Bochum. Derzeit produzieren noch mehrere Werke von Thyssenkrupp in Bochum. Doch die Vorstandspläne sehen eine deutliche Reduzierung vor.
Die jetzt vom Thyssenkrupp-Stahl-Vorstand initiierte Debatte über die künftige Entwicklung des Standorts Bochum rührt an der Substanz der Bochumer Stahlindustrie und droht einen Dominoeffekt zu beschleunigen, der seit Jahren die Bochumer Anlagen aushöhlt und die Mitarbeiterzahl kontinuierlich schrumpfen lässt. In etwa fünf Jahren könnten nur das Kaltwalzwerk und die Feuerverzinkung mit dem charakteristischen Turm übrig bleiben, befürchten Kenner.
Doch um die Zusammenhänge besser zu verstehen, muss erklärt werden, was der Stahlkonzern derzeit noch in Bochum produziert und wie die Zusammenhänge innerhalb des Konzerns sind. Das Unternehmen selbst stellt dazu öffentlich Informationen bereit, doch die Bochumer Besonderheiten kennen langjährige Mitarbeiter, die mit ihren Detailkenntnisse wichtige Hintergrundzahlen liefern.
Für Hüttenwerk in Brasilien wurde kräftig investiert
Zuletzt stand das Bochumer Werk in Höntrop 1997 im Zusammenhang mit dem Zusammenschluss von Krupp und Hoesch massiv auf der Kippe. Danach wurde das Werk im Zusammenhang mit dem Aufbau des Hüttenwerks in Brasilien (2005 bis 2009) mit gewaltigen Investitionen auf eine theoretische Walzkapazität von 380.000 Tonnen im Monat hochgerüstet.
Doch diese Tonnage wurde nie erreicht. In guten Jahren wurden in dem Warmbandwerk, das bis zu knapp 1000 Mitarbeiter beschäftigte, rund 300.000 Stahl im Monat zu Blechen verschiedener Stärke, Breite und Qualität gewalzt. Diese Bleche werden zu gewaltigen Rollen, sogenannten Coils, aufgerollt und danach entweder weiter verarbeitet, etwa im Kaltwalzwerk, oder direkt an die Kunden, zum Beispiel in der Automobilindustrie, verschickt.
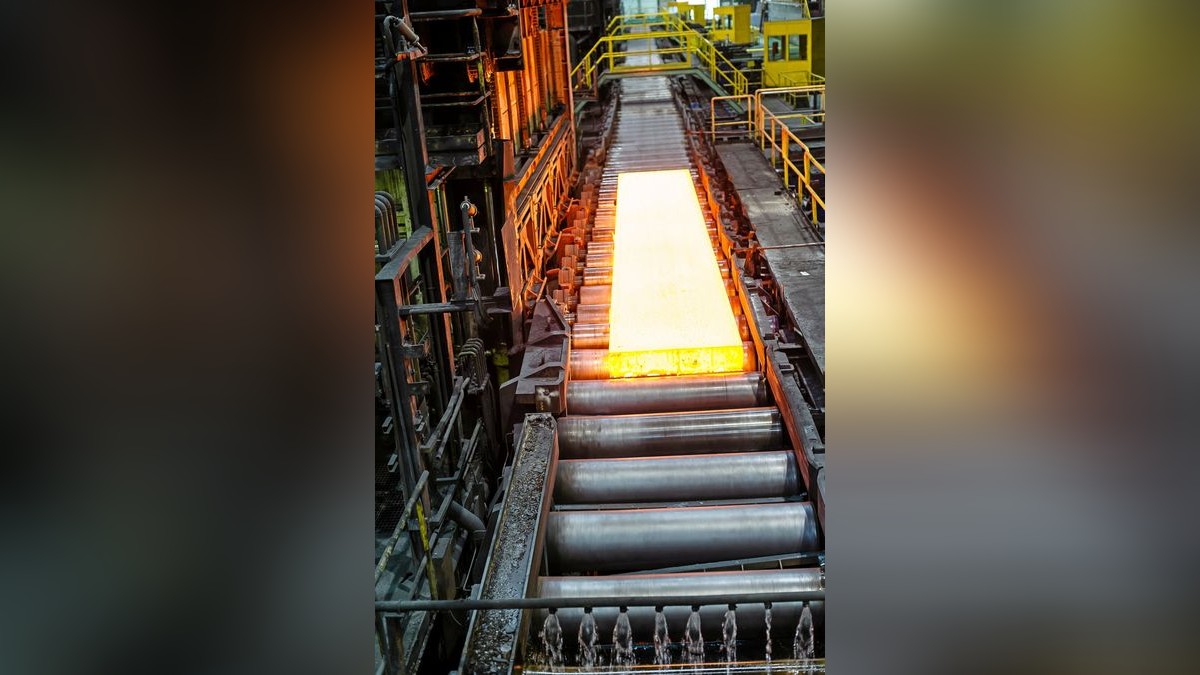
Das Warmbandwerk, das viele Jahre lang auch Edelstahl aus dem Nirosta-Walzwerk walzte, hatte bis zur Schließung des Werks durch den neuen Besitzer, das finnische Unternehmen Outokumpu, oft eine gute Auslastung. Als die Finnen 2015 das Werk schlossen, fehlte dieses Material.
Fachleute wissen genau, dass diese Bochumer Anlage im Konzert der insgesamt drei Warmbandwerke und der Gießwalzanlage von Thyssenkrupp Stahl die flexibelste ist. Nach Informationen der WAZ bescheinigt diese hohe Leistungsfähigkeit auch ein von der IG Metall eigentlich im Rahmen der geplanten Fusion mit Tata Steel beauftragtes Gutachten. Das noch nicht veröffentlichte Dokument benennt aber auch die beiden wesentlichen Nachteile Bochums: Die insgesamt vier Öfen, die zur Erwärmung der Stahlbrammen auf Schmiedetemperatur nötig sind, werden mit teurem Erdgas beheizt. Bei den Duisburger Anlagen kommt Koksgas aus der eigenen Kokerei oder Mischgas zu Einsatz. Nachteilig wirkt sich auch die Brammen-Logistik aus. Die Kolosse müssen per Bahn aus Duisburg transportiert werden. Oft, so heißt es, fehlt es an Eisenbahnwaggons.
Brammen mit einem Gewicht von bis zu 30 Tonnen
Die Brammen, die pro Stück ein Gewicht von bis zu 30 Tonnen auf die Waage bringen, kommen aus zwei Hüttenwerken. Eine Hälfte kommt aus dem Hüttenwerk Krupp Mannesmann (HKM) in Duisburg-Hüttenheim, die andere Hälfte aus Duisburg-Beeckerwerth. Eigentlich, so ein Insider, sollen in Bochum im Schnitt nur 150.000 Tonnen im Monat verarbeitet werden. Doch die wirklichen Zahlen sprechen eine andere Sprache: Der Schnitt liegt deutlich darüber. So wurden im November 170.000 Tonnen und im Oktober sogar 190.000 Stahl gewalzt – und das mit einer bereits heute auf weniger als 600 Leute ausgedünnten Mannschaft. Allein dies spreche für die Bedeutung des Walzwerks.
Sollte es bis etwa 2024 auslaufen, wie es die Folien des Vorstand deutlich gezeigt haben, glaubt kaum jemand an eine Zukunft der verbleibenden Reste, wie Kaltwalzwerk oder Feuerverzinkung. Das Bochumer Werk war auf den Folien schlicht durchgestrichen dargestellt, wie übrigens auch der Standort der Elektroblech-Fertigung an der Castroper Straße.

Auf dem Gelände an der Castroper Straße, dem ehemaligen Sitz der einst wesentlich größeren Stahlwerke Bochum, befindet sich das Elektrobandwerk (früher EBG), das mittlerweile unter dem Dach von Thyssenkrupp Stahl sogenannte nicht kornorientierte Werkstoffe walzt. Thyssenkrupp ist mit seinen unterschiedlichen Spezialwerkstoffen einer der globalen Marktführer. Das speziell beschichtete und behandelte Stahlband wird bei Stromgeneratoren, etwa in Kraftwerken, oder in Elektromotoren eingesetzt.
Thyssenkrupp wirbt damit, dass es „unmittelbar zu Ressourcenschonung und Umweltschutz im Bereich Energietechnik“ beiträgt. Doch an die Zukunft dieses Werkes mit seinen rund 500 Mitarbeitern glaubt der Konzern offenbar nicht mehr. Jedenfalls, wenn es nach den bekanntgewordenen Plänen des Vorstands geht.