Wesel. Altana hat in Wesel 15 Millionen Euro in ein digitales Labor investiert. Dort werden weltweit neue Maßstäbe in der Spezialchemie gesetzt.
Schon von außen wirkt das Gebäude an der Abelstraße beeindruckend. Oben im ersten Stock stehen die Autos der Mitarbeiter im Parkhaus, darunter werden neue Maßstäbe in der Welt der Spezialchemie gesetzt. Der Altana-Geschäftsbereich BYK hat hier ein weltweit einzigartiges, digitales Labor gebaut. Insgesamt 15 Millionen Euro - zehn Millionen für die einzelnen Module und fünf Millionen in den Umbau des Gebäudes - hat das Unternehmen in die so genannte High-Throughput-Screening-Anlage investiert.
„Ziemlich einmalig“, umschreibt auch Projektleiter Manfred Knospe, der die Anlage seit der ersten Idee vor etwas mehr als fünf Jahren verantwortet, die architektonische Bauweise. „Wir hatten auf dem Gelände einfach keine Expansionsmöglichkeit für unser Vorhaben.“ Zudem kommen hier auf dieser Seite der Firmenfläche sämtliche Rohstoffe an, teilweise auch brennbare Stoffe. Also machte Altana aus der räumlichen Not eben eine Tugend: Wo zuvor die Sattelschlepper ihre Ladung aufnahmen, baute die Schweizer Firma Chemspeed die 300 Quadratmeter große Anlage auf.
Neue Dimensionen durch Digitalisierung bei Altana in Wesel
Und die von Robotern gesteuerte Anlage ist das beste Beispiel dafür, wie Digitalisierung für die Chemiebranche völlig neue Dimensionen erschließen kann. Die Anlage prüft, wie bestimmte Zusatzstoffe, so genannte Additive, zum Beispiel in Lacken, aber auch Kunststoffen und Klebstoffen wirken. Die aus 32 Modulen und 27 Funktionseinheiten bestehende Anlage führt vollautomatisch und digital Serientests durch. Bis zu 220 Proben in 24 Stunden pro Tag können hergestellt und getestet werden. „Dafür bräuchte ein Mitarbeiter vier bis acht Monate“, rechnet Manfred Knospe vor.
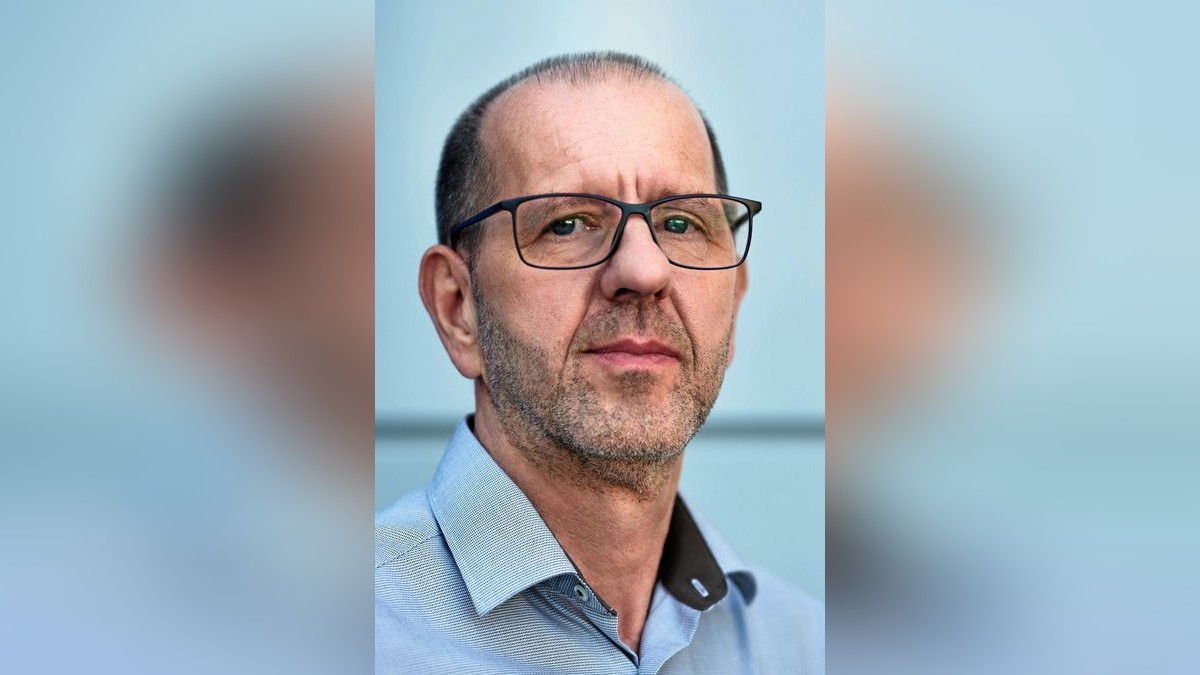
Neue Maßstäbe setzt aber auch die eingesetzte Digitaltechnologie. „Die Technik, die im digitalen Labor verwendet wird, mussten wir teilweise erst noch gemeinsam mit Partnern entwickeln. Daher sind einige der Bauteile weltweit einzigartig und kommen nur hier zum Einsatz, an unserem Heimatstandort in Wesel“, sagt Manfred Knospe stolz. Durch den Einsatz des digitalen Labors lassen sich ab sofort auch bereits existierende Produkte auf ihre Anwendbarkeit für andere Einsatzgebiete prüfen, ohne dass es dafür einen konkreten Bedarf gibt. „Das eröffnet ganz neue Möglichkeiten, die ohne die Digitalisierung von Serientests nicht denkbar wären.“
Maschine braucht statt mehrerer Monate nur Tage
Den „Maschinenraum“ betreten dürfen nur insgesamt sechs Mitarbeiter. In einem ersten Schritt füllt die Anlage alle für die Testung notwendigen Inhaltsstoffe in einen Becher oder ein Glas und wiegt es. Diese werden anschließend verschlossen, der Inhalt vermischt. Danach transportiert die Anlage die fertigen Proben (Shuttles) über ein Schienensystem weiter zu den Messinstrumenten. Die prüfen, ob die vollautomatisch gemischten Lacke den Kundenanforderungen entsprechen. Was früher Wochen oder Monate dauerte, ist nun in wenigen Tagen erledigt.
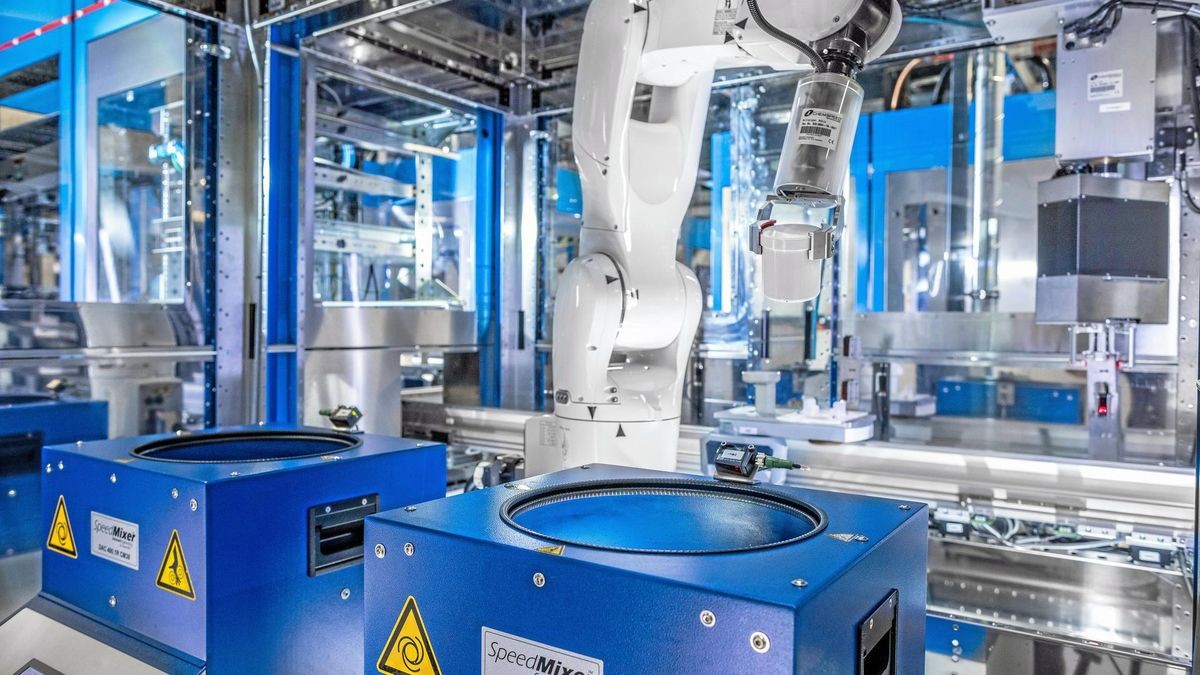
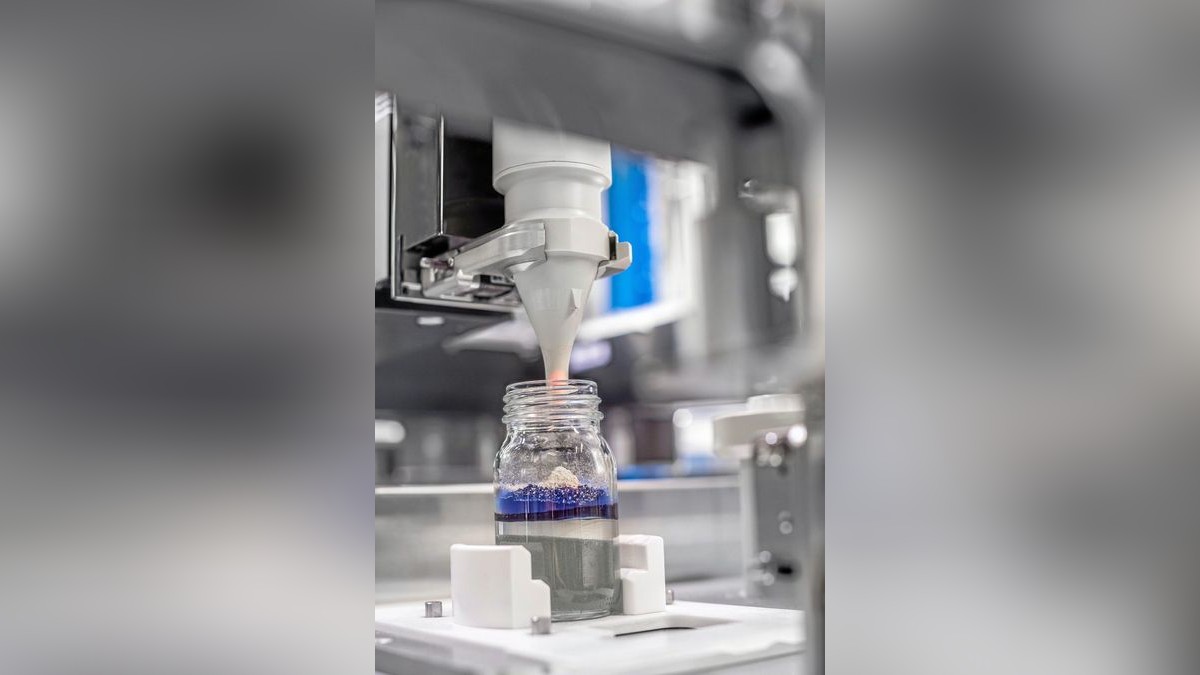
Und der durch die automatischen Reihenversuche erzielte Zeitgewinn ermöglicht den hoch qualifizierten Anwendungstechnikerinnen und -technikern bei Altana gleichzeitig auch mehr Freiraum für Kreativität: Denn wer sich bisher mit unzähligen Serientests beschäftigen musste, kann sich dank der neuen Anlage auf anspruchsvollere Laborarbeiten konzentrieren – und im besten Falle neue Lösungen entwickeln.
Was auf der anderen Seite der Abelstraße in den Köpfen entwickelt wird, erfährt im neuen Labor eine zeitnahe, schnelle Testung – in nur sechseinhalb Minuten pro Test. „Die Anlage macht exakt das, was drüben entwickelt wird“, erklärt Manfred Knospe, „nur eben automatisiert und viel schneller. Für unseren Prüfaufwand haben wir auch gar nicht ausreichend Personal.“ Im Gegenzug wird das in der Anlage Getestete auch noch einmal im Labor überprüft.
Seit knapp einem Jahr ist die Anlage in Betrieb und verdoppelt die Kapazität von BYK in der Anwendungstechnik. Noch müssen einige Dinge korrigiert und optimiert, auch mit dem Labor abgestimmt werden. „Bis die Anlage dann 24/7 läuft – und auch ohne Personal, dauert es noch etwas“, so Knospe. „Aber sie ist in ihrer Komplexität und Größe einmalig auf der Welt. Und das wird in zehn bis 15 Jahren Standard in der Industrie sein.“ In Wesel ist es das schon jetzt, denn Daten stehen hier viel schneller zur Verfügung. Zahlreiche Altana-Kunden haben sich die Anlage deshalb schon mit großem Interesse angeschaut. Vorsprung durch Innovation – das war eben schon immer die Maxime an der Abelstraße.