegen ist auch bei Facebook.