Hamminkeln. Die Unternehmensgruppe Max Bögl hat an ihrem Fertigteile-Standort Hamminkeln 3,5 Millionen Euro investiert. So werden Ressourcen eingespart.
Ressourceneinsparung und Qualitätssicherung - in diesen Zeiten zwei bedeutende Elemente. Auch die Firma Max Bögl hat sich diese Ziele auf die Fahnen geschrieben. Vor diesem Hintergrund hat das Unternehmen jetzt am Standort Hamminkeln eine neue Mattenschweißanlage in Betrieb genommen, dazu die Hallen A und B mit einer neuen Fassade und einem neuen Dach versehen. Eine Investition in Höhe von satten 3,5 Millionen Euro, die aber gleichzeitig Personal und auch Material einsparen soll. Denn es gibt praktisch keinen Verschnitt mehr.
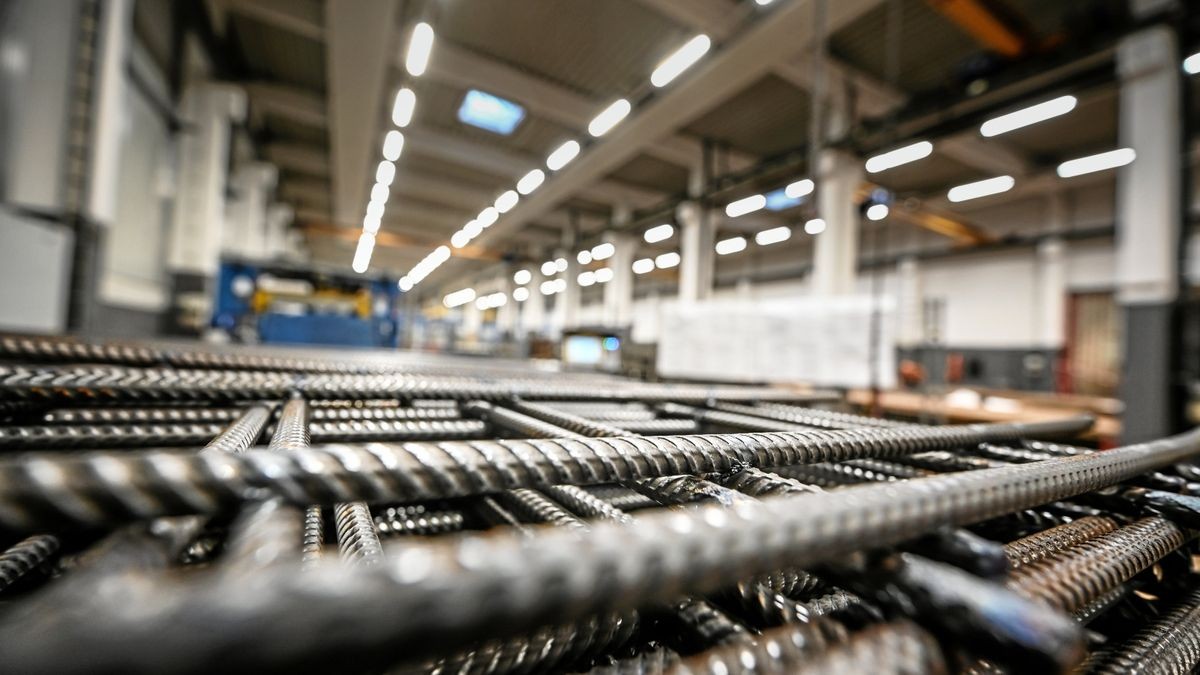
Vor versammelter Belegschaft wurde die neue Anlage, die am 2. Dezember in Produktion ging, jetzt auch offiziell eingeweiht. Dazu war auch Jens Bögl, Kaufmännischer Leiter und Geschäftsführer des Produktionsbereichs Fertigteile, an den Niederrhein gekommen: „Das ist eine der größten Investitionen am Standort Hamminkeln. Damit gehen wir einen neuen Weg der Herstellung von Bewehrungsstahl - wobei es auch wichtig ist, sich hier neu aufzustellen.“ Als Familienunternehmen zähle man auf den Standort Hamminkeln, wolle hier au künftig weiter investieren. „Wir wollen hier den Standort sichern.“
Eine frohe Kunde für die Belegschaft, aber auch für Bürgermeister Bernd Romanski, der sich beim Rundgang durch die Hallen auch an seine eigene Arbeit in jungen Jahren bei Hochtief erinnert fühlte. „Ich habe das nicht vergessen, habe den Geruch noch in der Nase.“ Der Verkauf des Firmengeländes an Bögl sei die richtige Entscheidung gewesen. Romanski wünschte Geschäftsführung und Mitarbeitern viel Glück für die Zukunft. Werkleiter David Heinze dankte den „engagierten Mitarbeitern“ für die Umsetzung der Maßnahme und den damit einhergehenden Hallenumbau. „Wir arbeiten jetzt auf höchstem Standard.“ Er freue sich auf die nächsten Herausforderungen.
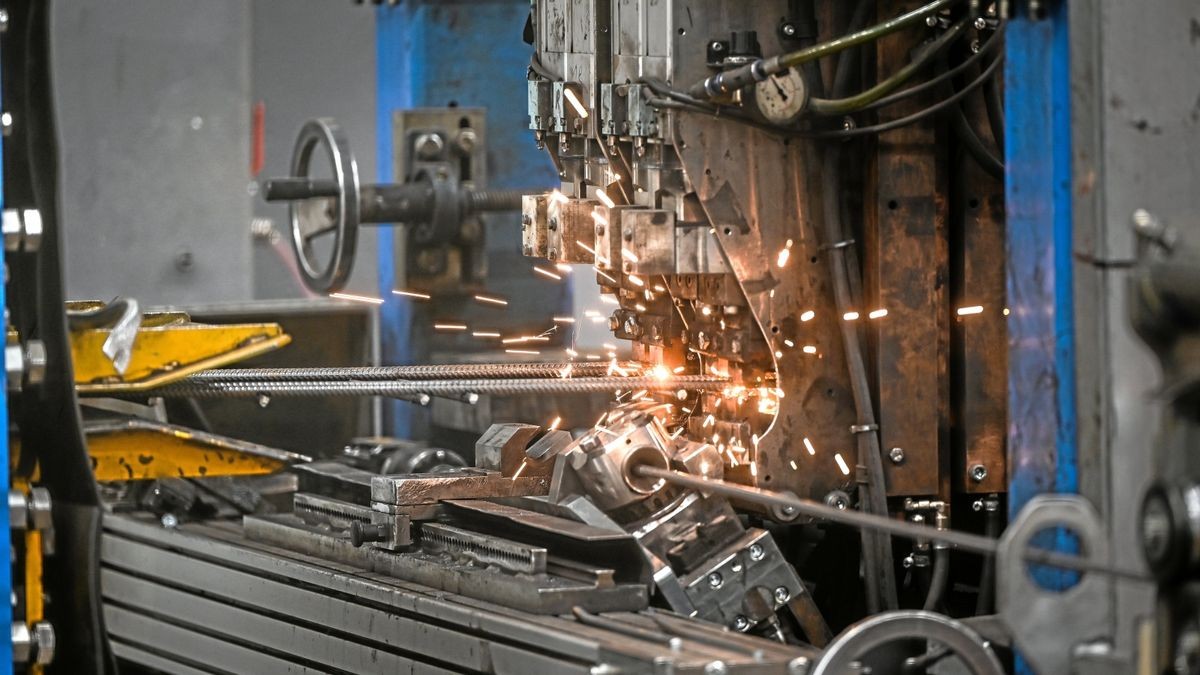
Beim Rundgang zuvor durch die Produktionshallen hatte der Werkleiter die neue Mattenschweißanlage, dazu die Fertigteil- und Tübbingproduktion und Bewehrungsherstellung vorgestellt. Bürgermeister Bernd Romanski, Hamminkelns Wirtschaftsförderin Nadine Jordan, der Kaufmännische Leiter NRW Oliver Santroch und Jens Bögl waren sichtlich beeindruckt. Denn die neue Mattenschweißanlage ersetzt die konstruktive Fertigung, die händischen Biegearbeiten in weiten Teilen, ist computergesteuert und kann verschiedene Größen von Listenmatten auf Länge genau und mit verschiedenen Abständen produzieren.
„Es ist viel weniger, allerdings auch anders ausgebildetes Personal nötig“, so David Heinze. „Die komplexe Anlage kann sehr viel.“ Etwa drei Minuten dauert die Produktion einer Matte, der Verschnitt sinkt von zuvor 15 Prozent auf fast Null. „Energie und Stahl sparen - das sorgt für Nachhaltigkeit“, lobte Bernd Romanski. Was im dritten Quartal durch die Installation einer Photovoltaik-Anlage auf dem Dach noch gefördert werden soll. 1,9 Millionen hat die Anlage an sich gekostet, der Umbau der Halle schlug mit weiteren 1,5 Millionen Euro zu Buche.
Auch die Tübbing-Produktion läuft derzeit auf Hochtouren, auf der Außenfläche türme sich rund 800 Steine für einen Stollenwasserkanal in Ibbenbüren. Ein wichtiger Bestandteil der Gesamt-Umsatzes von jährlich 45 Millionen Euro am Standort Hamminkeln.
Hintergrund
Die Mattenschweißanlage erstellt pro Tag im Zweischichtbetrieb etwa 10 Tonnen und im Jahresumsatz etwa 2.500 Tonnen Bewehrung her, Tendenz steigend. Die Spitzenleistung der Anlage liegt bei 400 m² pro Stunde. Die Leistung besteht aus passgenauen Listenmatten für die Herstellung von Wand- und Deckenplatten sowie auch in gebogener Form zur Herstellung von Stützen, Balken, Binder und Pi-Deckenplatten.