Hamburg. Auf Finkenwerder fährt die neue Endmontagelinie für A320-Jets hoch, die modernste im Konzern. Das Abendblatt durfte als Erstes hinein.
Der Kopf von Luise bewegt sich für seine 280 Kilogramm äußerst geschmeidig. Fast lautlos dreht er sich einmal um die eigene Achse und steuert ein kleines grünes Stück Blech an. Die Befehle erhält der Roboter von Fran Martinez. Per Tastatur gab der Spanier zuvor die Ziele von Luise ein. Kameras prüfen die Koordinaten. Ein rotes Licht flackert auf – die Position stimmt.
Dann erledigt Luise ihre Testaufgabe: Sie bohrt das Loch vor, finalisiert es und sorgt für eine Vertiefung zum Versenken des Niets. Und das Ganze überraschend leise. Es klingt wie eine etwas lautere Lüftung. Die Späne werden gleich abgesaugt. Ein paar Sekunden später ist Luise bereit für das nächste Loch. Martinez überwacht auf seinem Monitor die Bohrungen: „Perfekt!“
Luise und Renate, die Roboter-Schwestern
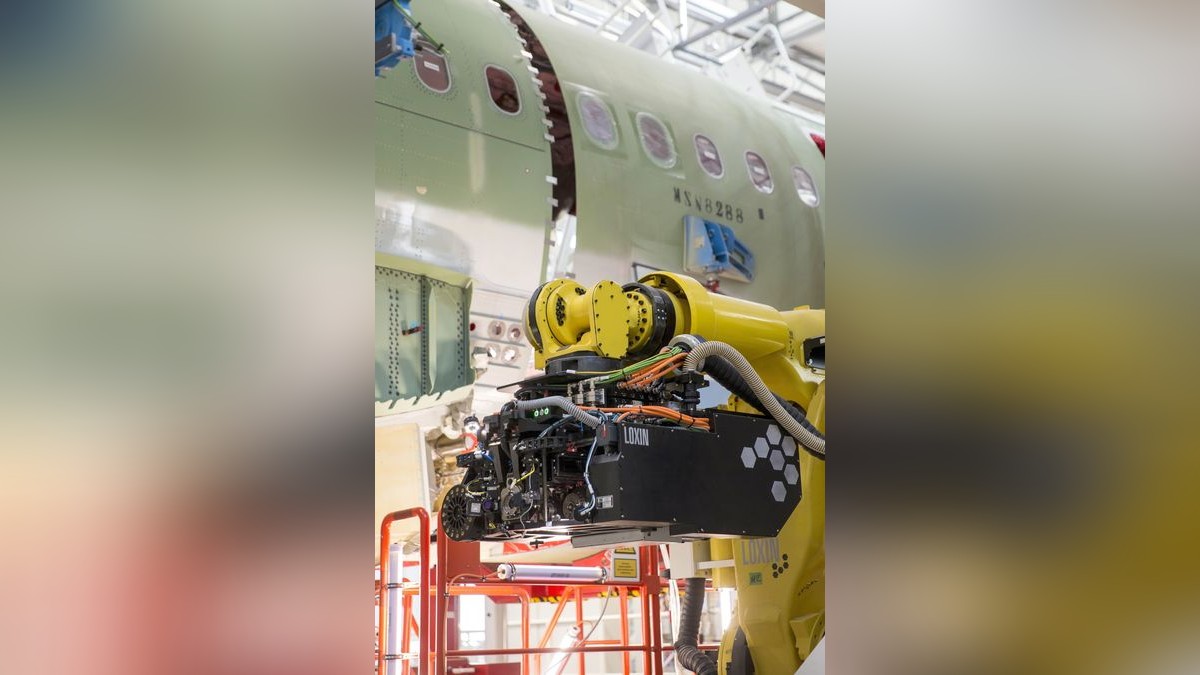
Luise hat noch eine Schwester namens Renate, eine spanische Mutter (die Firma Loxin) und wohnt seit Kurzem in Hamburg. Die beiden Roboter-Schwestern bilden das Herzstück der vierten Endmontagelinie in Hamburg, die Airbus im Herbst 2015 für die A320-Familie beschlossen hatte. Die Produktion des Verkaufshits soll von damals 43 Maschinen im Monat auf konzernweit 60 Stück bis Mitte 2019 hochgefahren werden. Der Flugzeugbauer will so den hohen Auftragsbestand abarbeiten, mehr als 6000 Maschinen stehen im Orderbuch. Dank der vierten Endmontagelinie soll die jahrelange Wartezeit für Airlines auf Maschinen nun deutlich verkürzt werden. Aber sie soll für den Konzern deutlich mehr sein: ein Labor für den Flugzeugbau der Zukunft.
„Wir machen die Tür für den Eintritt in die Digitalisierung auf“, sagte Frank Rocksien, der die vierte Endmontagelinie leitet. Eine große Aufgabe, schließlich ist das Flugzeug vor mehr als 30 Jahren in 2-D konstruiert worden. Das macht die Umwandlung in 3-D aufwendig. Seit 25 Jahren ist der gelernte Kfz-Mechaniker ununterbrochen bei Airbus. Nach seinem Einstieg als Quereinsteiger lernte er Metallflugzeugbauer, bildete sich stetig weiter und leitete später die Endmontage im chinesischen Werk in Tianjin.
Hamburg als konzernweites Vorbild bei Airbus
Der 53-Jährige hat viel erlebt, sagt aber: „Die vierte Endmontagelinie in Hamburg ist eine besondere Herausforderung für mich. Sie ist die modernste und Vorbild innerhalb des Konzerns.“ Es werden eine Reihe von neuen Technologien eingesetzt, die Arbeitsabläufe unterscheiden sich stark von den drei anderen Fertigungslinien.
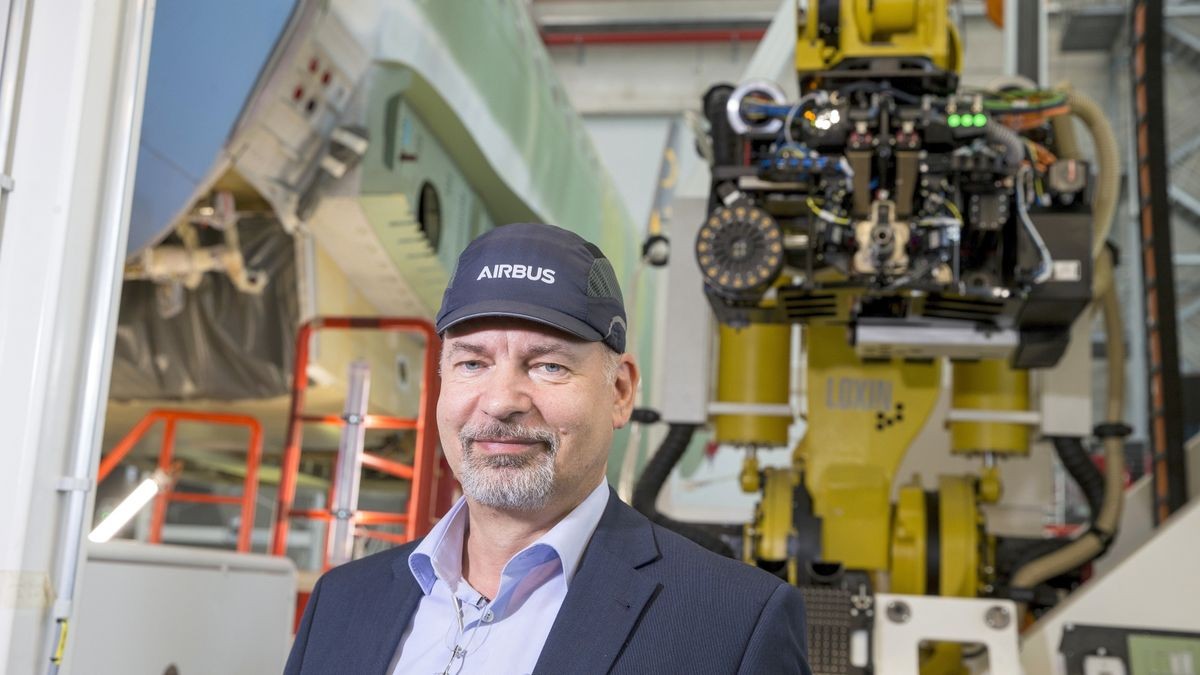
Eine grundlegende Neuerung wird bereits auf den ersten Blick deutlich. Bisher wurde das Flugzeug in Linie produziert. Vereinfacht gesagt: Die Rümpfe kamen links in die Halle rein, erhielten auf gerader Linie immer mehr Anbauten und kamen rechts als fast fertige Flugzeuge heraus. Das hat sich in der vierten Endmontagelinie geändert. In den Hallen 213 und 214 – in denen bis zum April 2017 noch am größten Passagierflugzeug der Welt, dem A380, gearbeitet wurde – wird jeder Winkel des Platzes ausgenutzt. Die Flugzeuge rücken in der Halle auch mal von links nach rechts an die Wand. Das ermöglichte, die Grundfläche um ein Drittel zu reduzieren.
Keine Kräne und keine Tide-Abhängigkeit
Auch beim Blick an die Hallendecke fallen Veränderungen auf. Es gibt dort keine großen Kräne. Die Rümpfe kommen auf multi transport platforms (MTP) in die Hallen und werden auf ihnen von einem Bauplatz zum nächsten gefahren. Die MTPs werden über ein GPS-System gesteuert. Insgesamt 40 Laser sind in beiden Hallen auf den MTPs und großen Arbeitsbühnen angebracht und bestimmen über Reflektoren immer wieder ihre Position.
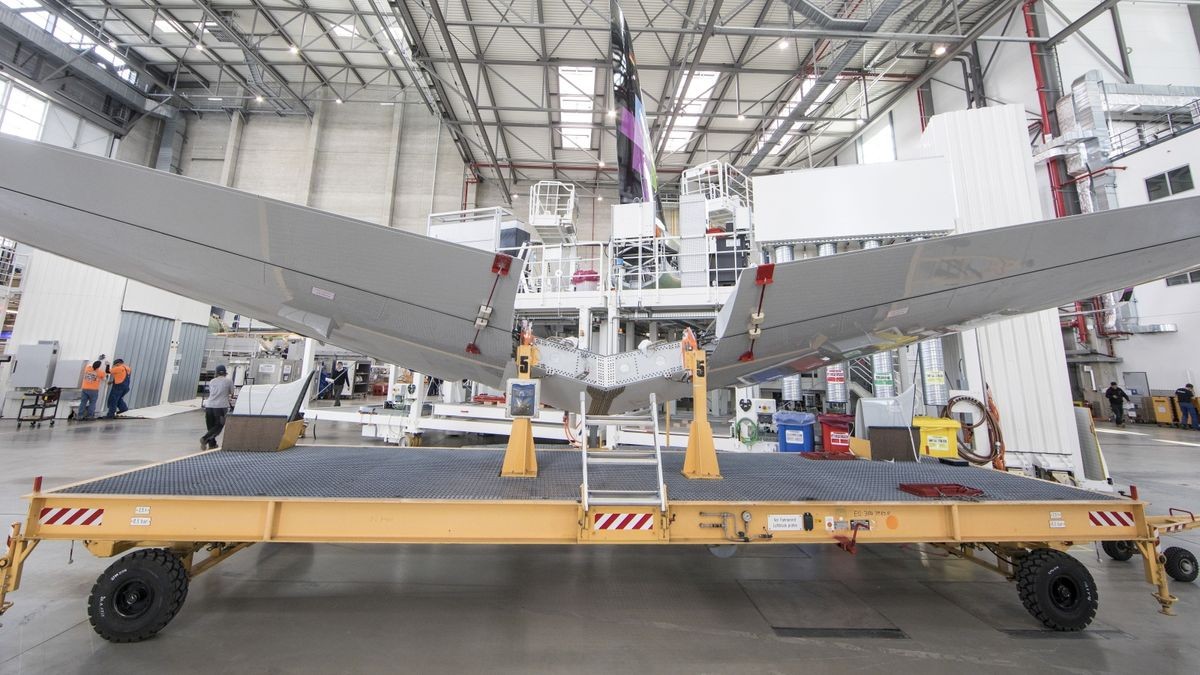
„Die MTPs bewegen sich mit rund 1,5 bis zwei Kilometern pro Stunde und einer Genauigkeit von zwei Millimetern beim Eintakten“, sagt Rocksien. Eintakten heißt der Wechsel von einem Bauplatz zum nächsten – in den anderen Endlinien werden dafür Kräne eingesetzt. Auf Cradles (Wiegen) kann das Flugzeug in alle Richtungen bewegt werden, sodass es perfekt ausgerichtet ist.
Damit macht sich der Flugzeugbauer unabhängig von der Tide, die beim Ausrichten in den anderen Linien berücksichtigt werden muss, weil sich mit Ebbe und Flut, die Neigung des Hallenbodens um Bruchteile von Millimetern verändert. „Alle Stationen sind beweglich. Wir können das System innerhalb von zwei bis drei Tagen ab- und in einer anderen Halle wieder aufbauen“, sagt Projektleiter Jens Siebels. „Damit haben wir eine neue Flexibilität geschaffen.“
Eine alte Air-France-Maschine als Testobjekt
Im vergangenen Juli kam erstmals ein A320 in die vierte Endmontagelinie. Eine alte Air-France-Maschine wurde zu Trainingszwecken gekauft, jeder Arbeitsschritt wurde immer wieder an ihr trainiert. Noch im selben Monat kam die erste Kundenmaschine in die Halle. Sukzessive gilt es nun die Geschwindigkeit zu erhöhen. Zunächst wurde alle 16 Tage getaktet, Ende des Monats soll es alle acht Tage passieren und Anfang Mai nächsten Jahres schon alle zwei Tage. „Wir werden ab dem Frühjahr 2019 zehn Flugzeuge pro Monat schaffen“, sagt Rocksien. Das seien genauso viele, wie die anderen drei Endmontagelinien jeweils ausstoßen.
Schnelligkeit sei nicht das vorrangige Ziel der neuen Fertigungslinie gewesen, sondern vielmehr der Einbau von Innovationen. Das sollen vor allem die Beschäftigten spüren. Derzeit sind rund 115 Mitarbeiter in den Hallen unterwegs. Wenn die Produktion auf vollen Touren läuft, sollen es 250 sein und damit ähnlich viele wie in den anderen Linien. Ihre Arbeit soll durch eine Reihe von Hilfsmitteln erleichtert werden.
Viele Innovationen zur Arbeitserleichterung
So gibt es an jeder Station Lastenaufzüge, die schwere Gegenstände auf Arbeitshöhe bringen. Es ist der Einsatz von Anzügen geplant, die die Bewegungen des Menschen so verstärken, dass er nur noch ein Zehntel seiner Muskelkraft einsetzen muss. Ähnliches leisten auch zupackende Handschuhe, mit denen beispielsweise Zangendrehbewegungen leichter werden. Bei Überkopfbohrmaschinen wurde das Gewicht bereits um etwa die Hälfte gesenkt.
Der Abbau von Beschlägen in luftiger Höhe kann statt vom wackeligen Steiger sitzend auf ausziehbaren Schubladen erfolgen. Ein neues Gerät hilft beim Anbau des Hauptfahrwerks. Statt zu dritt kann der Arbeitsschritt von einem Mitarbeiter allein erfolgen. Zudem ist das Mitschleppen von Werkzeugkisten vorbei. Jeder Monteur meldet sich mit seinem Ausweis am Werkzeugschrank an und entnimmt Zange und Co. Gibt er sie nicht zurück, schlägt das System Alarm. Das Führen von Papierlisten ist vorbei und die Sicherheit des Fliegens wird erhöht – vergessene Werkzeuge an Bord soll es nicht mehr geben.
Luise und Renate müssen Tausende Löcher bohren
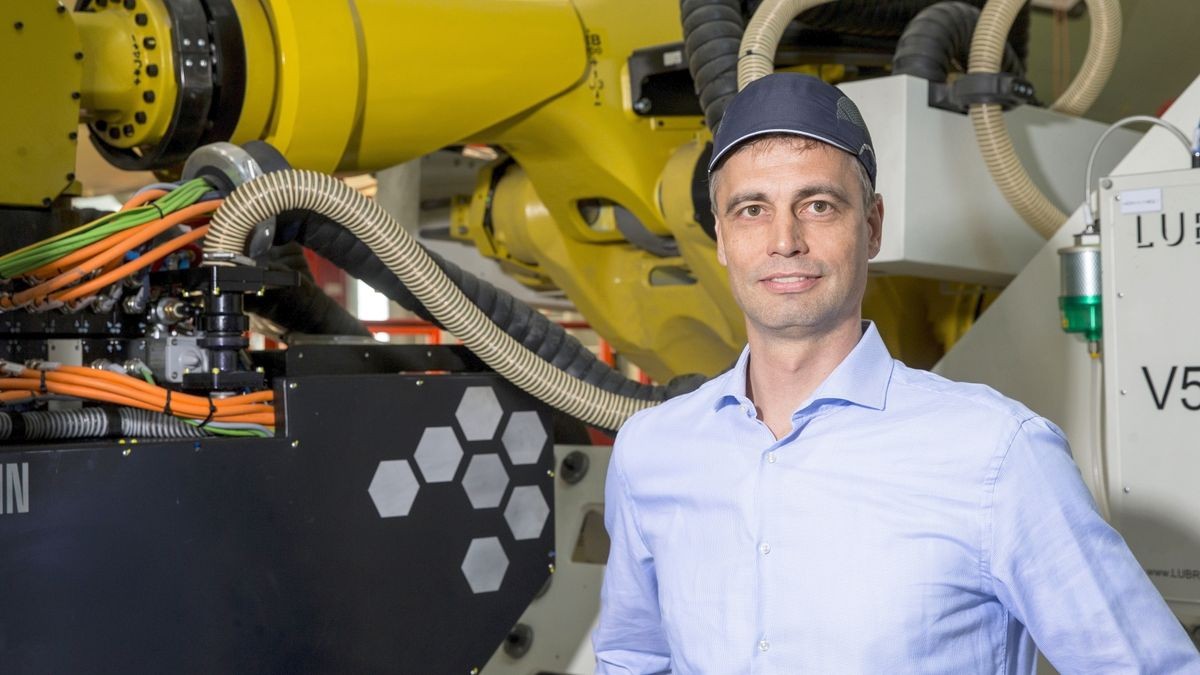
An der Station 42/43 steht beim Abendblatt-Besuch die Maschine mit der Seriennummer 8288. Sie wird links von Luise und rechts von Renate eingerahmt. Am nächsten Tag sollen die Roboter-Schwestern ihre Arbeit machen, nachdem die beiden Rumpfabschnitte manuell zusammengeführt wurden. 2800 Löcher müssen gebohrt werden, etwa 80 Prozent schaffen Luise und Renate. 15 Stunden brauchen sie dafür. „Der Roboter ist nicht schneller als die Monteure, aber viel präziser“, sagt Rocksien. Sieben Meter hoch lässt sich der Roboterkopf ausfahren, die Löcher werden mit einer Präzision von 0,2 Millimeter gebohrt.
Weil der Roboter an bestimmte Stellen allerdings nicht herankommt, müssen die Monteure die restlichen Löcher machen. Doch während der Roboter bohrt, können sie andere Arbeiten erledigen. So werden bestimmte Arbeiten in der Endlinie vorgezogen. Im Gegensatz zu früher ist das Seitenleitwerk der Maschine an dieser Station nun schon montiert. „Langfristig ist das Ziel, eine Station herauszunehmen, um die Produktionszeit weiter zu verkürzen“, sagt Siebels.
Auf der anderen Hallenseite steht die Seriennummer 7820. Sie kam im Juli 2017 in die Halle, ist nun fertig montiert und kommt in die Lackierhalle. In drei Wochen soll die erste Maschine aus der vierten Montagelinie an die Fluglinie China Southern ausgeliefert werden. Für Rocksien ein wichtiger Schritt: „Damit haben wir gezeigt, dass die neue Endmontagelinie funktioniert – und wir Flugzeuge so bauen können.“