Duisburg. Mikro kann Makro sein: Was das dreimal drei Meter große Loch im Forschungsbau der Uni Duisburg-Essen mit einer Mikro-Präzisonsfräse zu tun hat.
Um eine Mikro-Präzisionsfräse im Zentrum für Halbleitertechnik und Optoelektronik (ZHO) auf dem Duisburger Uni-Campus zu installieren, musste zuvor ein dreimal drei Meter großes Loch in die Fassade des LT-Gebäudes an der Lotharstraße geschlagen werden.
[Nichts verpassen, was in Duisburg passiert: Hier für den täglichen Duisburg-Newsletter anmelden.]
Als am Dienstag pünktlich um 9 Uhr der Lkw mit der Last der Firma Kugler vom Bodensee in Duisburg anrollt, ist klar: Diese Kisten passen nicht in den Schwerlastaufzug des Gebäudes. Mikro muss hier Makro sein: „Das Gerät muss Strukturen von der Dicke eines Haars sehr präzise fräsen, deshalb hat es dieses hohe Eigengewicht von rund vier Tonnen“, erläutert Prof. Dr. Nils Weimann. Ein massiver Unterbau der Fräse sorgt zudem für vibrationsfreie Arbeit bei der Herstellung von Bauelementen für Höchstfrequenz-Elektronik im Terahertz-Bereich.
Terahertz-Technologie: Bauteile gibt’s nicht im Elektronik-Fachmarkt
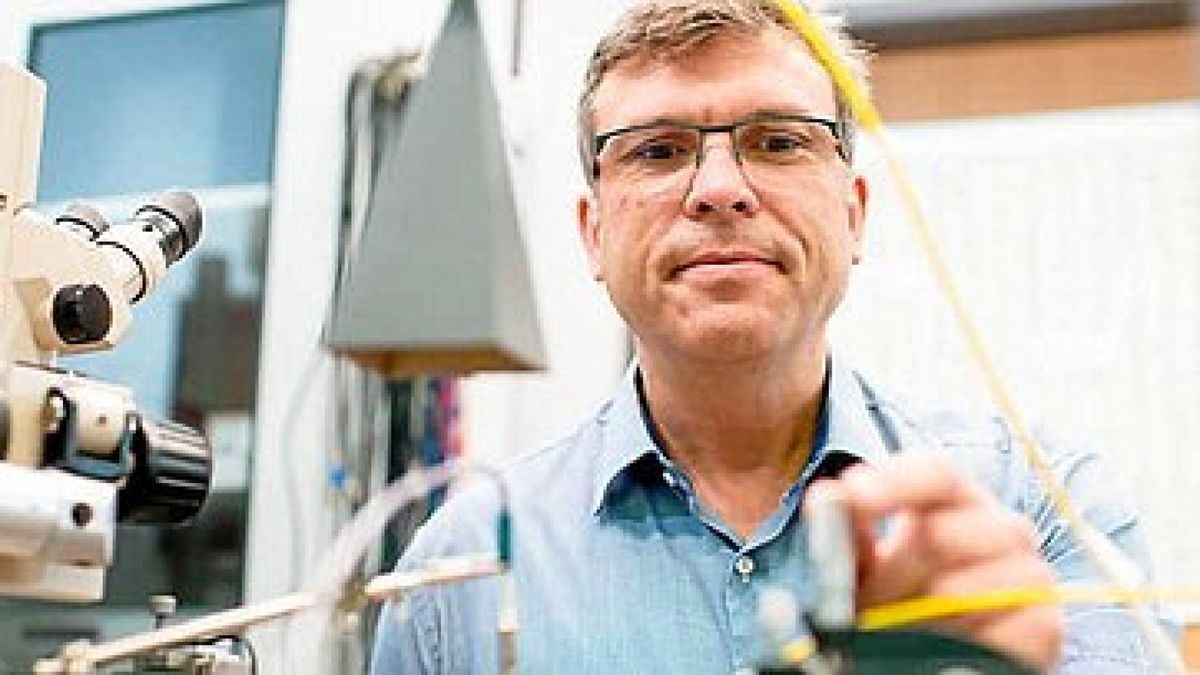
Was Weimann und seine Kollegen im Sonderforschungsbereich „Marie“ benötigen, gibt’s nicht im gut sortierten Elektronik-Fachmarkt: aus eigenem Halbleiter-Material selbst gefertigte Chips, die in wenige Zentimeter große Gehäuse eingebaut werden. Damit die auch als Antenne zur Übertragung der Signale dienen können, müssen extrem feine Kanäle präzise eingefräst werden. „Da zählt jeder Mykrometer“, erklärt Weimann. „In den Gehäusen stecken sehr viel Designarbeit und Präzision.“
Von der Anschaffung des rund 800.000 Euro teuren Geräts versprechen sich die Forscher „einen großen Schritt nach vorn“, erklärt Weimann. „Wir gehen jetzt über die Chips hinaus, um Komponenten zu bauen, die in künftigen Anwendungen verwendet werden können.“ Die Terahertz-Technologie soll sich in der kommenden 6G-Mobilfunktechnik ebenso finden wie Geräte zur Detektion und Materialbestimmung.
Schwerlastkran hievt die Kisten an ihren Standort im Labor
Präzisionsarbeit war dann auch der Einbau in Duisburg: Vom Laster ging’s für die etwa dreimal drei Meter großen Kisten zunächst per Stapler ans Gebäude, dann per Kran auf das eigens errichtete Gerüst und auf Schwerlastrollen durch das Loch in der Fassade an den Standort im zweiten Stock des LT-Gebäudes.