Lütjensee. Das Lütjenseer Unternehmen PAV produziert normalerweise Formularvordrucke. Jetzt werden jede Minute bis zu 700 OP-Masken gefertigt.
Hunderte Kilometer Vlies rattern rollenweise über die Antriebe und Umlenkrollen in der Produktionshalle des Paul-Albrechts-Verlags (PAV) in Lütjensee, werden gefaltet und verschweißt. Am anderen Ende der Maschine stehen Mitarbeiter in weißen Kitteln und verpacken die Ware in kleine Pappkartons mit grünem Aufdruck. Noch vor weniger als einem Jahr wurde hier die Mikroelektronik für Reisepässe hergestellt. Jetzt entstehen in der Halle OP-Masken. Bis zu 700 Stück des medizinischen Mund-Nasen-Schutzes fertigen die Maschinen in der Minute. Das Lütjenseer Unternehmen liefert mittlerweile jede Woche rund zwei Millionen Masken aus – und plant, die Produktionskapazitäten weiter zu erhöhen.
„Die Entscheidung, in die Maskenproduktion einzusteigen, ist kurzfristig gefallen“, sagt Geschäftsführerin Isabel Höftmann-Toebe. Gerade einmal vier Monate seien seit der Idee im März 2020 vergangen, bis im Werk an der Hamburger Straße Anfang Juli die erste Schutzmaske vom Laufband lief. „Hersteller im Inland wurden händeringend gesucht, weil Länder aus Fernost kaum noch Masken exportierten“, erinnert sich die Diplom-Kauffrau.
Zu den Produkten von PAV zählen eigentlich vor allem Druckerzeugnisse
Die Voraussetzungen für eine schnelle Umstellung brachte PAV mit. Zu den Produkten des 1925 gegründeten Familienunternehmens zählen eigentlich vor allem Druckerzeugnisse, etwa Arztvordrucke, Lieferscheine, Protokollbogen, Prospekte und Visitenkarten. „Wir hatten trotzdem einiges an Know-how im Haus, das auch bei der Herstellung von OP-Masken nützlich ist“, sagt Höftmann-Toebe.
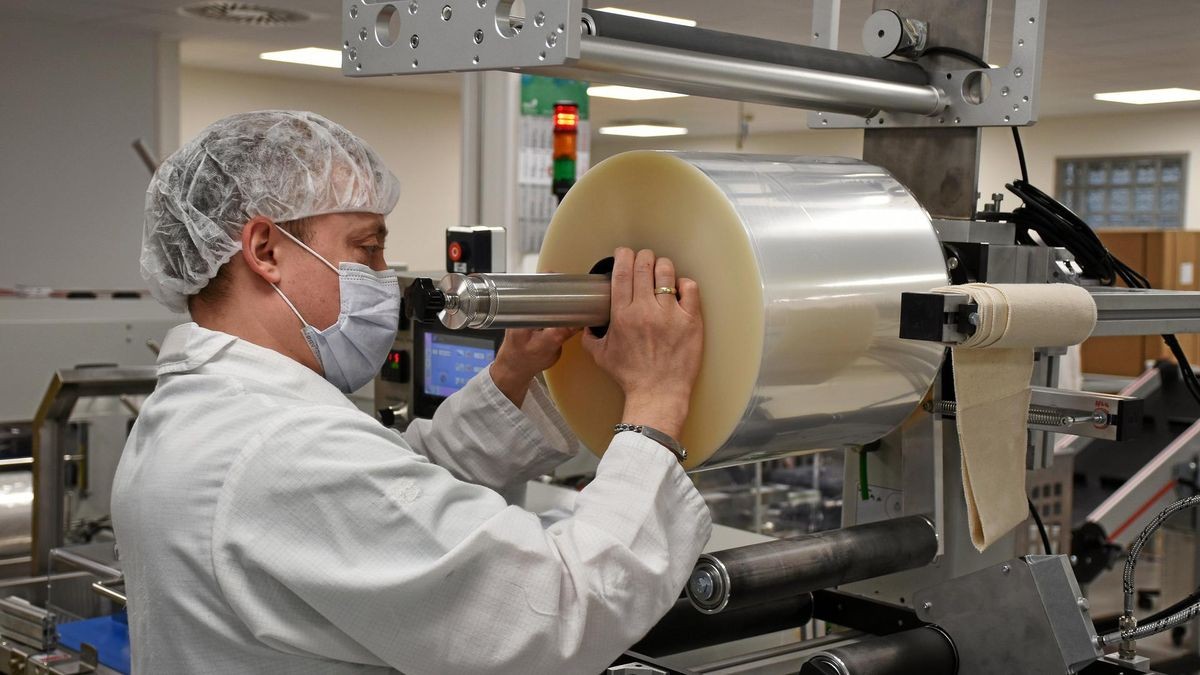
Auch die räumlichen Voraussetzungen waren günstig. „Wir haben zwei sogenannte Reinräume, die speziell gegen Staub und Schmutz abgeschirmt sind“, erklärt die Geschäftsführerin. Bislang wurde dort die Mikroelektronik für Chipkarten und Reisepässe hergestellt. „Während der Pandemie reisen die Menschen weniger“, sagt die PAV-Chefin. Deshalb habe das Unternehmen ohne weiteres kurzfristig Kapazitäten freimachen können. Einen der beiden Spezialräume hat das Lütjenseer Unternehmen nun für die Maskenproduktion umgerüstet. „Auch wenn die Grundanforderungen ähnlich sind, verlangt die Herstellung von medizinischen Produkten noch mal höhere Standards“, sagt Höftmann-Toebe.
Das Unternehmen hat viel investiert und wurde vom Land unterstützt
Einen siebenstelligen Betrag hat PAV in die Umrüstung investiert, drei spezielle Fertigungsmaschinen angeschafft. „Glücklicherweise wurden wir dabei von der Landesregierung unterstützt, dafür sind wir sehr dankbar“, sagt die Geschäftsführerin. Das Land Schleswig-Holstein hatte den Aufbau der Maskenproduktion bei PAV mit rund 950.000 Euro gefördert. Etwa 30 Mitarbeiter sind derzeit in der Maskenproduktion tätig, ein Großteil hat zuvor in der Herstellung der Elektronik der Reisepässe an derselben Stelle gearbeitet.
Die Produktion läuft überwiegend automatisch ab. Vom Verschweißen der Vliesbahnen bis zum Anschweißen der Gummibänder für die Ohren übernimmt alle Arbeitsschritte dieselbe Maschine. An einem Ende des mehrere Meter langen Gerätes rotieren weiße und blaue Vliesrollen mit rasanter Geschwindigkeit. „Daraus werden die verschiedenen Lagen der Maske“, erklärt Dierk Früchtenicht, der als Leiter der Entwicklungsabteilung für den Aufbau der Maskenproduktion verantwortlich war.
Die OP-Masken von PAV sind zertifiziert
Eine OP-Maske setze sich aus verschiedenen Gewebeschichten mit unterschiedlichen Eigenschaften zusammen. „Alle bestehen aus Polypropylen. Nur die Faserung ist unterschiedlich“, erklärt Früchtenicht. Das vielseitige Material zählt zu den weltweit am häufigsten verwendeten Kunststoffen, aus Polypropylen wird ebenso ein Großteil der Innenausstattung von Autos gefertigt wie Rohre, Folie und Verpackungsmaterial.
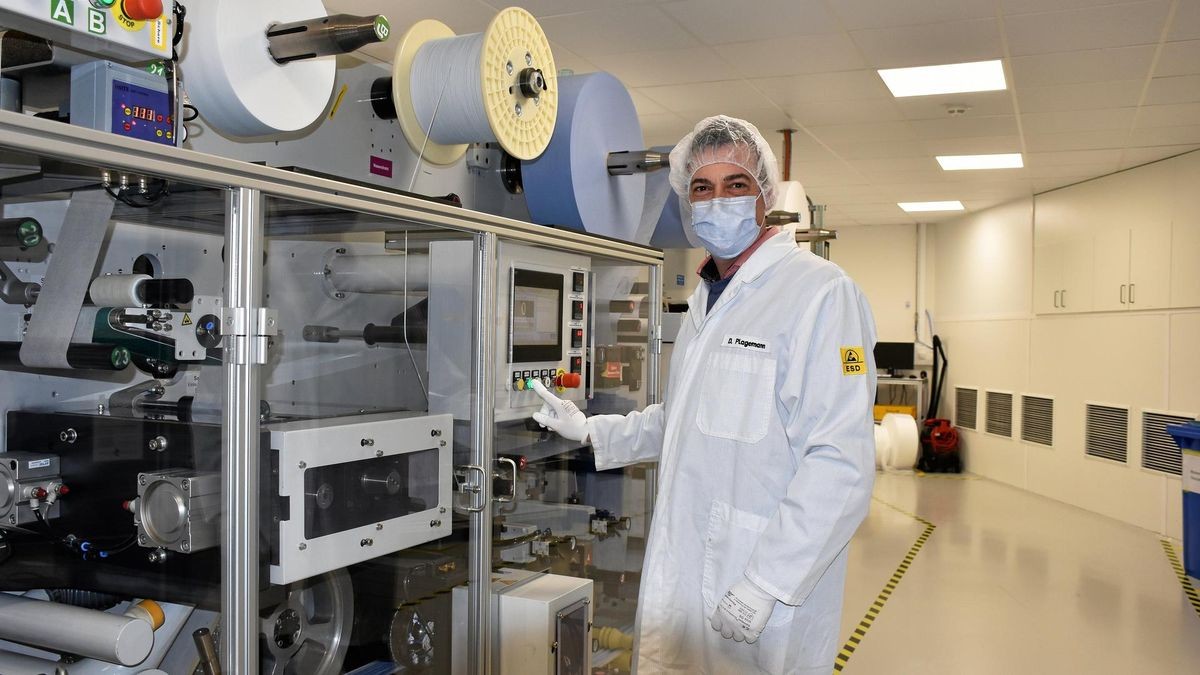
„Die äußerste Gewebeschicht ist das Spinnvlies“, erklärt Früchtenicht. Sie diene als Schutz vor Spritzern und sei blau eingefärbt, damit Innen- und Außenseite der Maske leichter zu unterscheiden seien. Dann folge das sogenannte Meltbown. „Diese Schicht ist der eigentliche Filter und verfügt über sehr kleine Poren“, sagt Früchtenicht. Auf der Innenseite schließt das Thermobond an, das für einen hautfreundlichen Sitz der Maske im Gesicht sorgen soll. „Das Gewebe wird von der Maschine zugeschnitten, übereinandergelegt und mit Ultraschall verschweißt“, erklärt der Entwicklungsleiter. Die OP-Masken von PAV sind nach dem europäischen Standard Typ II R, EN 14683 zertifiziert. Neben einer bakteriellen Filterleistung von mindestens 98 Prozent schreibt der Standard weitere Anforderungen zu Hautverträglichkeit, Spritzschutz, Keimbelastung und Atmungsaktivität vor.
Bis zu sechs Kilometer Vlies auf einer Spule
Mittels einer speziellen Rolle, deren Form entfernt an einen stilisierten Tannenbaum erinnert, wird das Vlies in Falten gelegt. Gleichzeitig wird der Draht für die Befestigung auf der Nase eingearbeitet. Als nächstes verschweißt die Maschine die Ränder der Masken.
Zuletzt fahren die Masken auf einem kleinen Fließband zwischen mehreren zylinderförmigen Vorrichtungen hindurch, die die bereits zugeschnittenen Gummibänder aufspannen und an den Seiten des Vlieses befestigen. Die eine Fertigungsmaschine produziert bis zu 500 Masken in der Minute, die anderen 100. Die Geschwindigkeit stellt Produktionsleiter Dirk Plagemann über ein Display ein.
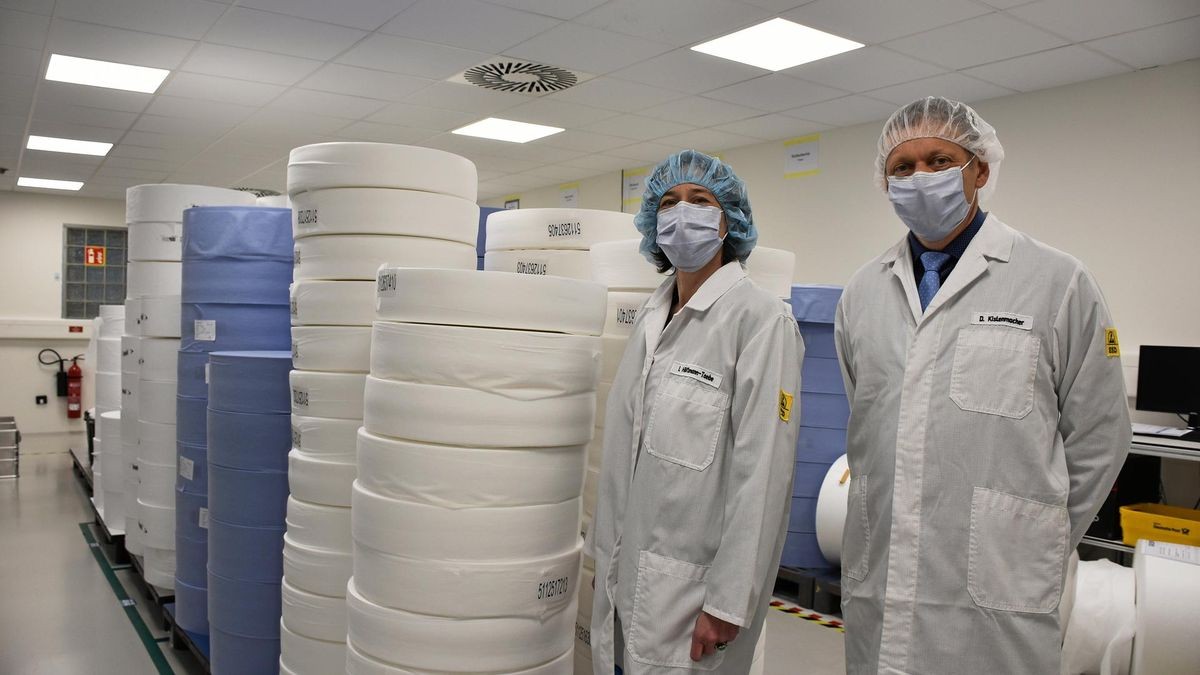
Die Vliesrollen müssen regelmäßig nachgelegt werden. Im hinteren Bereich der Werkshalle lagert der Nachschub. Zwischen 1,5 und sechs Kilometer Gewebe befinden sich auf einer Spule. Insgesamt liegen hier mehr als 200.000 Meter Vlies, dazu Gummiband, Draht und Folie. Daniel Giss ist damit beschäftigt, eine neue Rolle Verpackungsfolie in die Maschine einzuspannen. Den Beginn präpariert er mit einem Klebestreifen, der an dem Gerät befestigt wird und von dem aus die Maschine beginnt, die Folie einzuziehen.
Maschine wechselt automatisch auf die neuen Rollen
Von jedem Material sind jeweils zwei Rollen in die Maschinen eingespannt. „Das ermöglicht einen reibungslosen Wechsel, wenn eine aufgebraucht ist, ohne die Produktion zu unterbrechen“, sagt Dirk Kistenmacher. Der Diplom-Ingenieur ist als Technischer Leiter dafür verantwortlich, dass die Maskenproduktion reibungslos läuft. „Die Maschine wechselt dann automatisch auf die neue Rolle.“
Die letzten Produktionsschritte werden von Mitarbeitern übernommen. Die Aufgabe von Goitom Nur und Ykalo Mekil ist es, die fertigen Masken zu sammeln und in Kartons zu verpacken. Über ein Fließband rollen die Mundschutze aus der Fertigungsmaschine. Geschickt legen die jungen Männer die Mundschutze zu Stapeln von je 10 Einheiten aufeinander und schieben anschließend fünf Stapel in die vorgefalteten Pappschachteln. Ykalo Mekil sammelt die Schachteln in einem Plastikkorb, später werden sie in große Pappkartons verpackt und für die Auslieferung vorbereitet.
OP-Masken sollen nach Corona ein Geschäftszweig bleiben
Neben dem Standardmodell stellt das Unternehmen auch eine Komfort-Variante her, bei der die Befestigung für die Ohren aus einem speziellen Vlies gefertigt ist. „Die Bügel lassen sich einmal flexibel dehnen, anschließend sind sie eingestellt und ziehen sich nicht wieder zusammen“, erklärt Kistenmacher. Dadurch seien sie auf Dauer angenehmer zu tragen, drückten weniger auf die Ohren. Die Komfort-Variante wird an der Nachbarmaschine gefertigt. „Im Prinzip funktioniert alles genauso, nur dass diese Maschine die Produkte auch automatisch in Packs einschweißt und in Schachteln verpackt“, so der Technikchef.
Für Geschäftsführerin Isabel Höftmann-Toebe ist die Maskenproduktion ein voller Erfolg. „Natürlich wissen wir, dass die Nachfrage nicht immer auf dem Niveau der Pandemie bleiben wird“, sagt sie. Dennoch habe ein Umdenken in Politik und Gesellschaft stattgefunden. „Ich habe den Eindruck, dass wieder mehr Wert auf Produktionskapazitäten im Inland gelegt wird“, sagt sie. Die PAV-Chefin möchte die OP-Masken nach dem Ende der Pandemie als Geschäftszweig erhalten. In Zukunft werden in den Regalen der Ärzte und Apotheken also vermehrt Masken „Made in Lütjensee“ zu finden sein.