Gelsenkirchen.. Leser zu Besuch beim Weltmarktführer für Brandschutzglas Pilkington in Gelsenkirchen. Betrieb stellt pro Tag 22 000 Quadratmeter Verbundsicherheitsgläser her.
Heiß, höllisch heiß ist es hinter der Tür aus den 1950er-Jahren. Mit 840 Grad Celsius schlagen die Flammen gegen das Drahtglas. Es ist längst gerissen. Vorn ist es nicht viel besser. Papier geht nahe der Oberfläche mit ihren 685 Grad Celsius sofort in Feuer und Rauch auf. Ähnlich infernalische Zustände herrschten, wenn vor der Tür der Fluchtweg eines Bürogebäudes verliefe – Tapeten, Teppiche oder Gardinen – alles würde Opfer der gierigen Flammen. Und mit ihnen die Menschen.
Die WAZ-Leser, die gebannt das Experiment vor dem Ofen des Pilkington-Werks verfolgen, sind indes nicht in Gefahr. Sie können sogar die moderne Türverglasung des Weltmarkführers für Brandschutzglas an der zweiten Tür direkt daneben mit nackter Hand anfassen, als das Thermometer dahinter bereits die 600er-Marke überschritten hat. „Unglaublich“, sagt Norbert Löbler, „irre beeindruckend“ Heidrun Roth neben ihm.
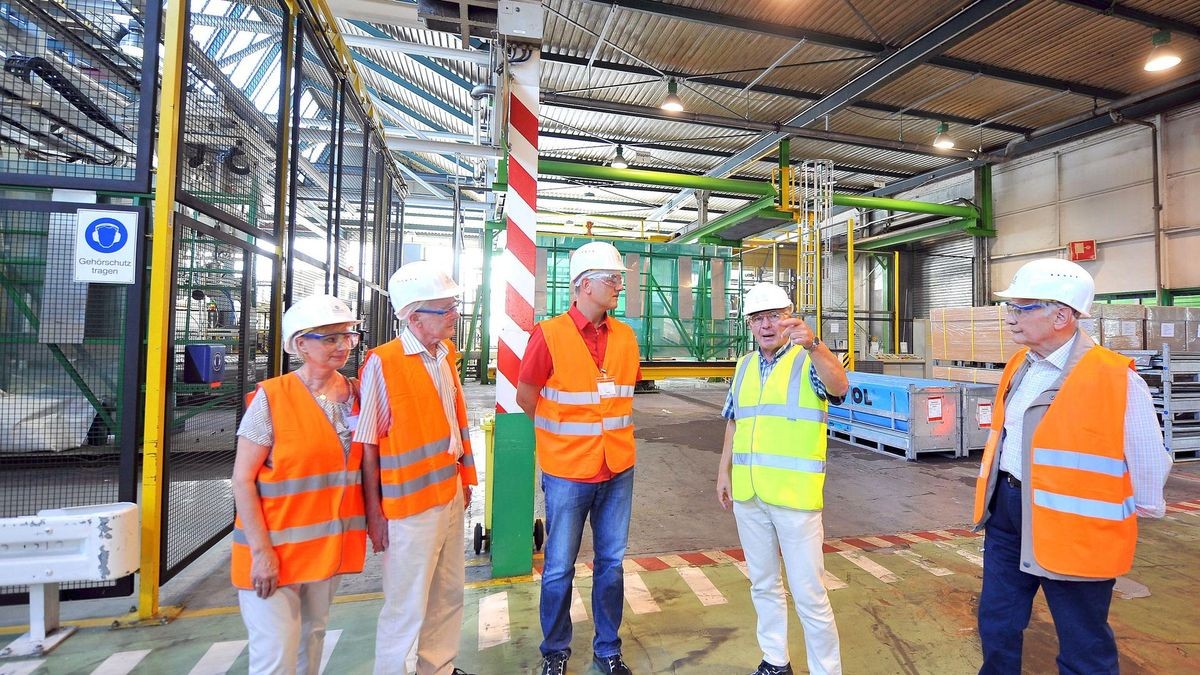
Der High-Tech-Standort in Rotthausen, 1925 als Delog AG gestartet und heute zum japanischen Multi Nippon Sheet Glass (NSG, 4,8 Milliarden Euro Umsatz in 2015) gehörig, hat den Lesern seine Pforten geöffnet. Standortleiter Dr. Martin Neifer, Betriebsleiter Bernhard Sattler und Klaus Peter Schulz, Chef am Versuchsbrandofen, führen durch das Werk. Es ist ein launiger Rundgang, am Ende steht – klar, der Durchblick.
Das Geheimnis, hinter dem Pilkington-Glas nicht gegrillt worden zu sein, liegt in seinem Aufbau. „Die Brandschutzgläser bestehen aus mehreren Gläsern, in denen Schutzschichten eingelassen sind, ähnlich einem Sandwich – zusammen bilden sie das Verbundglas.“, sagt Klaus Peter Schulz. Im Brandfall zerbricht zunächst die dem Feuer zugekehrte Seite, die Schutzschicht schäumt auf und absorbiert die Energie der Flammen. Schicht für Schicht setzt sich dieser Prozess fort – bis zu drei Stunden, dann aber ist das Glas, etwa für den Sicherheitsraum einer Bohrinsel 85 Millimeter dick. Und gut 5000 Euro pro Quadratmeter teuer.
In der Regel stellt das Werk an der Haydnstraße mit seinen 500 Mitarbeitern vier bis sechs Millimeter starke Verbundsicherheitsgläser her, und das durch automatisierte Produktionsstraßen. 22 000 Quadratmeter Glas pro Tag laufen so bei Pilkington auf, 4,5 Millionen im Jahr. Stückgröße: 6,0 x 3,21 Meter. Gewicht: gut 200 Kilogramm.
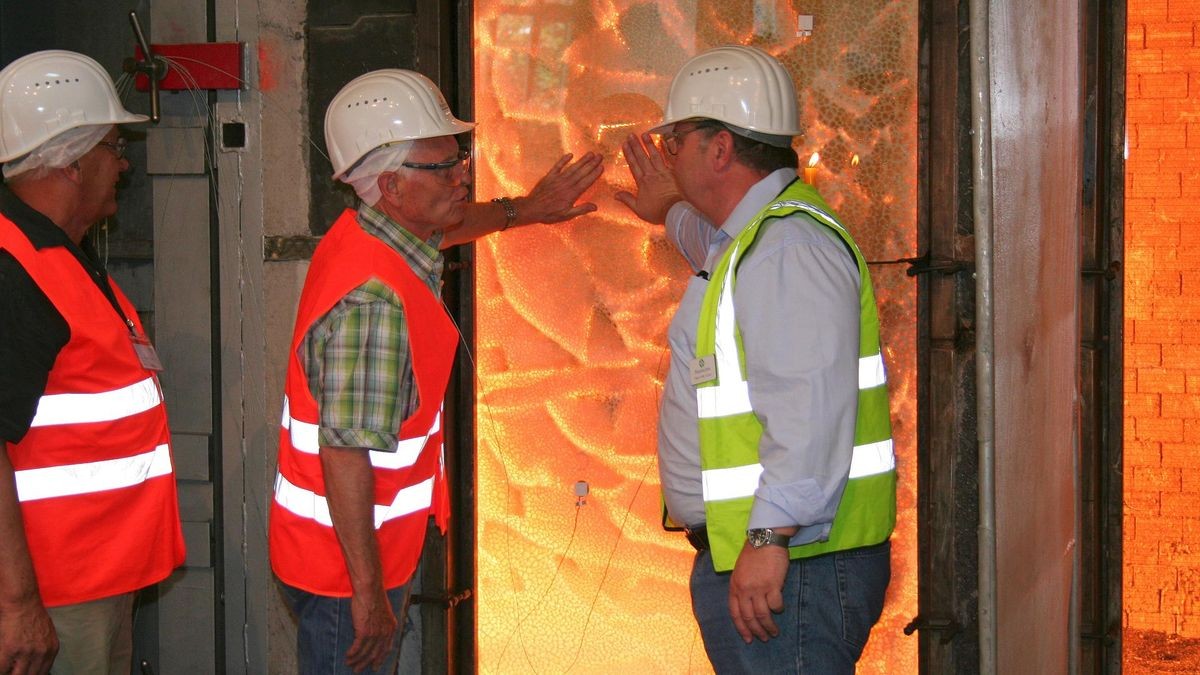
In der blitzsauberen Produktionshalle dürfen die Leser ganz nah dabei sein, wenn zwischen Ober- und Unterglas die Schutzfolien eingezogen, das „dreilagige Sandwich“ mit einer Gummiwalze verpresst und letztendlich bei 12,5 bar Druck und 135 Grad Celsius in einem monströsen Druckbehälter (Autoklav) „gebacken“ wird – das treibt auch das letzte Luftbläschen aus dem Verbundsystem und sorgt dafür, dass man als Nutzer freie Sicht hat. Anfänglich ist die Folie nämlich noch milchig weiß.
Keine Mördergrube aus seinem Herzen macht Betriebsleiter Bernhard Sattler, wenn er über die Konkurrenzsituation auf dem Markt spricht: „Vier Millimeter dickes Bauglas kostet 3,50 Euro pro Quadratmeter. Heben wir den Preis nur um zehn Cent an, werden wir mit billigerem Glas aus China überschwemmt.“ Superschiffe mit bis zu 20 000 Containern an Board machten das heute möglich. Die Strecke Hamburg China und zurück bewältige so ein Ozeanriese in einem Monat – „und das bei Transportkosten von 1000 Euro für einen Container“. Der gleiche Betrag wird für die Strecke Hamburg Gelsenkirchen fällig: paradox.
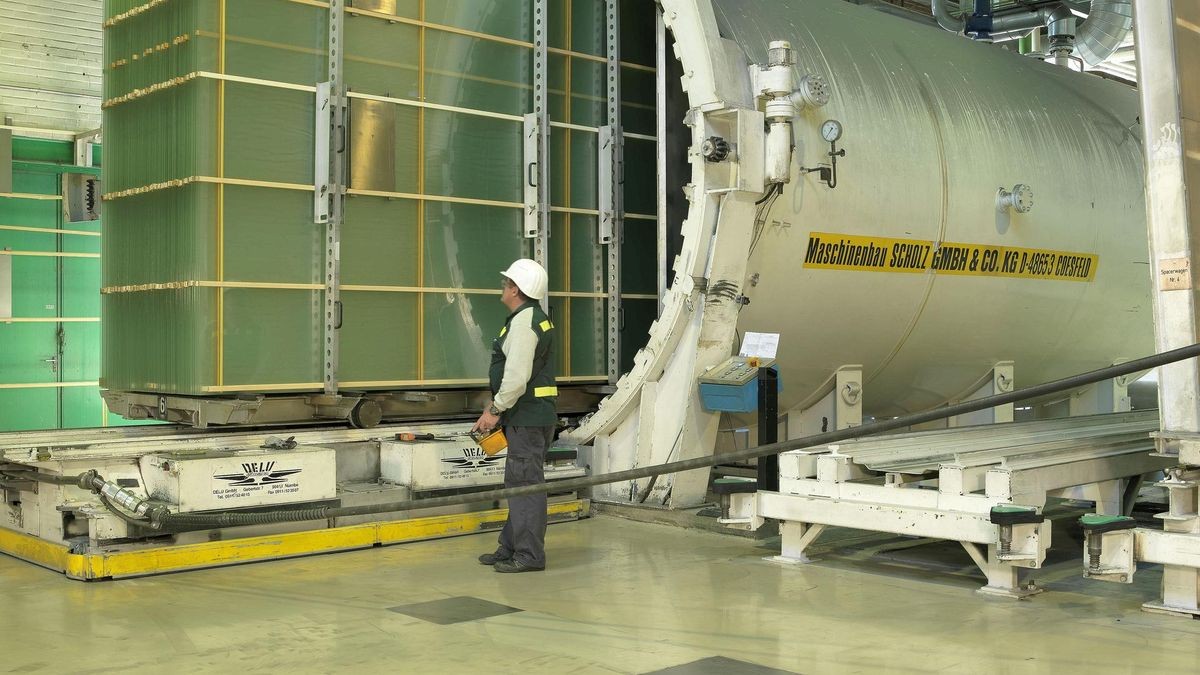
Dagegen halten lässt sich nur mit Know-how und Qualität. Dass davon reichlich vorhanden ist – davon zeugen eine ganze Reihe Referenzprojekte, die Pilkingtons guten Ruf gefestigt haben. So ist nicht nur die innere Kuppel des Reichstags mit dem Spezialglas aus Gelsenkirchen bestückt, sondern auch die Front des Musiktheaters im Revier und die Büros des Flughafen Düsseldorf nach dem verheerenden Brand – sicher ist sicher.