Duisburg. Der US-Chemiekonzern Westlake produziert in Duisburg mitten in einem Wohngebiet. Kaum jemand weiß, was dort hergestellt wird. Ein Ortsbesuch.
Wenn die Mitarbeiter der Westlake Expoxy GmbH etwas Besonderes zu feiern haben, gehen sie gerne in das benachbarte Restaurant Haus Laacks. Da treffen sie auf Anwohner ihrer Chemiefabrik mitten im Wohnviertel. „Wir stellen immer wieder fest, dass viele gar nicht wissen, was bei uns passiert“, sagt Werksleiter Frank Gladbach.
Das hat natürlich etwas Gutes. Offensichtlich brachte bisher kein Störfall das Chemiewerk negativ in die Schlagzeilen. Werk und Anwohner leben seit Jahrzehnten auf engem Raum friedlich vor sich hin. Obwohl die Wohnhäuser mit den Jahren immer dichter herangerückt sind. Aus heutiger Sicht würde so eine Fabrik mitten in der Stadt sicher nicht mehr genehmigt. Entsprechend hoch sind die Sicherheitsauflagen.
Tonnenweise Werkstoffe made in Duisburg, die aus dem Alltag nicht mehr wegzudenken sind
Auf der einen Seite des Werkzahns produzieren die Westlake-Mitarbeiter aus fast 20 Nationen tonnenweise Werkstoffe, die aus unserem Alltag nicht mehr wegzudenken sind. Auf der anderen Seite des Zauns glauben viele, an der Varziner Straße mitten in Obermeiderich würden noch immer wie früher Kunststoffe aus dem Teerabfall der Koksproduktion hergestellt.
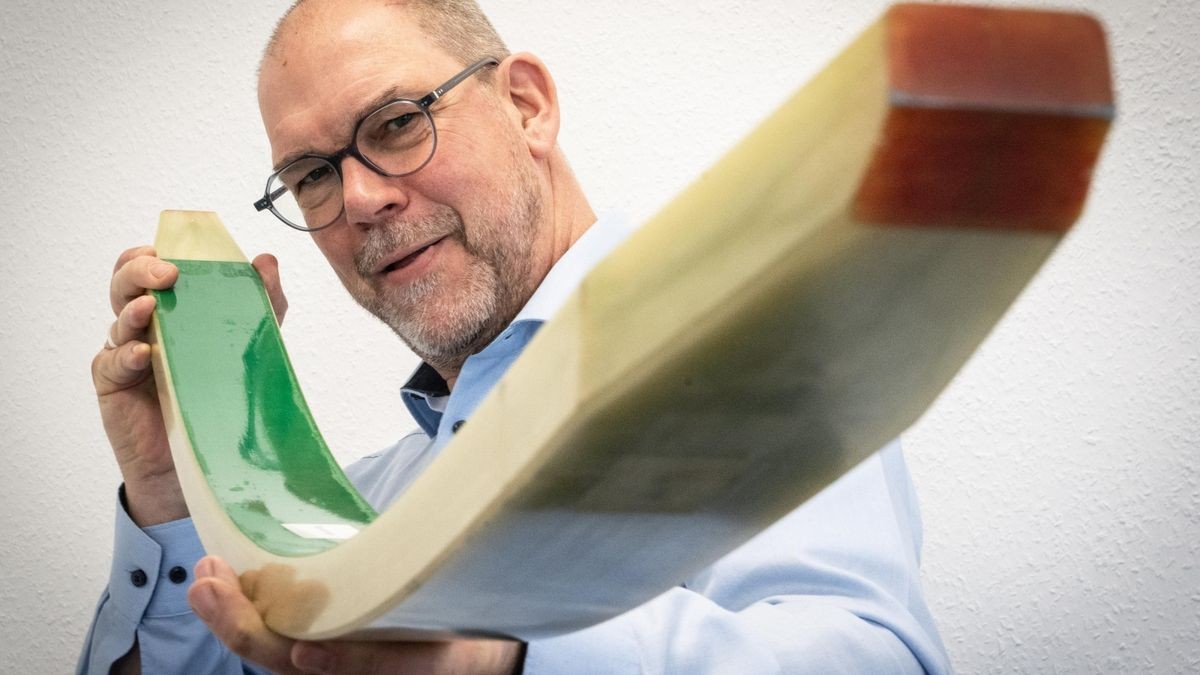
Das ist kein Wunder. In dem Chemiewerk hat sich in den vergangenen knapp 120 Jahren zu viel gewandelt, um auf dem Laufenden zu bleiben. Dabei haben sich die Firmenlogos am Eingang mehrfach geändert, zuletzt vor zwei Jahren von Hexion zu Westlake. Daneben stehen noch die Logos von Rain und dem Dienstleister Infratec. Alles Namen, die den wenigsten was sagen. Was also steckt dahinter?
Telefone aus Bakelit: Der erste Kunststoff wurde in Meiderich hergestellt
Zuerst der Rückblick: Die Gesellschaft für Teerverwertung eröffnete das Werk 1905, um aus den Rückständen der Koksproduktion chemische Grundstoffe herzustellen. Denn bei der Produktion von Koks, der für die Stahlherstellung gebraucht wird, fällt Teer an. Also ein Nebenprodukt, das gewinnbringend weiterverwendet werden kann. So entstand auch der erste Kunststoff überhaupt: Bakelit, bekannt von schwarzen Telefonen mit Wählscheibe, Dreh-Lichtschaltern oder Haarföns. Er wurde ab den 50er Jahren in Meiderich produziert.
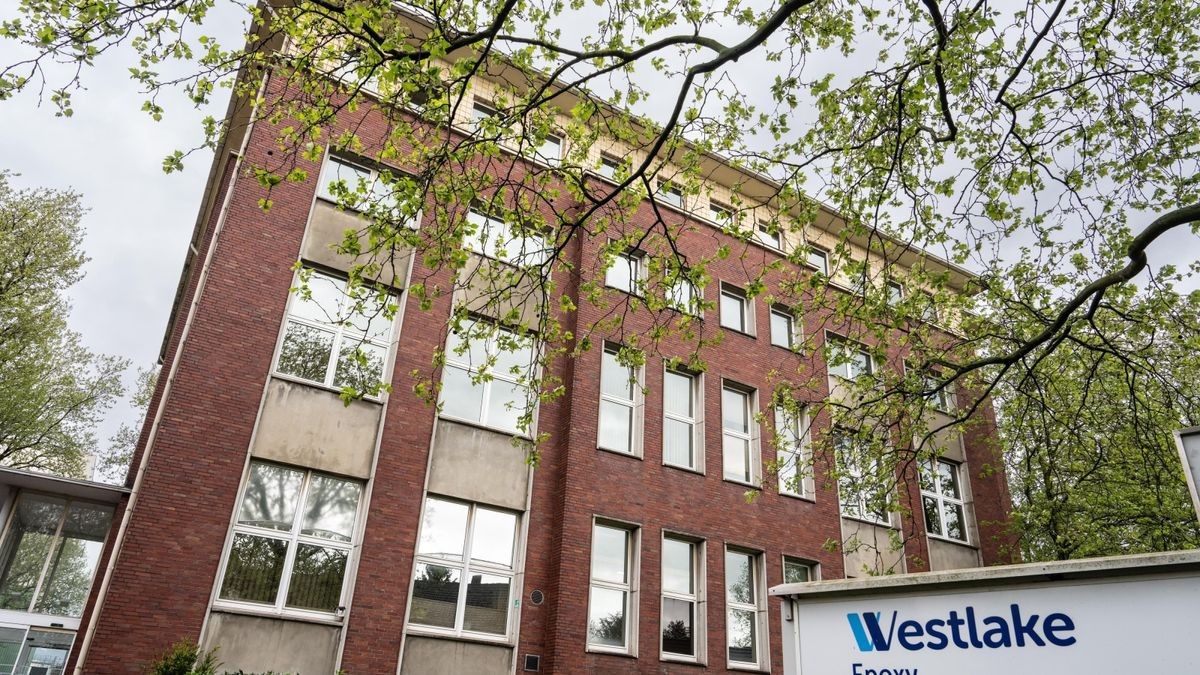
Die Gesellschaft für Teerverwertung schloss sich 1964 mit den Berliner Rütgerswerken zusammen. Rütgers ging in den 70er Jahren in der Ruhrkohle AG auf und wurde 2008 von Evonik an einen Investor verkauft. Deswegen gibt es heute drei Firmen im Meidericher Chemiewerk: eine Tochter der indischen Gruppe Rain mit 150 Mitarbeitern, die unter anderem Harze auf Basis von Kohlenwasserstoffen herstellt. Die Infratech GmbH mit 80 Mitarbeitern, die für die Infrastruktur sorgt. Und die deutsche Tochter des US-amerikanischen Chemiekonzerns Westlake aus Houston, die in Duisburg mit 300 Mitarbeitern hauptsächlich Epoxidharze produziert.
Epoxidharz für ellenlange Rotorblätter an Windkraftanlagen
Bei Epoxidharz handelt es sich um eine Spezialität. So werden in der Branche hochwertige und teure Kunststoffe genannt. „Wir können dem Harz jede Farbe geben und durch Beimischung des Härters den Zeitpunkt genau definieren, wann er hart wird“, erläutert Westlake-Manager Gladbach.
Einen größten Umsatzbringer hat der Duisburger Westlake-Standort nicht. Dafür werden zu viele verschiedene Produkte passgenau entwickelt und in Tankwagen oder auf Paletten an rund 1000 Kunden geliefert. Zum Beispiel ein Vorprodukt zur Herstellung von Lebensmittelverpackungen, die ohne den umstrittenen Stoff Bisphenol A auskommen. Oder Epoxid-Harz, aus dem bis zu 100 Meter lange Rotorblätter für Windkraftanlagen oder die Klappen der Handgepäck-Fächer in Airbus-Flugzeugen gegossen werden.
Blattfeder als Stoßdämpfer für den meistverkauften Pick-up der USA
Ein Produkt ist besonders anschaulich und steht deswegen im Büro des Werkleiters: eine Blattfeder für Lastwagen und schwere Autos, gegossen aus Harz und Carbon. Sie wiegt rund fünf Kilo und ist nur halb so schwer wie eine klassische Feder aus Stahl, soll aber genauso gut dämpfen. „Gewicht ist im Auto wie im Flugzeug besonders wichtig“, sagt Gladbach. Die Feder aus Meiderich ist im Pick-up F-150 von Ford verbaut – und damit in dem wohl meistverkauften Pick-up der USA.
- Die WAZ Duisburg informiert Sie auch hier: zum WhatsApp-Kanal +++ bei Instagram folgen +++ jetzt Duisburg-Newsletter ins E-Mail-Postfach schicken lassen +++ WAZ Duisburg bei Facebook abonnieren +++
Für einen großen Autobauer in Deutschland produzieren die Meidericher Harze zur Isolation der Spulen in Elektromotoren. Der Werkstoff darf nicht leiten und keine Risse bilden, wenn sich die Stromleiter bei hoher Geschwindigkeit drehen. „Das muss unser Harz aushalten, und zwar sehr lange“, sagt der 58-jährige Chemie-Ingenieur.
Elektroautos sind Wachstumsmarkt für das Duisburger Unternehmen
Elektroautos sind ohnehin ein Wachstumsmarkt für das Duisburger Unternehmen. Ein Risikofaktor stellen die Lithium-Batterien dar, die aus Gewichtsgründen auf dem Boden der Autos platziert sind. Die Insassen sitzen also darauf. Sollte eine Batterie in Brand geraten, wird es schnell gefährlich. „Wir haben einen Schutzschild entwickelt, der auf den Akkus montiert ist und den Insassen Zeit gibt, um das brennende Auto zu verlassen“, sagt Gladbach.
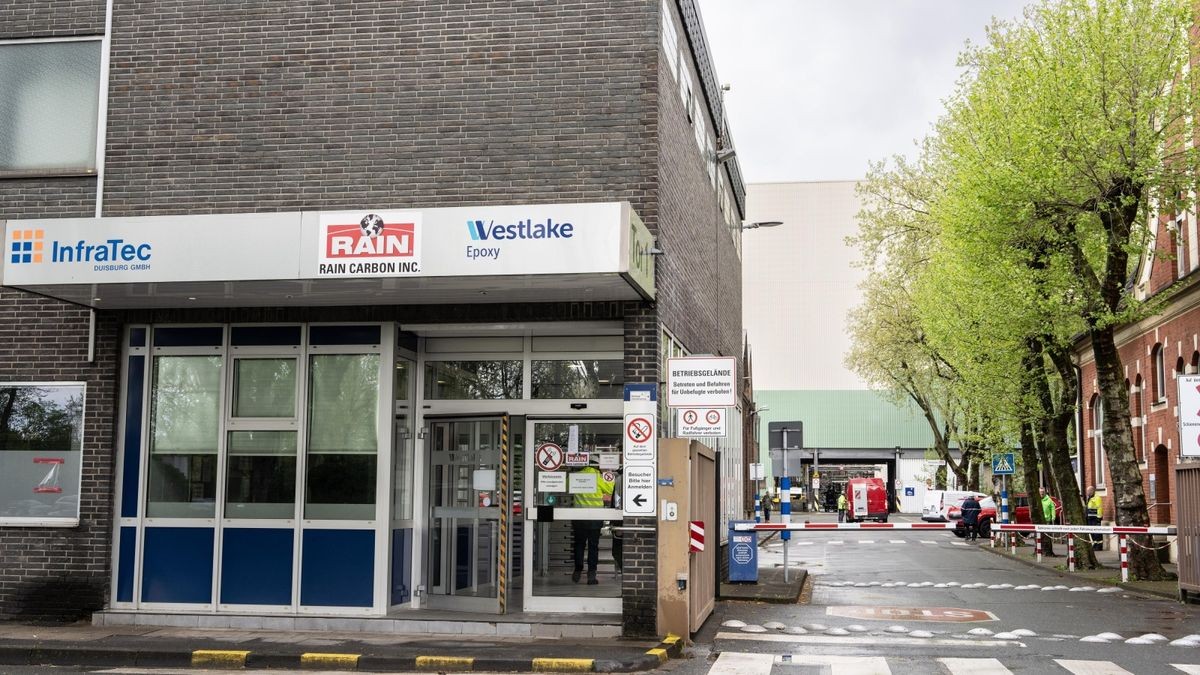
Insgesamt erwirtschaftet das Duisburger Werk, in dem noch einige Fassaden an die Kaiserzeit erinnern, einen „deutlichen dreistelligen Millionenbetrag“, so Gladbach. Wirtschaftlicher Druck entstehe vor allem durch hohe Energiekosten, die noch immer bis zu dreimal höher seien als vor Beginn des Ukraine-Kriegs.
„Zudem brauchen wir hoch qualifiziertes Personal und müssen als Chemiefabrik hohe Sicherheits- und Umweltstandards erfüllen. Das alles kostet natürlich“, sagt der Manager. Gegensteuern will er vor allem durch zwei Maßnahmen: die Organisation schlagkräftiger umbauen und Umsatzvolumen auf den Weltmärkten zurückgewinnen.