Gelsenkirchen. Bei Thyssenkrupp Electrical Steel in Gelsenkirchen dominiert trotz des Ukraine-Kriegs der Optimismus. Das Werk ist aber auf Erdgas angewiesen.
In den weitläufigen Werkshallen von Thyssenkrupp Electrical Steel im Gelsenkirchener Stadtteil Schalke stapeln sich Coils mit aufgewickelten Stahlbändern. Bis zu 22 Tonnen schwer ist ein Exemplar. Züge transportieren den Werkstoff vom Hochofen-Standort Duisburg zum benachbarten Thyssenkrupp-Areal. „Wenn ein Coil aus Duisburg bei uns in Gelsenkirchen ankommt, hat es meist eine Länge von 1100 Metern“, erzählt Werksleiter Dirk Stevens. „Nachdem wir das Material bearbeitet haben, sind es bis zu 12.000 Meter.“
Thyssenkrupp Electrical Steel stellt ein Produkt her, das Georgios Giovanakis, der Geschäftsführer der Konzerneinheit, als „Basiswerkstoff für die Energiewende“ bezeichnet: Elektroband, das benötigt wird, wenn neue Trafos für Stromnetze oder Elektroauto-Ladesäulen gebaut werden. „Die Potenziale sind groß“, sagt Giovanakis. Auch Motoren für Elektroautos seien ein neues Anwendungsgebiet. „Wir haben es hier mit einem Technologiegeschäft zu tun. Das ist etwas anderes als Massenstahl mit einer Millionen-Tonnen-Jahresproduktion. Wir stellen rund 200.000 Tonnen jährlich her, in einem sehr aufwändigen Prozess.“
Rund 1750 Beschäftigte arbeiten bei Thyssenkrupp Electrical Steel, davon etwa 660 am Stammsitz in Gelsenkirchen. Jeweils etwas weniger als 600 Mitarbeitende sind in Werken in Frankreich und Indien tätig. In Gelsenkirchen-Schalke wird rund um die Uhr in einem Fünf-Schicht-Betrieb gearbeitet. „Derzeit sind unsere Anlagen voll ausgelastet“, berichtet Standortchef Stevens. Es ist ein langer Weg durch einen komplexen Maschinenpark, bis das Material an die Kunden geliefert wird. „Das Material durchläuft verschiedene Thermoprozesse unter Schutzgasatmosphäre und Reaktionsgasen, wird gereinigt, von 2,3 Millimeter auf 0,23 Millimeter gewalzt und chemisch bearbeitet, etwa mit Stoffen wie Salzsäure, Magnesiumoxyd und Phosphorsäure“, erklärt Stevens. Sieben Tage lang wird auf bis zu 1200 Grad erwärmt. Es ist ein energieintensives Geschäft.
„Ende 2019 war unser Standort noch stark gefährdet“, erzählt Geschäftsführer Giovanakis. „Das haben wir erfolgreich gedreht. Jetzt sind die Perspektiven gut.“ Eine wesentliche Ursache für die Trendwende seien
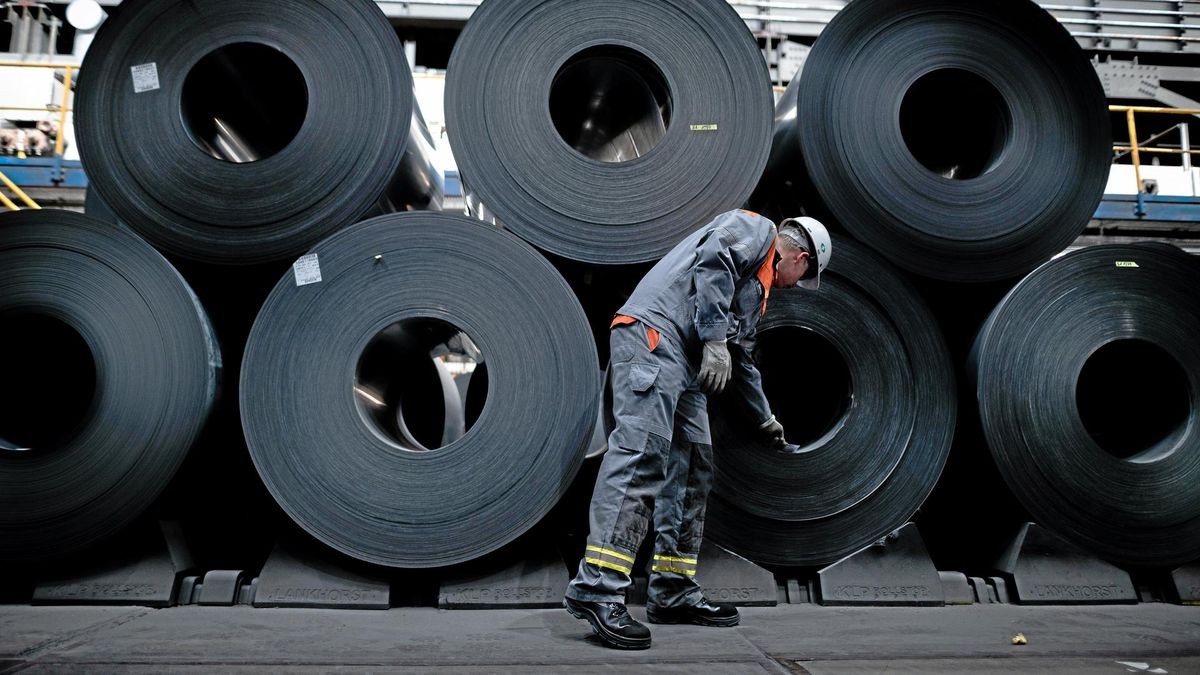
verbesserte Produkte. „Wir können nun qualitativ hochwertiges Elektroband anbieten: Top-Grades. Dieses Material wird stark nachgefragt, insbesondere bei Trafo-Herstellern“, sagt der Thyssenkrupp-Manager.
Ein Trafo habe üblicherweise eine Lebensdauer von 40 oder 50 Jahren. „Wenn er effizient ist, zahlt sich das über eine lange Strecke aus – ökonomisch und ökologisch“, betont Giovanakis. Bei jedem Trafo gebe es Wattverluste. „Wir arbeiten kontinuierlich daran, die Wattverluste noch weiter zu reduzieren.“ Je effizienter die Produkte seien, desto mehr ließen sich Emissionen des Klimagases CO2 verringern. Durch hochwertige Materialien könnten Trafos auch kleiner und leiser werden, erklärt der Thyssenkrupp-Manager. „Das spielt gerade in dicht besiedelten Gebieten eine wichtige Rolle.“
„Wir sind ein wesentlicher Teil der Elektrifizierung“
Zu den großen Trafoherstellern gehören Konzerne wie Siemens, Hitachi und General Electric. Die Wettbewerber von Thyssenkrupp Electrical Steel kommen insbesondere aus China, Japan und Korea. Das Werk im Stadtteil Schalke hat eine lange Tradition. Schon seit dem Jahr 1866 gibt es an dem Standort ein Stahlwerk. In Gelsenkirchen ist Thyssenkrupp Electrical Steel einer der größten privaten Arbeitgeber.
„Drei Millionen Tonnen Elektroband aus unserem Marktsegment werden weltweit hergestellt“, berichtet Giovanakis. Der Marktanteil von Thyssenkrupp Electrical Steel liege weltweit bei acht Prozent, in Europa ist er deutlich höher. „Wir sind ein wesentlicher Teil der Elektrifizierung“, sagt Giovanakis selbstbewusst. „Der Strombedarf wird sich weiter drastisch erhöhen.“ Die Auslastung der Werke sei gut. „Alles, was wir in Gelsenkirchen produzieren, wird uns auch abgenommen. Wir blicken positiv in die Zukunft.“
Die Geschichte der Einheit Electrical Steel passt zur Gesamtstrategie von Deutschlands größtem Stahlkonzern, die darauf abzielt, verstärkt Produkte für den Kampf gegen den Klimawandel herzustellen.
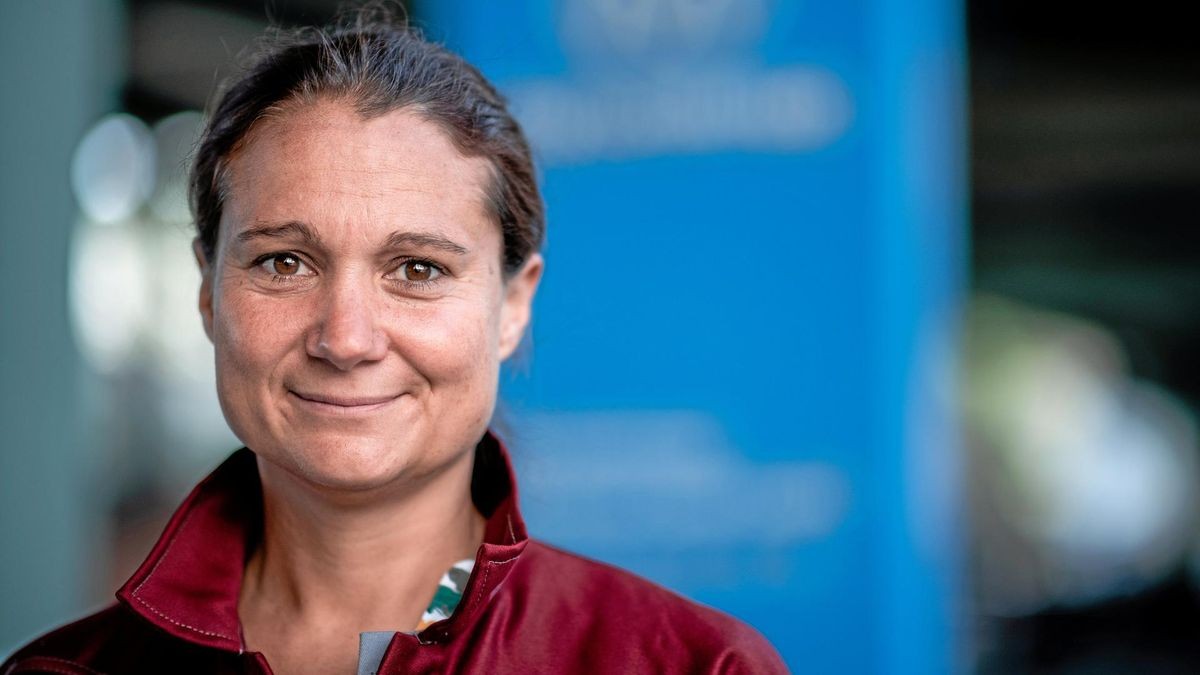
„Mit Electrical Steel können wir die wachsende Nachfrage nach grünen Materialien bedienen“, sagt Konzernmanagerin Marie Jaroni, die den Umbau voranbringen soll. „Daher spielt das Werk Gelsenkirchen in unseren Plänen zur Dekarbonisierung des Konzerns auch eine wichtige Rolle.“
Sichere Versorgung mit Erdgas wichtig für Standort Gelsenkirchen
Auch die Standorte von Thyssenkrupp Electrical Steel im französischen Isbergues und im indischen Nashik entwickeln sich gut, wie Geschäftsführer Giovanakis berichtet. „Wir beliefern unseren Standort in Indien auch aus Gelsenkirchen mit Material zur Weiterverarbeitung. Teilweise kommt das qualitativ hochwertige Elektroband aus Indien dann auch wieder auf den europäischen Markt, um den europäischen Bedarf zu decken.“
Aufmerksam verfolgt das Management, wie sich der Krieg von Russland gegen die Ukraine auf Europas Industrie auswirkt. Insbesondere ein Gas-Lieferstopp könnte negative Folgen für den Standort Gelsenkirchen haben. „Natürlich bereitet auch uns der Krieg in der Ukraine Sorgen – vor allem menschlich, aber auch für unsere Gesellschaft“, sagt Giovanakis. „Die großen Trends Dekarbonisierung und Elektrifizierung bleiben aber. Wenn wir das Erdgas aus Russland ersetzen wollen, müssen wir die Wirtschaft weiter elektrifizieren.“ Die Öfen im Gelsenkirchener Werk betreibt Thyssenkrupp mit Erdgas. „Daher sind wir auf eine sichere Versorgung angewiesen“, sagt Standortchef Stevens. „Die Öfen dürfen niemals aus sein. Sonst drohen Schäden an unseren Anlagen.“