Hamburg. Passagierzahlen wegen der Pandemie eingebrochen: Viele Airlines legten Jets still. In Hamburg werden sie wieder startklar gemacht.
In normalen Zeiten sind auf dem Gelände von Lufthansa Technik tagsüber alle paar Minuten startende und landende Maschinen vom benachbarten Hamburger Flughafen zu hören. An diesem Nachmittag ist es ruhig. Nur ab und an durchbricht ein Knarzen die Stille. Sobald der Wind etwas Fahrt aufnimmt, bewegt sich das im freien Spiel befindliche Seitenruder eines Flugzeugs durch den Luftstrom nach links und rechts – und gibt das Geräusch von sich.
Dieser Airbus A320 gehört zu knapp einem Dutzend Maschinen, die die Lufthansa beim Abendblatt-Besuch im Werk des Tochterkonzerns wegen der Corona-Krise geparkt hat. In der Spitze waren es sogar an die 20 Maschinen. Doch so langsam stockt die Fluggesellschaft ihre fliegende Flotte wieder auf. Das bringt den Hamburger Technik-Beschäftigten in Zeiten der Auftragsflaute wieder etwas mehr Arbeit ins Haus.
Motoren werden fürs Parken mit Folien geschützt
Ein paar Meter weiter in der Halle vier steht Wartungsleiter Nils Wiedemann vor dem Triebwerk eines A320. Mit der Hand streicht er über den vorderen, äußeren und nun glänzenden Ring der Triebwerksverkleidung. „Hier sieht man, dass geschliffen wurde“, sagt der 40-Jährige. Die Lufthansa-Maschine mit der Registrierung „D-AIUQ“ steht seit drei Monaten in Fuhlsbüttel. Vorher parkte sie schon eben so lang in München. Die Motoren waren für diesen Zeitraum mit einer Plastikfolie geschützt, damit sich weder Vögel noch Insekten einnisten und keine Fremdkörper in die Turbine hineinkommen.
„Als noch von draußen eine Folie draufgemacht wurde, konnte die dahinter liegende Feuchtigkeit oft nicht mehr weg und sorgte für Korrosion“, sagt der gelernte Flugzeugelektroniker. Das Abklebeverfahren wurde nun leicht modifiziert, sodass sich die im Volksmund „Rost“ genannte Korrosion an dieser Stelle gar nicht mehr bilden soll. So sorgte die Corona-Krise auch für einen Lerneffekt.
Flugzeuge können nicht einfach nur abgestellt werden
Bei der „Uniform Quebec“ – wie sie firmenintern nach dem Kürzel genannt wird – musste die Korrosion aber noch abgeschliffen werden. Denn sie soll nun zurück in den operativen Einsatz. Für den morgigen Tag ist der Überführungsflug geplant. Doch einfach nur an Bord gehen, einsteigen und losfliegen können die Piloten nicht. In der mit Vorschriften bespickten und auf Sicherheit bedachten Luftfahrtwelt müssen zunächst viele Schritte abgearbeitet werden – und das beginnt mit dem Parken des Flugzeugs.
Neben den Turbinen werden beispielsweise auch Sonden und Sensoren abgedeckt. Die Flugzeuge werden „sturmbetankt“ und erhalten teilweise Ballast im Frachtraum, damit sie schwerer sind und selbst bei größeren Windstärken sicher stehen. Die Wasseranlage für die Küchen und zum Händewaschen wird entleert. Die Batterien werden abgeklemmt. Aber auch im Anschluss werden die Jets nicht einfach nur abgestellt. In regelmäßigen Abständen stehen Aufgaben für die Techniker an.
Regelmäßig erfolgen Checks an geparkten Maschinen
Nach sieben Tagen kommen die Mechaniker zum ersten Check zurück zum Flugzeug. Sie schließen die Batterien wieder an und laden sie, schalten den Strom an. Sie kontrollieren den Zustand der Räder und untersuchen die gesamte Maschine auf Beschädigungen von außen. „Der Sieben-Tage-Check besteht größtenteils aus Sichtkontrollen“, sagt Wiedemann. Vier Stunden werden für ihn veranschlagt. Fällt etwas auf, wird ein Auftrag für Beanstandungen angelegt und anschließend abgearbeitet.
Lesen Sie auch:
- Jeden Monat ein neuer Airbus für Lufthansa
- Lufthansa Technik: Haifischhaut für Jets geht in Serie
- Gewinneinbruch – Lufthansa Technik baut weitere Stellen ab
Beim 15-Tage-Check müssen die Lufthansa-Technik-Beschäftigten weitere Aufgaben erledigen. Sie testen die Klimaanlage und mehrere Systeme, bewegen die Reifen, damit sich keine Unwuchten bilden. Nach einem Monat steht der nächstgrößere Check an. Es gibt weitere Systemtests, beide Triebwerke werden einmal angelassen und für zehn bis 15 Minuten laufen gelassen, damit der Kraftstoffkreislauf einmal in Bewegung ist. Der Bordcomputer wird mit Updates versorgt.
Nach drei Monaten ohne Flug kommen Jets ins Storage
Aus den Tanks wird an der untersten Stelle eine Probe genommen. Dort sammelt sich Kondenswasser, weil es schwerer ist als Kerosin. Mechaniker prüfen mit einem Testgerät und Teststreifen, ob sich Mikroben gebildet haben. Ist das der Fall werden Biozide beigemischt, um sie abzutöten.
Bis zu drei Monaten verbleibt ein Flieger im Parking-Modus. Will die Fluggesellschaft ihn noch länger nicht nutzen, ist es wirtschaftlicher, ihn ins Storage zu schicken. In diesem Lagerungszustand ist er nicht mehr lufttauglich, die Systeme werden lahmgelegt. „Der Aufwand, das Flugzeug ins Storage zu bringen, ist viel umfangreicher als beim Parking. Aber es gibt nur wenige Checks zwischendurch“, sagt Wiedemann. Es werden die Scheiben mit reflektierender Folie abgeklebt und einige Bauteile vorübergehend ausgebaut, auf einigen Flächen wird ein Korrosionsschutz angebracht. Das Öl in den Triebwerken erhält zusätzlich Konservierungsstoffe.
Die Reaktivierung aus dem Storage dauert rund 230 Arbeitsstunden
In der Halle 4 von Lufthansa Technik steht mit der „Lippstadt“ direkt neben der „Uniform Quebec“, für die sich noch keine Stadt als Namenspate gefunden hat, eine Maschine, die direkt aus dem Storage kommt. „Ein Flugzeug wieder zu reaktivieren dauert normalerweise etwa 230 Arbeitsstunden“, sagt Wiedemann. Bei dieser Maschine sind es durch Zusatzaufträge sogar 380 Stunden.
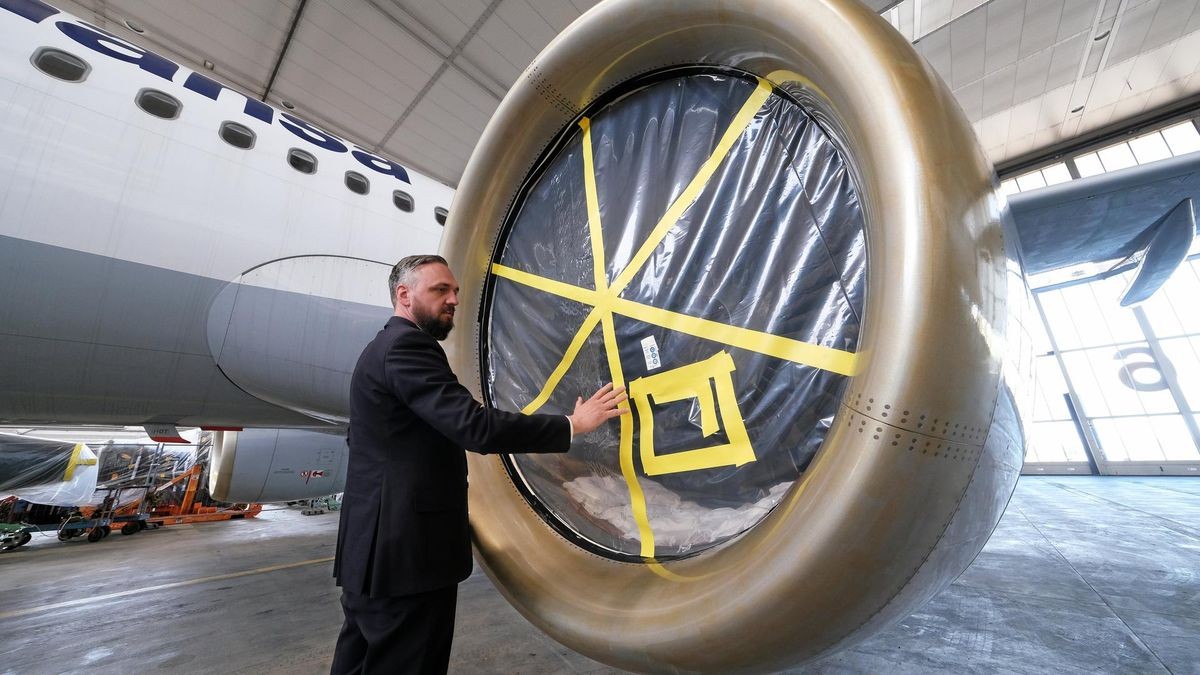
Er steht neben dem Triebwerk des A321, das noch mit einer Plane abgedeckt ist. Und sieht eventuellen Bedarf für das Einschreiten seiner Kollegen. Ein Aufkleber, der als Indikator für Luftfeuchtigkeit dient, hat sich wegen zu hoher Feuchtigkeit pink verfärbt. In der Turbine liegen Silikat-Kissen, die die Feuchtigkeit aufnehmen sollen. Möglicherweise müssen sie nun getauscht und die Folie neu verklebt werden.
Flugzeug nach 50 bis 70 Arbeitsstunden wieder flugfit
Schon deutlich weiter beim Fitmachen ist die „Uniform Quebec“. Das Prozedere begann vor zehn Tagen mit dem Studieren des Auftrags. „Als erster Schritt kommt das Flugzeug in die Halle. Dann werden die Triebwerke ausgepackt und geschaut, ob es Beschädigungen gibt“, sagt Wiedemann. Zusammen mit der Reaktivierung, die bei einem geparkten Flugzeug zwischen 50 und 70 Arbeitsstunden dauert, erfolgen nämlich häufig weitere Maßnahmen.
Die umfangreichsten Aufgaben stehen ganz oben auf der „To do“-Liste. So musste am hinteren Teil des Triebwerks zunächst viel von der Verkleidung abgebaut werden, um ein modifiziertes, durch neue Streben stabileres Element anzubauen. In das Electronic Flight Bag – quasi der elektronische Pilotenkoffer, der wichtige digitale Informationen beispielsweise wie Karten, Routen und Rollwege enthält – wurden Computersysteme des Flugzeugs miteingebunden. Dafür mussten Kabel neu verlegt und angeschlossen werden. Das treibt die Mannstunden für die „Uniform Quebec“ deutlich nach oben auf rund 280.
Frischwasseranlage für WC und Küchen wird desinfiziert
Zu den Reaktivierungsmaßnahmen zählt die Überprüfung der Anlage für das Frischwasser, mit dem später Stewardessen und Stewards an Bord wieder Tee und Kaffee kochen und sich Passagiere die Hände waschen. Die Anlage wird mit einer Mischung aus Wasser und Desinfektionsmittel aufgefüllt, die sechs Stunden einwirken muss. In einem Labor wird im Anschluss untersucht, ob Keime oder Schwebepartikel enthalten sind. Bei einem Befund wird das Vorgehen wiederholt, bis das System sauber ist.
Die derzeitige Flotte der Lufthansa |
Auf dem Höhepunkt der Corona-Krise hatte die Kranich-Linie von rund 300 Flugzeugen 260 Jets außer Betrieb genommen. Rund 120 Flugzeuge sind nun zurück im operativen Betrieb. „Derzeit setzen wir vor allem auf kleinere, sparsame und effiziente Flugzeugmodelle“, sagt Lufthansa-Sprecherin Mirjam Eberts dem Abendblatt. Neben dem A319 als kleinstes Flugzeug sind mit dem A320neo und A321neo alle spritsparenden Jets im Einsatz. Auf der Langstrecke fliegt die gesamte moderne A350-Flotte und Teile andere Modellreihen, während alle A380 am Boden stehen. Als Folge von Impffortschritten und der weiteren Verbreitung und Akzeptanz von Testmöglichkeiten rechne man mit einer deutlichen Markterholung im zweiten Halbjahr, so Eberts. Der Wunsch zu reisen sei bei den Menschen ungebrochen. Für das Gesamtjahr plant die Kranich-Linie, 40 Prozent der Kapazitäten des Vorkrisenniveaus zu erreichen. Kurzfristig könne man bei Bedarf auf bis zu 70 Prozent aufstocken. |
Unterhalb des Cockpits steht ein Rollwagen, auf dem sich ein gelber Koffer befindet: der sogenannte Air-Data-Tester. Druckleitungen führen zu den Pitotrohren. Sie sind für die Flugsicherheit extrem wichtig, messen den Staudruck des Flugzeugs und damit quasi die Geschwindigkeit. Der Air-Data-Tester simuliert Geschwindigkeit und Höhe des Fliegers.
In Tests werden Flughöhe und Geschwindigkeit simuliert
Der gelernte Flugzeugelektroniker Daniel von Zmuda hat im Cockpit auf dem Pilotensitz Platz genommen und hält die Fernbedienung des Air-Data-Testers in der Hand. „Der Techniker kann hier die vom Hersteller für Tests verlangte Flughöhe und Geschwindigkeit einstellen und mit den Cockpitinstrumenten abgleichen, ob die Werte auch vom Flugzeug korrekt angezeigt werden“, sagt von Zmuda. Bei „Uniform Quebec“ ist alles okay. Trotzdem erfolgt noch ein Arbeitsschritt.
„Am Ende des Parkings werden die Anschlüsse der Luftdaten-Systeme noch einmal durchgepustet“, sagt Wartungsleiter Wiedemann. „Das heißt: Wir nehmen von innen die Schläuche ab und pusten mit Stickstoff die Rohr- und Schlauchleitungen einmal komplett durch, falls sich Insekten, Staub und Wasser angesammelt haben.“ Anschließend erfolgt noch eine Dichtigkeitsprüfung.
Ein Gang durch die Kabine rundet den Check ab
An dem frisch gewaschenen Lufthansa-A320 stehen nur noch kleine Arbeiten an. Der Nachtdienst muss Aufkleber an der Maschine anbringen. Am nächsten Tag werden die Reifen auf Luftdruck und Beschaffenheit der Laufflächen kontrolliert. Der Ölstand der Triebwerke und der Federweg der Fahrwerke wird geprüft. „Es wird noch einmal durch die Kabine gegangen und geschaut, ob die Gurte und die Beleuchtung in Ordnung sind, die Batterien geladen und die Notfallausrüstung vorhanden ist“, sagt Wiedemann.
Die Techniker schauen sich an, ob alle vorgesehenen Arbeiten ausgeführt und ordnungsgemäß dokumentiert wurden und schreiben das „release to service“, also die Freigabe für den Flugbetrieb.
Flugzeug wird in Hamburg versiegelt
Im Anschluss durchsucht der Werkschutz den Flieger und versiegelt ihn. Vom Flughafen kommt dann ein Schlepper und zieht ihn – stets begleitet vom Werkschutz im Auto daneben – zum Airport. Dort steigen die Piloten ein und fliegen die Maschine nach München. Für die fünf Jahre alte Maschine steht am Nachmittag nach bisher 11.415 Flugstunden Start 8841 an – das Knarzen des Seitenruders des abgestellten anderen A320 dürfte dann bei dem Dröhnen der Turbinen nicht zu hören sein.