Gelsenkirchen-Schalke-Nord. . In den Ausbau der Kapazitäten und Modernisierung der Öfen investiert Trimet in Gelsenkirchen. Produziert wird Sekundäraluminium aus Aluschrott.
Sekundäraluminium aus Aluminiumschrott produziert Trimet in Gelsenkirchen.1993, acht Jahre nach der Gründung des Unternehmens, erwarb die Aktiengesellschaft das Gelsenkirchener Aluminium-Recyclingwerk. Es wurde zum wichtigen Baustein des international aufgestellten Konzerns mit mittlerweile (inklusive Automotive-Sparte) rund 3100 Beschäftigten an acht Produktionsstandorten.
Millionste Tonne Aluminium Mitte 2018 produziert
Das Umschmelzwerk am Stadthafen hat Mitte 2018 seine millionste Tonne Flüssigaluminium produziert. Die Rekordcharge ging damals per Lkw an die Fordwerke in Köln. Aus der Automobil-, Elektro- und Maschinenbauindustrie kommen auch die Recyclingmengen, die Trimet wiederum in Schalke-Nord von Kunden aus der Region verarbeitet. Mit einem neuen Drehtrommelofen werden jetzt Effizienz und Energieeinsatz im Werk optimiert. Der neue Ofen hat 40 Tonnen Fassungsvermögen und ersetzt zwei der drei bisherigen Anlagen mit jeweils 15 bis 25 Tonnen Fassungsvermögen.
Freitag wurde die neue Anlage in Betrieb genommen.Angaben zur Gesamtkapazität und Investitionssumme macht Trimet nicht.
90 Prozent des Aluminiums werden recycelt
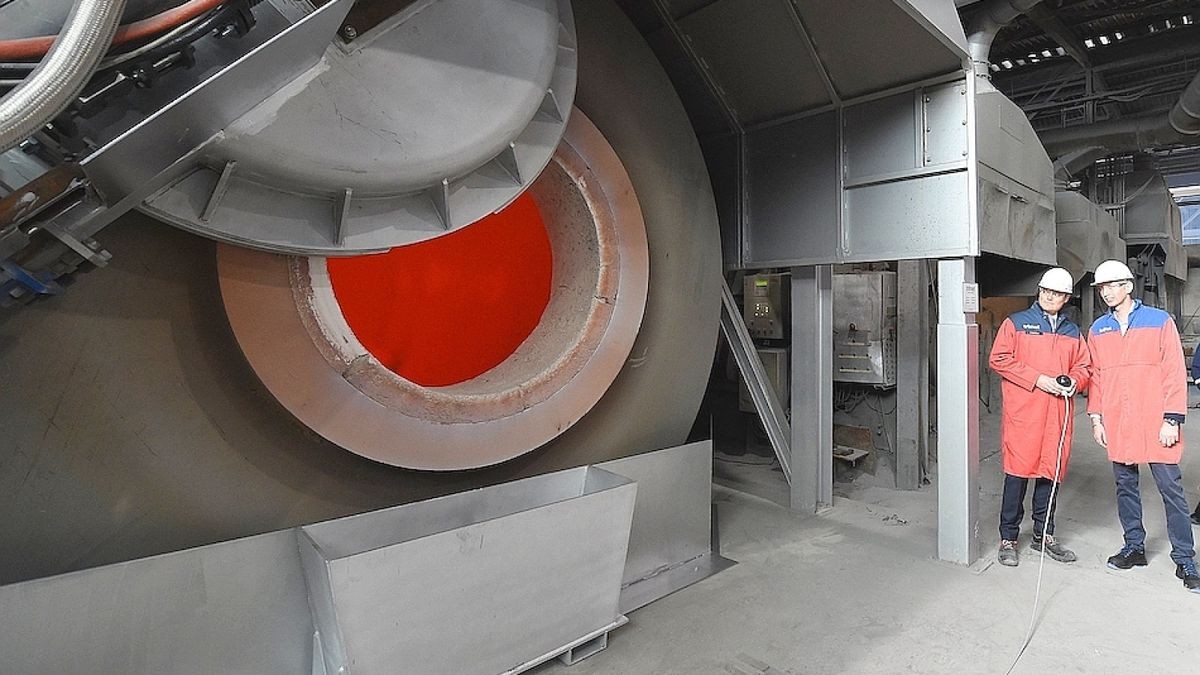
Rund 90 Prozent des im Umlauf befindlichen Aluminiums werden recycelt, die absolute Menge des wiederverwerteten Leichtmetalls nimmt angesichts des steigenden Bedarfs immer weiter zu. Deshalb ist es für uns folgerichtig, dass wir konsequent in den Ausbau unserer Kapazitäten und die Modernisierung unserer Anlagen investieren“, sagte Philipp Schlüter, Vorsitzender des Vorstands der Trimet Aluminium SE.
Der neue Trommelofen erhöhe die Umschmelzkapazitäten des Gelsenkirchener Trimet Standortes deutlich, so die Werkleitung. Gleichzeitig wurden auch die Infrastruktur und die Abgasführung des Umschmelzwerks modernisiert und erweitert – und zwar im laufenden Betrieb. Die 100-köpfige Belegschaft habe sich „mit viel Herzblut und großer Flexibilität an den Planungen und dem Umbau beteiligt“, nur so habe die Produktion in der Umbauphase „nahezu reibungslos“ weiterlaufen können, betonte Strandortleiter Jens Meinecke.
Ofen verfügt über eine intelligente Chargiertechnik
Der neue Ofen verfügt über ein sich selbst steuerndes Brennersystem, das nicht nur den Energieverbrauch deutlich senke, sondern auch den Anteil des rückgewonnenen Metalls erhöhe. Zudem verfügt der Ofen über eine intelligente Chargiertechnik, die eine schnellere Befüllung ermöglicht und je Schmelzvorgang größere Materialmengen aufbereiten kann.
Produziert werden Standardlegierungen in Drehtrommel- und Herd-Schmelzöfen. Im Werk gibt es fünf verschiedene Gießstationen für Flüssigaluminium und zwei Gießbänder für sogenannte Masseln (Barren) – allein die haben eine Leistung von fünf Tonnen pro Stunde.