OBERHAUSEN. . 3D-Drucker können mehr als Plastik-Spielzeugmännchen aus Kunststoff-Paste herstellen. MAN nutzt die Technik in einer weltweit einzigartigen Art.
Als weltweit erster Hersteller setzt MAN Diesel & Turbo in seinem Oberhausener Werk Metallteile aus dem dreidimensionalen Drucker in der Serienfertigung von Gasturbinen ein.
Während Konkurrenten weltweit diese neuartige Fertigungsmethode erst erproben, ist die Testphase bei den Oberhausenern schon abgeschlossen: Leitschaufel-Segmente aus dem 3D-Druck werden in die Turbine eingesetzt und bis nach China verkauft. Dabei werden für das kreisrunde Bauteil in der Turbine zwölf tausendstel Millimeter genau gebaute Segmente benötigt und zusammengesetzt. Zuvor waren für das wichtige Turbinenelement 72 Einzelteile erforderlich.
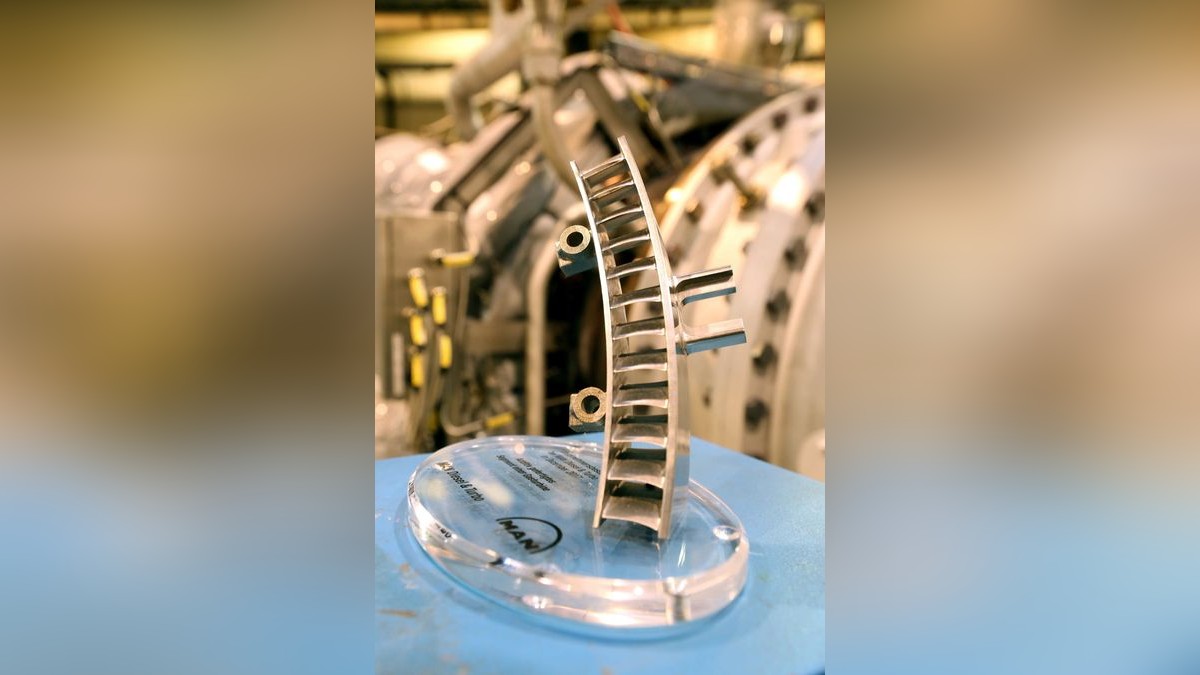
Der 3D-Drucker produziert diese Leitschaufelsegmente aus einfachem metallischen Pulver. Während bisher die silbrigen Minischaufeln aus Metallblöcken mit Computerhilfe gefräst werden mussten, erstellt der Drucker diese nun Lage für Lage aus dem Pulver. Dadurch müssen Kleinteile später nicht mehr aufwändig angefügt werden, sondern alles entsteht wie aus einem Guss. Die Anforderungen an diese Metallteile sind hoch: Sie müssen starke Temperaturschwankungen im Dauereinsatz über viele Jahre aushalten.
„Wir sind stolz auf diese innovative Leistung. Insgesamt betrachtet sparen wir durch diese Art der Herstellung des Teils auch noch Kosten ein“, sagte Werksleiter Christopher Antes im Dezember bei einem Besuch von NRW-Wirtschaftsminister Andreas Pinkwart (FDP). Dieser erhielt als Geschenk ein Leitschaufelsegment überreicht – als Erinnerung über die technische Erneuerungskraft der Oberhausener Ingenieure.
Der MAN Diesel&Turbo-Standort Oberhausen wird im Unternehmen, das dem VW-Konzern gehört, als Zentrum des 3D-Drucks geschätzt. Bisher lässt man die Bauteile noch bei einem externen 3D-Druck-Anbieter fertigen, doch schon bald will MAN im Werk selbst 3D-Drucker aufstellen.
Internationaler Verkaufsschlager
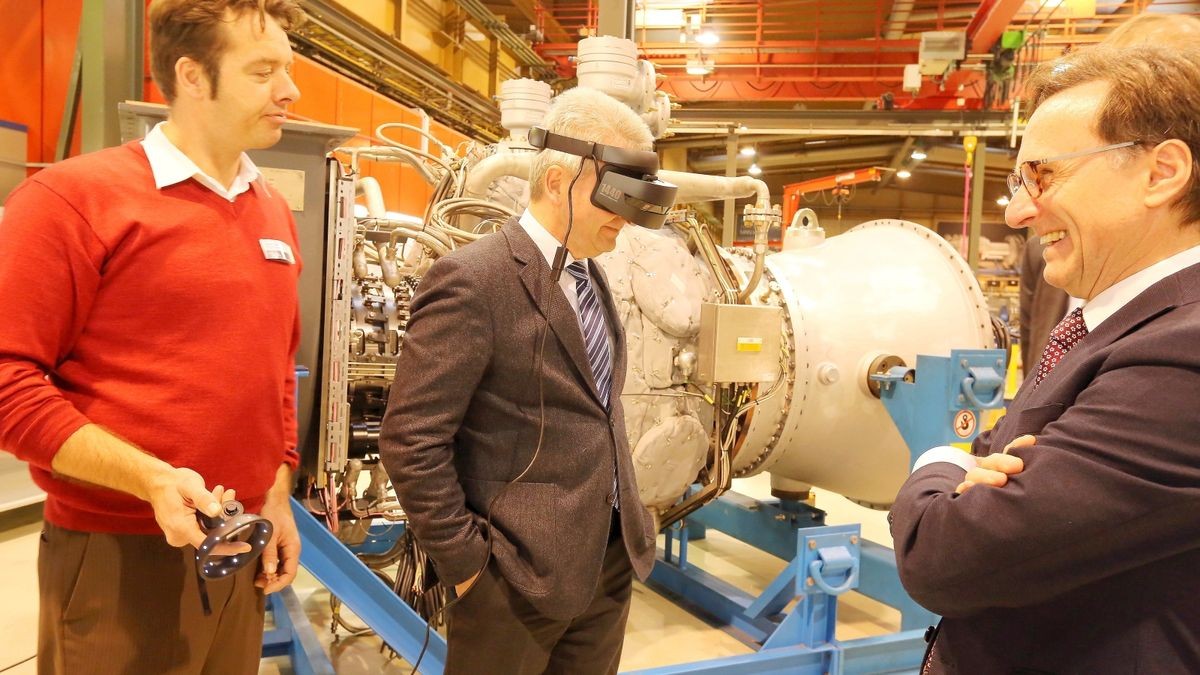
Sie sollen mithelfen, die über zehn Jahre entwickelte relativ kleine Gasturbine vom Typ MGT 6100 als Serie so zu produzieren, dass sie weltweit zum Verkaufsschlager für Mittelständler, Wohnviertel und Stadtwerke wird. Mit der Turbine von der Stange kann man Strom erzeugen und heizen – ob mit Erdgas, Biogas oder Bioethanol. Der Stickstoff-Ausstoß ist nach MAN-Angaben extrem gering, die Energieeffizienz der Turbine ist enorm hoch: Sie holt 90 Prozent an Strom und Wärme aus den Rohstoffen heraus.
MAN-Diesel&Turbo-Vorstandschef Uwe Lauber sieht in der Herstellung von Metallteilen per 3-D-Druck einen strategischen Meilenstein. „Bei der Herstellung unserer Produkte verschafft uns der 3D-Druck klare Wettbewerbsvorteile. So verkürzen die Verfahren etwa den Weg vom innovativen Konzept zum fertigen Produkt erheblich.“
>>> FREIHEITEN FÜR INNOVATIVE BAUTEILE
MAN Diesel&Turbo investiert derzeit 2,6 Millionen Euro in 3-D-Druckverfahren. Damit kann man auch deutlich billiger als mit anderen Methoden Modelle im kleineren Format real erstellen, um die im Computer entwickelten Produktideen auszuprobieren.
Das Verfahren mit den 3D-Drucktechniken hat nach Angaben von Roland Herzog, Leiter Materialtechnologie Turbomaschinen, aber noch weitere Vorteile: „Neben kürzeren Entwicklungszyklen schafft der 3D-Druck Freiheiten für innovative Bauteildesigns und verkürzt Fertigungs- sowie Lieferzeiten. Außerdem ermöglicht das Verfahren, Ersatzteile kurzfristig und bedarfsgerecht zu fertigen.“