Hamburg. Im Hamburger Airbus-Werk soll in der Halle 260 statt des Riesenjets schon bald der A321XLR gefertigt werden. Ein exklusiver Ortsbesuch.
Es ist das letzte Überbleibsel des A380. In der Halle 260 des Airbus-Werks auf Finkenwerder steht in einer Ecke eine riesige, weiße Metalleinheit: die sogenannte Reko-Box. „Der Rumpf wird wie in eine Garage hineingefahren und seine Oberfläche anschließend mit den entsprechenden Materialien konserviert“, sagt André Walter, der Deutschland-Chef von Airbus. Die Luft wird abgesaugt, damit keine Lösungsmittel freigesetzt werden. Sollten künftig Reparaturen beim größten Passagierflugzeug der Welt anstehen, können die Mitarbeiter des Flugzeugbauers nochmals auf die Reko-Box zurückgreifen – für die Fertigung neuer A380 wird der Metallklotz allerdings nicht mehr gebraucht.
2021 wird Airbus die Produktion des A380 einstellen. In der Halle 260 wurden dafür jahrelang in der Strukturmontage Schalen zu Rumpfsektionen gefertigt und anschließend in der Ausrüstungsmontage mit Kabeln, Rohren und Haltern versehen. Doch seit 1,5 Jahren ist Schluss damit. Die dafür benötigten Anlagen wurden demontiert – bis auf die Reko-Box, deren Abkürzung übrigens für Restkonservierung steht. Denn sie kann auch für die A320-Familie genutzt werden. Und mit ihr zieht der neue Hoffnungsträger des Konzerns ein. „Mit dem A321XLR werden wir hier einen Zukunftsflieger bauen“, sagt Walter beim Exklusiv-Termin mit dem Abendblatt, das als erstes Medium einen Blick in die neue Fertigungslinie werfen durfte.
Erster Testrumpf für den A321XLR soll bald kommen
Die Halle 260 ist nun quasi zweigeteilt. Auf der hinteren Seite liegt Rumpf neben Rumpf. Rechts kommen die nackten „Tonnen“, wie sie in der Airbus-Sprache heißen, hinein. Dann werden sie nach und nach ausgerüstet. Die Beschäftigten montieren Kabel, Verkleidungen, Hydraulik, Fenster und Türen. 17 Rümpfe werden nebeneinander bearbeitet. „In dieser XLR-Halle fahren wir die Produktion auf hoher Last, in anderen haben wir sie etwas heruntergefahren“, sagt Walter. Im April verringerte das Management wegen der Corona-Krise die Rate von 60 auf 40 Flieger der Reihe pro Monat. Wenn die Rümpfe mit der grünen Aluminium-Haut ausgerüstet sind, rutschen sie weiter nach links und verlassen letztlich die Halle. Anschließend werden Sitze, Küchen und Toiletten eingebaut.
Lesen Sie auch:
- Airbus erreicht wohl das interne Auslieferungsziel für 2020
- Hamburgs Luftfahrtbranche vor dem Jobabbau
- Wie in der Corona-Krise neue Fluggesellschaften entstehen
Die andere Neuerung ist auf der vorderen Seite der Halle zu finden. Mit Gitterzäunen und weißen Plastikplanen ist ein Teilbereich abgesperrt. Ein Arbeiter eines Zulieferers schmeißt die Flex an, Funken sprühen. Für den XLR wird die Pilotlinie für die Strukturmontage gebaut. Große Arbeitsbühnen aus Stahl mit Treppen, Geländern und mehreren Ebenen werden errichtet. In die Räume dazwischen wird später der Rumpf hineingeschoben. Dann können die Monteure mit der Arbeit beginnen. „Bald werden wir hier den ersten Testrumpf für den A321XLR bauen“, sagt Walter. Für Testzwecke entstehen im Regelfall zunächst drei bis vier Flieger, ehe der erste an eine Fluggesellschaft geht. 2023 soll es so weit sein.
Der Flieger gehört zur A320-Familie, die zu mehr als der Hälfte in Hamburg endmontiert wird und der Verkaufsschlager des Konzerns ist. Fast 6000 dieser Maschinen stehen im Orderbuch. Lange Zeit wurden die Jets nur auf der Kurz- und Mittelstrecke eingesetzt. Durch sparsamere Triebwerke und nach oben gebogenen Flügelspitzen konnte Airbus in Kooperation mit den Motorenherstellern die Reichweite des Flugzeugs in der neo-Variante von 6000 auf 6800 Kilometer steigern. Die Ingenieure platzierten drei Zusatztanks. So konnte das Flugzeug als LR(Long Range)-Version 7400 Kilometer nonstop zurücklegen. Das Unternehmen erhoffte sich damit den Einstieg in den Langstreckenbereich. Im Juni 2019 stellte es bei der Luftfahrtmesse in Paris noch weitergehende Pläne vor, die XLR-Version.
Die Nachfrage nach dem Jet ist hoch
Dank eines zentralen Tanks (Rear Center Tank) im Gepäckraum steigt die Reichweite nun sogar auf 8700 Kilometer. Neue Strecken wie von Hamburg nach Chicago oder Mumbai sowie von Sydney nach Tokio werden mit der Maschine möglich. Weil viele Passagiere wegen der Corona-Krise noch lange Zeit auf Langstreckenflüge verzichten werden, dürfte sich auf vielen sogenannten „dünnen Routen“ der Einsatz von Großraumflugzeugen nicht lohnen – die Chance für die 44,51 Meter lange Maschine mit Extrareichweite. „Diese ,dünnen Routen‘ wird es nach der Krise zunächst fast ausschließlich geben – durch den Einsatz der A321XLR können sie für Airlines aber profitabel werden“, sagt Chief Operating Officer (COO) Michael Schöllhorn. Die Nachfrage nach dem Jet sei hoch, mehr als 450 Bestellungen sollen vorliegen.
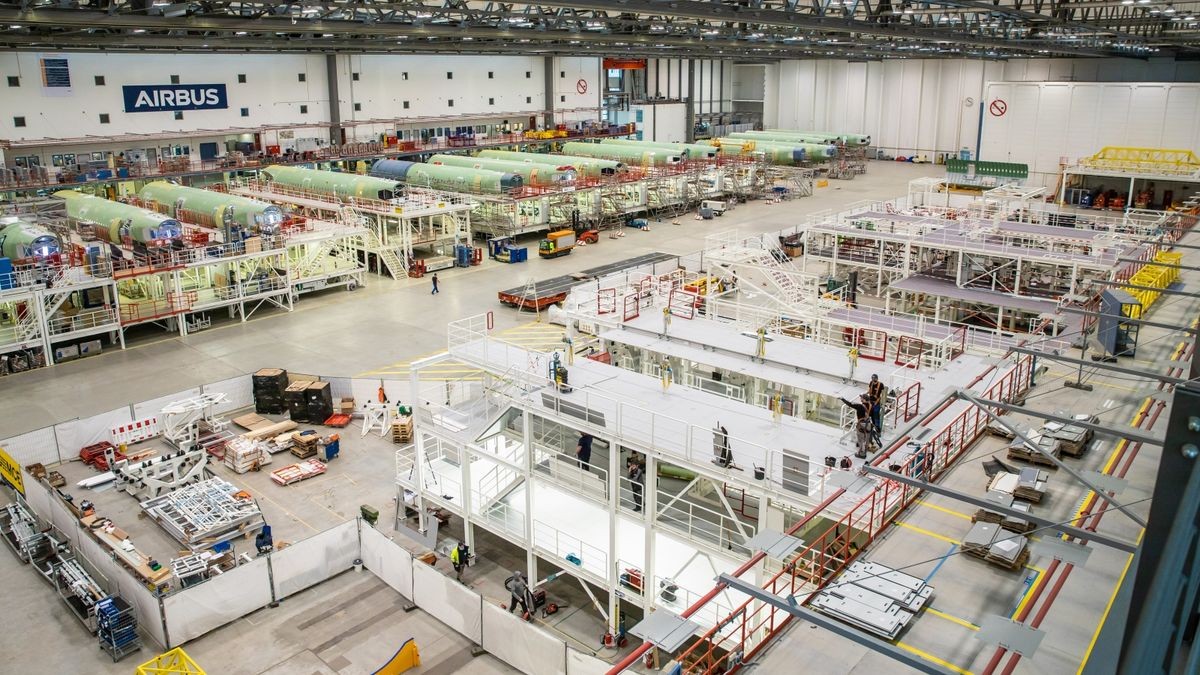
Ganz einfach ist die Fertigung der Maschine allerdings nicht. „Die größte Herausforderung beim XLR ist der Rear Center Tank“, sagt Walter. Er sitzt in der Mitte des Flugzeuges direkt hinter den Tragflächen, ist relativ steif und muss (natürlich) dicht sein. Im Rumpf ist eine Lücke für ihn vorgesehen. Später in der Produktion soll der Tank auf ein fahrbares Gestell gepackt werden, das unter den Rumpf rollt und den Tank passgenau hydraulisch hineinhebt. Millimeterarbeit.
Der Tank wird also Teil der äußeren Rumpfstruktur, auf die bei Start und Landung sowie durch Druck- und Temperaturunterschiede große Kräfte wirken. „Diese Kräfte dürfen aber nicht dazu führen, dass der Tank verformt wird“, sagt Walter. Aus dem Verteidigungs- und Raumfahrtbereich habe man bereits Erfahrungen mit solchen Tanks, die zum Beispiel im Eurofighter verbaut sind. Mit den Kollegen aus der Division würden Erfahrungen ausgetauscht. „Es ist das erste Mal, dass wir in ein ziviles Flugzeug so einen Tank in dieser Größe hineinbauen“, sagt Walter.
Das Flugzeug kann fast 40.000 Liter Kerosin fassen
Immerhin fasst der Tank, der von der Tochter Premium Aerotec kommt, 12.900 Liter. Die mögliche Füllmenge des Flugzeuges steigt damit auf knapp 37.000 Liter Kerosin. Mit einem weiteren optionalen vorderen Zusatztank wären es fast 40.000 Liter. Für die Koffer der Passagiere soll übrigens immer noch mehr als genug Platz da sein. Für Fracht, die ohnehin stets den Großteil des Gepäckraums füllt, wird es entsprechend weniger.
In der Halle 260 wird es sechs Plätze für die Strukturmontage geben. Wenn der Rumpf fertig ist und im Inneren Halter angebracht sind, kommt er in eine andere Halle. Durch das neue Kabinenlayout All Cabin Flex (ACF) haben die Airlines eine Vielzahl von Gestaltungsmöglichkeiten. Je nach Positionierung der Toiletten oder Wahl einer Business Class werden dort Leitungen und Rohre entsprechend der Kundenwünsche verlegt. Dieses flexible Kabinenlayout kostet allerdings viel Zeit. Als es vor gut zwei Jahren eingeführt wurde, wurde der Arbeitsaufwand unterschätzt.
Daher musste Personal von anderen Standorten hinzugezogen werden. Die Bauzeit für die XLR-Version soll nun grundsätzlich aber nicht länger werden. „Nur zu Beginn werden wir ein höheres Stundenvolumen fahren, also mehr Mitarbeiter in der Maschine haben“, sagt Walter. Schließlich solle der Flieger im Takt der anderen Maschinen bleiben und im Gesamtsystem mitfließen.
Rund 240 Mitarbeiter wurden zusätzlich für die Produktion des Fliegers eingestellt
Wie viel Geld Airbus in die XLR-Produktion in Hamburg investiert, will das Unternehmen nicht sagen. Insgesamt seien es über mehrere Jahre gesehen 300 Millionen Euro. „Dass wir den XLR in Hamburg trotz der Krise bauen wollen, ist ein klares Bekenntnis zum Standort und für die Beschäftigten“, sagt Walter. „Wir glauben an das Flugzeug, wir glauben an einen Neustart nach der Krise, und wir glauben an den Standort.“ Rund 240 Mitarbeiter wurden zusätzlich für die Produktion des Fliegers mit der extralangen Reichweite eingestellt, der zunächst nur auf Finkenwerder entsteht.
Mit der A380-Produktion sind hingegen nur noch wenige Mitarbeiter beschäftigt. Lackierarbeiten, der Einbau der Inneneinrichtung und Auslieferungen stehen noch an. Eine Handvoll Exemplare des größten Passagierflugzeuges der Welt werden noch ausgeliefert. Die japanische Fluglinie All Nippon Airways erhält eine, der Rest entfällt auf Emirates. Die arabische Airline war mit 123 Bestellungen bei insgesamt 251 Aufträgen der mit Abstand größte A380-Kunde. Die meisten Beschäftigten seien in anderen Flugzeugprogrammen untergekommen, heißt es. Ein Teil werde aber auch noch gebraucht, um in der Zukunft die Flieger sowie mögliche Modifikationen zu betreuen und Ersatzteile zu liefern.
Auch wenn das Aus für die A380-Produktion des Flugzeuges nur 14 Jahre nach der Erstauslieferung relativ früh kommt, verteidigt das Management das Programm. „Die Entscheidung für den Bau der A380 war richtig“, sagte Schöllhorn. Man sei dadurch eine andere Firma geworden, habe die Integration des Unternehmens insbesondere in Deutschland und Frankreich vorangetrieben. Zwar habe sich der Markt nicht wie gewünscht entwickelt, aber man habe viel gelernt, so Schöllhorn: „Der A380 war für uns ein ganz wichtiges Flugzeug. Die Passagiere lieben es, und viele Emotionen hängen an ihm.“