Bochum. In der WAZ-Serie Produktionswirtschaft geht es diesmal um den Bereich Antriebstechnologie. In Bochum gibt es dazu große Kompetenz.
Tief unten in der Erde haben sie jahrzehntelang zuverlässig ihren Dienst versehen. In Bergbaumaschinen von Eickhoff steckte immer auch ein Getriebe aus dem eigenen Haus. Die Stückzahl von Fräsmaschinen oder Walzenladern ist mit der Kohlekrise und der Energiewende zwar in den Keller gegangen. Dafür werden Getriebe made in Wiemelhausen heute vor allem für die Verwendung in luftiger Höhe hergestellt. So geht Strukturwandel.
2011 herrschte beim Tochterunternehmen „Eickhoff Wind Power“ zwar buchstäblich Flaute, weil die Finanzkrise von 2007 zeitverzögert auch den Windenergiemarkt erfasste. Und noch immer gibt es weltweite Überkapazitäten. Aber Eickhoff produziert mit Rückenwind. Das Werk in Klipphausen bei Dresden arbeitet unter Volllast, mehr als die derzeit 650 jährlich hergestellten Getriebe geht nicht.
„Darauf sind wir stolz, zumal wir nicht nur einen Getriebetyp fahren, wie das beim Bau des Werks 2006/07 geplant war, sondern einen Produktmix fahren mit vier bis fünf Plattformen“, so Dr. Ralf Wittor, Geschäftsführer der Eickhoff-Töchter Antriebstechnik und Wind Power. Die Auftragslage fordere das Haus „auf eine besondere Art und Weise“.
Entwicklung und Service in Bochum
Und auch am Stammsitz in Bochum, wo der Servicebereich ausgebaut wurde, die Entwicklungsabteilung beheimatet ist, die Prototypen getestet und unter anderem in Kühlkammern Härtetests unterzogen und wo die ersten 50 Stück neuer Serien produziert werden, laufen die Geschäfte offenbar gut. Investiert werden soll in eine effektivere Abwicklung der Montage. Und nachdem das Mutterhaus sich vor Monaten von Personal trennen musste, werden wieder Arbeitskräfte gesucht: Ingenieure, Entwicklungsingenieure, Zerspanungsmechaniker und andere Fachkräfte mehr will Eickhoff einstellen.
Es läuft. Fast 200 Millionen Euro beträgt der Jahresumsatz im Getriebebereich. Der Löwenanteil entfällt dabei auf das Windgeschäft, das ein wichtiger, wenn nicht der wichtigste Pfeiler des Hauses ist.
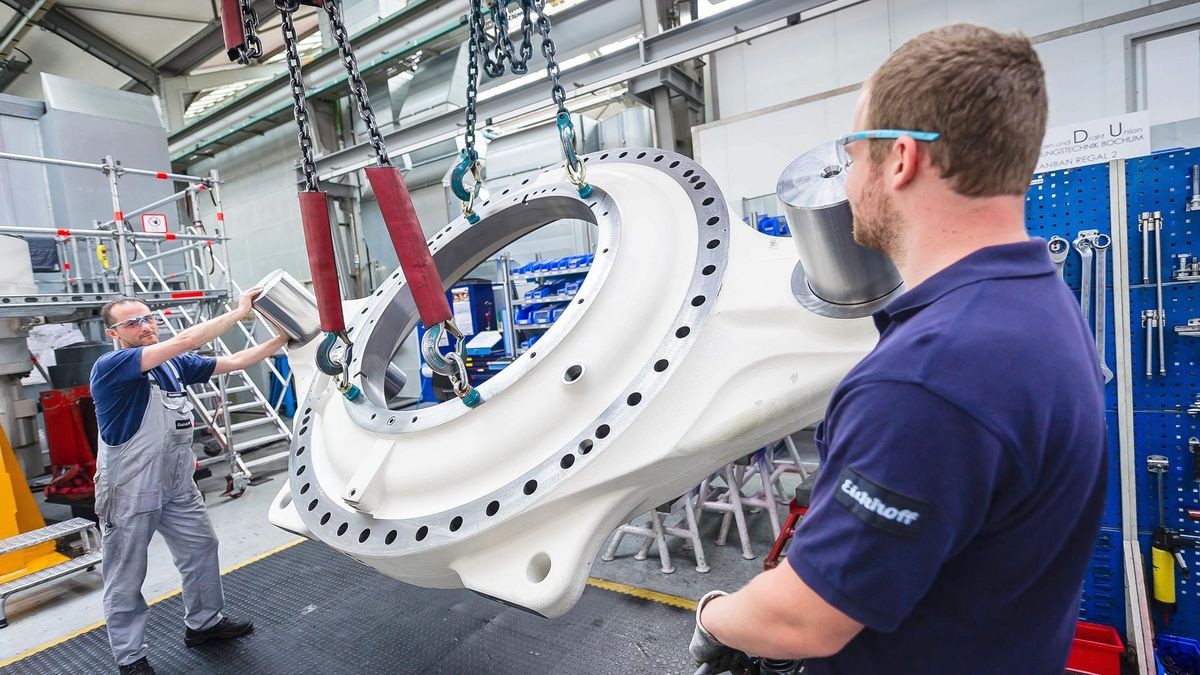
Großen Mitbewerbern wie Siemens oder ZF hat die Wind-Power-Sparte „das eine oder andere vom Brot genommen“, sagt Ralf Wittor. In deren Phalanx vorzudringen sei aber nicht das Ziel. „Wir wollen den mittelgroßen Qualitätsspielern aus Deutschland die Möglichkeit geben, flexibel zu arbeiten.“ Die eigene Flexibilität, auf die es neben hervorragenden Produkteigenschaften und termingerechter Lieferung ankomme, sei das Pfund, mit dem Eickhoff wuchere. Sechs Monate nach Auftragseingang kann eines der tonnenschweren Getriebe aus etwa 600 Einzelteilen fertiggestellt sein. „Wir liefern 20 bis 30 Tonnen Stahl, der hochpräzise und hochgenau bearbeitet und der in seiner Güte immer am oberen Rand der Toleranzen eingekauft werden muss. Man muss sehr viel Aufwand betreiben, um das richtige Material durch die Wärmebehandlung und die Fertigung zu kriegen“, so Wittor.
Und man müsse in der Lage sein, bei Bedarf eines der Getriebe zur Seite zu stellen, um ein anderes, eigentlich für einen späteren Lieferzeitpunkt vorgesehenes Getriebe vorzuziehen. Das schätzen vor allem zwei Hersteller besonders: Nordex und Senvion, deren Onshore-Windenergieanlagen mit Getrieben von Eickhoff bestückt sind.
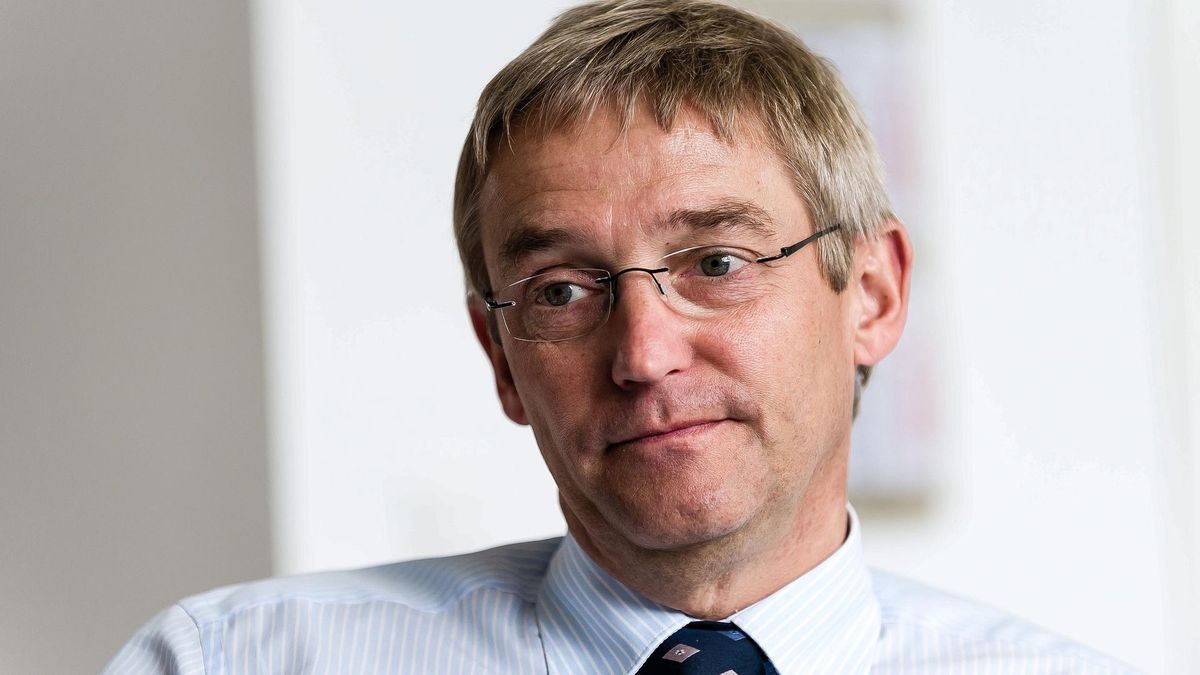
Der Chef der Antriebstechnik verschweigt nicht, dass er gerne noch einen dritten großen Abnehmer hätte. Aber der sei nicht einfach zu kriegen. Immerhin: „Was uns ein bisschen ruhiger schlafen lässt, ist, dass die Verteilung bei unseren Kunden in die Märkte hinein sehr stark differenziert ist.“ Kein unwichtiger Aspekt auf dem politischen Markt der Windkraft.
„In NRW ein Auto mit NRW-Playern bauen“
Das Auto hat eine Motorhaube – aber ein Motor ist nicht drin. Viele Kabel, Apparaturen. Aber der Antrieb des Kleintransporters mit einer Ladefläche vom Umfang einer Europalette steckt ganz woanders. Er befindet sich zur Verblüffung des Besuchers des Instituts für Elektromobilität an der Hochschule Bochum hinten in der Radfelge.
Im „BoWerk“ gebaut, dem bald abgerissen Opel-Werk I in Laer, und mit Standardteilen wie Achsen oder Bremsen von Opel ausgestattet, haben Studenten der Hochschule mit einem „innovativen Ansatz ein neues Fahrzeug konzipiert“, so Professor Michael Schugt. Und wäre die Schließung des Opel-Werks nicht gekommen, das „BoMobil“ wäre in Laer womöglich in Serie gegangen.
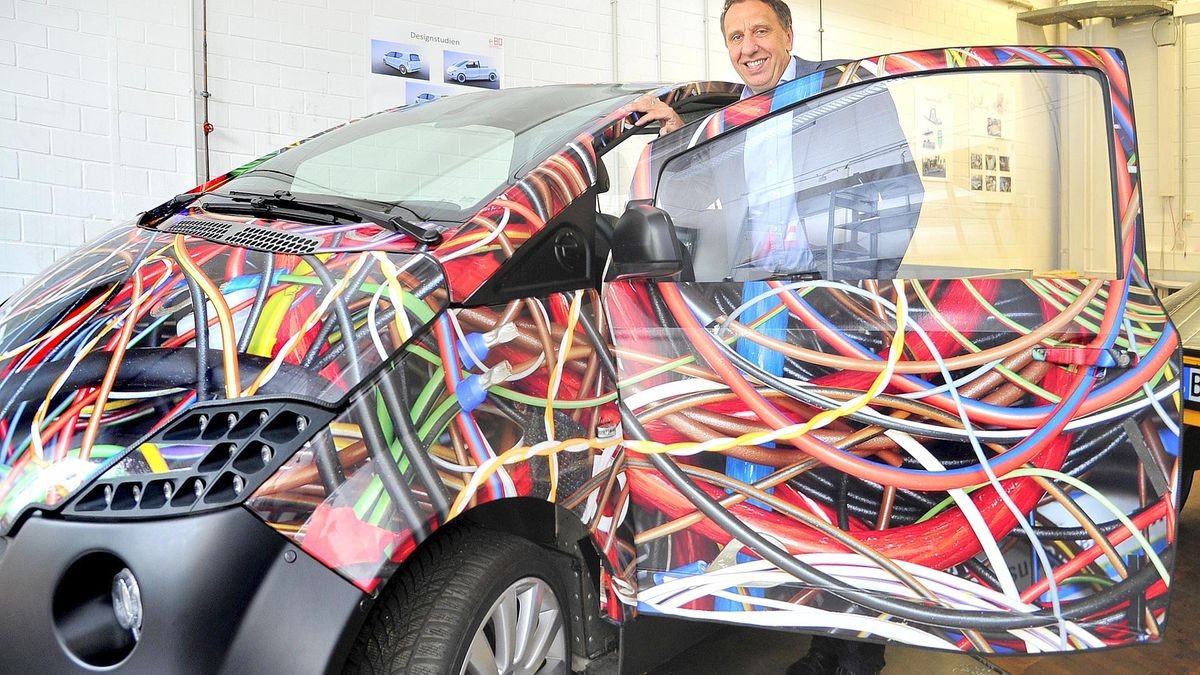
„Wir haben gekämpft dafür, dass wir den Produktionsstandort Bochum nicht verlieren“, so Schugt. „Zum Elektroauto gehört ja nicht nur, dass man ein Auto hinstellt, eine Batterie reinpackt und Motoren baut. Sie müssen Fahrzeugbau-Know-how in einem neuen Bereich aufbauen. Und das haben wir getan. Das war unser Ziel: In NRW ein Auto mit NRW-Playern zu bauen.“
Bei aller Enttäuschung darüber, dass das vom Land mit einer Millionen Euro geförderte Projekt zwar in die Nähe der Produktionsreife kam, aber dennoch nicht gebaut wird: „Das BoMobil war als Türöffner für uns etwas Phantatisches, weil eine weitestgehend maschinenbau-dominierte Welt plötzlich elektrisch geworden ist“, so Schugt.
Und es haben sich neue Chancen ergeben. Mit anderen Partnern, derzeit mit Thyssen-Krupp, bauen Hochschulstudenten Solarfahrzeuge wie derzeit etwa den „SunRiser“. Wichtig gewesen ist die Erkenntnis, „dass Studenten Großes bewegen können“.
Und sie tun es immer noch – im neuen „BoWerk“ in Wattenscheid. Dort laufen neue Projekte, etwa mit dem Logistikunternehmen Schenker. Es geht darum, elektrisch betriebene Lieferfahrzeuge zur Versorgung von stark frequentierten Innenstadtbereichen zu entwickeln.
Studenten so früh wie möglich in die Praxis einbinden
Zwei Missionen verfolgen die Hochschul-Professoren Michael Schugt und Friedbert Pautzke: Sie wollen mit ihren Studenten die Elektromobilität technisch vorantreiben und werben für eine größere gesellschaftliche Akzeptanz. Zumal, so Schugt, nach Untersuchungen des ADAC 98 Prozent aller täglichen Autofahrten in Deutschland unter 130 Kilometer liegen. Das heißt: mit aktuellen E-Mobilen bestritten werden könnten.
Und sie wollen ihre Studenten so früh wie möglich in die Praxis einbinden. Der gebürtige Bochumer ist selbst ein gutes Beispiel dafür, dass ein kluger wissenschaftlicher Kopf auch ein erfolgreicher Unternehmer sein kann. Vor seiner Hochschulkarriere arbeitete er in der Wirtschaft. Er ist Mitgründer und Gesellschafter des Unternehmens Scienlab, das 90 Mitarbeiter beschäftigt.