Bad Laasphe. . Das Traditionsunternehmen „Treude & Metz“ aus Bad Laasphe entwickelt zusammen mit Forschern der RWTH Aachen einen nachhaltigen Baustoff.
Fast 30 Prozent der Daunen mussten bislang bei der Produktion entsorgt werden, weil die Federn nicht weiter zu verarbeiten waren. Ein Zustand, der nicht nur kostenintensiv, sondern auch fragwürdig im Hinblick auf die Nachhaltigkeit ist. Das Bad Laaspher Traditionsunternehmen „Treude & Metz“, das auf die Herstellung von Daunenkissen und -decken spezialisiert ist, hat das zum Anlass genommen und nach einer Lösung gesucht. Herausgekommen ist ein neues Produkt: der Federputz. Zusammen mit einem Forscherteam der RWTH Aachen hat Geschäftsführer Dr. Paul-Friedrich Metz knapp zwei Jahre an diesem Projekt gearbeitet. Im Rahmen eines Innovationstages hat Metz diesen neu entwickelten Kalk-Zement-Putz jetzt vorgestellt, der bis zu zehn Prozent Federn enthält.
Die Vorteile
Historie reicht fast 175 Jahre zurück
Im Jahr 1844 ließ sich Johann Jost Metz in Laasphe nieder, um dort als Barchent- und Leinenweber zu arbeiten.
1884 wurde die Firma „Treude & Metz“ handelsrechtlich angemeldet.
Hauptbestandteil von Federn ist Keratin, ein wasserunlösliches Protein, das in der Natur generell als Schutzbarriere vor Fremdkörpern fungiert. Als Metz und Mitarbeiter vom Institut für Baustoffforschung an der RWTH Aachen mit der Keratinforschung begannen, konnten sie schnell einige vorteilhafte Eigenschaften feststellen: es speichert Wärme, ist aber nur schwer entflammbar, es ist atmungsaktiv und lässt Feuchtigkeit besonders gut entweichen. Eigenschaften, die als Qualitätsmerkmale für Putz gelten. „Vor allem geht es uns aber darum, die Nachhaltigkeit dieses Materials zu sichern und es in das Bewusstsein der Verbraucher zu bringen“, so Metz.
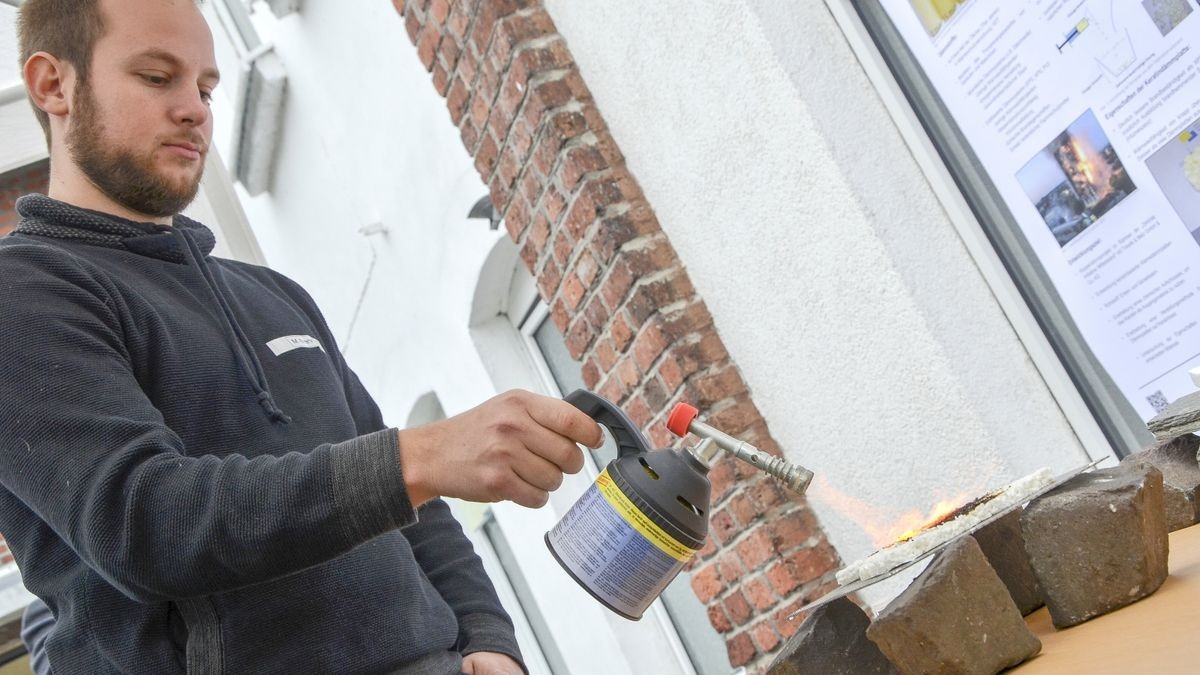
Markus Brenner, RWTH-Mitarbeiter am Institut für Bauforschung, demonstrierte die Feuerfestigkeit von Keratin, indem er ein mit Keratin behandeltes Styroporstück mit dem Bunsenbrenner bearbeitete. „Es kokelt zwar an, brennt aber nicht“, so Brenner.
Den neu entwickelten Federputz brachte Udo Schlabach von der Firma Berge Bau öffentlichkeitswirksam an eine Backsteinfassade an.
Der Unterschied zu gewöhnlichem Putz? „Er ist viel geschmeidiger und lässt sich leicht an der Wand verarbeiten“, so Schlabachs erstes Fazit. Inwieweit der Putz auch auf Wänden hält, die mit nicht-mineralischen Farben gestrichen worden sind, ist noch nicht erforscht. „Daran arbeiten wir noch. Wir möchten das Produkt weiterentwickeln“, erklärt Metz.
Weitere Produkte
Der Federputz soll jedoch nicht die einzige Neuentwicklung sein. Es gibt erste Überlegungen, die in Richtung Dämmplatten oder auch in die Textilindustrie gehen. „Wir forschen gerade unter anderem an Garnen, für die ich mir bereits ein Patentrecht in vielen EU-Ländern gesichert habe“, sagt Metz. „Damit könnten wir im Idealfall auf Baumwolle verzichten.“ Ein entscheidender Schritt für nachhaltiges Produzieren.