Hamburg. Arcelor Mittal investiert 15 Millionen Euro und bekennt sich zum Standort. Anlage verbraucht deutlich weniger Energie.
Schrauben, Stahlseile und -federn, Nägel, Kurbelwellen, sogar Angelhaken. Die Liste der Produkte, die aus Hamburger Stahl hergestellt werden, ist lang. „Die Automobilindustrie ist einer unserer großen Abnehmer“, sagte Uwe Braun, der Chef des zum ArcelorMittal-Konzern gehörenden Stahlwerks an der Dradenaustraße in Waltershof. Etwa eine Million Tonnen Stahl pro Jahr stellen die 550 Mitarbeiter dort her. Sie schmelzen Schrott ein, verarbeiten und veredeln Eisenerze zu Rohstahl – und verbrauchen dabei Unmengen von elektrischem Strom in einem sogenannten Elektrolichtbogenofen. Das Hamburger Stahlwerk ist – noch vor dem Kupfer- und Metallhersteller Aurubis – der größte Stromverbraucher der Stadt.
50 Jahre nach der Inbetriebnahme ist das in Zeiten günstiger Energiepreise geplante und errichtete Werk zugleich auf dem Weg zum Hersteller von „grünem“ Stahl. In den nächsten Jahren soll an der Dradenaustraße eine Antwort auf die Frage gefunden werden: Lässt sich Stahl auch herstellen, ohne dass dabei klimaschädliches Kohlendioxid (CO2) freigesetzt wird?
Ein Schritt auf dem Weg zum Öko-Stahl wurde am Donnerstag gemacht: Das Stahlwerk weihte eine neue Anlage ein, die deutlich weniger Energie verbraucht und deshalb auch weniger CO2 freisetzt als ihre Vorgängerin. Ein sogenannter Hubbalkenofen, 15 Millionen Euro teuer. Ungewöhnlich: Zu den Feierlichkeiten unter Schutzhelm und Warnweste fanden sich mit Michael Westhagemann (parteilos) und Jens Kerstan (Grüne) gleich zwei Hamburger Senatoren ein.
Große Bedeutung der Grundstoffindustrie
Westhagemann betonte dabei die große Bedeutung der Grundstoffindustrie für den Wirtschaftsstandort Hamburg. „Wir brauchen die Hersteller von Kupfer, Stahl und Aluminium in der Stadt. Wenn es dort nicht mehr ordentlich läuft, haben wir ein Problem“, sagte der frühere Industriemanager. Das Stahlwerk sei ein besonders gelungenes Beispiel für ein nachhaltiges Industrieunternehmen, das Klima- und Umweltaspekte berücksichtige. Kerstan sagte zugleich, er sei stolz auf die bei diesem Themen „innovative Industrie“ in der Hansestadt – und lobte, dass im Stahlwerk bereits „weitere Projekte in der Pipeline“ seien. Der in den vergangenen drei Jahren errichtete Hubbalkenofen wird pro Jahr etwa 19.000 Megawattstunden aus Erdgas gewonnene Energie weniger verbrauchen als sein Vorgänger. Nach Angaben von ArcelorMittal werden dadurch zudem sieben Prozent weniger Kohlendioxid ausgestoßen – insgesamt etwa 3800 Tonnen pro Jahr.
Der ökologischen Nutzen des geringeren Schadstoffausstoßes ist aber nur einer von vielen Gründen für das 15-Millionen-Euro-Investment. Auch wirtschaftlich sprach sehr viel dafür. Denn, wenn es weniger Kohlendioxid ausstößt, muss das Stahlwerk auch weniger Emissionsrechte teuer einkaufen. Vor allem aber kann das Unternehmen mit der neuen Anlage jetzt Produkte herstellen, die seine Kunden verlangen.
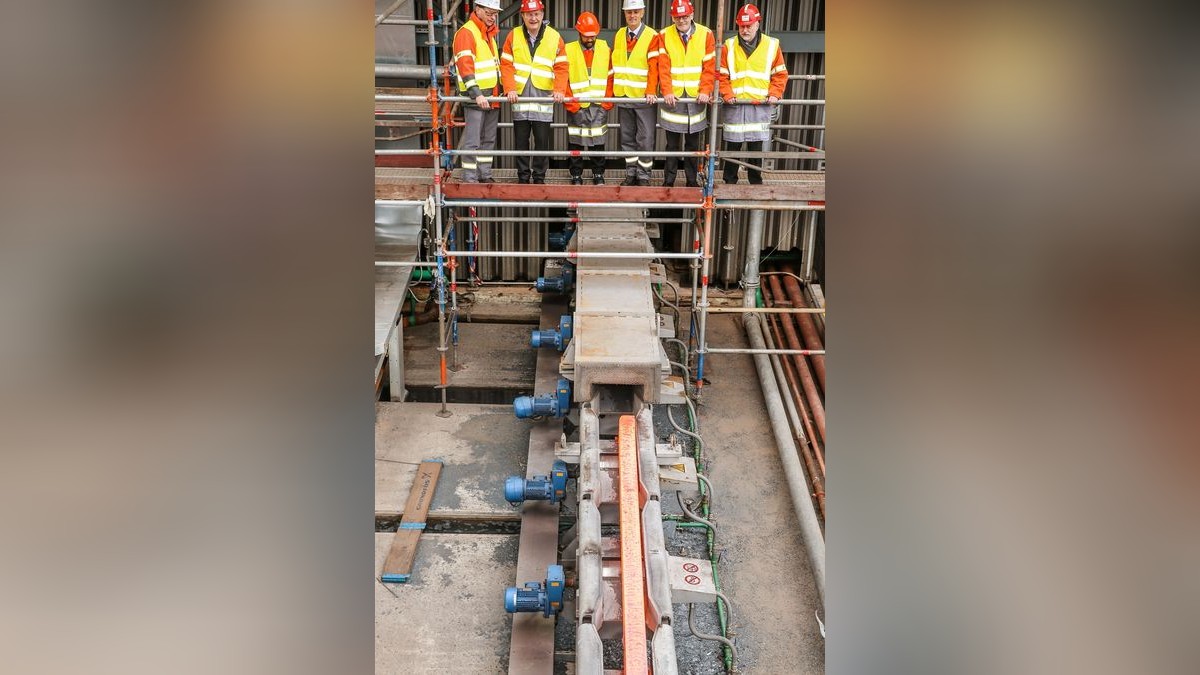
In dem Ofen werden die sogenannten Knüppel – mehr als zehn Meter lange und tonnenschwere Stahlstäbe vom Umfang eines Bierdeckels auf mehr als 1000 Grad erhitzt. Dann kann der rotglühende Stahl zu dünnem Draht ausgewalzt werden – in insgesamt 20 verschiedenen Stärken zwischen drei und 17 Millimetern. Am gängigsten sind 5,5 Millimeter. Aus einem Knüppel entstehen dann acht Kilometer Draht, aufgerollt zu einem 1,5 Tonnen schweren sogenannten Coil. Die Kunden aber wollen die 300 unterschiedlichen Stahlsorten aus dem Hamburger Werk lieber in längeren und schwereren Drahtrollen kaufen. Weil sie damit weniger Arbeit haben.
Zwei Tonnen schwere Coils
„Jetzt können wir bis zu zwei Tonnen schwere Coils produzieren“, sagte Werksleiter Braun. Das Ziel sind 2,5 Tonnen. Dafür sollen in den nächsten Jahren weitere zehn Millionen Euro an der Dradenaustraße investiert werden. Der Vorstand des Stahlkonzerns hat den Grundsatzbeschluss dazu bereits gefasst. Werksleiter Braun sieht in den Investitionen auch ein Bekenntnis des Unternehmens zum Standort Hamburg.
Der behauptet sich auf dem hart umkämpften Markt vor allem durch Stahl von besonders hoher Qualität. Dieser ist bei den Kunden durchaus gefragt. Daher soll in Waltershof künftig auch mehr produziert werden können. Eine weitere Zehn-Millionen-Euro-Investition ist ebenfalls von der Konzernspitze bereits abgenickt worden. „Die Stranggussanlage, in der der flüssige Stahl zu Knüppeln gegossen wird, soll von sieben auf acht Linien erweitert werden“, sagte Lutz Bandusch, früher selbst Chef des Stahlwerks. Er ist jetzt bei ArcelorMittal für einen Teil des sogenannte Langprodukte-Geschäfts und damit für sieben Werke des Konzerns in Europa zuständig.
Ausstoß von CO vermeiden
Ein weiterer Schritt in Richtung Ökostahl ist schon vorbereitet. Die Abwärme des neuen Ofens kann künftig als Fernwärme genutzt werden. Es ist genug vorhanden, um damit insgesamt rund 2500 Hamburger Wohnungen zu beheizen. Derzeit ist das allerdings noch Theorie, weil keine Leitung unter dem Strom hindurch in die Wohngebiete am Nordufer der Elbe existiert, geplant aber ist sie. Die Wärme aus dem Stahlwerk würde dazu beitragen, das Kraftwerk Wedel zu ersetzen. Es ist eines der „weiteren Projekte in der Pipeline“, auf die der Umweltsenator hinwies.
Ein anderes ist womöglich noch ambitionierter: Die Stahlherstellung ganz ohne die Nutzung fossiler Brennstoffe und die Freisetzung von Kohlendioxid. Beim Einschmelzen von Stahlschrott kann das zweifellos gelingen. Vorausgesetzt, der Strom stammt ausschließlich aus erneuerbaren Quellen wie Wind und Sonne.
Weitaus komplizierter ist das jedoch bei der Verarbeitung von Eisenerz zu Rohstahl. Die Energie dafür stammt heutzutage bereits zu 60 Prozent aus Wasserstoff, zu 40 Prozent aus Erdgas. „Wir wollen in den nächsten Jahren herausfinden, ob es möglich ist, in der Reduktionsanlage zu 100 Prozent Wasserstoff einzusetzen“, sagte Bandusch. Ob genug von dem Energieträger zur Verfügung stehe und zu welchem Preis, das sei derzeit noch nicht wichtig. „Wir wollen zunächst herausfinden, ob es überhaupt funktioniert“, betonte Bandusch.
Die beiden Senatoren betonten, die Industrie habe die Unterstützung der Hamburger Politik auf dem Weg zu einer nachhaltigeren Produktion. Die Stahlmanager hörten das gerne - und lobten „konstruktive Gespräche“ mit den Behörden. Ganz reibungslos – auch das klang bei der Feierstunde an der Dradenaustraße zwischen den Zeilen an – läuft das nicht immer. Das Verfahren zur Genehmigung einer Windkraftanlage auf dem Stahlwerksgelände hatte schließlich sechs Jahre gedauert.