Bochum. Mit seiner Wärmebehandlung hat es die Eisenhütte Heintzmann im Tunnelbau und bei Bohrung nach Öl und Gas zu einer Ausnahmestellung gebracht.
Die Schweizer Berge sind weit weg. Aber wer den Gotthard-Tunnel durchfährt, bei dem darf ruhig ein bisschen Bochumer Heimatgefühl aufkommen. Schließlich sorgen 35.000 Tonnen, bei der Eisenhütte Heintzmann hergestellte Profilträger dafür, dass die 57 Kilometer lange Vorzeigeröhre ihre Stabilität unter dem Bergmassiv nicht verliert. „Das ist unser Referenzprojekt. Und darauf sind wir wirklich sehr stolz“, sagt Geschäftsführer Rüdiger Oostenryck.
Das Traditionsunternehmen ist ein Musterbeispiel für die erfolgreichen Weiterentwicklung eines Produkts der alten Industrie. Stahl gilt auf den ersten Blick nicht gerade als innovatives Material. Bei Heintzmann aber wird es dazu – durch eine Veredlung, die weltweit vor allem da nachgefragt wird, wo unter schwierigsten Bedingungen gearbeitet wird: im Tunnelbau und in der Explorationsindustrie – bei der Suche nach Erdöl oder Gas.
„Mittlerweile haben wir nahezu ein Alleinstellungsmerkmal“, sagt Werksleiter Arno Depping. Bei der Erdölbohrung etwa sehen sich die in Bochum hergestellten Bohrgestänge erst Widerständen wie Druck und Strömungen bei der Überwindung von 2000 Meter tiefem Wasser und zusätzlich noch von zwei Kilometer Gestein ausgesetzt. Und in Zukunft werde es wohl Bohrungen in 5000 oder 6000 Meter Wassertiefe geben. Auch dafür muss es (neue) Lösungen geben. Entscheidend sei es, so der diplomierte Werkstoffingenieur, dem Stahl durch die Behandlung in der Eisenhütte eine Festigkeit und Zähigkeit zu geben, die diesen enormen Anforderungen standhält.
In einem 34 Meter langen Durchlaufofen bei etwa 1000 Grad erhitzt
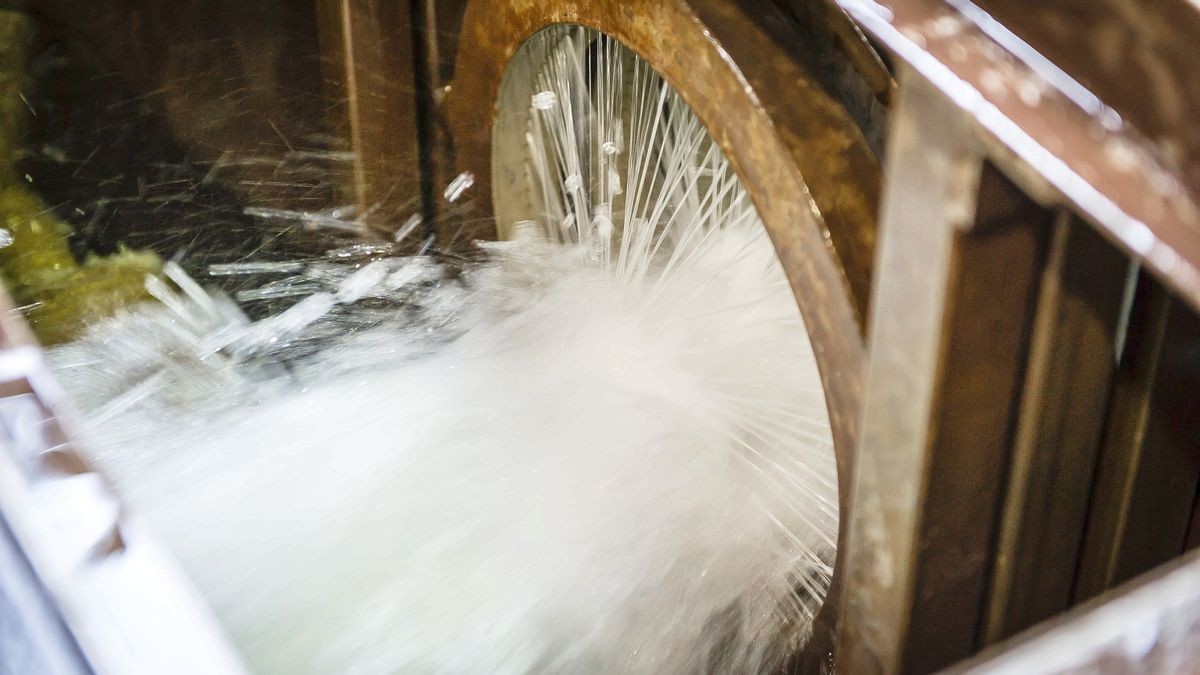
Das Verfahren dazu, eine intelligente Wärmebehandlung, ist zwar schon seit langem bekannt. Bei Heintzmann haben sie, nachdem sie 1955 damit angefangen haben, es perfektioniert. Das Prinzip: Der Stahl wird erst in einem 34 Meter langen Durchlaufofen bei etwa 1000 Grad erhitzt, kühlt dann in einem Wasserbad, bei dem je Stunde 210 Kubikmeter Wasser auf die heißen Rohre gespült werden, wieder ab, um anschließend im sogenannten Anlassofen bei 500 bis 700 Grad noch einmal erhitzt zu werden, um so die Spannungen aus dem Material herauszuholen.
„Das Entscheidende dabei ist nicht das Erhitzen“, so Depping, sondern das Wasserbad. „Um die notwendigen mechanischen, technologischen Eigenschaften zu erzielen, kommt es darauf an, wie gezielt man das Material abkühlt, um die erforderliche Güte zu bekommen.“ Je nach Anforderungen werden unterschiedlichen Brausen, Drücke oder Geschwindigkeiten beim Durchlaufen der Rohre verwendet. „Das ist keine Hexerei“, sagt Geschäftsführer Oostenryck. „Aber es erfordert viel Erfahrung, große Verantwortung, eine standardisierte Produktion und eine Produktentwicklung gemeinsam mit dem Auftraggeber.“
Kombination von Materialien und Suche nach neuen Legierungen
Drei Felder haben großes Potenzial
Eine Prognos-Studie attestiert der Bochumer Produktionswirtschaft vor allem auf den Felder Smart Production (Industrie 4.0, IT-Sicherheit), Hochleistungswerkstoffe und Antriebstechnologie großes Potenzial.
Die wesentlichen Ergebnisse der Studie stellt die WAZ in einer Serie vor. Im dritten Teil geht um Hochleistungswerkstoffe.
Als das Unternehmen um die Jahrtausendwende über den Tunnelbau nach weiteren Verwendungsmöglichkeiten für seine im Bergbau gewonnenen Erfahrungen gesucht hat und bei der Behandlung von runden und eckigen Rohren landete, habe es einige Jahre gedauert, um die höchsten Ansprüche erfüllen zu können. Aber der Einsatz hat sich gelohnt. Heute ist Heintzmann zwar immer noch ein Bergbauzulieferer und wird es nach Einschätzung des Geschäftsführers auch noch lange bleiben. Aber längst hat sich das Unternehmen breiter aufgestellt – dank seiner innovativen Werkstoffbehandlung.
Möglich war das wegen der hohen Affinität zum Stahl, so Arno Depping. „Man muss Spaß haben an einer Produktion, die dreckig ist, die mit viel Schweiß verbunden ist, und die laut ist.“ Es ist in der modernen Werkstofftechnik die Alternative zum Legierungskonzept, bei dem über die Kombination von Materialen und die Suche nach neuen Legierungen besondere Eigenschaften erreicht werden.
Werkstoff-Forschung verheißt große Sprünge
Werkstoff-Forschung ist bisweilen Glückssache. „Es gibt viele Beispiele dafür“, sagt Professor Alfred Ludwig, Inhaber des Lehrstuhls für Mikrotechnik.
Dabei will er es aber nicht belassen. „Wir wollen durch noch systematischeres Vorgehen die Chancen erhöhen, dass man etwas Neues entdeckt.“ Er arbeitet seit geraumer Zeit an sogenannten Materialbibliotheken. Legierungen aus zwei, drei oder mehr Ausgangsstoffen werden aus unterschiedlichen Winkeln und bei unterschiedlichen Temperaturen mit Ionen beschossen. Die Vielzahl der unterschiedlichen Beschichtungen auf den Trägern werden dann mit standardisierten Hochdurchsatzexperimenten auf vielversprechende Eigenschaften und Auffälligkeiten untersucht.
Kombinatorische Materialforschung nennt der gebürtiges Karlsruher diese im Vergleich zur herkömmlichen Versuchen zeit- und kostensparende Verfahren, für das er in seinem Labor eine 1,5 Millionen Euro teure, sogenannten Magnetron-Sputteranlage verwendet.
„Die Chancen für die Erfindung neuer Werkstoffe stehen gut“
Ein vielversprechendes Gerät, in dem Temperaturen bis zu 1000 Grad erzeugt werden können. Und ein Verfahren, von dem er sagt: „Die Chancen für die Erfindung neuer Werkstoffe stehen gut“ — selbst wenn sich die Wissenschaftler allein auf möglichst umweltverträgliche oder häufig verfügbare Trägerstoffe konzentrieren.
„Das Periodensystem ist sehr groß, es besteht große Hoffnung, dass man noch ganz tolle neue Werkstoffe entwickeln kann.“ Neue Werkstoffe entdecken – oder die Anwendung bestehender optimieren. Zumal: Die Wissenschaft sei sich ziemlich einig darüber, so Professor Werner Theisen, Leiter des Lehrstuhls für Werkstoffe, „dass in der Konstruktionstechnik zwar einige neue Ideen möglich sind. Aber über die Werkstoffe kann man noch Sprünge machen und wirklich Dinge schaffen, die ganz außergewöhnlich sind.“ Superlegierungen etwa müssen bis 1000 Grad funktionieren, hohe mechanische Belastungen aushalten oder sich zukünftig womöglich selbst überwachen.
Interdisziplinäres Arbeiten ist auf dem Weg dahin seit jeher ein Prinzip der Werkstoff-Forscher. „Zwischen den Fakultäten gibt es eine sehr gute Kommunikation“, so Ludwig. „Chemie und Ingenieurwesen, Physik, Elektrotechnik, Geowissenschaft, sie alle verbindet die Materialforschung. Und demnächst wird das interdisziplinäre Arbeiten an der Ruhr-Uni eine noch höhere Stufe erreichen (nebenstehender Text
40 Millionen Euro für interdisziplinäres Forschungszentrum
2017 wird das Zentrum für Grenzflächendominierte Höchstleistungswerkstoffe (ZGH) an der Ruhr-Uni fertiggestellt. Gebaut wird es im Zuge der Erneuerung der gerade abgerissenen Gebäude IA und IB. 40 Millionen Euro investieren Bund und Land in Gebäude und Ausstattung. Die Spitzenstellung der Ruhr-Uni soll so ausgebaut werden. 80 Wissenschaftler werden fachübergreifend auf 2800 Quadratmetern arbeiten, Forschungspartner kommen vom Max-Planck-Institut für Eisenforschung in Düsseldorf, dem Forschungszentrum Jülich und dem Deutschen Zentrum für Luft- und Raumfahrt.
Der neue Lehrstuhl für Werkstoffdesign ist schon besetzt: Der Inder Prof. Easo George hat sich nach 25 Jahren Forschung in den USA für den renommierten Werkstoff-Forschungsstandort Bochum entschieden, er ist auch Direktor des ZGH.