Schalke-Nord. . Arsol Aromatics im Stadthafen hat fünf Tage für die Revision eingeplant. Die Reinigung der Wärmetauscher geschieht mit Wasser und über 1000 Bar.
- Produktions-Stillstand bei Arsol Aromatics – das bedeutet im Stadthafen höchste Geschäftigkeit
- Der Chemikalien-Produzent unterzieht seine Anlagen einer turnusmäßigen Revision und TÜV-Kontrolle.
- Dabei kommt modernste Industrieservice-Technik von Lobbe zum Einsatz - mit Wasserdruck bis zu 2500 Bar
Kohlrabenschwarz klebt der Dreck im Wärmetauscher, wirkt wie festgebacken in den 380, bis zu sechs Meter langen Edelstahlröhren, die in einem massiven Rundrohr gebündelt sind. Fünf dieser Wärmetauscher stehen in Reihe. Allesamt sitzen weitgehend zu. Alle Jahre wieder bietet sich bei Arsol Aromatics dieser Anblick. Wärmetauscher, sagt Ingenieur Olaf Stommel sind „systembedingt vercrackt“.
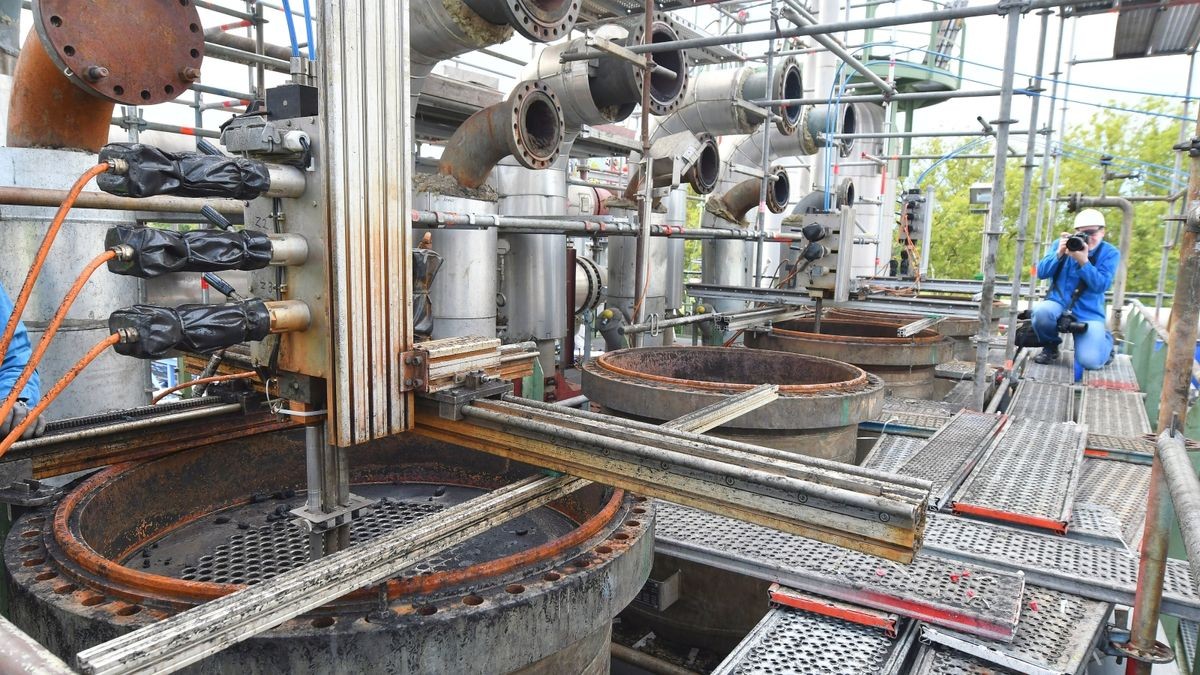
Toluol, Xylol und Arsol, die Basis-Chemie für Kunstfasern, Waschmittel oder Dämmstoffe produziert das Unternehmen im Stadthafen. „Kohlenwertstoffe“ werden hier veredelt, wie eben Benzol, das als Nebenprodukt bei der Produktion von Koks für die Stahlindustrie anfällt. Den Ursprung sieht man nach zig Produktionsdurchläufen – als rußige, dreckige Rückstände. Alle elf Monate heißt es daher: Stop für die Grundreinigung, für Instandsetzungs- und Wartungsarbeiten, für die regelmäßigen TÜV-Abnahmen und Prüfverfahren jenseits des laufenden Betriebs. Mehr als 3000 Rohrleitungen werden gecheckt, jeder einzelne Druckbehälter geprüft, die turmhohen Destillationskolonnen kontrolliert, die Wärmetauscher schließlich mit Endoskopen abgefahren.
Drei komplett autarke Arbeitsmaschinen
„Hier ist Hochdruck gefragt“ – buchstäblich. „Nächsten Mittwoch wollen wir wieder produzieren“, sagt Geschäftsführer Klaus-Dieter Westermann. Die Uhr tickt. Der Stillstand im Betrieb – er ist eine Firmenphase voller Geschäftigkeit. An die 20 Gewerke sind vor Ort, mit bis zu 50, 60 Spezialisten, vom Gerüstbauer bis zum TÜV-Ingenieur. Die Regie hat Stommel, der Betriebsingenieur. Seit 20 Jahren ist er bei Arsol Aromatics, 1999 hat er hier seinen „ersten Stillstand miterlebt“. Den nächsten wird er wenige Wochen nach der aktuellen Revision anfangen zu planen. Die nötigen Spezialisten ins passende Zeitfenster zu bekommen, ist eine Herausforderung – bei Großraffinerien in der Nachbarschaft in Horst und Scholven oder dem Chemiepark in Marl, die Tausende Kräfte für ihre Revisionsarbeiten binden.
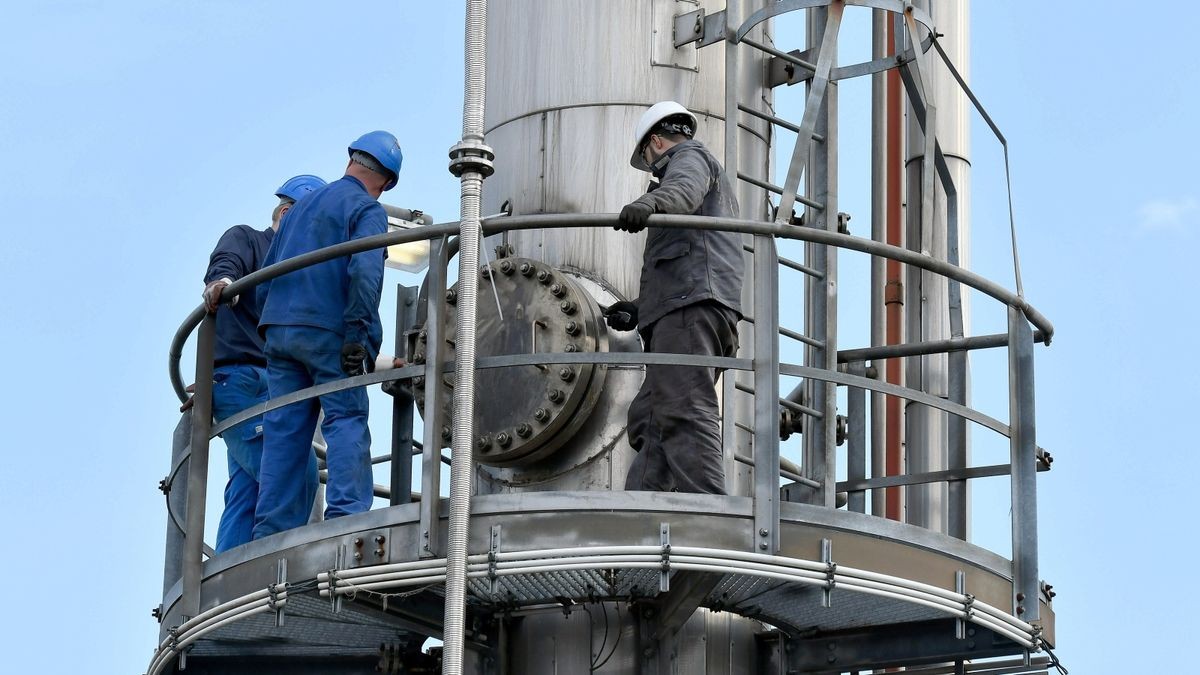
Mit einem ganzen Team und gleich drei komplett autarken Arbeitsmaschinen – Lastzüge mit Hochdruckaggregaten und eigenem Werkstattbereich – ist die Firma Lobbe vor Ort. Auf Abfallentsorgung, Sanierung und Havariemanagement hat sich der Mittelständler aus Iserlohn spezialisiert. Hier im Stadthafen ist aber seine Sparte Industrieservice gefragt. Lobbe übernimmt die Reinigung der Wärmetauscher. Früher (und zum Teil heute noch) eine absolute Drecksarbeit. Aufwändig, mühsam. Rohr für Rohr wurde im Handbetrieb gereinigt. Lobbe setzt jetzt hauptsächlich robotergestützte Hochdrucktechnik ein – mit bis zu 2500 Bar werden verstopfte Rohre freigeschossen.
Haushalts-Hochdruckreiniger bringt es auf 130 Bar.
Das ist deutliche Überschalllgeschwindigkeit und reicht, um Beton und Stahl zu zerlegen. Zum Vergleich: Ein haushaltsüblicher Hochdruckreiniger bringt es auf 130 Bar. Eingerichtet und ausjustiert wird dafür ein Rahmen über den Wärmetauschern. Rechnergesteuert werden gleichzeitig drei Hochdruckschläuche von dort aus bewegt und in die Rohre gefahren – ein Zeitgewinn. Ein Computer zeichne zugleich den Reinigungsvorgang auf und dokumentiere das Ergebnis, erklärtBodo Skaletz, der für Lobbe vor Ort die Arbeiten leitet. Ein Arbeiter steuert dabei den Prozess per Fernbedienung außerhalb des Gefahrenbereichs. Im gleichen Schritt wird zudem das Spülwasser für die fachgerechte Entsorgung aufgefangen. Eine saubere Sache – was das Endergebnis angeht. Doch auch mit modernster Technik bleibt die Reinigung ein Knochenjob. Die Arbeiter tragen Vollschutzmasken, die Lärmentwicklung mit bis zu 130 Dezibel ist enorm.
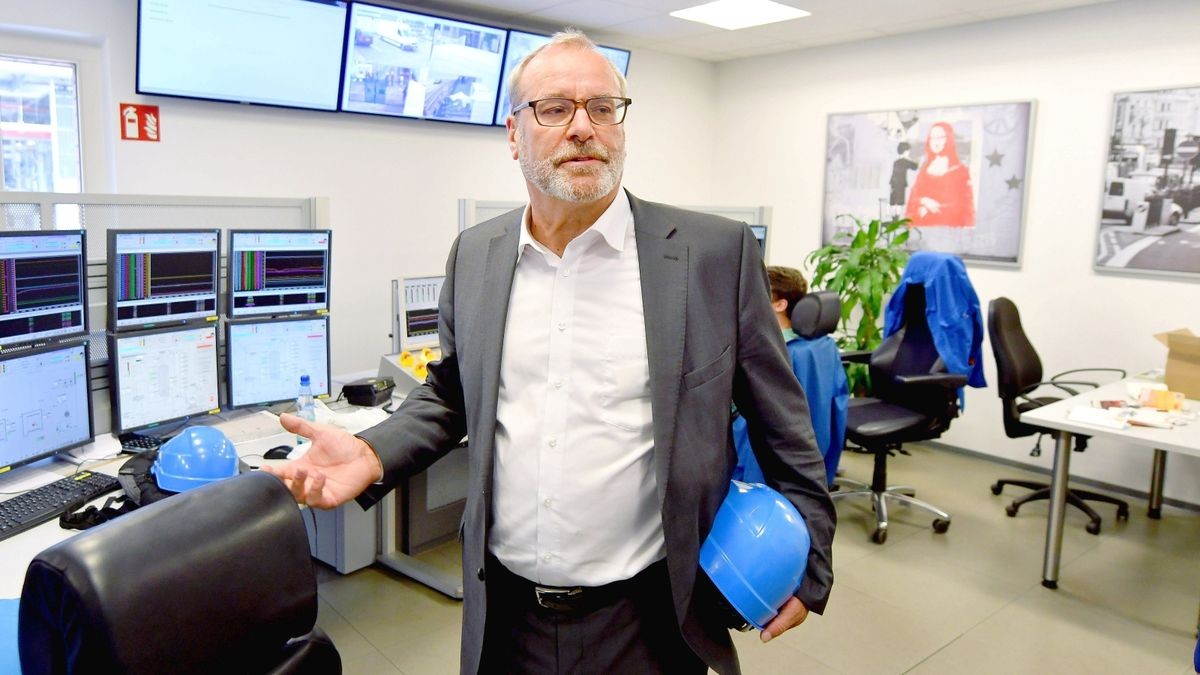
„Rund 1,5 Millionen Euro“ kosten die Arbeiten in dieser Woche. „Das ist für uns eine große Menge und ungefähr die Hälfte unseres jährlichen Instandhaltungsbedarfs“, sagt Westermann. Nach dem Stillstand ist vor dem Stillstand: 2018 wird wieder geprüft, repariert, gereinigt. Mit Hochdruck.
„Wir haben eine Nische besetzt“
Mit jeweils fünf Mitarbeitern im Wechselschichtbetrieb wird die Produktion rund um die Uhr gefahren. Insgesamt arbeiten bei Arsol Aromatics 21 Beschäftigte in der Produktion, fünf in der Instandhaltung, der Rest der insgesamt gut 45 Kräfte arbeitet in der Verwaltung und vor allem im Verkauf. Arsol Aromatics ist der größte Händler für chemische Basisprodukte in Deutschland. „Wir besetzen eine Nische. Und wir sind klein, deshalb gibt es uns noch“, sagt Geschäftsführer Klaus-Dieter Westermann. Klein zumindest nach Konzern-Maßstäben. Wendig aber auf jeden Fall. Was sich auch aktuell im Einsatz der neuen, automatisierten Reinigungstechnik für die Wärmetauscher durch Lobbe zeigt.
Entscheidungswege sind kurz bei Arsol Aromatics
Entscheidungswege sind kurz bei Arsol Aromatics: „Als kleineres Unternehmen können wir sagen: Das testen wir jetzt mal.“ Vom Ergebnis ist Westermann überzeugt. „Die Arbeit war früher eine unglaubliche Schweinerei. Das war Klofrau hoch vier. Der ganze Kohlendreck kommt einem entgegen geschossen. Man kriegt ja auch kaum noch die Leute, die so eine Arbeit machen.“
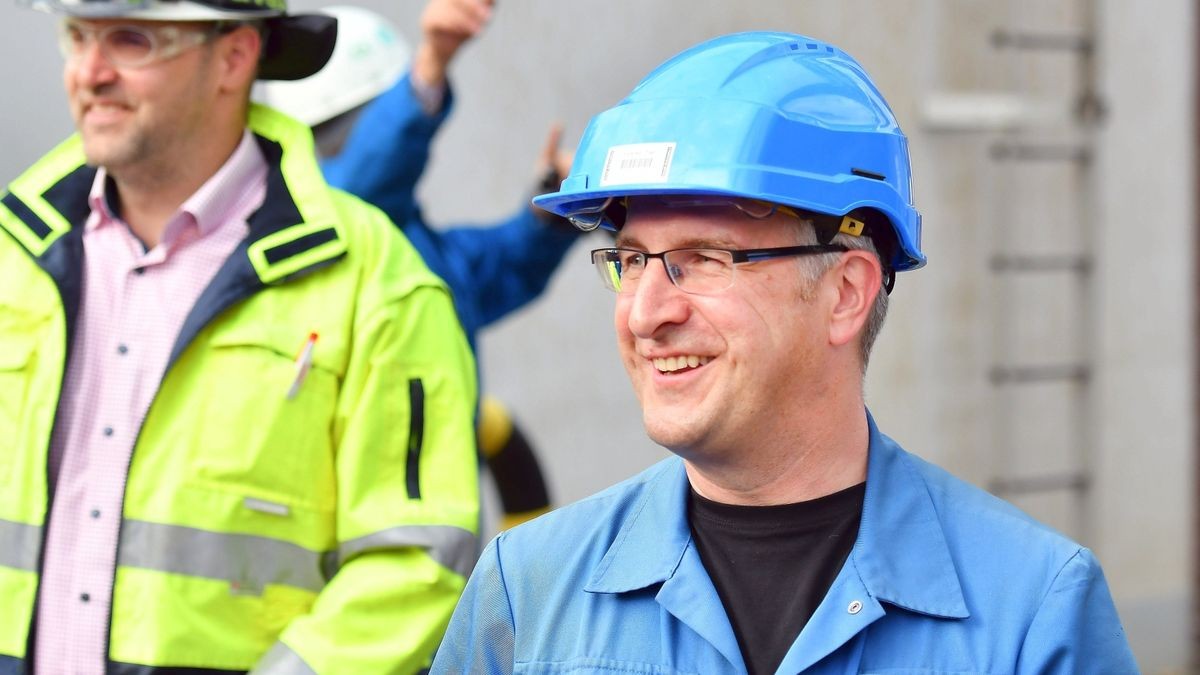
Fünf Tage und Nächte im Schichtdienst läuft die Revision. Wenn die Produktion wieder anläuft, wird man das auch in der benachbarten Großmälzerei merken. Westermann: „Wir versorgen die mit unserer Abwärme. Das spart an dieser Stelle über 10 000 Tonnen CO2 pro Jahr. Und wir können Rechnungen schreiben, was uns sehr freut.“