Hamburg. Fasern für die Zukunft: Dem Material werden spektakuläre Eigenschaften zugeschrieben. Wie realistisch der Einsatz in der Luftfahrt ist.
Spinnen sind der natürliche Feind vieler Flugobjekte. Schließlich sind deren Netze häufig für das tödliche Ende von Fliegen oder Mücken verantwortlich. Einmal gefangen in dem Fadengewirr, gibt es für die Tiere kein Entrinnen mehr. Das Netz ist für die Insekten kaum zerstörbar.
Was für Fliegen und Mücken ein Problem ist, könnte Airbus in Zukunft helfen. Spinnenseide ist dehnbarer als Stahl, zugfester als Nylon, kann dreimal so viel Energie aufnehmen wie Kevlar, ist flexibel und ein absolutes Leichtgewicht. „Wir schauen, ob Spinnenseide für den Flugzeugbau relevant sein kann“, sagt Detlev Konigorski. Der Astrophysiker ist bei dem MDAX-Konzern als Innovationsmanager für neue Technologien und Konzepte beschäftigt und hat seinen Arbeitsplatz im benachbarten Zentrum für Angewandte Luftfahrtforschung (ZAL) auf Finkenwerder.
Airbus kooperiert mit Start-up Amsilk aus Bayern
Dem organischen Material werden fast schon spektakuläre Eigenschaften zugeschrieben. Rein rechnerisch könnte ein Spinnennetz mit Fasern so dick wie ein Bleistift ein Großraumflugzeug vom Typ A350 fangen, heißt es. Mit einem Gewicht von rund 200 Tonnen. Konigorski wiegelt bei solchen Vergleichen ab. Rechnerisch sei das wohl richtig, aber der 54-Jährige sagt: „Wir müssen Marketing und Hype von den wahren Fakten trennen. Was das Material wirklich kann, kommt in unseren Tests heraus.“
Seit rund einem Jahr beschäftigen sich die Forscher im ZAL mit dem Material. Dabei wird mit Amsilk kooperiert. Das Biotechunternehmen aus der Nähe von München entwickelte das Know-how für die Produktion der künstlichen Spinnenseide. Der dafür zuständige DNA-Strang der Spinne wurde isoliert, reproduziert und in ein Bakterium eingesetzt, das die Spinnenseide herstellt. „Wir erschließen mit der Spinnenseide die organischen Materialien“, sagt Konigorski. Sie bestehe ausschließlich aus Proteinen, sei bio und vegan.
Bakterien produzieren bei 37 Grad Celsius die Spinnenseide
In vierstöckigen, 60.000 Liter fassenden Wassertanks wird das Material nun künstlich erzeugt. Restwärme aus Kraftwerken kann genutzt werden, um die Wassertemperatur auf 37 Grad Celsius zu erhöhen und so ideale Bedingungen für das Wachstum der Bakterien zu erhalten. Als Nahrung für die sich schnell vermehrenden Bakterien reichen Zucker, Salz und Spurenelemente. Am Ende stellen sie ein weißes Pulver her, das wie feines Mehl aussieht und zu Fäden oder Gelen umgewandelt wird.
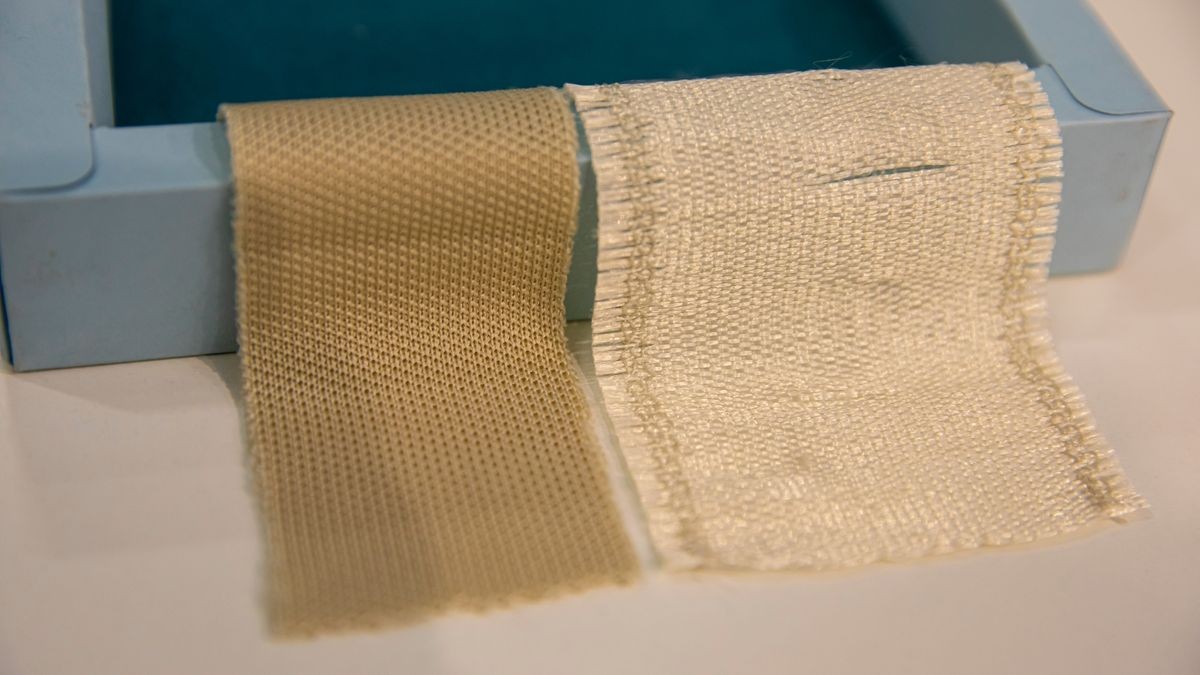
Konigorski holt eine blaue Pappschachtel hervor und öffnet sie. In ihr befinden sich zwei kleine Stofffetzen und ein Plastikteil – so sieht es zumindest aus. „Gemeinsam haben Amsilk und Airbus als erste Unternehmen weltweit Spinnenseide zu einem maschinell hergestelltem Gewebe verarbeitet“, sagt Konigorski und zeigt auf das breitere Stück Stoff. Es ist gewebt worden. Die maschinelle Herstellung sei wichtig, um die später für den Flugzeugbau notwendigen großen Mengen erzeugen zu können. Eine zweistellige Zahl von Metern Spinnenseide seien bisher gewebt worden.
Spinnenseide hat gute Crashtest-Eigenschaften
Aber wie soll dieses dehnbare Gewebe oder das daneben liegende noch nachgiebigere Stück gestrickte Spinnenseide im Flugzeugbau einsetzbar sein? Nun kommt das daneben liegende Plastikteil ins Spiel. Es ist in Wirklichkeit ein mit Harz getränktes Gewebe aus Spinnenseide, ein sogenanntes Composite-Material und hart. In dieser Konsistenz kann man es sich in einem Jet vorstellen. „Das klassische Einsatzgebiet ist dort, wo etwas einschlägt“, sagt Konigorski. Also beispielsweise in der Flugzeugnase, in unteren Rumpfteilen oder der Triebwerksverschalung, gegen die gerade beim Start auch häufiger mal Vögel krachen.
„Bei der Auswertung von Materialdaten haben wir gesehen, dass Spinnenseide hohe Bruchdehnung aufweist und sich deshalb herausragend zur Crash-Absorption eignet“, sagt Gunnar Haase. Der 49-Jährige ist Chefingenieur des Thor-Programms, bei dem High-Tech-Materialien mit dem Ziel getestet werden, sie in der Realität einsetzen zu können.
Das erste große Projekt des Thor-Programms war ein Flieger, dessen Einzelteile im 3D-Druck-Verfahren hergestellt wurden. Airbus experimentiert seit einigen Jahren mit der additiven Fertigung, bei der aus Pulver die Teile Schicht für Schicht in einem Drucker aufgebaut werden. So stammen beispielsweise Kabinenhalter für den modernen Großraumjet A350 daraus. Der Vorteil: Lediglich fünf Prozent des Materials wird zu Abfall, während es früher beim Fräsen 90 bis 95 Prozent waren.
Erster Mini-Flieger aus 3D-Drucker kostete 20.000 Euro
Aber kann man auch ein Flugzeug 3D-drucken? Schließlich muss es nicht nur robust, sondern auch innen hohl und aerodynamisch sein. Mehr als 60 Teile wurden aus Polyamid – aus dem Material bestehen auch Nylonstrümpfe – gedruckt. Probleme machten dem zehnköpfigen Team vor allem wellige Flügel. Im November 2015 war es geschafft. Der vier mal vier Meter große und ohne Technik etwa 16 Kilogramm leichte Flieger war in drei Wochen zusammengebaut worden und nach Stade transportiert worden. Dort flog er dann zwei, drei Runden über den Platz. „Damit haben wir gezeigt, dass wir ein Flugzeug drucken können“, sagt Konigorski und ergänzt: „Wenn er weit genug weg ist, sieht er aus wie ein richtiger Airbus.“
Im Laufe der Zeit folgten weitere Flüge mit neuen Aufträgen. Vollgestopft mit Technik sollten Telemetriedaten gesammelt werden, elektrischer Antrieb und widerstandsarme Flügel wurden ebenso getestet wie verschiedene Materialien. Während Chefingenieur Haase in Stade das Fluggerät beim Erstflug noch per Fernsteuerung lenkte, ist das heute anders: „Heute fliegen wir voll automatisiert.“ Künftig sollen auch Anwendungen aus dem Bereich der künstlichen Intelligenz folgen. Das Thor-Flugzeug soll eigenständig landen, Hindernisse auf der Start- und Landebahn entdecken und bestimmen, ob es sicher ohne Unterstützung vom Boden landen kann.
Der Airbus, der abstürzen darf
Scheitern gehört dabei zum Konzept. Zweimal legte das 3D-Flugzeug bereits Bruchlandungen hin und hatte nur noch Schrottwert. Natürlich erfolgen die Flüge nur auf auf einem dafür vorgesehenen Versuchsgelände. „Es geht nicht darum, dass das Flugzeug heil zurückkommt. Wenn wir neue Risikotechnologien unter realen Bedingungen testen wollen, müssen wir den Verlust des Flugzeuges einkalkulieren“, sagt Konigorski.
Möglich wird dies durch die binnen weniger Wochen mögliche und relativ günstige Herstellung. 20.000 Euro habe der erste Mini-Flieger gekostet. Heute sind sie in der Produktion noch günstiger. In der Elektronik, die im Rumpf des Flugzeugs steckt, sind fast nur Standardteile eingebaut. Das teure seien die Algorithmen darauf, die Millionen kosten – deren Back-up aber auf Rechnern oder USB-Sticks gesichert sind. Weil das Fluggerät inklusive Technik, Motor und Batterien leichter als 25 Kilogramm ist, muss es nicht vor dem Abheben zertifiziert werden.
2021 könnten Spinnenseiden-Teile Premiere finden
Schon bald ist der Start des kleinen Flugzeugs mit Teilen aus organischem Material möglich. „2021 könnte Spinnenseide im Thor-Programm eingesetzt werden“, sagt Konigorski. Interessant sei der Stoff übrigens auch für die Beschichtung von Oberflächen wie Sitzen. Schließlich werde er bereits in der Kosmetik und Medizin (als Überzug von Implantaten) eingesetzt und habe hervorragende antibakterielle Eigenschaften.
Damit Spinnenseide tatsächlich in richtigen Airbus-Passagierflugzeugen über den Wolken mitfliegt, muss es im Praxistest mit guter Leistung überzeugen, darf nicht teurer sein als konkurrierende Materialien und sollte leichter sein. Das Einsparen von Gewicht ist stets ein zentrales Ziel im Flugzeugbau, damit der Kerosinverbrauch und damit auch die Betriebskosten gesenkt werden können.
Durch die starke Welle der Klimaschutzbewegung könnte der Einsatz der Spinnenseide gepuscht werden, wenn die Herstellung energieintensiver Produkte durch Preisaufschläge teurer würde. Doch Hoffnung auf einen allzu schnellen Einsatz in richtigen Jets dämpft Konigorski: „Alles, was wir tun, soll strategische Impulse für Airbus bringen. Die Erkenntnisse, die wir gewinnen, gehen aber erst in die übernächste Flugzeuggeneration ein.“