Harburg. Hinter den historischen Fassaden der Phoenix am Harburger Bahnhof ist ein Hochtechnologie-Zentrum für moderne Kunststoffprodukte entstanden.
Der Kühlschlauch fühlt sich an, als sei er aus Gummi. Allerdings ist er sehr leicht. Das wichtige Autobauteil besteht aus Kunststoff und ist auf einer High-Tech-Produktionsstraße entstanden. Es ist ein Vertreter der neuesten Produktgeneration der Firma Continental in der ehemaligen Phoenix-Gummifabrik am Harburger Bahnhof. Hinter den historischen Backsteinfassaden aus dem 19. und frühen 20. Jahrhundert entwickelt der Automobil-Zulieferer heute Produkt-Prototypen für E-Mobile großer Automarken und erschließt sich mit dem Einsatz digitaler Technik neue Geschäftsfelder.
2,7 Millionen Euro für Gebäude und Anlagentechnik
„Bei uns spiegelt sich der industrielle Wandel wider, der ganz Harburg betrifft: Wir legen unseren Schwerpunkt weniger auf die Produktion, sondern vielmehr in neue Entwicklungen, in Lösungen für die Mobilität der Zukunft“, sagt Peter Scholtissek, der den Harburger Standort leitet. Zu diesem Zweck hat Continental für sein „Kunststoffkompetenzzentrum“ 2,7 Millionen Euro in Gebäude und Anlagentechnik investiert, um dort leistungsfähige Schlauchleitungen für Elektrofahrzeuge zur Serienreife zu entwickeln.
Ein Kunststoffrohr aus drei Schichten
Das Herz des Zentrums ist die Kunststoffextrusion. Sie ist vor wenigen Monaten in Betrieb gegangen. In der Anlage wird zunächst Kunststoffgranulat erwärmt und verflüssigt. Der flüssige Kunststoff wird dann durch eine formgebende Öffnung gepresst (extrudiert), aus der ein Endlos-Kunstoffrohr herausquillt. Nach einem kühlenden Bad passiert das Rohr eine Strickmaschine, die es mit einem Gewebe umgibt. Im letzten Schritt wird außen eine zweite Kunststoffschicht über den Schlauch gezogen.
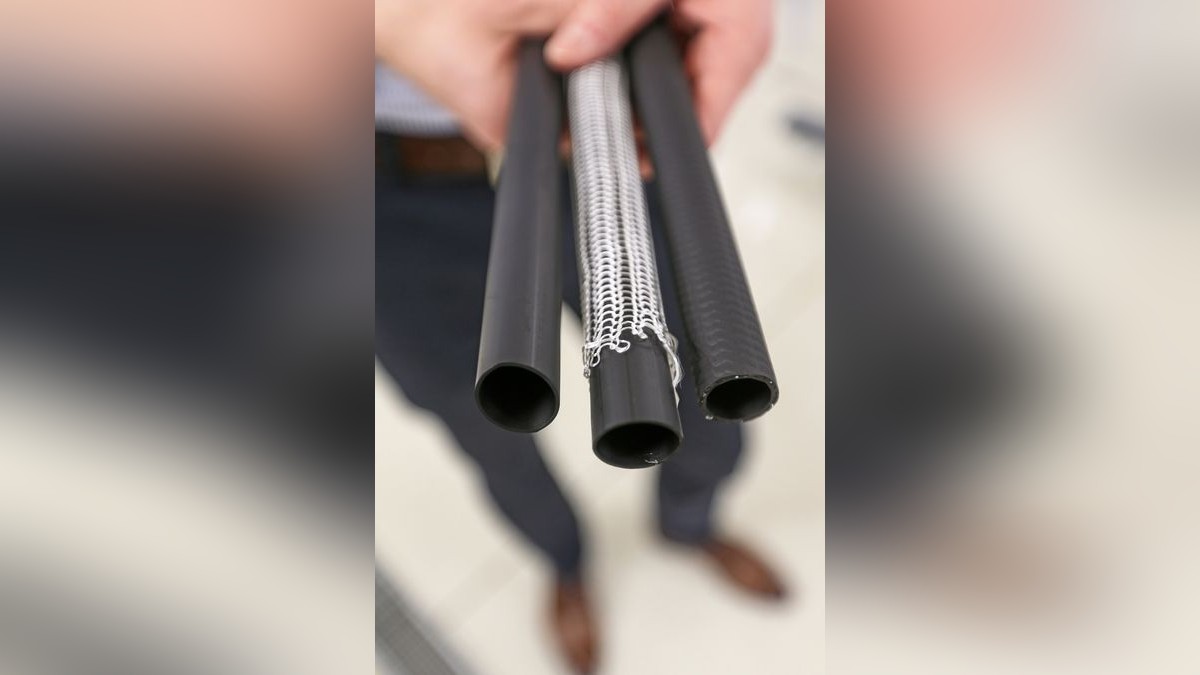
E-Mobilität verlangt nach mehr Kunststoffkomponenten
Das dreischichtige Rohr ist der Ausgangspunkt für die Prototypen-Entwicklung. „Durch die E-Mobilität steigt der Kunststoffeinsatz in den Fahrzeugen“, sagt Dirk Stuhrmann, der das neue Technologiezentrum leitet. In ihm arbeiten mehr als 140 Mitarbeiter, rund 100 in der Entwicklung und 40 in der Produktion. „Wir entwerfen für viele große Automobilhersteller Prototypen, die dann später in den Produktionsstandorten von Continental in Serie gehen“, sagt Stuhrmann und reicht ein besonders schlankes Rohr mit komplizierten Windungen über den Tisch. „Dies ist ein Kühlschlauch für das Tesla-Modell S.“ Jährlich verließen 100.000 bis 120.000 Prototypen das Technikzentrum, oftmals seien es aber „Lösungen von der Stange“.
Prototypen aus Harburg für die Weltproduktion
Die mit den Autoherstellern entwickelten Komponenten werden in Deutschland, aber auch in China, den USA, Mexiko und weiteren Ländern produziert. Auch Kraftstoffe oder Getriebeöle können durch die Schläuche fließen. Doch geht es vor allem um Kühlwasserschläuche. Bei der Elektromobilität spiele die Kühlung eine zentrale Rolle, betont Anlagenleiter Maximilian Schöngart: „Hier ist Hochvolt-Technik im Einsatz, das erhöht die Brandgefahr. Unser Ziel sind Thermosysteme: Lösungen, die mit möglichst wenig Batterieeinsatz bedarfsgerecht zum Beispiel Motor oder Batterie kühlen oder heizen. Als Voraussetzung müssen wir die Schläuche mit Sensoren ausstatten.“ Continental könne „den Wandel Richtung E-Mobilität mitgestalten“, sagt Stuhrmann.
Außen Industriedenkmal – innen Hochtechnologie
Standortleiter Scholtissek führt über das Betriebsgelände, vorbei am werkseigenen Kraftwerk mit dem Phoenix-Schornstein: „Von außen sieht es aus wie ein Industriedenkmal, doch innen ist modernste Technik im Einsatz.“ 2004 hat Continental die Phoenix AG übernommen, ein Jahr später wurde sie mit ContiTech zusammengelegt. Heute hat das Werk rund 800 Mitarbeiter. Noch einmal so viele Menschen beschäftigen Tochterfirmen von Phoenix, die weiterhin autark sind. Sie haben ihren Sitz in der Nähe und arbeiten mit der „Stiefmutter“ eng zusammen.
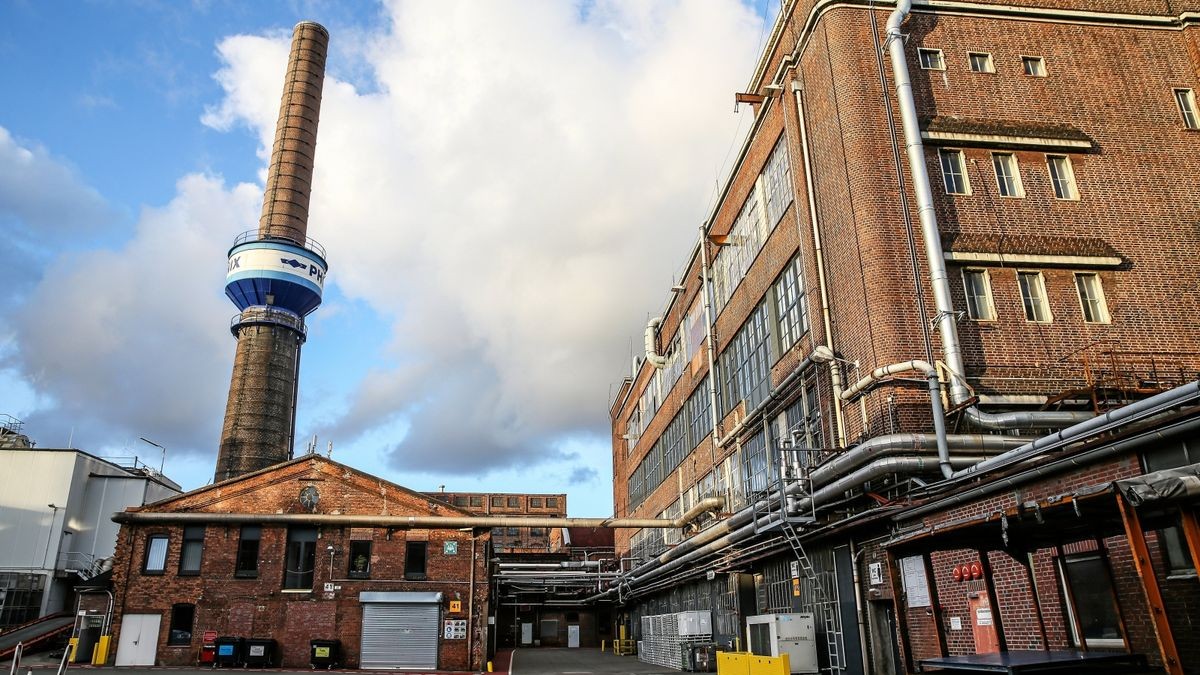
Die den Harburgern und vielen Bahnreisenden vertrauten Phoenix-Schriftzüge sollen bestehen bleiben, so Scholtissek. Schließlich stecke noch viel Phoenix im Standort. „Wir stellen hier Mischungen für viele unserer Gummi-Produkte her“, sagt der Werkschef. „Gummi besteht aus Kautschuk, einem Vernetzer (meist Schwefel) und einem Füllstoff, klassischerweise Ruß. Wir haben hier mehr als 1000 Rohstoffe und 3000 Rezepte.“ Das Mischwerk habe Continental von Phoenix übernommen und weiterentwickelt.
Tradition der Phoenix bleibt bestehen
Die Gummimischungen gehen größtenteils an andere Continentalwerke. In Harburg werden daraus neben Kühlwasserschläuchen, die ebenfalls schon bei Phoenix ein Entwicklungsschwerpunkt waren, Luftfedern für Schienenfahrzeuge hergestellt. Auch Fahrgäste der Hamburger Hochbahn profitieren vom Komfort durch Harburger Luftfedern. Technisch sind sie – vereinfacht gesprochen – rund ein halben Meter große Ballone, die oben und unten zwischen zwei Metallplatten gezwängt sind. „Es gibt keinen anderen Continental-Standort, der so vielfältig ist“, sagt Scholtissek.
Innovationszentrum mit eigener Fertigung
Er steigt in einen alten Lastenfahrstuhl, der sich langsam in den fünften Stock eines historischen Fabrikgebäudes hocharbeitet. Auf mehreren Stockwerken stehen große Hallen leer. Ihnen ist anzusehen, dass hier einst eifrig produziert wurde. In einem der beiden Flügel des fünften Stocks ist die Neuzeit eingezogen. Hier befindet sich der Innohub (Innovationszentrum), eine moderne, offene Bürolandschaft, in der digitale Projekte des Autozulieferers vorangetrieben und neue Geschäftsfelder erschlossen werden. Corona fegte die Ideenschmiede leer, die Entwickler arbeiten dezentral zuhause. Dennoch ist dies nicht nur gestalterisch die Speerspitze der Continentalen Transformation eines reinen Produktionsstandorts zu einem Technologie-Campus mit angeschlossener Fertigung.
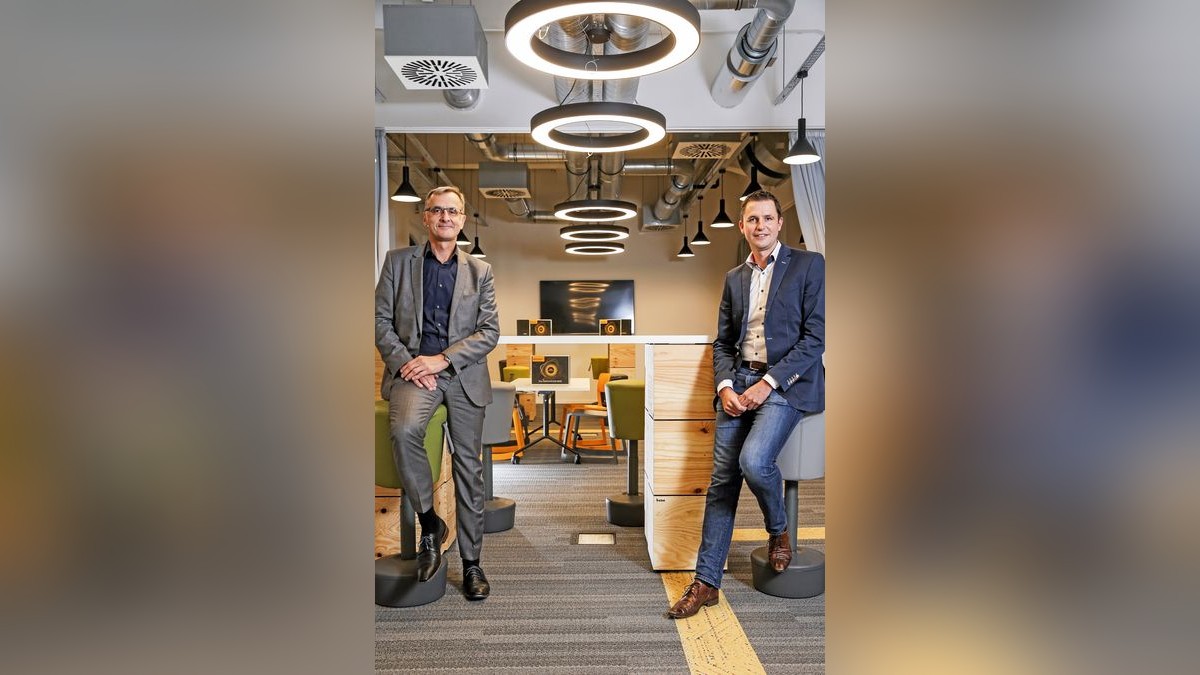
Christoph Seeger führt durch die Räumlichkeiten. Er leitet in Harburg den Bereich Innovationen, Geschäftsfeldentwicklung und digitale Lösungen. „Wir haben hier mehr als 15 Projekte laufen, um neue Geschäftsmodelle im digitalen Bereich zu erschließen“, sagt er. Ein Beispiel sei Fleetmatch, eine Software, die über Internet und Smartphone qualifizierte Berufskraftfahrer stärken soll. Sie können zum Beispiel Verladerampen bewerten und damit Vorreiter, aber auch mit Wartezeiten verbundene Abläufe sichtbar machen. Ein anderes neues Geschäftsfeld sei eine digitale Inspektionstechnik für Erzförderbänder, die 30 Kilometer lang sein können. Hier fliegt eine Drohne die offenen Bereiche ab.
Anbindung an die lokalen Hochschulen
Intensiver als herkömmlich arbeite das Innovationszentrum mit Studierenden zusammen, so Seeger. Eine große Rolle spielt dabei die Technische Universität Hamburg in Harburg und die Tutech Innovation als Brücke zur Wirtschaft. „Als wir vor zwei Jahren zu entscheiden hatten, ob wir das Innovationszentrum hier in Hamburg-Harburg ansiedeln sollten, habe ich lange mit Martin Mahn von der Tutech gesprochen und mich überzeugen lassen, dass wir hier gut eingebettet sind. Genau das ist eingetreten.“