Hamminkeln. Die Firmengruppe Max Bögl hat einen wichtigen Produktionsstandort in Hamminkeln. Hier kümmern sich rund 175 Mitarbeiter um Betonfertigteile.
Der Filder-Bahntunnel in Stuttgart. Von der Firmengruppe Max Bögl gebaut. Oder das stylische Studentenwohnheim im dänischen Lyngby. Auch von Max Bögl gebaut. Die Modulbrücke bei Emmerich über die Autobahn 3. Klar, von Max Bögl gebaut. Nicht zu vergessen das neue Werk für einen amerikanischen Elektrofahrzeughersteller in Brandenburg, auch hier finden sich Beton-Bauteile der Firmengruppe. Irgendwo und irgendwann wird jeder mal einem Bau, einer Fassade des international tätigen Bauunternehmens Max Bögl begegnen. Als die Firma Hochtief Anfang 2005 das Gelände an der Industriestraße in Hamminkeln verließ, griff die Firmengruppe mit Hauptsitz im oberpfälzischen Neumarkt zu.
„Es war auch strategisch gesehen eine sehr gute Entscheidung, damals fehlte uns noch ein Standort im Westen, in der Region Niederrhein“, erinnert sich Oliver Santroch, kaufmännischer Leiter NRW. Und der Standort Hamminkeln – einer von inzwischen schon 31 bundesweit und 17 im Ausland – liegt infrastrukturell gesehen perfekt – mit der unmittelbaren Anbindung an die A3 und dem eigenen Gleisanschluss auf dem Firmengelände, zu dem die tonnenschweren Betonteile über ein Kransystem transportiert werden können.
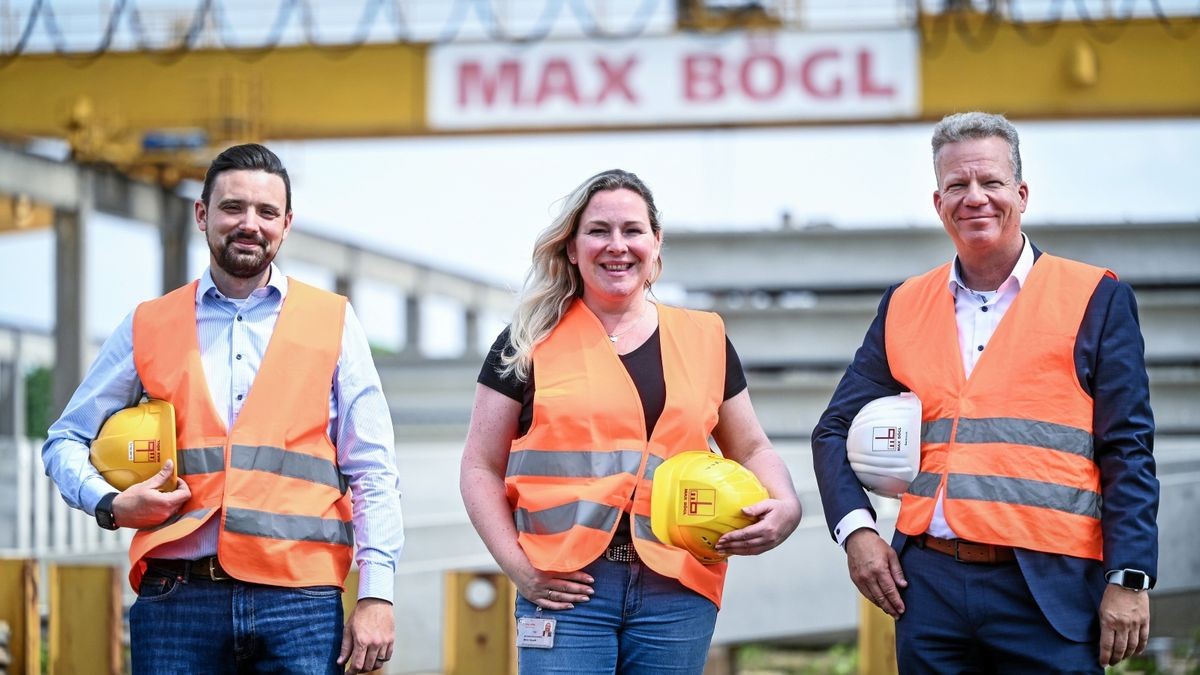
Derzeit rund 175 Mitarbeiter zählt der Produktionsstandort Hamminkeln, wo Betonfertigteile – beispielsweise Wandplatten für Fassaden; Stützen und Betonbinder für Hallen – entstehen. Ein Spezialgebiet in Hamminkeln ist die Fertigung des so genanten Tübbings – ein vorgefertigtes Betonsegment der Außenschale eines Tunnels. Mehrere Tübbing-Elemente bilden einen Ring, der Tunnel setzt sich aus mehreren Ringen zusammen.
Die Tübbinge werden im Tunnelbau von einer Vortriebsmaschine eingebaut. „Es ist ein kleineres Geschäftsfeld, da arbeiten wir projektbezogen“, berichtet David Heinze, Leiter des Fertigteilwerks. Zuletzt hat das Familienunternehmen größere Aufträge vor allem in den Beneluxstaaten, England und auch Hamburg umgesetzt. Dann sind die Max Bögl-Fertigteilwerke in Sengenthal, Linthe und Hamminkeln für die Herstellung der Tunnel-Tübbings im Geschäft.
Bis zu 80.000 Kubikmeter Beton im Jahr
Den Großteil der Arbeit in den vier Produktionshallen an der Industriestraße umfasst die Produktion von Fertigteilen aus Beton. „Das längste Segment, das wir bislang hier gebaut haben, hatte eine Spannweite von 45,5 Metern“, verrät Werkleiter David Heinze. In Hamminkeln werden bis zu 80.000 Kubikmeter Beton pro Jahr verbaut, hinzu kommen 8000 bis 10.000 Tonnen Stahl für den Beton. „Die Stahltonnage hat die Dimensionen des Eiffelturms“, schmunzelt Oliver Santroch, „und noch etwas mehr.“ Auch deshalb hat das Unternehmen 2009 eine eigene Schlosserei und Schreinerei gebaut – in der unter anderem Verschalungen gefertigt werden. Zuletzt kam eine vierte Halle hinzu. Und eine weitere Vergrößerung des Grundstückes ist durchaus noch möglich.
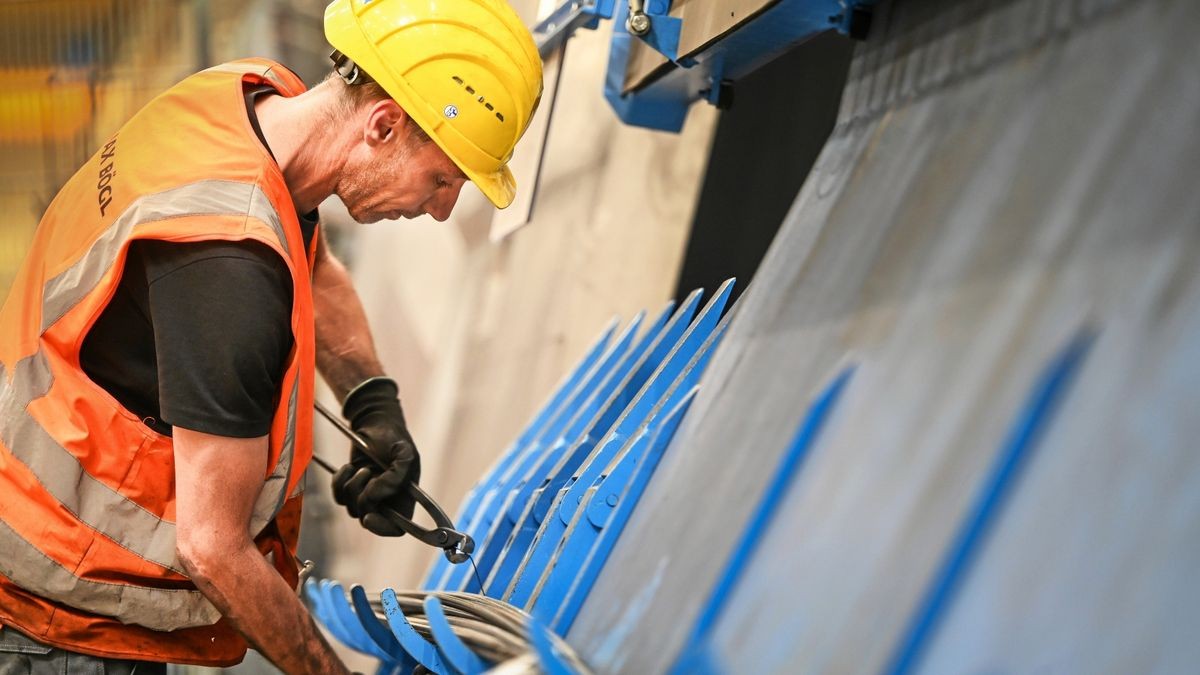
Noch in diesem Jahr wird eine Mattenschweißanlage mit einer Fläche von rund 500 Quadratmetern installiert, die die Fertigung von Bewehrungsstahl für den Beton automatisieren soll. Dadurch werden die Fertigungsprozesse beschleunigt. „Das trägt zur Automatisierung bei, ist aber auch eine Folge des Fachkräftemangels“, erklärt Werkleiter David Heinze. Gerne bildet das Unternehmen auch in Hamminkeln aus – zwischen 10 und 15 Ausbildungsplätze vom Schlosser bis zum Bauzeichner sind im Angebot.
Nachhaltigkeit und CO2-Reduzierung
Max Bögl möchte ein attraktiver Arbeitgeber in der Region bleiben, konzentriert sich deshalb auch künftig auf die Themen Arbeitssicherheit, Nachhaltigkeit und CO2-Reduzierung. Und zuletzt hat die Firmengruppe auch Spenden für die Opfer des Ukraine-Krieges gesammelt, einen Hilfskonvoi in die Region geschickt. Auch das macht einen Global Player aus.
In Halle 1 werden Betonplatten gegossen, auch hier ist der Lärmpegel erstaunlich niedrig. „Das war aber früher mit der Rütteltechnik noch anders, da hätten Sie hier kaum ein Wort verstanden“, weiß Oliver Santroch. Gerührt, nicht gerüttelt – ist heute die Devise beim selbstverdichtenden Beton. Von einer Zwangspause während der Pandemie blieb die Firmengruppe – auch der Standort Hamminkeln – indes verschont – auch weil die Hauptrohstoffe Sand und Kies aus der Region bezogen werden.
„Corona ist an der Bauwirtschaft abgeprallt“, umschreibt es Oliver Santroch. Gut möglich also, dass man bald wieder auf eine Halle, eine Fassade, ein Parkhaus oder einen Tunnel von Max Bögl trifft. Irgendwo und irgendwann bestimmt.