Hamburg. Wie der Hamburger Zulieferer Diehl Comfort Modules mit 1000 Beschäftigten vom Boom kleiner Flieger profitiert.
Andre Borgardt hat auf der Toilette Platz genommen. Er beugt sich unter den Waschtisch, schraubt ein Steuergerät für den Wasserhahnsensor fest, montiert die Kabel und baut die Verkleidung an. An die Enge des Raums ist der Monteur gewöhnt. Borgardt fertigt die WC-Einheiten für den Kurzstreckenjet A320 von Airbus. Rund 1800 Exemplare stellt sein Arbeitgeber Diehl Comfort Modules (DCM) in diesem Jahr für diesen Flugzeugtyp her. Tendenz steigend.
„Die Stückzahl für die A320-Familie wird in den nächsten Jahren sicherlich nach oben gehen“, sagt Produktionsleiter Torsten Gerhardt. Schließlich will der europäische Flugzeugbauer, der auf Finkenwerder nur einige Hundert Meter entfernt in der Nachbarschaft von DCM sitzt, die monatliche Rate seines Verkaufsschlagers von derzeit 44 Stück bis Mitte 2019 auf 60 Exemplare hochfahren. Es ist ein rasanter Anstieg, der DCM-Geschäftsführer Horst Ullrich aber keine schlaflosen Nächte beschert: „Der geplante Ratenhochlauf stellt für uns kein Problem da.“
Ein Klo kann soviel kosten wie eine Luxuslimousine
Das Unternehmen kann intern die Kapazitäten verschieben. Denn während das Geschäft bei Airbus mit dem Kurzstreckenjet boomt, fehlen Neuaufträge für das größte Passagierflugzeug der Welt, sodass das Fertigungstempo des A380 gedrosselt wird – für den die Toiletten ebenfalls von DCM kommen. Und während der Großraumjet bis zu 18 Toiletten an Bord hat, sind es bei der A320-Familie im Normalfall zwischen drei und fünf. Wobei eine so teuer ist wie ein Auto. „Je nach Ausstattung kostet eine WC-Einheit so viel wie ein Mittelklassewagen oder eine Luxuslimousine“, sagt Gerhardt. Genaue Zahlen gibt das Unternehmen aber nicht heraus. Noch teurer sind die Duschen, die das Unternehmen für den A380 baut. Die Nasszelle an Bord muss den Fluglinien einen sechsstelligen Betrag wert sein. Es ist für den Zulieferer ein Nischengeschäft, nur rund 30 Stück werden pro Jahr auf Finkenwerder gefertigt. Von den Toiletten waren es im Jahr 2015 rund 3000 Stück – und alle wurden an Airbus geliefert.
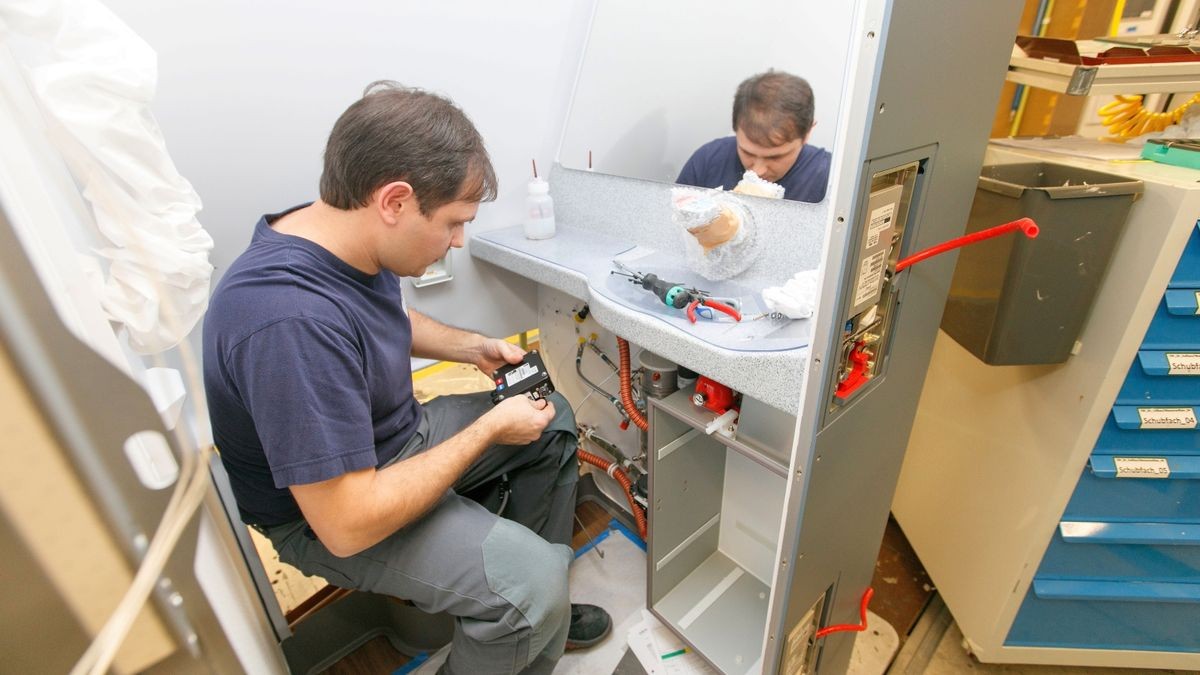
Es ist eine Abhängigkeit, die sich geschichtlich erklärt: Unter dem Namen Dasell wurde die Firma vor gut 20 Jahren als Gemeinschaftsunternehmen von Airbus und dem hessischen Bordküchenhersteller Sell gegründet und 2010 vom Nürnberger Industriekonzern Diehl übernommen. Es ist eine Abhängigkeit, die Risiken birgt: Denn beim neuen Langstreckenjet A350 wurde erstmals der französische Zodiac-Konzern als Lieferant der Bordtoiletten ausgewählt. Es ist aber auch eine Abhängigkeit, die Ullrich durchbrechen will: „Es ist unser strategisches Ziel, mit anderen Flugzeugherstellern ins Geschäft zu kommen. Embraer wäre schön, vor allem Boeing aber wäre wichtig, um auch Volumen bei den Aufträgen zu generieren.“
Rund drei Viertel des Jahresumsatzes von rund 190 Millionen Euro machen die Airbus-Aufträge aus, der Rest stammt aus dem Verkauf von Ersatzteilen und dem Nachrüstgeschäft. Nach mehreren Jahren im Einsatz sehen einige Toiletten und Waschräume nicht mehr schön aus. DCM hofft auf Aufträge von Fluglinien zur Modernisierung. Ullrich, 51 Jahre alt und Diplom-Ingenieur der Technischen Informatik, sagt: „Das Nachrüstgeschäft wollen wir ausbauen. Hamburg wird dabei eine große Rolle spielen.“
Die Schwesterfirma baut Bordküchen
Das im Takt der Branche kontinuierlich gewachsene Unternehmen bekannte sich im April 2015 zum Standort. Damals wurde der Umzug der Schwesterfirma Diehl Service Modules (DSM), die bei 40 Millionen Euro Jahresumsatz vor allem Bordküchen herstellt, aus Niendorf in einen Neubau am Genter Ufer in Waltershof bekannt gegeben.
Im Januar zogen nun die ersten Mitarbeiter in das langfristig gemietete Gebäude. Es wird ein Zentrallager geben. Die Bordküchen-Tochter soll in DCM integriert werden, sodass es beim drittgrößten Luftfahrtindustrieunternehmen in der Stadt dann eine Firma mit insgesamt rund 1000 Beschäftigten gibt. Statt sieben Standorten soll es Ende 2016, wenn der Umzug abgeschlossen ist, nur noch zwei geben. Ullrich ist froh, dass der Teiletourismus und die Personalverschiebungen zwischen den Werken ein Ende haben – und über die Umzugsentscheidung: „Ich finde es sehr beachtlich, dass die Firma Diehl hier in Hamburg investiert und die Produktion nicht in Billiglohnländer verlagert.“ Zur Höhe des Investments will er sich aber nicht äußern.
Die Produktion am Hein-Saß-Weg ist in zwei Teile gegliedert. Für die Vormontage werden die von Zulieferern bezogenen Teile wie Türen und Waschtische auf Container gepackt. Dann bereiten die insgesamt rund 500 Monteure die Teile für den Einbau vor. Beispielsweise setzen sie Gewinde und Aschenbecher in die Türen ein und montieren die Schlösser. Nach der Lackierung durch eine Fremdfirma im Haus gehen die Teile in die Endmontage. „Alles, was durch eine Flugzeugtür passt, montieren wir hier fertig“, sagt Produktionsleiter Gerhardt.
Sein Mitarbeiter Christian Grabbert steht auf einer Leiter und arbeitet von oben an einer Toiletteneinheit. Der Monteur schraubt Abluftkrümmer fest, schließt Schläuche an und baut damit das Luftaustauschsystem mit Rauchwarngeber auf. Wichtige Arbeiten für den späteren Einsatz in der Praxis. Grabbert: „Wenn an Bord einer raucht, geht der Feuermelder an, und das System saugt die Luft ab.“