Gelsenkirchen. . Leser besichtigen den Automobilzulieferer und -entwickler ZF TRW. Heimischer Standort beschäftigt 560 Mitarbeiter. 25 000 Quadratmeter Fläche. 200 Millionen Euro Umsatz.
Wer sich am Steuer seines Autos über die Annehmlichkeiten seiner ebenso feinfühligen Lenkung erfreut, oder etwa über lebensrettende Sicherheitssysteme wie Spurhalteassistent und Tote-Winkel-Erkennung, der kommt vielleicht auf den Gedanken, dass das High-Tech aus deutschen Landen ist. Wohl kaum einem kommt es in den Sinn, dass sich ausgerechnet dahinter „Made in Gelsenkirchen“ verbirgt.
Auch die gut 20 WAZ-Leser, die jetzt das Werk von ZF TRW an der Freiligrathstraße besichtigen durften, wissen nun um die Tatsache, dass hier ein Konzern von Weltrang einen von seinen 230 Standorten in 40 Ländern betreibt – erfolgreich noch dazu.
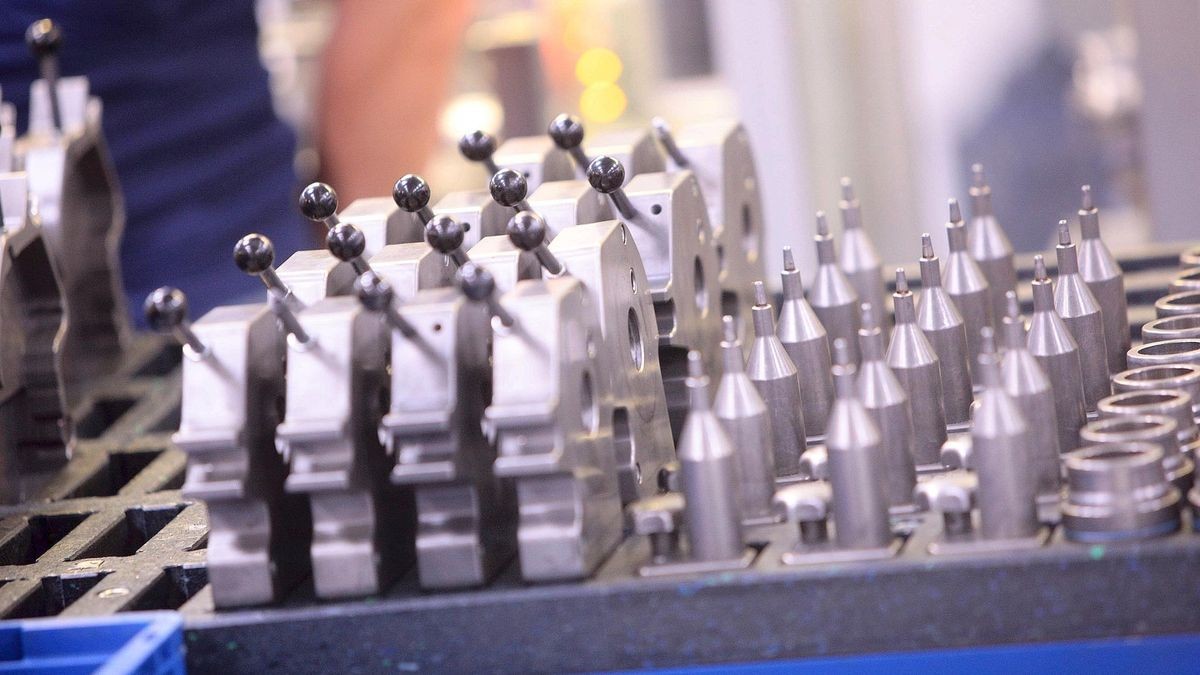
„25 000 Quadratmeter Werksfläche, 560 Mitarbeiter, 200 Millionen Euro Umsatz im Jahr – zu den Kunden zählen alle großen Fahrzeughersteller wie Volvo, Opel, Renault oder Ford“, erklärt Produktionsleiter Gottfried Kühn. Nicht wenige sind da schon recht baff.
Für noch mehr Erstaunen sorgen die blitzsauberen Produktionsstraßen, an denen einzelne Fachkräfte gleich mehrere hochkomplexe Präzisionsmaschinen bedienen und dabei wieselflinke Roboter überwachen. Etwa dort, wo die Kugelgelenke hergestellt werden. „2500 solcher Bauteile stellen wir hier in einer Schicht, also in siebeneinhalb Stunden, her“, erläutert Gottfried Kühn die Kapazität der Produktionseinheit. Kosten des Werkstücks: fünf Euro, drei Euro allein für das Material. „Im Zubehörhandel allerdings“, so der Ingenieur, „werden dafür schon 50 Euro fällig.“ Verdienst für das Unternehmen an so einem Teil: fünf Prozent.
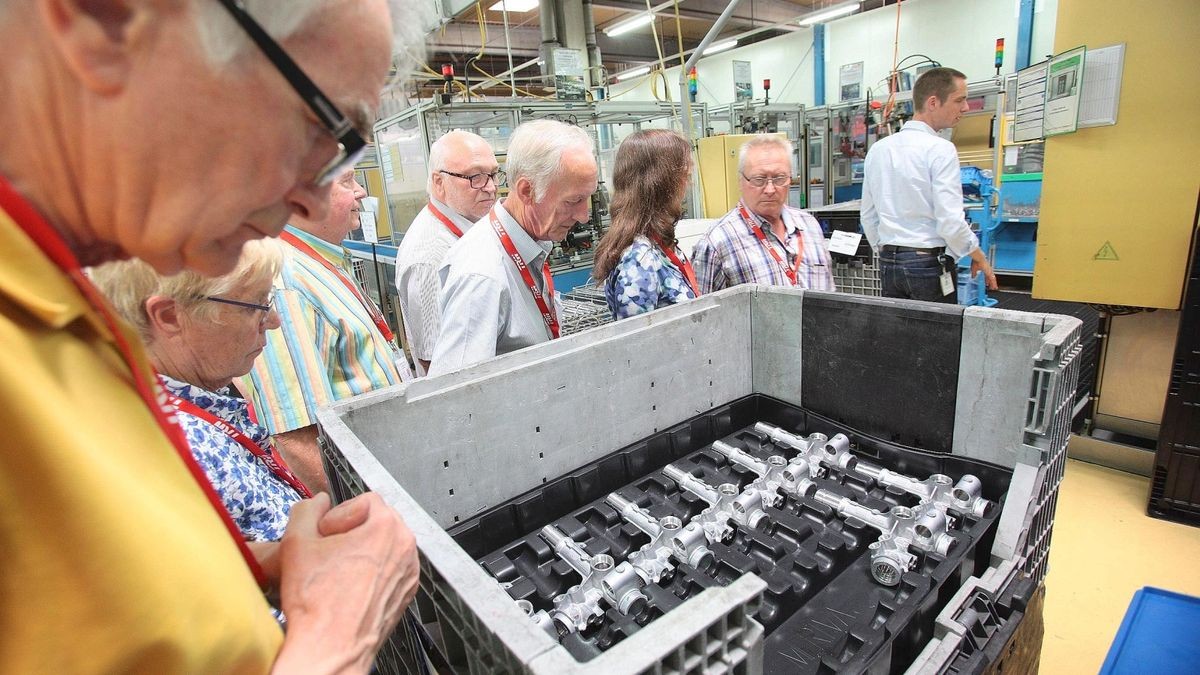
Noch größere Spannen eröffnen sich ein paar Schritte weiter – dort, wo die „kleine Hochzeit“ gefeiert wird. Die große kennzeichnet die Zusammenführung von Karosserie und Motor. Hier also, wo die Elektro-Lenkung mit dem Motor-Pumpenaggregat und dem Tank für die Hydraulik verbunden werden, schaffen die Arbeiter an einer sechs Millionen Euro teuren Anlage 1500 Einheiten am Tag. „200 Euro würde das Bauteil kosten, im Handel das Fünffache“, weiß der Produktionsleiter. Kopfschütteln bei den Lesern. „Unglaublich“ ist mehr als einmal zu hören.
Da könnte so manch’ Autoschrauber auf die Idee kommen, ein Ersatzteil hier zu kaufen, oder nicht? „Nein“, sagt Gottfried Kühn schmunzelnd, „einen Ersatzteilverkauf ab Werk gibt es nicht.“ Wohl aber eine ausgeklügelte Qualitätssicherungssystem. Ob bei den kleinen Gelenkenteilen, die mit Wirbelstrom auf Risse im Material untersucht werden bis hin zur kompletten Lenkung, bei der ein Vergleich der Ventilkennlinie am Computer darüber Aufschluss gibt, ob man oder frau potenziell zu viel Kraft aufwenden muss, um die Räder einzuschlagen. „Wir haben eine Nachbearbeitungsquote von nur ein Prozent“, sagt Gottfried Kühn. Stolz schwingt in seiner Stimme mit ob der Präzision. Nicht anders ist es bei den Lesern, schließlich ist das High-Tech – und zwar aus Gelsenkirchen!
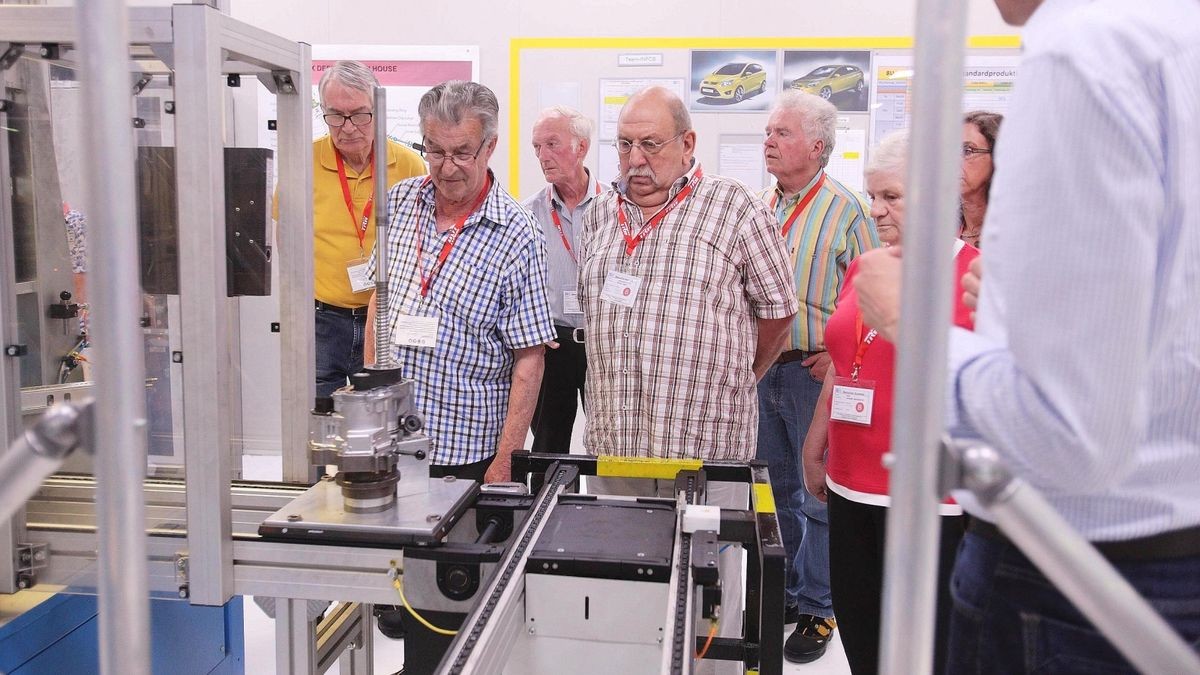