Welschen Ennest. Maschinenbauer ODO-Engineering aus Welschen Ennest entwickelt Spezialsysteme für Riesenpressen und ist damit weltweit erfolgreich.
Ein weißer Bungalow mitten im Gewerbegebiet Am Heid in Welschen Ennest, dahinter eine Montagehalle von überschaubarer Größe. Kaum jemand ahnt, dass hier die Firma ODO-Engineering besondere Produkte entwickelt und konstruiert, ohne die in der Wüste bei Phoenix/Arizona, nahe der mexikanischen Grenze, riesige Pressen stillstehen würden. ODO, das sind Ingo Oberste-Dommes (57), sein Sohn Simon (30), beide Maschinenbau-Ingenieure, und ihr Team. ODO steht für eine in der Branche renommierte und bestens vernetzte Denkfabrik für Sondermaschinen. Und ODO baut das, was viele nicht können: Werkzeugwechselsysteme für riesige Pressen und Schwerlasttransportsysteme. Also da, wo es richtig schwerlastig wird, muss ODO ran.
Lesen Sie auch:
- Kreis Olpe: Unternehmer fordern Abbau der Bürokratie
- Ruhrverband stellt sich auf neues Hochwasser im Kreis Olpe ein
- Globuli-Diskussion: Patienten empört über Lauterbachs Haltung
Als gelernter Werkzeugmacher bekam der gebürtige Silberger schon früh Einblicke in die Welt der Pressen, arbeitete sich nach Fachabi und Ingenieurstudium in Siegen bei der Firma Gräbener Pressensysteme in Netphen schnell in leitende Positionen in Vertrieb und Konstruktion. Nach einigen Jahren als Betriebsleiter machte er sich 2007 selbstständig und baute erste Werkzeugwechselsysteme.
Die WESTFALENPOST im Kreis Olpe ist auch bei WhatsApp. Jetzt hier abonnieren.
Folgen Sie uns auch auf Facebook.
Bestellen Sie hier unseren Newsletter aus dem Kreis Olpe.
Alle News aufs Handy? Jetzt die neue WP-App testen.
Die WP im Kreis Olpe ist jetzt auch bei Instagram.
Die Initialzündung dafür kam in Brasilien als Projektleiter in einem Mercedes-Benz-Werk in der Nähe von Sao Paulo. Der Werkzeugwechselwagen eines Zulieferers funktionierte nicht. „Wir haben getrickst und umgebaut, bis es ging. Da habe ich mir gedacht, das kann man auch besser machen.“
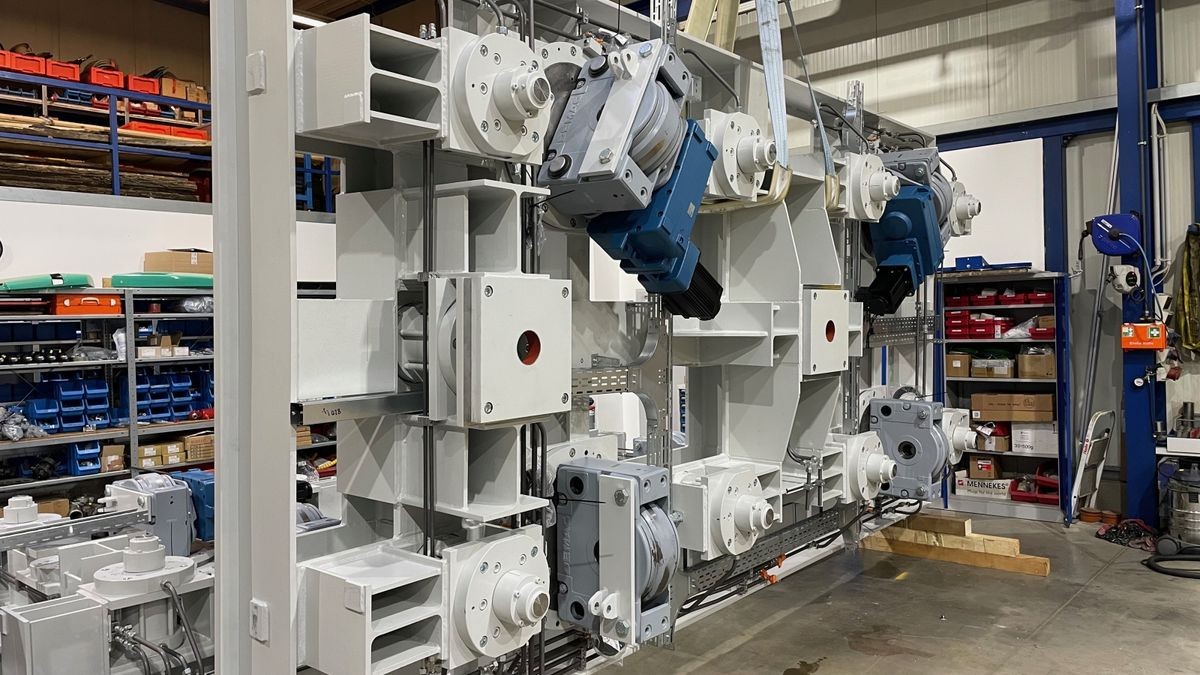
Damals gab es nicht viele Anbieter für diese Systeme. Die Werkzeuge, die dem Blech oder Kunststoff beim Pressvorgang die Form geben, wurden einfach mit dem Gabelstapler bewegt. „Das geht aber nicht mehr, wenn die Werkzeuge 30, 40 oder 50 Tonnen schwer sind“, so Ingo Oberste-Dommes. „Mittelgroße Pressen ohne eigene Schiebetische benötigen deshalb eine Werkzeugwechseleinrichtung, die die Werkzeuge möglichst schnell und sicher in die Pressen rein- und wieder raustransportieren. Wir liefern schienengebundene Wechselwagen oder integrierte Lösungen, aber auch klassische Konsolen mit integriertem Verschiebeantrieb.“ Heute hat ODO 32 Wechselwagen-Typen unter dem Namen ODO-Mat und ODO-Cart für verschiedene Umformungsverfahren im Portfolio. Kunden sind große Zulieferer für die Automobilindustrie wie ZF Schweinfurt, Schaeffler oder Tenneco. Das Know-how kommt aus dem eigenen Haus, die Konstruktionen sind Eigenentwicklungen. „Wir haben uns da reingefuchst, man wächst an seinen Aufgaben. Und ich habe viele Erfahrungen im Schwerlastbereich“, sagt der Chef.
Sonderanfertigungen bevorzugt
„Am liebsten bauen wir Systeme mit vielen Sonderanfertigungen“, sagt Ingo Oberste-Dommes. Der Auftrag aus Arizona war so eine besondere Herausforderung. Für einen US-Badausrüster wurde in dem Werk in Casa Grande eine Pressenlinie mit 16 Schuler-Riesenpressen gebaut, mit denen u. a. komplette Whirlpools gepresst werden können. Die acht Werkzeugwechselwagen für bis zu 80 Tonnen schwere große Kunststoffwerkzeuge stammen aus dem Hause ODO. „Das ist schon anspruchsvoll. Wir fangen mit einem weißen Blatt Papier an, ich habe am Anfang nur die Abmessungen, die Tonnage und die Umgebungsbedingungen, zum Beispiel 45 Grad Hitze in der Halle im Sommer und die Werkzeugtemperatur und wir müssen einen Wagen bauen, der ein 80-Tonnen-Werkzeug millimetergenau in die Presse bringt. So lautet die Anfrage“, so Oberste-Dommes. Herausgekommen ist ein komplexer Wechselwagen, der in alle Richtungen beweglich ist und über ein Belüftungssystem für das Fahrgestell verfügt. Unter anderem wurden Keramikplatten verbaut, die den Hitzefluss vom Werkzeug zum Wagen mindern. Schwenkbare Radsätze, eine besondere Zentriereinheit, eine mechanische Verriegelung und vieles mehr wurden eingebaut und das alles mit Batterieantrieb, Hydraulik, Steuerung und Sensortechnik gekoppelt. Die ersten sechs Wagen arbeiten bereits zuverlässig in Amerika, die restlichen beiden folgen in diesem Jahr, dann ist der Millionenauftrag abgehakt.
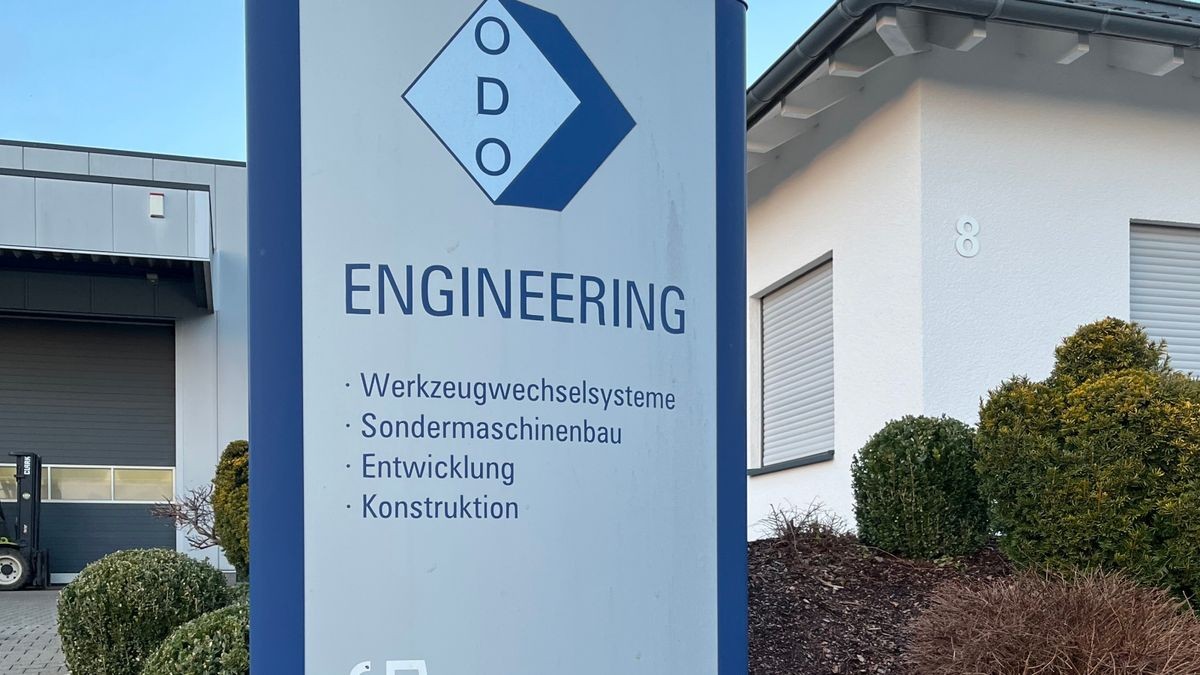
Ein weiteres Highlight in der jüngeren Firmengeschichte war der Bau eines vollautomatischen Hochregallagers in der Schweiz für 140 Presswerkzeuge von 2 bis 6 Metern Größe und 8 bis 35 Tonnen Gewicht – insgesamt 140 Meter lang, 6,25 Meter breit und 14 Meter hoch. „Wie bei Amazon, nur mit Werkzeugen bis zu 35 Tonnen“, so Ingo Oberste-Dommes. Für dieses Megaprojekt über 2,5 Jahre nahm er einen Stahlbauer und einen Statiker mit ins Boot und baute vor der Auslieferung in einer Halle in Welschen Ennest ein Testgelände auf, um die Grundfunktionen zu testen. In Tschechien bauten die Tüftler aus Welschen Ennest ein System, um 70 Meter lange Eisenbahnschienen lagerichtig in eine Presse zum Schmiedevorgang einzulegen. Dass ODO-Engineering trotz dieser Großaufträge und hoher Fertigungstiefe mit „nur“ sieben bis zehn Mitarbeitern auskommt, ist erstaunlich. „Wir fertigen unsere Projekte mit viel Herzblut, da muss jeder mal ran, auch ich muss schon mal die Fräsmaschine anschmeißen“, so der Chef.
Nach dem USA-Geschäft zeichnen sich bereits neue Projekte ab. „Wir überlegen, ein neues System mit einem multidirektionalen Fahrwerk zu bauen. Der Trend geht weg von den schienengebundenen zu autonom frei fahrenden Fahrzeugen.“ So etwas gebe es bereits im Logistikbereich, aber nicht im Werkzeugbereich mit 20 bis 40 Tonnen Gewicht. Oberste-Dommes: „Wir sind ständig auf der Suche nach neuen Produkten, hier zeichnet sich unsere Flexibilität aus. Jedes System hat seine Besonderheiten und spezifischen Anforderungen und wir sind in der Lage Lösungen dafür zu entwickeln. Das zeichnet uns aus.“