Gelsenkirchen..
Pause bei BP in Scholven, das heißt hektische Betriebsamkeit: Im Moment wird die Olefinanlage 4 von Grund auf gecheckt. Dazu muss die Anlage komplett stillstehen. 50 Millionen Euro werden dabei in den Standort investiert.
Revisionsstillstand: Das bedeutet große Pause bei BP am Standort Scholven. Aber keinesfalls Ruhe und Gemütlichkeit, sondern eher Arbeit unter Hochdruck, im engen Zeitrahmen mit hunderten Spezialisten und mit Millionenaufwand.
Im Norden des Werkes wird der Anlagenkomplex der Olefinanlage 4 von Grund auf gecheckt, gereinigt, geprüft, erneuert und abgenommen. 600 000 Tonnen Ethylen und rund 400 000 Tonnen Propylen für die Kunststofferzeugung werden hier jährlich aus Rohbenzin hergestellt. „Die erste Teilanlage ist am 6. September außer Betrieb gegangen, die Hauptanlage ist am 15. September abgefahren worden. Ende Oktober wollen wir wieder anfahren“, sagt Volker Daams.
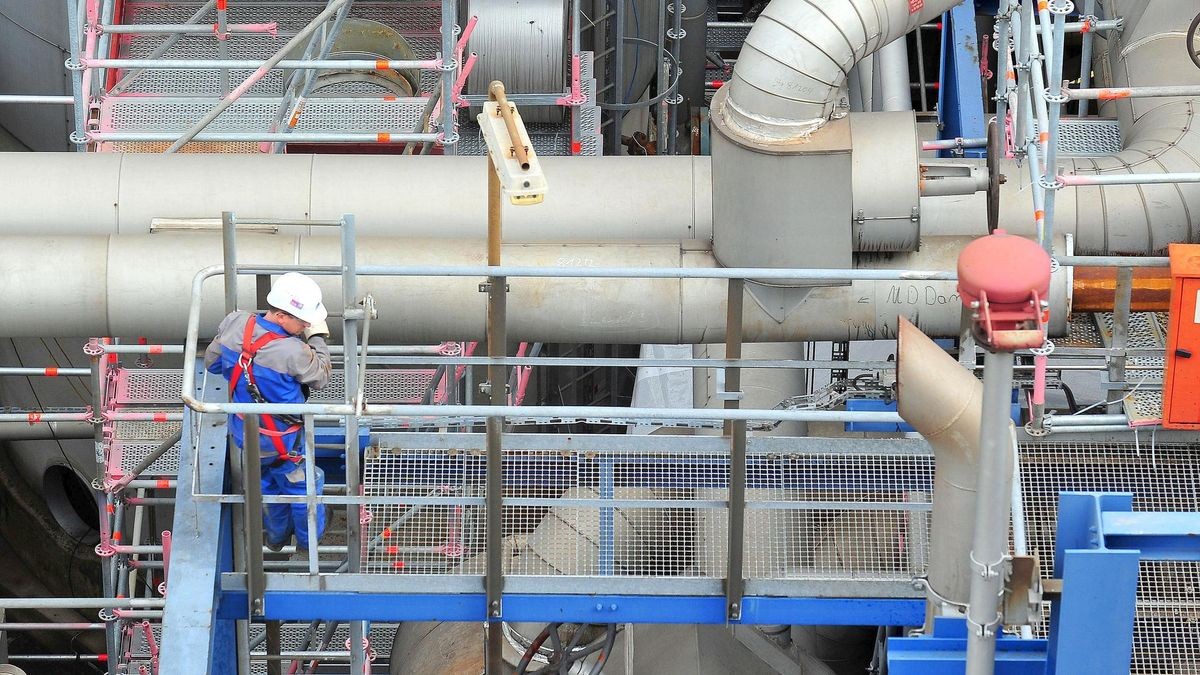
Der Maschinenbauingenieur ist in Gelsenkirchen bei BP für die Großstillstände, den vorgeschriebenen Turnaround der Anlagen zuständig – eine logistische XXL-Aufgabe mit einem Planungsvorlauf von bis zu drei Jahren. Bereits ein halbes Jahr bevor die Anlage ruht, rollen sie bereits an: die Lkw mit Material für die Gerüste, die Container für die Handwerker, die Krane. Das Isoliermaterial wird demontiert. Nummeriert und ausgebreitet liegen die Einzelteile in Reih’ und Glied neben der Werksstraße. Ein Riesenpuzzle wartet auf seine Vollendung.
Ein Detailterminplan mit 30 000 Positionen wird in diesen Tagen abgearbeitet. Am Ende werden rund 50 Mio Euro investiert sein. Dafür gibt’s für weitere sechs Jahre die Betriebserlaubnis. Nicht gerade eine TÜV-Plakette, sondern – angesichts der Mammutaufgabe naheliegend – dicke Ordner voller Prüfprotokolle und Unterschriften.
Der Ist-Zustand ist gelinde gesagt unüberschaubar. Wie das so ist bei einer Anlage, die den Platz von mehreren Fußballfeldern füllen würde und die komplexe Technik, tausende Tonnen Stahl, verwickelte Leitungssysteme, acht Riesenöfen, Kolonnen und und und vereint. Und in der sich jetzt noch Autokrane breit machen, in der geschweißt und gereinigt, geflext und gestrichen wird, in der neben turmhohen Kolonnen für die mehrstufige Destillation turmhohe Gerüste für die Arbeiter und Kontrolleure stehen.
Im Wirrwarr der Maschine wirken Menschen wie wahre Winzlinge. Hier reckt sich ein Blaumann aus einem Ofenloch, dort strebt ein Mann im knallgelben Schutzanzug zu einem Druckbehälter, dort rangiert ein Staplerfahrer, hoch oben auf Anlagenbrücken wird gewerkelt. Für die Sicherheitsbeauftragten eine Ausnahmesituation. „Man muss darauf achten, dass die Leute sich nicht gegenseitig gefährden“, wenn sie so unter- und übereinander arbeiten“, sagt Daams.
Hunderte Menschen sind auf der Anlage. „In der Tagesspitze sind es 1200 allein von Partnerfirmen“, sagt Daams. Wenn in Horst die gesamte Raffinerie im Revisionsstillstand ist, beschäftigt das bis zu 3000 Menschen täglich. Im Jahr 2012 wird das wieder für rund 45 Tage der Fall sein. Zukunftsmusik. Zunächst gilt es, die Olefinanlage 4 wieder betriebsbereit zu kriegen.
Waschplatz für die Wärmetauscher
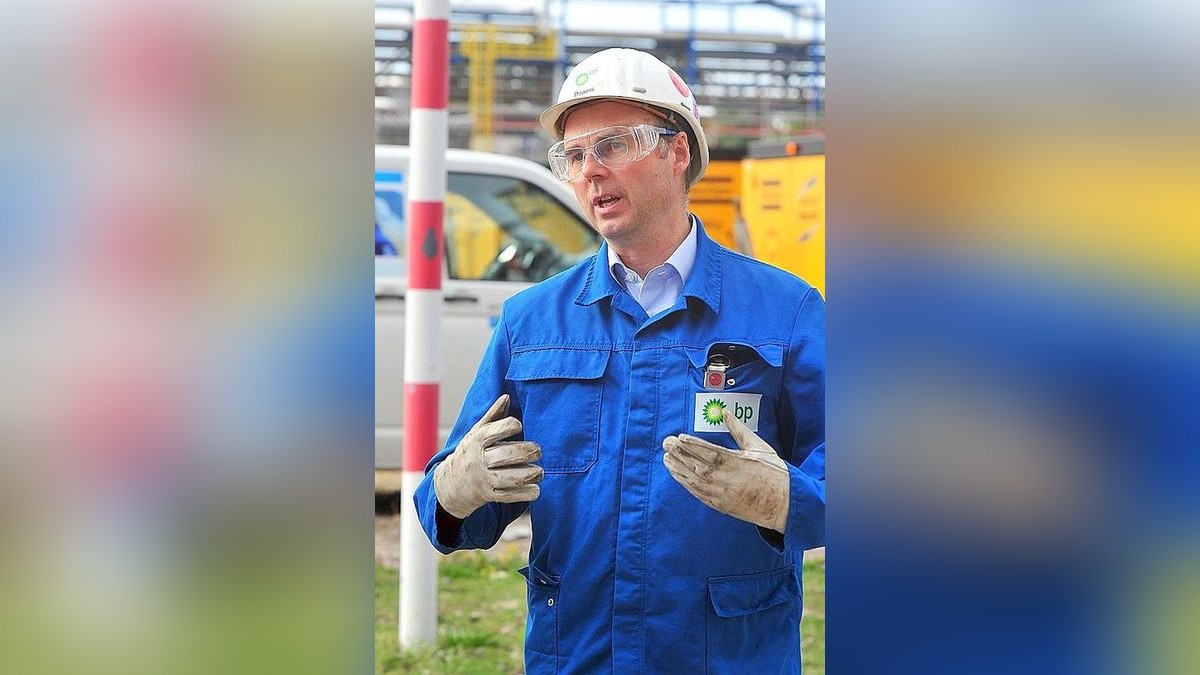
Wärmetauscherbündel liegen befreit von ihren Stahlhüllen auf dem Waschplatz. Mit Hochdruck werden die feinen Rohre gereinigt. Lanzen fahren in die Hohlräume, spülen sie mit bis zu 1400 bar frei. Behälterhauben liegen auf dem Platz daneben. In den nächsten Tagen werden sie wieder vereint sein in der Anlage. Die Prozessöfen wurden zum Teil schon neu ausgemauert, die Brenner werden inspiziert. Sie sind das Herzstück der Anlage, liefern die Power für die thermische Reaktion.
Bis zu 100 Meter hoch sind die Kolonnen, die auf Herz und Nieren geprüft werden. „Die zerstörungsfreie Werkstoffprüfung läuft vorwiegend nachts“, sagt Daams. Bedeutet: Dann werden die Riesenteile geröntgt, werden Schweißnähte und Leitungen geprüft. Mehr als 800 Druckbehälter und Wärmetauscher, fast 1800 Armaturen sowie um die 1000 Mess- und Regeleinrichtungen werden getestet und bei Bedarf repariert oder ausgetauscht.
Im Hauptmaschinenhaus machen sich Arbeiter über Gehäusedeckel und Rohgasverdichter her. Jedes Bauteil hat locker des Format eines Kleintransporters. Laufräder werden poliert und geschliffen. Rund um das Gebäude kleiden Planen Gerüste und Anlagenteile ein. „Überall, wo eingehaust ist, wird auch gearbeitet“, sagt Daams.
In der 43 Kalenderwoche soll es mit dem Stillstand vorbei sein. Zumindest der Faktor Mensch hat dann wieder eine überschaubare Größe. 80 Mitarbeiter halten die Anlage im Vierschicht-Betrieb in Gang. „Produziert wird 24 Stunden am Tag, 365 Tage im Jahr. Wenn es gut geht, sechs Jahre lang“, sagt Daams. Bis zur nächsten Revision.